Exploring Aluminum and Scandium: Benefits and Uses
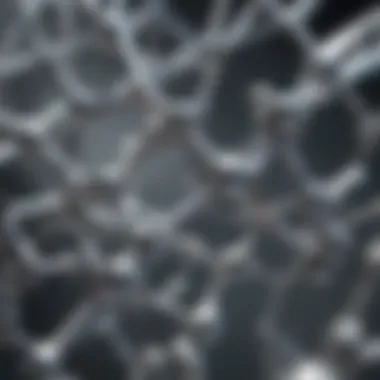
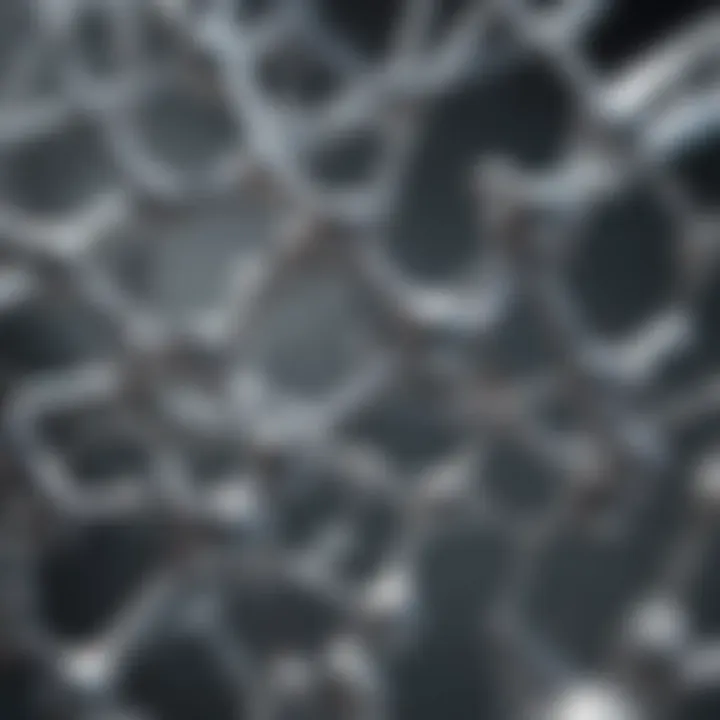
Intro
Understanding the intricate relationship between aluminum and scandium is crucial for advancements in metallurgy and materials science. Both elements hold unique properties that, when combined, offer intriguing advantages over conventional materials. This intersection has spurred research and development aimed at optimizing their synergy for various applications—from aerospace to sporting goods. In the following sections, we delve into the specific characteristics of each element, their respective roles, and the innovative possibilities that emerge from their interaction.
Research Methodology
Description of Research Design and Approach
The research conducted for this study unfolded in a systematic manner, employing a mixed-methods approach. This included both qualitative and quantitative data collection to ensure a well-rounded understanding of the aluminum and scandium interplay. A deep dive into case studies supplemented by laboratory experiments laid the groundwork for a comprehensive analysis.
Materials and Methods Used in the Study
- Sample Preparation: Pure aluminum and scandium samples underwent rigorous preparations. Alloy compositions were meticulously controlled to evaluate the outcomes accurately.
- Experimental Techniques: Various methods, such as X-ray diffraction and scanning electron microscopy, were used. These techniques helped in observing the microstructural features of the alloys created during the study.
- Data Collection: The tensile strength, ductility, and fatigue resistance were measured using standard mechanical testing procedures. This quantifiable data formed the backbone of our interpretation.
Discussion and Interpretation
Interpretation of Results in the Context of Existing Literature
The results indicate that the addition of scandium to aluminum can enhance mechanical properties significantly. Research aligns with previous studies, suggesting improvements in strength-to-weight ratios, which are critical for industries like aerospace. The synergies discovered prompt a re-evaluation of how these materials can be employed more effectively, opening doors to ambitious engineering solutions.
Implications for Future Research or Practical Applications
The combined properties of aluminum and scandium show promise not only in theoretical applications but also in practical scenarios. Future research should focus on scaling production methods and examining the long-term stability of scandium-alloyed aluminum in extreme conditions, like high temperature or underwater environments. Additionally, the economic implications, such as cost reduction in aerospace manufacturing, warrant attention.
"Understanding the blend of aluminum and scandium is not merely an academic exercise; it holds potential to redefine material applications across various fields."
The findings encapsulate a momentous step in materials science, making a case for broader adoption of scandium in aluminum alloys. Continued exploration will significantly impact both technology and manufacturing processes.
Preamble to Aluminum and Scandium
The realm of materials science is vast and intricate, but a spotlight often shines on aluminum and scandium due to their unique properties and growing applications. This section serves as an entry point for understanding these two elements. Both metals play a crucial role in modern metallurgy, with significant implications across various industries. Their pairing, especially in alloy forms, opens doors to innovations that can shift paradigms in technology and manufacturing.
Overview of Aluminum
Aluminum is one of the most abundant metals in the Earth’s crust, making up about 8% of it. Its lightweight nature, coupled with excellent corrosion resistance, makes it a cherished material in areas ranging from aerospace to construction. With a silvery sheen and a low density, aluminum is often preferred for applications requiring a strong yet lightweight component.
In terms of properties, aluminum is non-toxic and recyclable, which enhances its appeal in the age of sustainability. Its transformation through processes like extrusion and alloying allows for extensive versatility. Typically, aluminum is alloyed with elements like copper and zinc to improve its strength, but recent advancements suggest that incorporating scandium could further increase its performance.
Overview of Scandium
Scandium, on the other hand, is much less abundant and is classified as a rare earth metal. Although it may not enjoy the same level of fame as aluminum, its role is growing in importance. The metal exhibits unique characteristics. For instance, it is notable for its ability to enhance the strength and stability of aluminum alloys without significantly increasing weight. Scandium has a melting point higher than aluminum, lending added thermal stability to the mixtures in which it is included.
Not just limited to metallurgy, scandium is also being explored in various high-tech applications, such as in solid oxide fuel cells and in powerful lighting solutions due to its remarkable luminescent properties. By examining scandium's interplay with aluminum, crucial opportunities for advancement can be understood. The knowledge of these elements sets the stage for investigating their combined attributes and the expansive landscapes they can influence.
Chemical Properties of Aluminum
Understanding the chemical properties of aluminum is crucial for evaluating its role in various applications, especially when considering its alloying with scandium. Aluminum has a distinctive atomic structure and unique characteristics that contribute significantly to its versatility in metallurgy.
Atomic Structure and Characteristics
Aluminum is characterized by its atomic number 13 and a relatively compact atomic radius of 143 picometers. Instead of being a dense metal, it holds a favorably low density of about 2.7 g/cm³. This quality allows for lightweight constructions that can lead to energy savings during transportation and usage across a myriad of industries.
The electronic configuration of aluminum is [Ne] 3s² 3p¹, which indicates it has three valence electrons. These electrons play a pivotal role in dictating the behavior of aluminum when it interacts with other elements, particularly scandium. The ability of aluminum to form a protective oxide layer upon exposure to air is significant. This layer not only imparts corrosion resistance but also facilitates a myriad of bonding interactions with scandium, leading to enhanced mechanical properties.
Reactivity and Oxidation Behavior
Aluminum is generally known for its moderate reactivity. It resists corrosion due to the formation of a passivation layer of aluminum oxide, which can be both a blessing and a curse. On one hand, this oxide layer protects the metal underneath from further oxidation; on the other hand, it can make welding and other metallurgical processes somewhat challenging due to a potential need to remove this barrier.
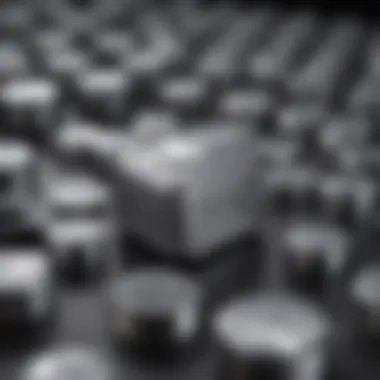
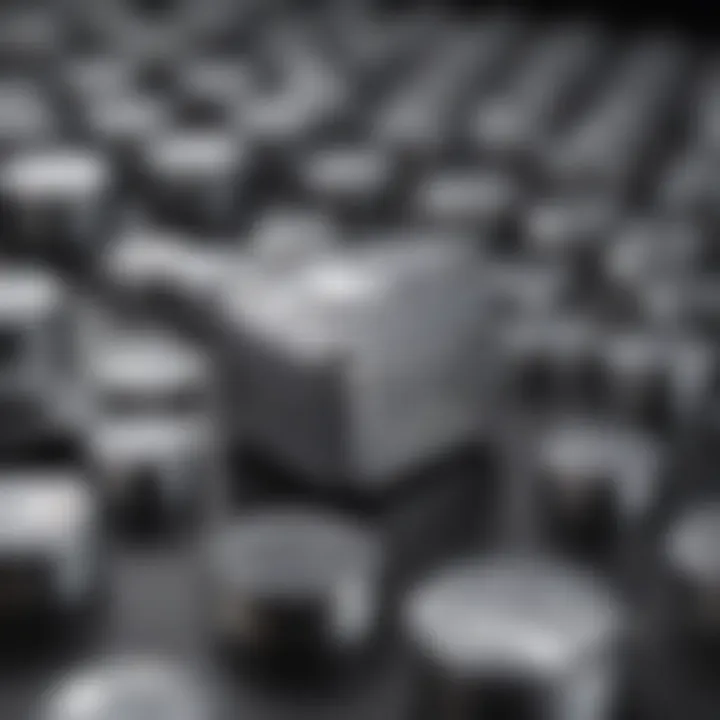
When considering the chemical behavior of aluminum, understanding its oxidation states is essential. Aluminum typically exhibits a +3 oxidation state in its compounds, leading to a wide range of applications, from aluminum oxide used in abrasives to aluminum sulfate in chemical processes.
The ability of aluminum to react with alkali and acids adds further utility in various applications, especially in the creation of aluminum-scandium alloys. These alloys benefit from aluminum's propensity to bond with different elements, allowing for tailored mechanical properties suitable for specific demands in aerospace and automobile industries.
"Aluminum’s reactivity, while often regarded as a limitation, serves as a catalyst for innovation in combining materials such as scandium to achieve remarkable engineering feats."
In summary, aluminum's atomic structure and oxidation behavior significantly inform its application potential. Recognizing how these chemical properties interact with scandium opens pathways to developing advanced materials that promise higher performance in various technological sectors.
Chemical Properties of Scandium
Understanding the chemical properties of scandium is crucial in assessing its performance and utility in various applications, particularly when combined with aluminum. Scandium, a transition metal, brings a unique blend of characteristics that enhance the alloys' properties, making them suitable for advanced engineering applications. With a relatively low density and a propensity for high melting points, scandium is known for contributing strength and stability in the mixtures it forms with aluminum. It assists in reducing the overall weight of components while retaining structural integrity.
Atomic Characteristics and Position in the Periodic Table
Scandium's atomic number is 21, placing it in group 3 of the periodic table. This positioning signifies its classification among the lanthanides and actinides. The electron configuration of scandium is [Ar] 3d¹ 4s², indicating that it has two electrons in the 4s subshell and one in 3d. This arrangement plays a vital role in its chemical behavior and its ability to form various compounds.
Scandium possesses a specific atomic radius compared to its neighbors in the periodic table, which enhances its reactivity and capacity to bond with other elements. The trivalent state is notably prevalent, wherein scandium tends to lose three electrons, showcasing its behavior as a metal with potential for forming ionic bonds. As such, its placement is not merely of academic interest; it underscores scandium's role in producing lightweight yet sturdy materials crucial for applications in aerospace and automotive industries.
Oxidation States and Compounds
Scandium typically exhibits oxidation states of +3, predominantly in its compounds. This consistent oxidation state is a key feature contributing to its utility in alloy formation. The stability offered by scandium in the +3 state allows for predictable interactions with aluminum, leading to enhanced alloy performance.
Common compounds include scandium oxide (Sc2O3) and scandium fluoride (ScF3), which demonstrate the element’s reactivity with oxygen and fluorine respectively.
"Scandium's affinity to form stable compounds underscores its significance in metallurgical processes and material science, allowing researchers to leverage its unique properties for innovative applications."
These properties facilitate the development of aluminum-scandium alloys, which are not only lighter than traditional alloys but also exhibit improved mechanical properties, like increased strength and corrosion resistance. Understanding these oxidation states aids researchers and industrial professionals when developing new alloying strategies that maximize performance while minimizing weight, thus anticipating the demands of modern industries.
The Synergy of Aluminum-Scandium Alloys
The combination of aluminum and scandium presents a remarkable opportunity in the field of materials science. The real beauty lies in what happens when these two elements are synthesized to create aluminum-scandium alloys. This merging not only enhances the properties of aluminum but also opens the door to numerous applications across various industries. Understanding this synergy is essential as it can lead to advancements that contribute significantly to technological progress and economic growth.
Combining Elements: Benefits and Challenges
When you take aluminum—a lightweight, versatile metal known for its corrosion resistance—and introduce scandium into the mix, you're set to produce alloys featuring considerable strength and improved durability.
Benefits:
- Increased Strength: Aluminum-scandium alloys have enhanced mechanical properties, particularly tensile strength. This is crucial in applications where weight savings are vital, like in aviation and automotive industries.
- Improved Weldability: Alloys that include scandium typically exhibit better weldability than traditional aluminum, enabling more efficient manufacturing processes.
- Resilience to Fatigue: The fatigue resistance of these alloys makes them suitable for applications with repeated stress cycles, reducing the risk of failure.
- Thermal Stability: Scandium allows these alloys to maintain their strengths at elevated temperatures, widening their potential uses.
Challenges:
- Cost of Scandium: Scandium is much rarer and more costly than aluminum, which can lead to higher initial production costs for these alloys.
- Processing Difficulties: Creating aluminum-scandium alloys requires precise control over the manufacturing process to fully realize the benefits. This can complicate the production procedures.
- Limited Availability: Since scandium is not widely produced, securing a consistent supply chain can be a hurdle.
The combination of these elements allows for strong but lightweight materials, but navigating the challenges will be key in leveraging their benefits efficiently.
Mechanical Properties and Enhancements
The mechanical properties of aluminum-scandium alloys stand out when compared to their aluminum counterparts.
- Higher Yield Strength: Yield strength can be significantly enhanced which is paramount for structures that need to be light yet strong.
- Ductility: While maintaining strength is important, the ability of these alloys to deform without breaking adds to their application potential, particularly in automobile manufacturing, where components must absorb impact.
- Toughness: The toughness of these alloys ensures that while they are lightweight, they can withstand impacts and stress without succumbing to failure—a vital aspect in areas like aerospace equipment.
“Harnessing the unique properties of aluminum and scandium through alloying, one can achieve a balance of strength, ductility, and durability unavailable in traditional materials.”
Applications of Aluminum-Scandium Alloys
In recent years, the applications of aluminum-scandium alloys have gained significant attention across various industries. This trend is mainly due to the unique blend of properties these alloys infuse, providing notable advancements in specific fields such as aerospace, automotive, and even sporting equipment. The combination of aluminum's lightweight and corrosion resistance with scandium's remarkable ability to enhance mechanical properties creates opportunities that resonate well beyond traditional uses of aluminum.
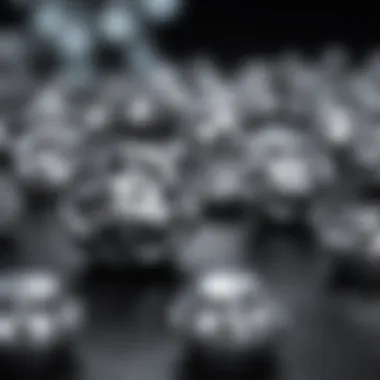
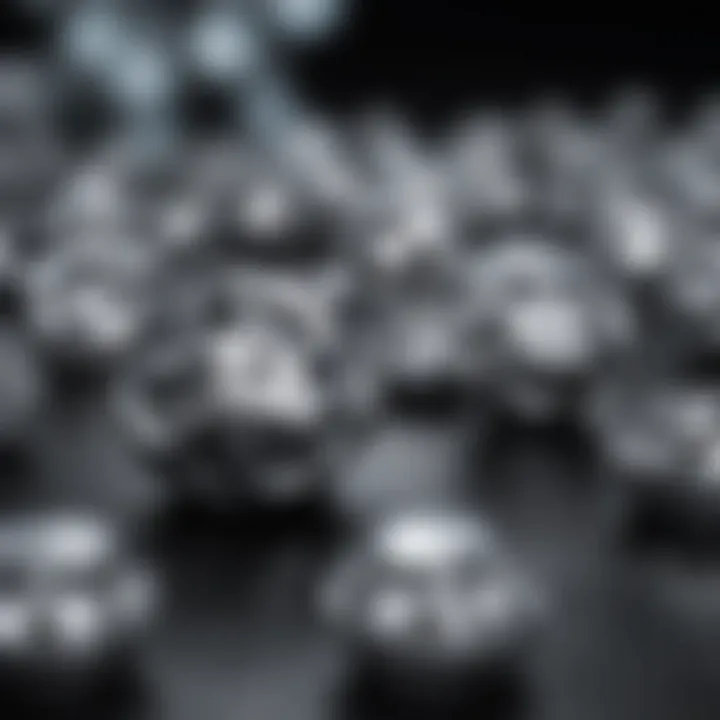
Aluminum-scandium alloys stand out largely due to their unique mechanical properties that lead to superior performance criteria. This blend not only decreases weight and improves strength but also enhances weldability, making them attractive for numerous sectors. Their utility in modern applications addresses key consideration such as sustainability and efficiency, intrinsic to evolving industrial standards.
Aerospace and Aviation Industry
In aerospace, the demand for lighter and stronger materials is relentless. Aluminum-scandium alloys meet this demand admirably, providing significant weight savings essential for fuel efficiency and payload capacity. These alloys are prized for their high strength-to-weight ratio, a critical factor when considering aircraft design.
By integrating aluminum-scandium into airframe design, manufacturers achieve substantial reductions in both operational costs and emissions. The aerospace sector relies heavily on the enhanced fatigue resistance presented by these alloys, allowing for the creation of components that endure harsh environmental conditions without premature failure.
Moreover, current projects, such as the development of next-gen aircraft structures, incorporate aluminum-scandium due to its excellent weldability, enabling streamlined fabrication methods. This is a marked departure from conventional methods that often faced limitations when it came to joining dissimilar metals.
Automobile Manufacturing
The automobile industry is no stranger to the push for lighter materials. Aluminum-scandium alloys fit the bill perfectly. With the increasing emphasis on fuel efficiency and lower emissions standards, manufacturers are pushed to innovate in materials that promote weight reduction without sacrificing durability.
These alloys facilitate greater flexibility in design while providing the mechanical stability necessary for automotive applications. This means that manufacturers can craft lighter, more efficient vehicles without compromising safety or performance. Furthermore, aluminum-scandium alloys exhibit improved resistance to corrosion, thereby extending the lifespan of automotive components.
In a nutshell, integrating aluminum-scandium alloys into vehicle construction can lead to a shift in market dynamics, influencing everything from production costs to consumer preferences towards eco-friendlier automobiles.
Sporting Equipment and Beyond
When it comes to sporting goods, the demand for high-performance, lightweight materials is crucial. Aluminum-scandium alloys have made their mark in equipment such as bicycles, baseball bats, and even custom golf clubs. The properties of these alloys contribute to not just strength but also improved handling and responsiveness, key elements for athletes at all levels.
For instance, in the cycling world, frames constructed from aluminum-scandium provide the perfect balance of rigidity and lightweight characteristics that avid cyclists crave. Bats made from these materials tend to deliver higher performance during swings due to their enhanced strength, making them a preferred choice among professionals and amateurs alike.
"Lightweight, durable, and flexible – the essence of performance sports equipment often hinges on the use of aluminum-scandium alloys."
Ultimately, the applications of aluminum-scandium alloys extend far beyond initial expectations, with industries ranging from aerospace to sports equipment uncovering the tangible benefits embedded in this unique material synergy. As the exploration continues, further advancements and discoveries are likely to emerge, solidifying their place in the future of material science.
Economic Implications of Aluminum-Scandium Usage
The economic aspect of combining aluminum and scandium extends well beyond mere numbers on a balance sheet. Understanding the financial implications of using aluminum-scandium alloys is colossal for stakeholders in various industries. This section delves into the market dynamics surrounding these materials, the pricing factors at play, and a rigorous cost-benefit analysis, providing clarity to those navigating this intersection of materials science and economics.
Market Dynamics and Pricing Factors
Aluminum and scandium market dynamics are intricate, influenced by various economic factors such as supply, demand, and production costs. With aluminum being one of the most widely used metals globally, its price is subject to fluctuations based on global markets. On the other hand, scandium is rarer and commands a higher price due to limited sources and the complexities involved in its extraction and processing.
Several key factors influence pricing:
- Supply Chain Constraints: The extraction process for scandium can be costly and environmentally taxing. Thus, the limited availability impacts prices significantly. This contrasts starkly with aluminum, which is more abundant and widely mined.
- Global Demand: Industries such as aerospace and automotive are increasingly adopting aluminum-scandium alloys for their superior properties. When demand from these sectors rises, it pushes prices up for both metals.
- Technological Advancements: As methods improve for alloy production and scandium integration, costs may stabilize, potentially making these alloys more economically viable.
- Geopolitical Factors: Import/export regulations, tariffs, or trade relationships can also affect the cost and availability of both aluminum and scandium.
As the market continues to evolve, stakeholders must stay aware of these dynamics to make informed decisions on investments and procurement.
Cost-Benefit Analysis in Manufacturing
When considering aluminum-scandium alloys for manufacturing, undertaking a comprehensive cost-benefit analysis is essential. This process evaluates the overall financial impact against potential benefits, an exercise that has implications far beyond immediate expenses.
Benefits of Utilizing Aluminum-Scandium Alloys:
- Lightweight Properties: The reduced weight of components can lead to savings in fuel and energy consuption, particularly in aerospace applications. This efficiency translates directly into operational cost savings over time.
- Increased Strength and Durability: Scandium enhances the mechanical properties of aluminum. The longevity of products made with these materials often results in lower long-term maintenance and replacement costs.
- Competitive Advantage: Companies that adopt advanced materials can leverage this for improved performance and differentiation in crowded markets, attracting customers and increasing their market share.
Costs to Consider:
- Initial Cost of Raw Materials: The price of scandium is significant compared to aluminum. Manufacturers need to determine if the performance enhancements justify the costs.
- Processing Expenses: The alloying process requires specialized techniques, and the associated costs must be calculated carefully.
- Production Risks: Entering new material territories may come with inherent risks, including manufacturing trials or failures that lead to additional costs.
In summary, the economic implications of employing aluminum-scandium alloys are substantial and multifaceted. By analyzing both the market dynamics and the cost-benefit ratio, stakeholders can position themselves for strategic advantages in the ever-evolving landscape of materials science.
Environmental Considerations
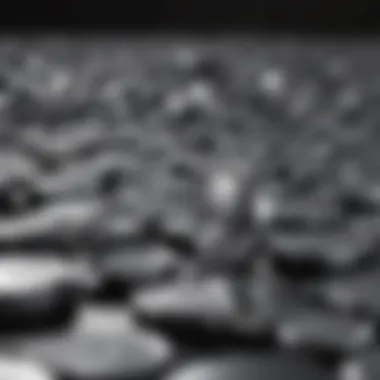
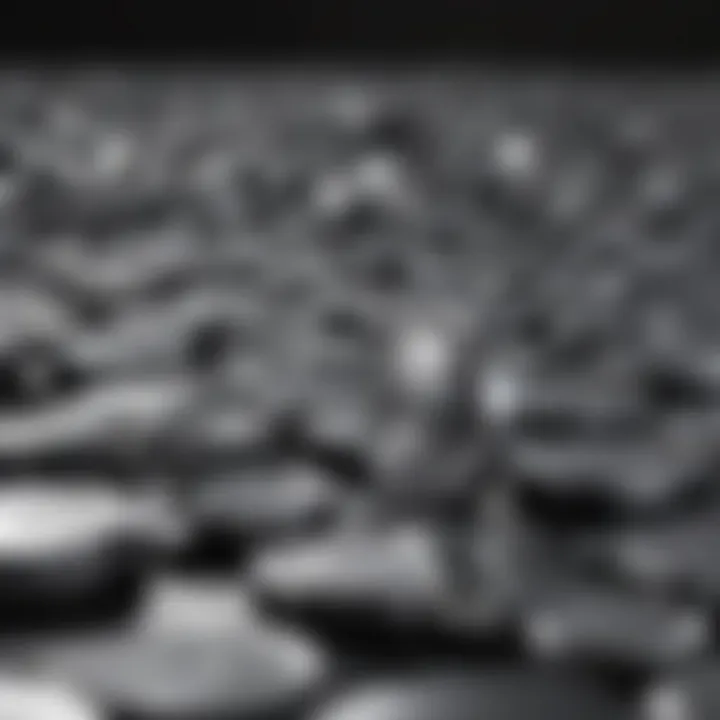
Understanding the environmental implications when utilizing aluminum and scandium is crucial in today's world, especially as industries strive to become more sustainable. The extraction and production of metals come with their fair share of challenges, including resource depletion, habitat destruction, and pollution. Thus, it is vital to delve into specific aspects, such as sustainability in material production and the recycling processes that significantly influence the lifecycle of these metals.
Sustainability in Material Production
Sustainability in the production of aluminum and scandium is not just a buzzword; it's a necessity. Here are some key elements to consider:
- Efficiency of Resource Use: Aluminum is already known for its excellent recyclability, but the way it is produced can greatly affect its environmental footprint. Choosing the right form of primary production, as well as incorporating scandium into the equation, can enhance the performance and efficiency of the resulting alloys.
- Energy Consumption: The production process for both metals is energy-intensive. However, advancements in technology aim to reduce energy consumption. For instance, using renewable energy sources, such as solar or wind, during the smelting of aluminum can drastically cut down carbon emissions.
- Biodegradable Alternatives: Integrating biodegradable fillers and composites into aluminum-scandium alloys could reduce overall environmental impact, leading to even more sustainable products. This could be particularly meaningful in reducing waste in applications ranging from automotive parts to aerospace components.
Sustainability isn't merely about conserving resources; it’s about responsibly addressing the full circle of material production, from sourcing to disposal.
Recycling and Lifecycle Analysis
Recycling offers a promising avenue to minimize the environmental impacts associated with aluminum and scandium. Here’s why:
- Aluminum’s High Recyclability: Unlike many materials, aluminum can undergo recycling indefinitely without degrading its properties. Each cycle of melting down and reforming aluminum consumes about 5% of the energy required for primary production. This capacity significantly lowers the carbon footprint of aluminum products.
- Scandium Recycling: While scandium is less commonly recycled compared to aluminum, its value is increasingly recognized. The recovery of scandium from scrap alloys or production waste could become a viable method as demand grows. Studies are being conducted to develop effective recycling processes that do not compromise the purity and efficacy of scandium in the alloy.
- Lifecycle Assessment: Evaluating the lifecycle of aluminum-scandium alloys can provide insights into their environmental impact. This analysis considers everything from extraction and production through to recycling and disposal. A comprehensive lifecycle analysis can inform manufacturers on ways to improve their practices and minimize harm to the environment.
"The path to sustainability for aluminum and scandium is not merely paved with technological advancements but also with a shift in mindset towards responsible material management."
As industries become more aware of their environmental responsibilities, the recycling initiatives and especially lifecycle analyses will become vital tools in shaping the future strategies of aluminum and scandium use across multiple sectors. Adopting sustainable practices in both material production and waste management can foster a more balanced interaction with our planet.
Future Directions in Research and Development
The exploration of aluminum and scandium alloys is at a critical juncture, as research continues to grow in importance given the escalating demand for advanced materials across numerous industries. Understanding the future directions in this field not only facilitates the adaptation to changing technological needs but also ensures sustainability. There is a clear link between the advancement of knowledge and the practical applications that follow, making this an essential area of focus.
Innovative Research on Aluminum-Scandium Alloys
In recent years, researchers have turned a sharper focus on aluminum-scandium alloys due to their unique properties. These materials, known for their lightweight and strength, have led to an expansion of interest in various research endeavors.
Ongoing studies are particularly looking into enhancing the thermal resistance of these alloys, enabling their use in more extreme environments, such as in aerospace where conditions often fluctuate drastically. Another intriguing aspect is the aim to improve the alloys' weldability. Traditionally, aluminum-scandium combinations have faced challenges when welded. By targeting the underlying microstructural transformations during processing, scientists are working to overcome these setbacks.
Innovations in the realm of aluminum-scandium alloys could very well redefine the parameters of material performance across disciplines, from transportation to construction.
Moreover, collaborative research efforts between academia and industry could accelerate developments significantly. When expert applications of metallurgical knowledge meet real-world demands, the results can be groundbreaking.
The potential for novel applications in various sectors like marine, automotive, and clean energy systems is on the horizon, with research poised to create materials with tailored properties specifically suited for each application. The future is far from static; it's dynamic, full of promise and new avenues for exploration.
Potential New Applications and Markets
With the foreseeable growth of innovative aluminum-scandium alloys, the potential markets are equally expanding. The aerospace sector remains a primary benefactor, where reducing weight directly translates to fuel efficiency— a critical factor in operational costs. Beyond aerospace, the automotive industry is witnessing a push towards lighter vehicles, and aluminum-scandium alloys could be part of the solution to meet these demands for efficiency and sustainability.
- Marine applications are also blooming as these alloys demonstrate increased resistance to corrosion, particularly crucial for seafaring vessels.
- Energy generation and storage methods are ripe for these alloys, especially in wind and solar technologies where material durability and resistance directly impact energy production efficacy.
Additionally, sporting goods industries are eyeing this combination due to its weight advantages without compromising strength, ideal for high-performance gear used in various sports.
In summary, embracing new methodologies in research and understanding market needs will not only enhance material qualities but will also spearhead growth across diverse sectors. The integration of aluminum and scandium fundamentally represents a step towards a more innovative future in material sciences.
The End
The intersection of aluminum and scandium lies at the heart of modern metallurgy. Understanding how these two metals complement each other has significant implications across various sectors. In an increasingly competitive market, harnessing the specific properties of aluminum-scandium alloys can unlock new potentials in efficiency and performance.
Summarizing Key Insights
Through the course of this article, several key insights have emerged:
- Chemical Synergy: Aluminum and scandium combined produce alloys with improved strength-to-weight ratios, making them suitable for critical applications in aerospace and automotive industries.
- Economic Impact: The usage of these alloys signals a shift towards more sustainable practices, potentially reducing production costs and maximizing material efficiency.
- Environmental Considerations: The emphasis on recycling and lifecycle analysis points to a future where material production is aligned with environmental goals.
These insights illustrate not only the technical advantages of aluminum and scandium alloys but also highlight a growing need for sustainable innovation in material science.
Final Thoughts on the Future of Aluminum and Scandium in Science
Looking ahead, the future of aluminum and scandium in scientific research seems promising. As we face pressing challenges in the field of materials science, ongoing studies may reveal novel applications. For instance, the realms of nanotechnology and structural engineering could greatly benefit from further exploration of these alloys.
Moreover, emerging industries, such as renewable energy technologies, may open new markets for aluminum-scandium combinations, creating avenues for exploratory research that bridges various fields. Such developments will not only enhance the performance of existing structures but could also lead to breakthroughs in new materials that redefine standards.
In summary, the interplay between aluminum and scandium not only enriches our understanding of metallurgy but also acts as a catalyst for innovation in science and technology.