Exploring Aluminium: Forms, Uses, and Innovations
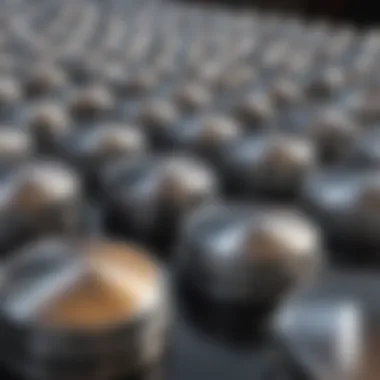
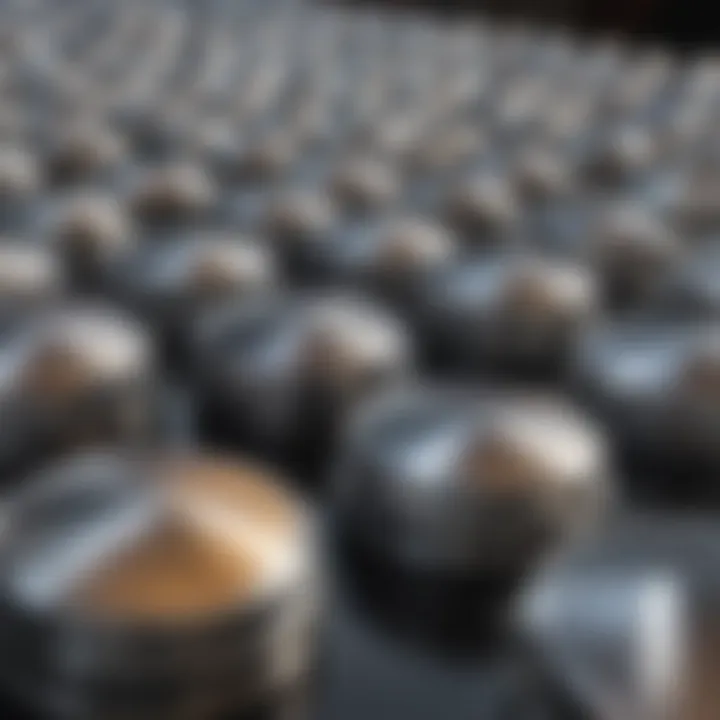
Intro
Aluminium is a metal that finds itself at the heart of countless industries and applications, from aeronautics to architectural design. This lightweight, yet sturdy metal is known for its versatility and unique properties, which allow it to be molded into various forms. The aim of this exploration is not merely to list these forms but to comprehensively discuss them in the context of their applications, properties, and manufacturing processes.
By navigating through the maze of aluminium alloys, shapes, and surface treatments, we aim to uncover the multifaceted roles that this remarkable metal plays in our modern world. We will also address the environmental aspects associated with its production and recycling, ensuring that our discussion is well-rounded.
Through this article, we will shine a light on how aluminium adaptation has significant implications for industries and environments alike. Understanding these complex layers is particularly relevant for students, researchers, and professionals keen on remaining at the forefront of aluminium technology and applications.
Research Methodology
Description of Research Design and Approach
This study undertakes a qualitative approach to primarily gather insights on the various forms of aluminium. The research draws from existing literature and industry reports to create a comprehensive picture of current knowledge and trends. We also explore case studies where aluminium's utility has demonstrated innovation and adaptability.
Materials and Methods Used in the Study
The exploration utilizes a combination of resources including:
- Academic journals from materials science and engineering disciplines.
- Industry whitepapers outlining advancements in aluminium technology.
- Interviews with professionals from the fields of metallurgy and manufacturing.
- Data and statistics on aluminium use and recycling processes from reputable organizations, such as the International Aluminium Institute.
This array of sources ensures a robust foundation for the discussion that follows, leading to a greater understanding of aluminium’s multifarious forms.
Discussion and Interpretation
Interpretation of Results in the Context of Existing Literature
The research sheds light on how aluminium's diverse forms cater to specific industry needs. For instance, while some alloys are employed in aviation for their high strength-to-weight ratios, others are utilized in packaging due to their non-toxic nature. The interplay of physical properties—like conductivity, malleability, and resistance to corrosion—makes it indispensable in numerous sectors.
Implications for Future Research or Practical Applications
Moving forward, it is crucial that future research seeks to optimize the eco-friendliness of aluminium production. Innovations in recycling methods could lead to vastly reduced energy consumption and waste.
Furthermore, as industries pursue sustainable practices, the role of aluminium in environmental conservation as a recyclable material should be emphasized. There is immense potential for advancements in aluminium applications, especially in lightweight automotive designs and renewable energy sectors, like solar panels.
In summary, aluminium is not merely a material; it is a participant in the story of modern innovation and environmental strategy.
Overall, the continuous study of aluminium forms will further unveil their potential and push the boundaries of what we consider possible in using these materials.
Preface to Aluminium
The exploration of aluminium as a material is not just about its physical properties; it’s a journey into understanding its historical significance and chemical characteristics that shape our modern world. This section serves as the gateway to grasping how aluminium influences various fields, from aerospace to packaging, and everything in between.
Including an understanding of aluminium in industry and art can reveal much about human ingenuity and the materials we utilize in our everyday lives.
Historical Context
Aluminium's history is quite remarkable. Discovered in the early 19th century, its first extraction in a pure form occurred in 1825 by Hans Christian Ørsted, paving the way for future applications. However, it wasn't until the late 19th century that advances in electrolysis made aluminium production more feasible. By the end of the 1800s, aluminium was viewed as an incredibly precious material, even more expensive than gold at the time. This makes us realize how far we have come in terms of technology and industrial processes.
During the mid-20th century, with the advent of the Bayer process for refining bauxite to produce aluminium oxide, the production of this metal skyrocketed. This period marked the transition of aluminium into a common household metal due to the growing demand in sectors like transportation and construction. Its lightweight nature and resistance to corrosion made it highly desirable.
Physical and Chemical Properties
Aluminium is known for its unique set of properties that make it suitable for a multitude of applications. It’s lightweight yet incredibly strong, with a density of about one-third that of steel. This property is particularly beneficial in aerospace, where reducing weight can enhance fuel efficiency and performance. It also boasts excellent thermal conductivity, which is advantageous in cooking and electronic applications.
Chemically, aluminium is highly reactive but quickly forms a protective oxide layer when exposed to air, thereby minimizing further corrosion. This layer makes aluminium durable in harsh environments, lending itself well to outdoor structures and automotive parts.
Its malleability and ductility allows it to be shaped into various forms without breaking, which is vital in manufacturing processes. This versatility means aluminium finds a home in everything from cans to airplane wings.
In summary, the importance of understanding aluminium lies not just in its properties but also in the way it has shaped industries historically and continues to evolve in the modern era. Whether it's being used in a sleek airplane or in the kitchen, aluminium significantly impacts our day-to-day lives.
Classification of Aluminium Forms
Understanding the classification of aluminium forms is crucial as it provides a framework through which the various types of aluminium can be appropriated for specific applications. The classification highlights distinctions in physical and chemical properties, ensuring that manufacturers, engineers, and designers can make informed choices regarding the form of aluminium most suited for their needs. Each form, whether pure aluminium or its alloys, embodies unique characteristics that play a pivotal role in the performance and durability of the end product.
Pure Aluminium
Pure aluminium is a marvel of simplicity and utility. Characterized by its high ductility and resistance to corrosion, this form of aluminium is often harnessed in applications where weight savings and minimal conductivity are paramount. Its native state is relatively soft compared to alloys. This softness can limit its use in structural applications; however, it finds a prominent role in the production of electrical conductors and appliances, where high corrosion resistance and low density are favorable.
Aluminium Alloys
Aluminium alloys are a significant segment in the classification of aluminium, drawing attention due to their enhanced properties, making them desirable across various industries.
Types of Aluminium Alloys
The landscape of aluminium alloys is rich and diverse, classified primarily into two categories: wrought and cast alloys. Wrought alloys are mechanically worked into their desired shapes, offering refined characteristics and improved strength. On the other hand, cast alloys are melted and poured into molds—an impactful method that allows for intricate designs. One unique attribute of wrought alloys, such as the 6061 alloy, is its excellent machinability. This feature not only renders it a popular choice for intricate components in the aerospace industry but also aids in minimizing production costs.
Properties of Alloys
The properties of aluminium alloys greatly vary, influenced by the specific elements alloyed with the aluminium. For instance, when copper is added, the resulting alloy often exhibits improved strength, making it suitable for applications where lightweight materials are critical. In contrast, alloys with magnesium are favored for their outstanding weldability. Understanding these properties is foundational for selecting materials for particular applications.
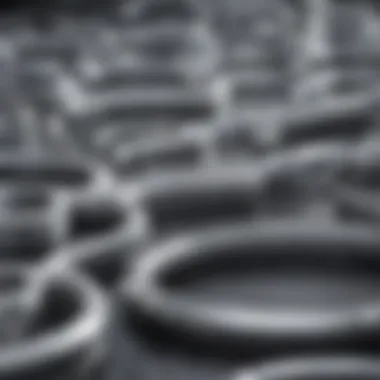
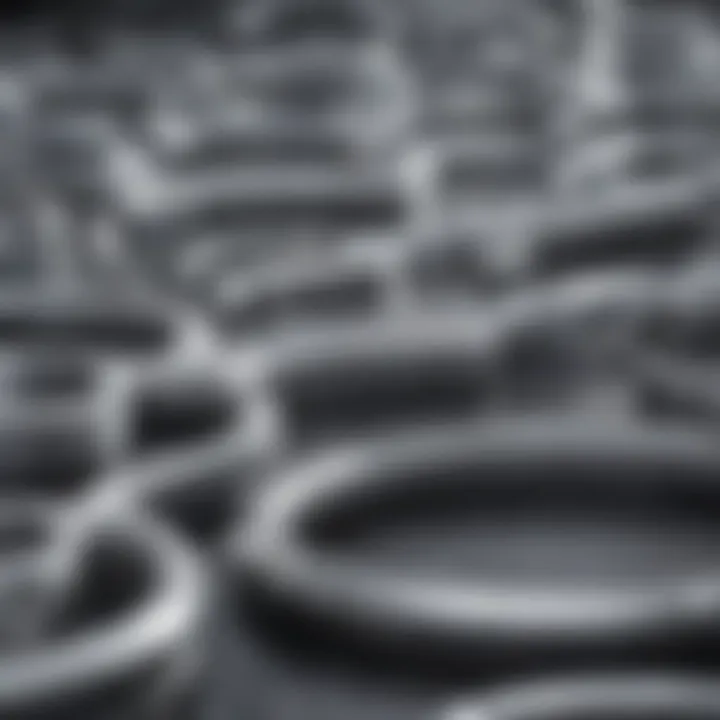
Applications of Alloys
The applications of aluminium alloys span a broad spectrum, from structural components in skyscrapers to lightweight parts in automotive manufacturing. A distinctive feature of these alloys is their ability to retain strength and resist corrosion, making them invaluable in harsh environments. The aerospace industry, for instance, relies heavily on specific alloys like 7075 due to its high strength-to-weight ratio, critical for maximizing performance while minimizing fuel consumption.
"Aluminium alloys offer a unique blend of strength and versatility, making them a staple in modern engineering."
In summary, classifying aluminium forms—including pure aluminium and various alloys—serves not only as an organizational tool but also as a guide for practical applications. Each classification reveals particular benefits and constraints, enabling industries to leverage the best that aluminium has to offer.
Forms of Aluminium in Manufacturing
The manufacturing of aluminium takes on various forms, each bounded by specific methods and applications. Understanding these processes is crucial, as each form has its own characteristics that enhance its functionality in diverse industries. From aviation to automotive, the significance of aluminium manufacturing forms can’t be overstated—it impacts not only the performance of the end products but also influences cost-efficiency and sustainability.
Casting
Casting is one of the primary manufacturing techniques of aluminium. In this method, molten aluminium is poured into a mold where it solidifies into a desired shape. It’s like creating a sandcastle, but instead of sand, we’re dealing with metal. This process allows for intricate designs and complex geometries that would be quite challenging to achieve using other methods.
There are several casting techniques, such as:
- Sand Casting: This involves creating a mold from sand, which is relatively inexpensive and adaptable.
- Die Casting: Here, high pressure is used to inject molten aluminium into metal molds, leading to precise shapes and dimensions.
- Investment Casting: Employing a wax pattern, this technique achieves outstanding surface finishes.
Casting plays a vital role in multiple sectors, notably in automotive and aerospace industries, where components must withstand significant stress and strains. The benefits of casting aluminium include:
- Cost-Effectiveness: Especially with large production runs.
- Versatility: Capable of creating complex shapes that might be difficult to manufacture otherwise.
- Material Efficiency: Wastes much less material compared to machining.
However, there are considerations to keep in mind such as:
- Potential porosity in castings, which can affect strength and durability.
- Higher lead times in mold creation compared to other methods.
Extrusion
Extrusion of aluminium involves forcing the metal through a die to create long profiles. Think of it as tube toothpaste—squeezing the contents through an opening shapes the product. This method is especially useful for producing continuous lengths of material with a constant cross-section.
The process is highly favored for creating items like:
- Aluminium tubing: Used extensively in construction and machinery.
- Structural profiles: Commonly found in window frames and railings.
Extrusion offers a handful of benefits:
- Efficiency: Highly automated, reducing labor needed.
- Flexibility: It can create complex shapes with favorable mechanical properties, making it lightweight yet strong.
- Surface Finish: Often, it results in an excellent finish that reduces post-production handling.
Yet, certain considerations must be acknowledged:
- The initial cost of the die can be significant, making it less ideal for low-volume projects.
- It necessitates heating the metal, which might affect its properties if not managed properly.
Rolling
Rolling aluminium involves passing the metal between rollers to reduce its thickness. Imagine flattening dough with a rolling pin—that’s the gist of it. It’s one of the oldest methods and is still in wide use today for producing sheets and plates.
There are primarily two types of rolling processes:
- Hot Rolling: Conducted at elevated temperatures—this method is effective for reducing thickness significantly.
- Cold Rolling: Done at room temperature, resulting in better surface finishes and improved dimensional accuracy.
The impact of rolling in manufacturing is profound:
- Production of Thin Sheets: Essential for industries looking for lightweight yet sturdy materials.
- Strain Hardening: Cold rolling enhances the strength of the metal, making it suitable for high-performance applications.
However, considerations include:
- Control over the process is key, as poor rolling can lead to defects such as uneven thickness.
- It also requires precise machinery and skilled operators, impacting operational expenses.
"Each method of aluminium manufacturing holds the potential to create innovative solutions for modern challenges, from sustainability to performance efficiency."
Understanding these forms is a pathway to realizing the vast potentials of aluminium in both current usage and future applications.
Aluminium Shapes and Their Applications
Aluminium shapes, spanning a wide range of profiles and forms, play a crucial role in numerous industries. Their significance goes beyond basic functionality, influencing design choices and material efficiency in various applications. From construction to automotive sectors, the versatility of aluminium shapes aids innovation and progress. Understanding these shapes is essential not only for their practical uses but also for appreciating the unique characteristics that make them advantageous.
Sheet Aluminium
Uses in Building and Construction
Sheet aluminium is a fundamental form found extensively in building and construction sectors. Its lightweight nature and high strength-to-weight ratio make it an ideal choice for cladding, roofing, and interior panels. One of its key characteristics is its corrosion resistance, which prolongs the life of structures, minimizing maintenance costs over time.
In terms of building aesthetics, the shiny surface of sheet aluminium provides a modern appeal while allowing for a range of coating options to match design specifications. A unique feature of sheet aluminium is its ability to be easily fabricated into different shapes without compromising its integrity, making it suitable for customized solutions. One disadvantage, however, might be its thermal conductivity, which can lead to insulation challenges if not properly managed.
Automotive Industry Applications
The automotive industry heavily relies on sheet aluminium for several reasons. One specific aspect is its use in car bodies, where reducing weight is paramount to improve fuel efficiency. The lightweight quality of sheet aluminium directly contributes to lower emissions, making it a popular choice in vehicle manufacturing today. Its formability allows it to be shaped into complex curves and designs, enhancing the vehicle's aerodynamics.
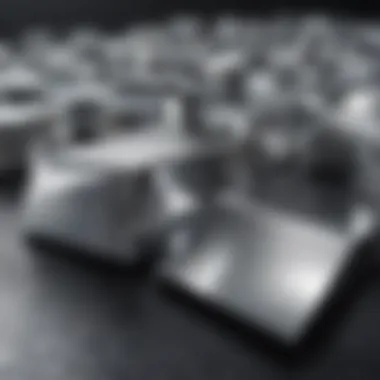
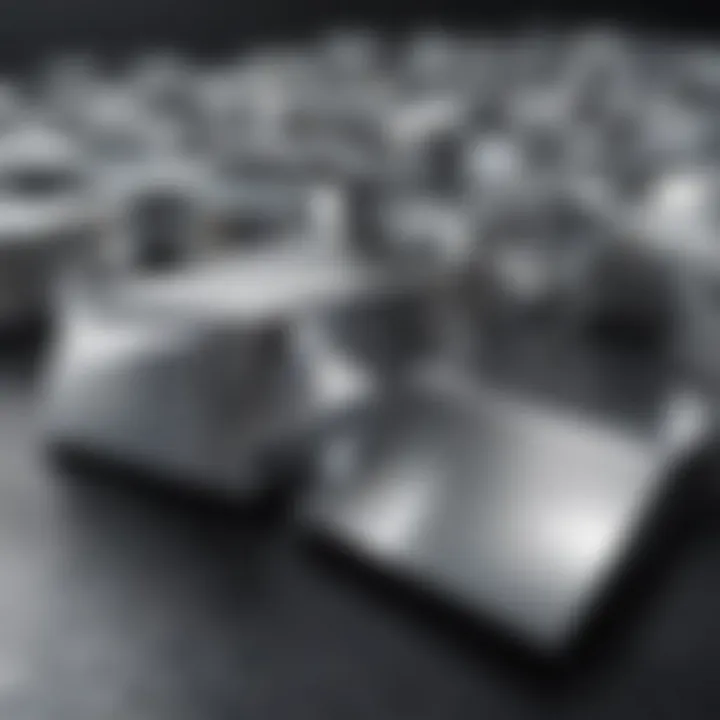
A unique feature in automotive applications is the material's resistance to impact, which, while advantageous, can also involve challenges in recovery after a collision. This characteristic has led to ongoing research into better alloy formulations to enhance not just formability but also durability in the face of everyday wear and tear.
Foil Aluminium
Packaging Applications
Foil aluminium has established itself as a cornerstone in packaging sectors. The specific aspect of barrier properties is what makes it indispensable for packaging food and pharmaceuticals. Its unique characteristic is the ability to block light, moisture, and air, helping preserve the freshness of contents. As such, it is a beneficial choice for perishable goods, extending shelf life significantly.
The lightweight and flexible nature of foil aluminium facilitate cost-effective manufacturing processes while providing minimal material usage. However, one might argue that while it offers excellent protective qualities, foil recycling can pose challenges, leading to some environmental scrutiny.
Insulation Properties
Another important aspect of foil aluminium is its insulation properties. Used in construction and product packaging, this material reflects heat, making it exceptionally efficient for thermal insulation applications. This reflective characteristic can help in reducing energy consumption in homes and businesses, which resonates perfectly with current sustainability trends.
Its ability to create barriers against sound as well enhances its appeal. One major challenge, though, is its susceptibility to tearing, which could compromise the insulation effectiveness if mishandled during installation. Thus, while foil aluminium presents several advantages in energy savings and sound insulation, it requires cautious handling to maintain its performance.
Aluminium Rods and Bars
Mechanical and Structural Applications
Aluminium rods and bars have notable importance in mechanical and structural applications. These shapes are often used in frameworks due to their strength versus weight balance, making them ideal for construction and manufacturing processes. The standardized dimensions of rods enable seamless integration into larger assemblies, promoting structural integrity.
A unique feature is the capability to be custom-fabricated to meet specific project requirements. While advantageous, it’s crucial to note that aluminium's lower modulus of elasticity compared to steel can lead to deflection issues in certain applications, potentially requiring additional support structures.
Electromagnetic Uses
Electromagnetic uses of aluminium rods and bars open a fascinating avenue, especially in electrical applications. Aluminium's conductive properties make it suitable for busbars and wiring, providing an efficient pathway for electric currents. One characteristic is its weight advantage, making it easier to install and manage in various systems.
The unique feature here is its anti-corrosive nature, which maintains performance even in exposed environments. Nevertheless, a significant disadvantage might include its lower conductivity compared to copper, which can limit its application in highly demanding electrical tasks. Recognizing these strengths and limitations is essential for making informed decisions in material selection.
Surface Treatments of Aluminium
Surface treatments of aluminium play a critical role in enhancing its performance and aesthetics across various applications. Aluminium, while highly valued for its lightweight and strength, can face challenges like corrosion and wear over time. By applying different treatments to its surface, we can significantly improve its durability and functionality. This section unpacks the importance of these treatments, delving into the specifics of anodizing, painting and coatings, and powder coating. Each method brings unique benefits and considerations, vital for students, researchers, educators, and professionals alike to understand.
Anodizing
Anodizing is a widely used electrochemical process that converts the metal surface into a decorative, durable, corrosion-resistant, anodic oxide finish. The method involves immersing aluminium in an acid electrolyte bath and passing an electric current through it. This process not only thickens the natural oxide layer but also allows for coloring through dyes, enhancing the aesthetic appeal of metal components.
The benefits of anodizing include:
- Corrosion Resistance: The thickened oxide layer acts as a barrier against corrosive elements, making anodized aluminium ideal for outdoor applications.
- Durability: Anodized surfaces are hard and scratch-resistant, which is important for products that demand high resilience.
- Eco-Friendliness: Anodizing is less harmful to the environment compared to traditional paint finishes, as it does not emit volatile organic compounds (VOCs).
However, the process does involve careful control, as the thickness of the anodic layer can affect performance in specific environments.
Painting and Coatings
Painting and applying coatings to aluminium surfaces is another effective way to improve both aesthetic and functional properties. This method can involve various types of paint, including acrylic, epoxy, or polyurethane, each having its blend of benefits.
Key advantages include:
- Customization: A broad spectrum of colors and finishes can be applied, allowing products to fit specific design requirements.
- Protection Against Corrosion: High-quality coatings can provide robust protection against environmental factors, particularly in harsh conditions where aluminium is exposed to chemicals or saltwater.
- Improved Lifespan: Properly applied coatings not only enhance appearance but also contribute to long-term durability of aluminium parts.
It is essential to note that surface preparation is crucial for the success of paint applications. If the surface is not thoroughly cleaned or primed, the paint may not adhere properly, resulting in peeling or chipping.
Powder Coating
Powder coating is a popular choice for finishing aluminium due to its resilience and superior finish. In this method, fine particles of pigment and resin are electrostatically charged and sprayed onto the aluminium surface. Following this, the part is cured under heat, allowing the powder to melt and form a durable layer.
Benefits of powder coating include:
- Durability & Hardness: Powder-coated surfaces resist scratching, chipping, and fading better than conventional paint.
- Environmental Safety: Like anodizing, powder coating is a more eco-friendly option since it creates minimal volatile organic compound emissions during application.
- Color & Texture Variety: Powder coating offers extensive possibilities for colors and textures, providing additional options for designers and engineers.
In summary, the choice of surface treatment can greatly influence the properties and longevity of aluminium products. Understanding the nuances of each method, from anodizing to powder coating, equips professionals to make informed decisions about how to protect and enhance aluminium surfaces for various applications.
"Surface treatments not only enhance the lifespan of aluminium but also allow for creativity in design, making them indispensable in many industries."
With ongoing developments in surface treatment technologies, the future holds exciting possibilities for improved coatings and processes.
Corrosion Resistance of Aluminium
Corrosion resistance is a pivotal aspect of aluminium's utility across various applications. While aluminium may not be the first metal that pops to mind when considering rust, its resistance to corrosion is a defining characteristic that allows it to thrive in numerous environments where other metals would fail. This component of aluminium not only enhances its longevity but also contributes to the reduction of maintenance costs and increases its attractiveness as a sustainable material choice.
Aluminium forms a thin layer of aluminium oxide when exposed to air. This layer acts like a shield, preventing further oxidation. Unlike other metals, like iron, which corrode rapidly, aluminium holds up significantly better. Because of its unique properties, understanding how aluminium interacts with its surroundings can be a game changer for industries such as construction, automotive, and aerospace.
Types of Corrosive Environments
Corrosive environments can range from the benign to the brutal. Key factors include moisture, salinity, temperature, and exposure to chemicals. Below are common types of environments that can challenge even the most resilient forms of aluminium:
- Marine Environments: High salt content from seawater can significantly affect aluminium. The chloride ions found in saltwater can be particularly aggressive, leading to localized corrosion known as pitting.
- Industrial Settings: Exposure to various chemicals, such as acids and bases, can erode the protective layer. The degree of damage often depends on the specific chemical involved.
- Urban Environments: Atmospheric pollutants, including sulphur dioxide and nitrogen oxides, can accelerate corrosion through processes like acid rain formation.
- Desert Climates: While dry, these environments can still create challenges through temperature fluctuations that can lead to stress corrosion cracking.
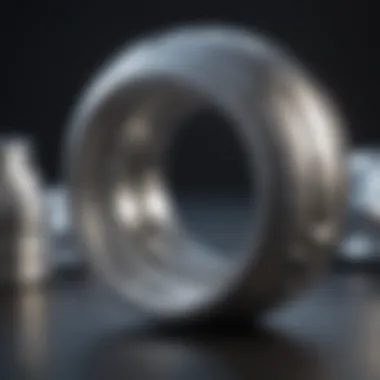
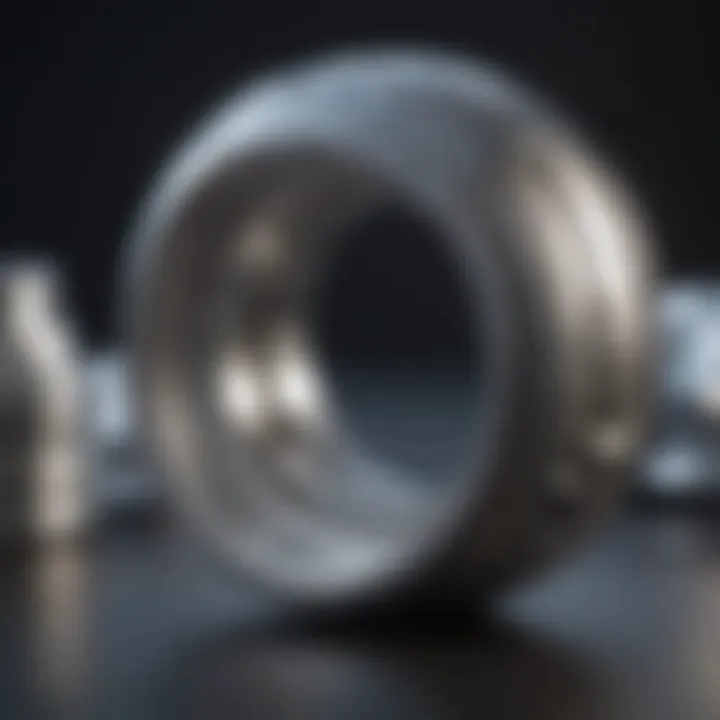
Mitigation Techniques
To combat corrosion and extend the life of aluminium, several mitigation techniques can be employed. Among them are:
- Protective Coatings: Applying a suitable coating can effectively insulate aluminium from external factors. Paints, varnishes, or specialized coatings can create a barrier against corrosive agents.
- Anodizing: This electrochemical process enhances the natural oxide layer on aluminium, making it thicker and more resistant to wear and corrosion. Anodized surfaces can be dyed in various colors, providing aesthetic benefits along with functional performance.
- Environmental Control: Adjusting environmental conditions—where possible—can help mitigate corrosion. For example, using dehumidifiers in storage areas or buffering against heavy industrial emissions can reduce exposure to harmful moisture and pollutants.
- Material Selection: Choosing the right alloy for specific environments can prevent numerous issues. Alloys designed for marine use, for instance, are engineered to withstand harsher conditions better than standard aluminium.
"Combatting corrosion is not just about materials – it’s about strategy and understanding the environment too."
Employing these techniques can transform aluminium from a metal susceptible to corrosion into one that thrives in challenging conditions. This adaptability cements aluminium's role as a vital material in today's industrial landscape.
Sustainability and Recycling of Aluminium
The significance of sustainability in the context of aluminium cannot be overstated. As industries continue to evolve, an increased focus on environmental impacts and resource conservation becomes paramount. Aluminium, thanks to its unique properties and characteristics, plays a crucial role in promoting sustainability. Importantly, one of the standout features of aluminium is its ability to be recycled repeatedly without compromising its quality. This aspect positions it as a metal of choice for a more sustainable future.
Sustainability isn't merely about reducing waste or cutting emissions. It encompasses a broader spectrum of practices that can lead to better resource management and decreased environmental burden. By prioritizing recycling and the responsible sourcing of aluminium, we can mitigate the negative impacts on our planet. The recycling of aluminium leads to significant energy savings, reduces carbon emissions, and conserves natural resources.
Key elements that make aluminium recycling sustainable include:
- Energy Efficiency: Recycling aluminium consumes up to 95% less energy compared to producing new aluminium from bauxite ore. This significant energy reduction results in lower greenhouse gas emissions.
- Resource Conservation: By recycling, we minimize the need for new raw materials, therefore preserving bauxite deposits and reducing habitat destruction.
- Waste Reduction: Recycling helps divert waste from landfills, promoting a circular economy where products are reused and repurposed instead of discarded.
By addressing sustainability in the aluminium industry, manufacturers can help pave the way for future innovations and practices that are environmentally friendly. Now let’s dive deeper into the life cycle assessment of aluminium products, which offers an insightful look at the environmental impacts associated with various stages of aluminium usage.
Life Cycle Assessment
A life cycle assessment (LCA) is a systematic approach that evaluates the environmental impacts of a product from its inception to its end. In the context of aluminium, LCA is particularly important as it highlights how decisions made at one stage can influence sustainability outcomes all the way to disposal or recycling.
An LCA for aluminium typically includes several stages: extraction of raw materials, production, use, and end-of-life management. It assesses factors such as:
- Resource extraction: Understanding the ecological footprint of mining and processing bauxite.
- Production: Evaluating the energy consumed during aluminium smelting and processing.
- Transportation: Considering emissions from moving materials across distances.
- Usage phase: Analyzing the operational efficiency of aluminium products in their intended applications.
- Disposal and recycling: Looking at how the product is handled at its lifespan's end, emphasizing recycling opportunities.
An important takeaway is that the knowledge garnered from LCAs can guide stakeholders in making informed decisions that lead to enhanced sustainability outcomes.
Recycling Processes
The process of recycling aluminium is intricate yet efficient, employing methods that maximize resource recovery while minimizing environmental impact. The journey begins with the collection of scrap aluminium, which may come from various sources such as:
- Post-consumer waste, including beverage cans and packaging materials.
- Industrial scrap, derived from manufacturers producing aluminium products.
Once collected, the recycling process generally follows these steps:
- Sorting: Scrap aluminium is sorted based on its grade and type. This ensures that different alloys do not contaminate each other, which is crucial for maintaining the quality of the recycled product.
- Shredding: The sorted aluminium is shredded into smaller pieces to facilitate melting.
- Melting: Shredded aluminium is heated in a furnace. During this stage, impurities are removed, and the aluminium turns into a molten state.
- Casting: The molten aluminium is poured into molds, forming ingots or other desired shapes, ready for further processing.
- Reprocessing: The recycled aluminium ingots can then be rolled, extruded, or further processed to form new products.
"Recycling aluminium not only saves energy but also significantly reduces greenhouse gas emissions, making it a cornerstone of sustainable practices in metal manufacturing."
In summary, the sustainability and recycling of aluminium represent a vital intersection where environmental stewardship meets industrial excellence. By grasping the principles behind life cycle assessments and the recycling processes, we can appreciate how crucial aluminium is in forming a more sustainable future.
Future Developments in Aluminium Research
As the world increasingly pivots towards sustainability and innovation, aluminium research stands at the forefront of material science. Aluminium’s lightweight and durability make it a prime candidate for various applications, from transport to construction. The advancements made in this field are not simply useful; they represent a significant shift towards more efficient materials that respond to the demands of modern society.
New developments in aluminium are crucial when considering global challenges, such as reducing carbon footprints and increasing energy efficiency. This focus is especially important in industries where aluminium is a primary material, like aerospace, automotive, and packaging. The potential benefits of ongoing research include enhanced performance in demanding environments, reduced costs of production, and increased recyclability, which can ultimately contribute to a circular economy.
Additionally, emerging research in aluminium technology links closely with environmental goals, fostering a greener future.
Innovative Alloys
In the quest for improved aluminium products, innovative alloys have emerged as a game-changer. The development of these alloys is not merely about adding elements but about rethinking how aluminium interacts with other materials. For instance, incorporating elements like lithium can reduce weight while maintaining strength, turning heads in the aerospace industry eager for functional and efficient designs.
Moreover, there is a growing trend to experiment with non-traditional alloying elements. For example, magnesium and silicon combinations result in alloys that are particularly resistant to corrosion, which is invaluable for coastal construction applications. Other recent innovations involve combining aluminium with advanced materials, such as carbon composites, to further enhance performance properties. These innovative alloys are paving the way for new applications and enhanced capabilities in existing ones, showcasing aluminium's flexibility as a material.
Advanced Manufacturing Techniques
Manufacturing has taken significant strides in recent years, affecting how aluminium is processed and used. Advanced manufacturing techniques like additive manufacturing (3D printing) and digitally integrated processes are reshaping the landscape. These methods allow for more complex geometries that traditional techniques cannot achieve, resulting in parts that are not only lighter but also stronger and more efficient.
One significant advantage of these techniques is the reduction in material waste. With precision manufacturing processes, less aluminium is discarded during production, making the process not only more cost-effective but also more sustainable. Additionally, these methods allow for rapid prototyping, which accelerates product development cycles and meets market demands swiftly.
As we move forward, it becomes clearer that the fusion of research into innovative alloys and advanced manufacturing processes is essential for maximising aluminium's potential.
The combination of collective knowledge from the past and those new groundbreaking techniques can lead to breakthroughs that redefine how aluminium is perceived, used, and recycled.
Finale
In wrapping up the extensive exploration of aluminium in its varied forms, it’s crucial to recognize the multifaceted role that this metal plays across numerous sectors. This conclusion doesn't merely summarize what has been discussed; it brings to light the significance of understanding aluminium’s properties, applications, and the ongoing advancements that are set to shape its future.
Recap of Key Points
To highlight the core ideas emerged in this exploration:
- Diverse Forms: Aluminium exists primarily in two forms: pure aluminium and various alloys. Each form has distinct properties that cater to different industrial needs.
- Manufacturing Methods: Processes like casting, extrusion, and rolling create the myriad shapes we find in products, from kitchen foil to aircraft components.
- Surface Treatments: Techniques such as anodizing and powder coating enhance durability and aesthetics, ensuring aluminium's longevity in various applications.
- Corrosion Resistance: Understanding environmental factors and corrosion resistance enables better application in settings where aluminium is exposed to harsh conditions.
- Sustainability: The recycling aspect of aluminium is becoming increasingly significant, reflecting a global push toward sustainable practices.
- Future Directions: Research is ongoing, particularly in innovative alloys and advanced manufacturing, highlighting a promising future for aluminium applications.
This synthesis of information aids in grasping not just the material itself, but also its broader implications in technology and society.
Implications for Future Research
Looking ahead, the field of aluminium research presents vast opportunities. Continued advancements may include:
- Development of New Alloys: Innovating stronger, lighter, and more corrosion-resistant alloys that can meet specific needs in aerospace, automotive, and construction sectors.
- Improved Manufacturing Techniques: Enhancing current methodologies or developing new ones to increase efficiency and reduce waste.
- Sustainability Focus: Investigating new recycling methods or processes that minimize the carbon footprint of aluminium production and usage.
- Smart Aluminium Applications: Exploring aluminium’s role in smart technologies and materials that adapt to environment, enhancing functionality in sectors like electronics and building materials.