3D Printed Molds for Casting: Revolutionizing Manufacturing
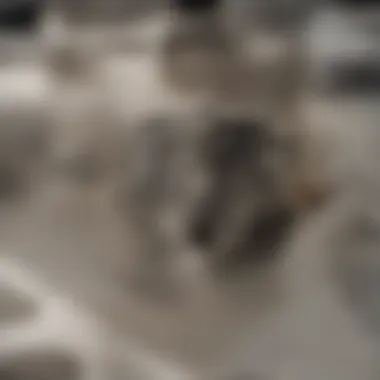
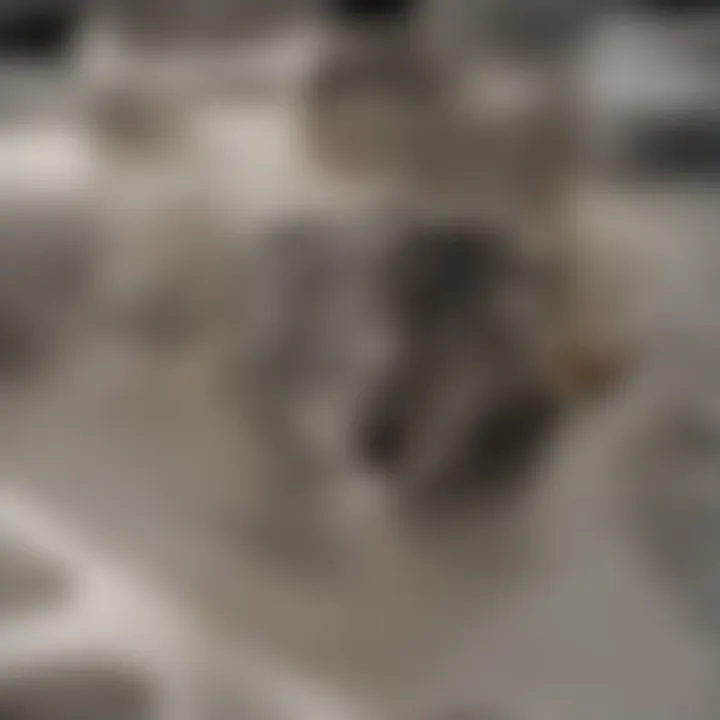
Intro
The integration of 3D printing technology within the production of molds for casting has introduced a significant shift in manufacturing practices. This evolving method influences several sectors, making the process more efficient and precise. By understanding how 3D printed molds function, one can appreciate their role in enhancing sustainability and accuracy in casting processes.
Research Methodology
Description of research design and approach
The research on 3D printed molds employs a mixed-methods approach. It incorporates quantitative data from industry case studies and qualitative insights through expert interviews. This combination allows for a well-rounded examination of both the numbers and the narratives behind the use of 3D printing in mold production.
Materials and methods used in the study
The primary materials explored in this research include thermoplastics such as PLA, and advanced polymers like Nylon 12. Various 3D printing methods are assessed, including Fused Deposition Modeling (FDM) and Selective Laser Sintering (SLS). These methods were chosen for their relevance in the production environments that utilize casting processes. For practical applications, several industries, such as automotive and aerospace, are analyzed to showcase how these molds are implemented.
Discussion and Interpretation
Interpretation of results in the context of existing literature
The findings from the study reveal that 3D printed molds significantly reduce lead times and costs in casting processes. This aligns with existing literature which indicates a growing trend towards additive manufacturing in industrial settings. The adaptability offered by 3D printing allows for customized mold designs that meet specific needs without the constraints of traditional manufacturing.
Implications for future research or practical applications
Future research should expand on the long-term reliability of these molds in high-volume production settings. Further examination of material innovations could lead to even better performance standards. As industries continue to seek sustainable practices, the implications of using 3D printed molds highlight a promising future for environmentally conscious manufacturing processes.
"The transformation of manufacturing through 3D printing is not just a trend; it's a testament to the power of innovation in industrial processes."
Foreword to 3D Printing in Manufacturing
In recent years, 3D printing has emerged as a transformative force in manufacturing. Its relevance is particularly significant in the realm of mold making, which is a critical component of casting processes across various industries. Understanding this topic can provide insights into how manufacturing practices have evolved and how they may continue to develop.
The integration of 3D printing in manufacturing presents numerous advantages. One important benefit is the ability to create complex and customized designs with precision. Traditional mold-making techniques often limit creativity due to material and process constraints. However, 3D printing allows for intricate details that can improve the characteristics of the final product, enhancing functionality and aesthetics.
Furthermore, 3D printing promotes efficiency in production timelines. With traditional methods, the lead times for mold creation can be extensive. In contrast, 3D printed molds reduce this period significantly, which can be crucial for industries that require rapid prototyping or production changes. This time-saving effect along with the ability to customize designs can lead to faster innovation cycles and better market responsiveness.
However, it is essential to consider some challenges that accompany this technology. Material limitations and concerns regarding finish quality can impede the effectiveness of 3D printed molds in certain applications. Thus, while the benefits are substantial, careful thought must be given to the specific requirements of each use case in order to maximize the advantages of 3D printing in manufacturing.
In summary, the importance of understanding 3D printing in manufacturing extends beyond mere technological advancements. It reshapes practices and strategies within various sectors. This introduction will set the stage for exploring how 3D printed molds specifically enhance casting processes, drawing connections to material selection, methods, and applications.
Understanding 3D Printed Molds
Understanding 3D printed molds is central to grasping the significant impacts of 3D printing technology on casting processes. These molds offer new opportunities in terms of design flexibility, production efficiency, and customization. Their importance extends across various industries, providing solutions that traditional molding methods often cannot achieve. In this section, we will delve into the different types of molds, how they function, and how 3D printing enhances their production.
Defining Mold Types
Permanent Molds
Permanent molds are durable molds made from materials like metal, designed to be reused many times. Their main benefit lies in their longevity, leading to reduced costs per part over time. They are capable of producing high volumes of castings with excellent surface finish. The key characteristic of permanent molds is their robust nature, which supports a variety of casting processes. However, they require significant initial investment and are best suited for high-volume production.
In this context, the unique feature of permanent molds is their ability to maintain dimensional accuracy over time. This stability is crucial in industries where precision is critical, such as aerospace or automotive. The disadvantage might stem from their initial setup costs and the time required to produce them, which can be substantial.
Disposable Molds
Disposable molds made of materials like sand or shell can only be used once. The specific aspect of disposable molds is their rapid production capability, ideal for short production runs. This characteristic allows manufacturers to quickly adapt to new designs without the burden of long lead times.
A key characteristic of disposable molds is their low cost, as they require less material compared to permanent options. The advantage here is evident: organizations can produce a variety of shapes and designs without a heavy investment in equipment or materials. However, the disadvantage includes ongoing costs with each new mold, which can be high for large production volumes.
Core Molds
Core molds, often used in conjunction with either disposable or permanent molds, create internal cavities in cast parts. Their importance lies in producing complex geometries that cannot be achieved with traditional methods. A critical aspect of core molds is their design flexibility, which facilitates intricate parts and improves overall quality.
The key characteristic of core molds is their ability to allow for added detail and improved flow of casting material. This effectiveness leads to superior casting results in sectors like consumer goods and automotive. However, integrating core molds into a production line may increase complexity and require additional handling.
How 3D Printing Enhances Mold Production
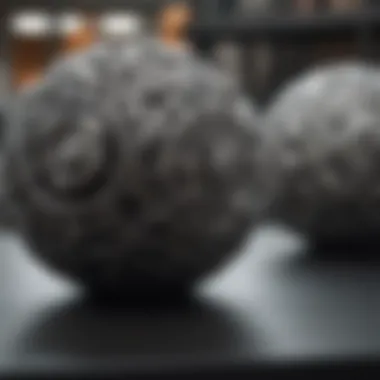
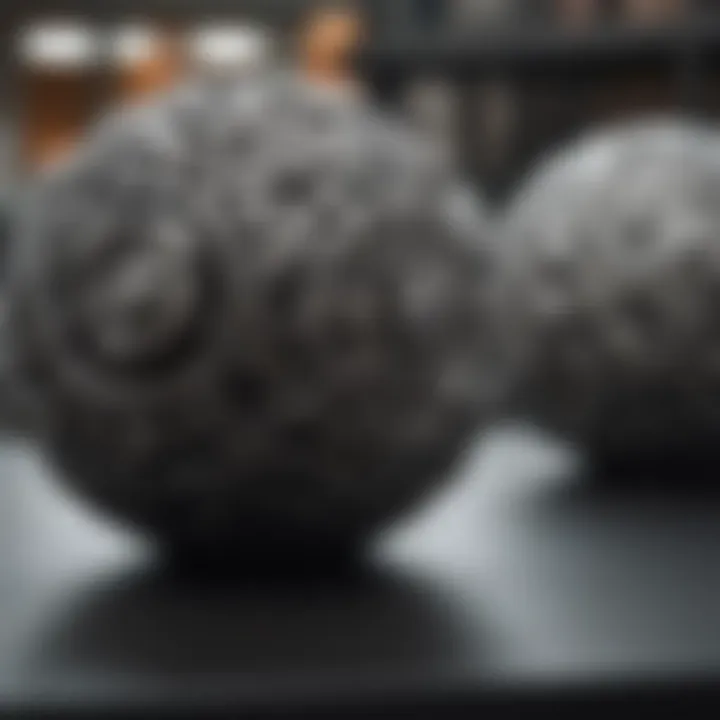
3D printing significantly enhances mold production by reducing the time and effort required in the design and manufacturing phases. It allows for rapid prototyping, which enables designers to iterate quickly based on testing feedback. This capability is particularly crucial in industries needing constant innovation and adaptation.
- The additive process of 3D printing allows for the creation of complex internal structures that cannot be achieved through traditional subtractive methods.
- It also reduces waste material production, as 3D printing only uses what is necessary for the mold. This not only minimizes costs but also aligns with sustainability goals.
By refusing the limitations of traditional mold making, 3D printing opens the door to new design possibilities, thus revolutionizing the way molds are created for casting.
Materials for 3D Printed Molds
The selection of materials for 3D printed molds is crucial in determining the effectiveness and efficiency of the casting processes. Different materials influence the moldβs durability, thermal properties, and overall performance in various conditions. A thorough understanding of material types leads to optimal outcomes, whether in terms of precision, speed, or cost-efficiency. The advent of 3D printing technology allows for a variety of materials that were previously not feasible in traditional mold making methods.
Common Materials Used in 3D Printing
Thermoplastics
Thermoplastics are widely used in 3D printing for molds. Their ability to soften when heated and solidify when cooled makes them adaptable. A key characteristic of thermoplastics is their versatility, being available in various formulations that enhance performance. This is beneficial when creating complex mold designs, as they can be printed with intricate details.
A unique feature of thermoplastics, like ABS and PLA, is their ease of use. They can often be printed quickly and are less expensive compared to other materials. However, they can have limitations, especially under high thermal stress. Their mechanical properties may degrade with prolonged exposure to extreme heat; hence they might not be suitable for high-temperature casting applications.
Photopolymers
Photopolymers are another category of materials significant in the realm of 3D printed molds. They consist of liquid resins that harden when exposed to a light source. The defining characteristic of photopolymers is their precision. Layers can be cured with extreme accuracy, enabling the production of highly detailed molds.
A unique advantage of photopolymers is their exceptional surface finish. Molds produced from photopolymers can have smoother surfaces, reducing the need for additional machining or finishing work. On the downside, photopolymers might not be as durable as other materials, particularly under harsh manufacturing environments. They can be susceptible to temperature fluctuations, which can restrict their application scope.
Metals
When it comes to durability and strength, metals stand out as an essential material for 3D printed molds. Typically, metals like stainless steel and aluminum are employed for their high heat resistance and structural integrity. A key characteristic of metals is their ability to withstand significant thermal and mechanical stresses, thus enhancing mold longevity.
The unique feature of metal molds is their capability for high-volume production. They can produce batches of parts with greater consistency and accuracy due to their inherent properties. However, the costs associated with metal 3D printing are generally higher due to the required specialized processes and machines, such as Direct Metal Laser Sintering. This can act as a barrier for smaller operations or prototyping phases.
Material Properties for Casting Applications
The material properties of 3D printed molds are vital for successful casting applications. Key considerations include thermal conductivity, hardness, and resistance to chemical corrosion. Molds must exhibit characteristics that align with the casting material, ensuring compatibility for effective process execution.
- Thermal Conductivity: Essential for maintaining the moldβs shape during the casting process. Higher thermal conductivity aids in faster cooling, resulting in better-surfaced final products.
- Hardness: Affects abrasion resistance. Mold durability is paramount, especially in high-wear applications.
- Chemical Resistance: Important for molds used with reactive metals or materials. This property ensures the mold doesn't degrade or interact adversely with the casting material, ensuring a successful operation.
Understanding these properties helps in selecting the right material for specific casting scenarios.
"Choosing the right material is critical. It can significantly affect the casting quality and efficiency of the production process."
The 3D Printing Process for Molds
The process of 3D printing molds plays a critical role in modern manufacturing practices. It offers precision engineering and enables complex geometries that traditional methods cannot achieve. By employing 3D printing technologies for mold creation, manufacturers can reduce lead times, achieve higher accuracy, and introduce unique customization possibilities. Each stage of the 3D printing process is essential for translating a digital design into a physical mold, ultimately impacting the quality and efficiency of the casting process.
Designing a Mold for 3D Printing
Designing a mold specifically for 3D printing involves several considerations to ensure successful fabrication. Designers must account for the properties of the chosen material, the complexity of the part being cast, and the limitations of the 3D printing technology. A well-thought-out design promotes optimal flow of casting material and minimizes the risk of defects.
Key factors that influence mold design include:
- Wall thickness : Sufficient thickness is crucial to maintain structural integrity yet avoid excessive material usage.
- Draft angles: These are necessary to facilitate easy removal of the mold once the casting process is complete.
- Feature size: The resolution of the 3D printer will dictate what detail can be included in the mold design, aligning with the casting requirements.
A proper design ensures that the mold meets the specific needs of casting while taking full advantage of the benefits offered by 3D printing.
Additive Manufacturing Techniques
Additive manufacturing techniques vary widely, each with specific strengths and weaknesses. Here, we discuss three prevalent methods in 3D printing for molds: Fused Deposition Modeling, Stereolithography, and Selective Laser Sintering.
Fused Deposition Modeling
Fused Deposition Modeling (FDM) stands out for its simplicity and versatility. In FDM, a thermoplastic filament is heated and extruded layer by layer to create the mold. One key characteristic of FDM is its ability to work with a range of materials, including ABS and PLA, making it a popular choice for many applications.
The temperamental layer adhesion in FDM is a unique feature, wherein layers bond as they cool. This can present challenges for mechanical strength but can also allow for rapid prototyping, which accelerates the design phase. The primary advantages of FDM include affordability and accessibility, making it favored among startups and educational institutions.
Stereolithography
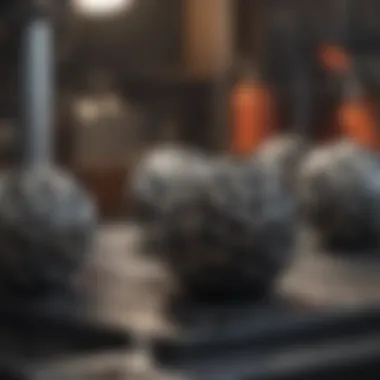
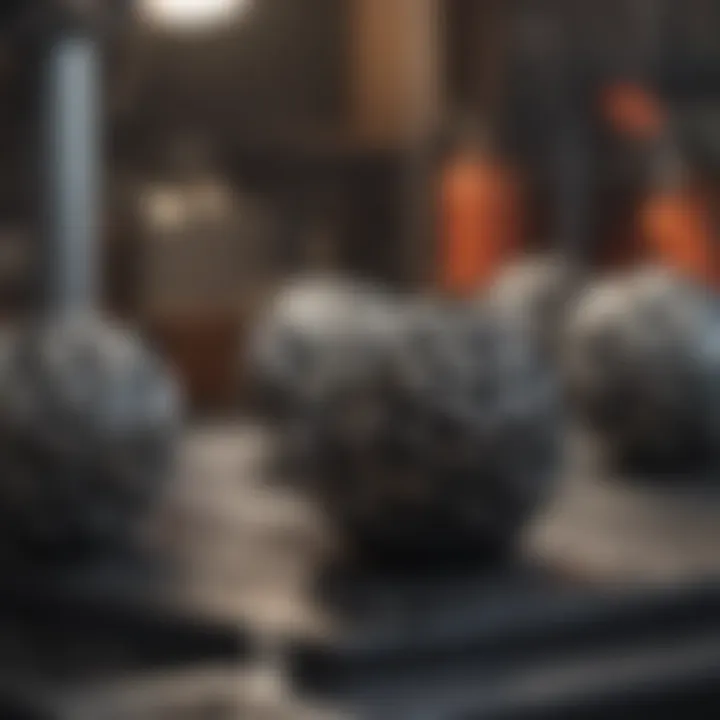
Stereolithography (SLA) provides exceptional detail and surface finish, a vital element in mold making. This technology uses ultraviolet light to cure a liquid resin in a layer-by-layer process. The principal advantage of SLA is its high precision and smooth finish, which results from the ability to utilize fine laser beams.
SLA is especially beneficial for parts requiring intricate details that would otherwise be difficult to achieve. However, one must consider the rigidity of the cured resin, which may not withstand high thermal stress over multiple uses compared to other techniques. This trade-off needs careful evaluation during the design stage.
Selective Laser Sintering
Selective Laser Sintering (SLS) employs a laser to fuse powdered material, typically nylon or other polymers, layer by layer. Its most significant characteristic is the ability to create complex geometries without needing support structures since excess powder acts as a support.
SLS is notable for producing durable molds suitable for functional testing and low-volume production. This technique supports a wide range of materials, yet it can be more costly than other processes. SLS molds may require post-processing to achieve desired surface finishes, yet the mechanical properties of the final product often justify these additional steps.
Overall, understanding these additive manufacturing techniques allows for informed choices when selecting a method for 3D printing molds, aligning choices with specific project requirements.
Applications of 3D Printed Molds
The use of 3D printed molds is increasingly significant in various sectors. This technology introduces a flexible, cost-effective, and efficient way to produce molds for casting. The adaptability of 3D printed molds allows for innovations that were once difficult or impractical. As industries evolve, the need for high precision and short turnaround times has grown. All these points illustrate that understanding the applications of 3D printed molds is crucial for manufacturers aiming to optimize their production processes.
Industrial Applications
Aerospace Industry
In the aerospace field, 3D printed molds play a vital role in creating complex components. These molds can support intricate design shapes that traditional methods often struggle to achieve. One major characteristic of the aerospace industry is its demand for high strength-to-weight ratios in parts. 3D printed molds enable manufacturers to produce lightweight components that meet safety standards and perform effectively.
A unique feature of these molds is their ability to create cooling channels within parts, which help in reducing weight while maintaining structural integrity. This contributes significantly to fuel efficiency and overall performance in aerospace applications.
Automotive Manufacturing
For the automotive sector, 3D printed molds are valuable in rapid prototyping and low-volume production. The automotive industry requires fast-paced development cycles, which makes the shortened lead time of 3D printing an attractive solution. The capability to quickly iterate designs allows manufacturers to fine-tune components before mass production.
A distinguishing aspect is the ability to produce customized components that cater to specific vehicle designs or performance requirements. The flexibility of 3D printed molds can lead to cost savings in manufacturing while minimizing waste, making it a beneficial approach in this highly competitive market.
Consumer Goods
In consumer goods, the use of 3D printed molds can vary widely from Artistic designs to practical home products. This sector benefits from the customization capabilities that 3D printing offers. It allows companies to create unique products that resonate well with increasingly diverse consumer preferences.
The main characteristic of consumer goods applications is emphasis on aesthetics as well as functionality. 3D printed molds help to produce visually appealing and ergonomic designs that stand out in the market. However, it is important to ensure that the molds can still handle the stress and strain associated with mass production.
Healthcare and Medical Devices
The healthcare sector increasingly relies on 3D printed molds to develop specialized medical devices and prosthetics. This technology allows for tailored solutions that meet individual patient needs. Customization is especially important in orthopedics and dental applications, where molds must fit precisely to ensure effectiveness and comfort.
Another advantage is the speed at which these devices can be produced, which is crucial in time-sensitive medical situations. Nevertheless, the challenge persists regarding regulatory approvals for new medical device designs. Companies must navigate these regulations carefully to ensure compliance.
Art and Sculpture
In the realm of art, 3D printed molds have introduced new creative possibilities. Artists can explore complex shapes and forms that traditional techniques may not accommodate. These molds enable artists to experiment with materials and textures in ways that enhance their work.
Moreover, the capability for rapid prototyping also extends to the art world. It allows for immediate adjustments and revisions during the creative process. Despite the artistic advantages, there are often discussions on the value of handmade versus machine-made creations. Artists must decide how they want to balance authenticity with innovation in their work.
Advantages of 3D Printed Molds
The surge of 3D printing technology has significantly changed manufacturing, especially in mold production. The advantages of using 3D printed molds in casting are not only numerous but also crucial for enhancing production efficiency, customization, and cost-effectiveness. This section discusses the main benefits, underscoring their relevance and importance in modern manufacturing settings.
Customization and Complexity
3D printing allows for a high level of customization that is difficult, if not impossible, to achieve with traditional molding techniques. Designers can create molds that are tailored to specific requirements, integrating complex geometries that would typically require multiple parts when manufactured conventionally.
The ability to make intricate designs enables more precise control over the casting process. For example, cooling channels can be integrated directly into the mold structure, which optimizes the solidification process and improves the overall quality of the final product. This flexibility not only satisfies specific customer demands but also opens up opportunities for innovation in product design.
Reduced Lead Time
One of the most significant advantages of 3D printed molds is the reduction in lead time for production. In traditional manufacturing, creating molds can take weeks or even months depending on complexity. However, with 3D printing, the turnaround time is substantially shorter, often reduced to days.
This expedited process allows for faster concept-to-market timelines. Manufacturers can respond to market demands more quickly, thus improving their competitiveness. In addition, rapid prototyping is feasible with 3D molds, allowing for testing and modifications prior to full-scale production, further streamlining operations.
Cost Efficiency

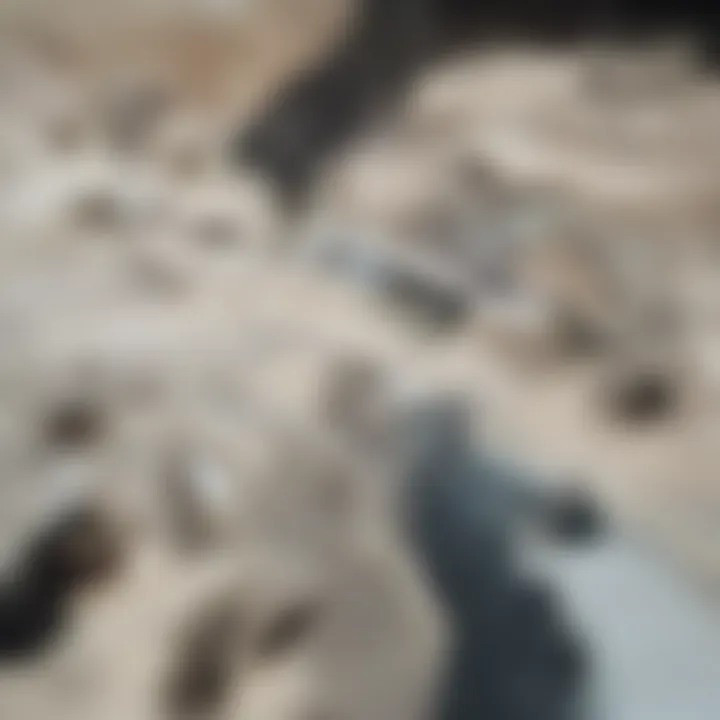
Cost efficiency is another compelling benefit of using 3D printed molds. Traditional mold production often requires high initial investments in tooling and setup, which can be prohibitive, especially for low-volume runs. With 3D printing, the costs associated with developing and producing molds are notably lower, primarily due to the reduction in material waste and the absence of costly molds and tooling.
Furthermore, because 3D printed molds can be easily modified or repaired, manufacturers can save on replacement costs. This is particularly beneficial for businesses focused on small batch productions where the conventional methods are less economical. By leveraging 3D printed molds, companies can enhance their bottom line while producing high-quality castings that meet customer specifications.
By providing significant advantages in customization, lead time reduction, and cost efficiency, 3D printed molds are transforming how businesses approach manufacturing and casting processes.
In summary, the advantages of using 3D printed molds for casting processes are profound. They empower manufacturers to innovate while maintaining control over costs and production timelines, allowing for a more adaptable approach to market needs.
Challenges Faced in 3D Printed Molds
The integration of 3D printing into the production of molds has transformed manufacturing practices. However, it is essential to acknowledge the challenges that come with this technology. These challenges can influence the overall effectiveness, quality, and viability of 3D printed molds. Addressing these issues is critical for advancing the field and ensuring that the benefits of 3D printing can be fully leveraged.
Material Limitations
One significant challenge in the use of 3D printed molds is the limitations of available materials. The properties of materials used in 3D printing often do not align with the requirements for durable molds in casting processes. For instance, while thermoplastics are common in additive manufacturing, they may not withstand the high temperatures seen in certain metal casting processes. Furthermore, not all materials offer suitable mechanical strength or thermal stability, potentially leading to mold failure during operation.
Consequently, identifying materials that are not only compatible with 3D printing but also suitable for end-use in casting remains a pursuit for many professionals in the field.
Surface Finish and Tolerances
Surface finish is another challenge that users of 3D printed molds often face. The layer-by-layer nature of 3D printing frequently results in a rougher finish compared to traditional mold-making methods. Such finishes may require additional post-processing steps to achieve the desired smoothness. Furthermore, maintaining precise tolerances is crucial in mold design, as even minor inaccuracies can lead to product defects. Tolerances can vary significantly among different 3D printing technologies, which means careful calibration and optimization during the design and printing phases is necessary.
It is crucial for manufacturers to implement rigorous testing and quality assurance protocols to mitigate these concerns and deliver molds that meet specific standards.
Scale and Production Volume Constraints
The scalability of 3D printing technology also presents challenges, especially when aiming for large-scale production. Although 3D printing allows for rapid prototyping and customization, it may not always be the most efficient option when large quantities of molds need to be produced. The time taken for each print cycle can become a bottleneck, particularly when high-volume production is required. Additionally, certain 3D printers may have limitations on the size of the mold they can create, further complicating matters for larger projects.
These constraints necessitate a thorough analysis of production needs and a comparison with traditional manufacturing methods to determine the most effective approach.
In summary, while 3D printing offers numerous advantages, it is essential to navigate the challenges it presents to fully harness its potential in mold making. The limitations in materials, surface finish and tolerances, and production scalability are critical factors that need careful consideration.
Future Prospects of 3D Printed Molds
The future prospects of 3D printed molds signify a transformation in casting processes and manufacturing practices. As industries strive for heightened efficiency, lower costs, and innovative designs, the relevance of this topic becomes increasingly prominent. The advancements in 3D printing technologies are not simply a passing trend; they are evolving into a cornerstone of modern production.
Technological Advancements
Technological advancements in 3D printing continue to reshape the landscape of mold making. New materials and processes are emerging, offering enhanced performance and greater adaptability in mold design. For example, the introduction of high-temperature resistant polymers allows for the creation of molds that can withstand the rigors of casting better than conventional materials.
Moreover, artificial intelligence and machine learning are beginning to play a role in optimizing mold designs. These technologies can analyze performance data and suggest modifications that can lead to improved efficiency and quality in production.
Some notable advancements include:
- Improved material properties: Enhanced strength, durability, and thermal stability in 3D printed molds.
- Rapid prototyping capabilities: The speed at which molds can be created minimizes downtime and streamlines the manufacturing process.
- Hybrid manufacturing techniques: Combining traditional techniques with 3D printing to leverage the strengths of both methods can lead to innovative product designs.
These advancements are important not just for factory settings; they can also empower small businesses and startups with opportunities previously reserved for larger manufacturers.
Sustainability Considerations
Sustainability is becoming a critical conversation in manufacturing disciplines. The shift towards 3D printed molds carries substantial implications for environmental considerations. 3D printing, inherently an additive process, reduces material waste compared to subtractive manufacturing methods. Traditional mold making often results in significant scrap material, whereas 3D printing allows for precise control over material usage.
Key sustainability benefits include:
- Reduced energy consumption: 3D printing techniques often consume less energy compared to traditional methods.
- Material recycling opportunities: Certain 3D printing materials can be recycled, further minimizing environmental impact.
- Location flexibility: On-demand production can be conducted close to the point of use, potentially reducing transportation emissions.
Furthermore, businesses adopting sustainable practices can enhance their market position. Consumers increasingly favor options that prioritize environmental responsibility, leading to new market opportunities in the future.
"Sustainable manufacturing is not just a choice; itβs becoming a necessity in todayβs market."
As we look forward, the integration of 3D printed molds into manufacturing not only represents a potential for operational efficiency but also a commitment to environmental stewardship.
Overall, the future of 3D printed molds in casting seems poised for growth, driven by continuous technological advancements and a pressing need for sustainable practices in the industry.
Epilogue
The conclusion of this article encapsulates the multifaceted importance of 3D printed molds in modern casting processes. As we have discussed, 3D printing technology significantly transforms traditional manufacturing practices by offering customization, efficiency, and sustainability benefits. It enables manufacturers to produce molds with intricate designs that were once deemed impossible with conventional methods. This capacity for innovation enhances the scope of product development across various industries.
Summarizing Key Insights
- Customization: 3D printed molds allow for tailored designs to meet specific product requirements. Each mold can be uniquely designed for various applications, reducing the need for multiple inventory stocks.
- Efficiency: Reduced lead times in mold production directly impact overall manufacturing cycles. With faster production, companies can respond more readily to market demands.
- Material Versatility: Utilizing a range of materials like thermoplastics and photopolymers can optimize mold effectiveness, allowing for a wide array of casting materials.
- Sustainability: 3D printed molds often generate less waste than traditional mold-making processes. This reduction in waste aligns with the increasing pressing need for eco-friendly manufacturing practices.
The Impact on Casting and Manufacturing
The shift to 3D printed molds heralds significant changes in the casting industry. Traditional methods of mold-making are often time-consuming and resource-intensive. In contrast, 3D printed molds simplify production while enhancing precision. The overall impact includes:
- Cost Reduction: Lower production costs arise from streamlined processes, allowing smaller businesses to participate in the market.
- Innovation in Design: The ability to produce complex structures opens new avenues for creativity in product development.
- Rapid Prototyping: The quick turnaround permits rapid testing and iteration of designs, which is invaluable for innovation.
- Enhanced Collaboration: Cross-disciplinary collaboration between engineers and designers is encouraged, leading to more innovative outcomes.