The Electronic Manometer: Design, Function & Applications
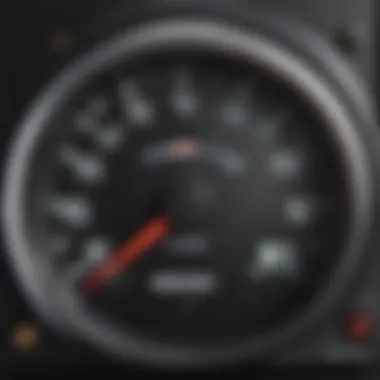
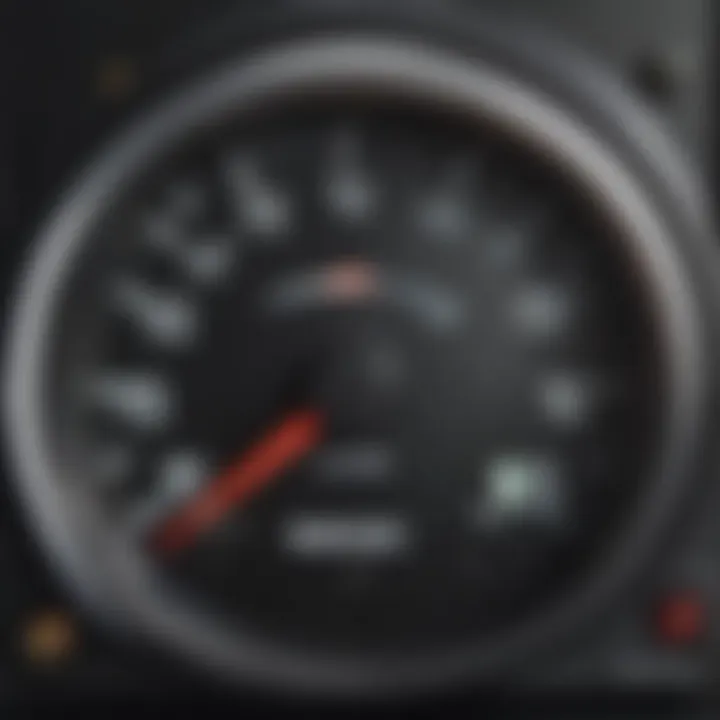
Intro
The electronic manometer is a crucial device in pressure measurement that has developed significantly with advancements in technology. It is designed to provide accurate and real-time pressure readings, making it essential in various sectors such as engineering, physics, and medical diagnostics. Understanding the electronic manometer involves exploring its design, principle of operation, and significant applications.
Unlike traditional manometers that rely on mechanical movements, electronic manometers utilize sensors and digital displays. This change enhances their accuracy and facilitates easier data interpretation. They are capable of measuring both static and dynamic pressures, thus serving a broad range of functions.
The following sections will delve into the intricate aspects of electronic manometers. We will first examine the research methodology employed in studying these devices, followed by a discussion on their design and functionality. Finally, we will highlight their various applications and consider future directions for this technology.
Prolusion to Electronic Manometers
Electronic manometers are crucial instruments in a range of scientific and industrial contexts. They excel in measuring pressure, providing good precision and reliability. Understanding electronic manometers involves exploring their features, functions, and the vital roles they play.
In this section, we will define what an electronic manometer is, and highlight its significance in various settings. This is important for students, educators, and professionals who rely on accurate measurements in their work. The information presented aims to provide a comprehensive overview that is both informative and engaging.
Definition of Electronic Manometer
An electronic manometer is an advanced device designed to measure the pressure of gases and liquids. Unlike traditional mechanical manometers, electronic models utilize electronic sensors to gauge pressure changes. This enables precise measurements, which are displayed digitally. They can measure various forms of pressure, including absolute, gauge, and differential pressure, making them versatile tools in numerous applications.
The use of electronic components facilitates quick data processing and real-time monitoring. Devices such as these are often equipped with a microcontroller that interprets the sensor data and converts it into readable formats, easily viewed by users.
Importance in Scientific and Industrial Settings
Understanding pressure accurately is essential in numerous fields, including engineering, medicine, and environmental science. Electronic manometers provide significant advantages in these arenas. Here are some of the key benefits of using electronic manometers:
- Precision: Electronic manometers typically have better accuracy compared to mechanical ones. This precision is vital in scientific research and high-stakes industrial processes.
- Ease of Use: The digital readouts simplify the monitoring of pressure, reducing human error and enhancing safety.
- Versatility: They can be used in various applications, from simple lab experiments to complex industrial systems.
- Data Logging: Many electronic models allow for data storage. This feature is vital for trend analysis and compliance purposes.
In summary, the relevance of electronic manometers in both scientific and industrial settings is significant due to their adaptability and accuracy. They form the backbone of effective pressure measurement, influencing outcomes in critical applications.
Principles of Pressure Measurement
Understanding the principles of pressure measurement is essential when studying electronic manometers. These principles underpin the functionality and application of the devices in various fields. Knowledge of how pressure is defined and measured enhances a user's ability to interpret data accurately. Pressure measurement plays a critical role in both scientific research and industrial processes.
Basic Concepts of Pressure
Pressure is defined as the force exerted per unit area. Mathematically, it is expressed as:
[ P = \fracFA ]
where (P) is the pressure, (F) is the force applied, and (A) is the area over which the force is distributed. There are several key concepts related to pressure that should be understood:
- Static Pressure: Refers to pressure measured in a fluid at rest. It is crucial for applications like hydraulic systems.
- Dynamic Pressure: This occurs when the fluid is in motion. It is important for understanding fluid dynamics and aerodynamics.
- Total Pressure: The sum of static and dynamic pressures, often used in high-speed applications.
These concepts form the foundation for more advanced discussions on pressure types and their measurement.
Differences Between Absolute, Gauge, and Differential Pressure
In practical applications, pressure is typically categorized into three main types: absolute, gauge, and differential pressure. Each type has its unique significance and context in which it is used.
- Absolute Pressure: This measurement provides pressure relative to a perfect vacuum. It is crucial in areas where precise measurements are necessary, such as meteorology and physics. For example, absolute pressure is used in barometric pressure readings, which are important for weather predictions.
- Gauge Pressure: Gauge pressure measures pressure relative to atmospheric pressure. It is widely used in industrial applications like tire pressure monitors and water systems. For example, a pressure gauge that reads zero when it is at atmospheric pressure is indicating gauge pressure.
- Differential Pressure: This measures the difference between two pressure points. It is essential in applications like flow measurement in process industries. Differential pressure sensors are often employed in air filters to indicate when a filter is clogged.
These differences highlight the versatility and specificity of electronic manometers. Understanding pressure types is vital for anyone involved in fields like engineering, physics, and manufacturing, where accurate pressure measurement impacts safety and efficiency.
"Accurate pressure measurement is not just about reading the numbers; it is about understanding what those numbers mean in context."
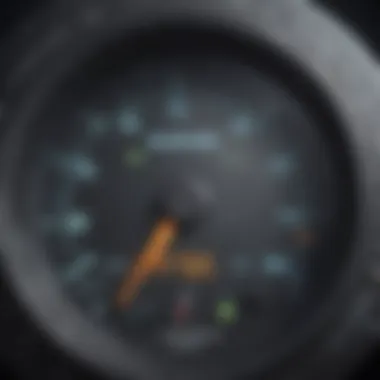
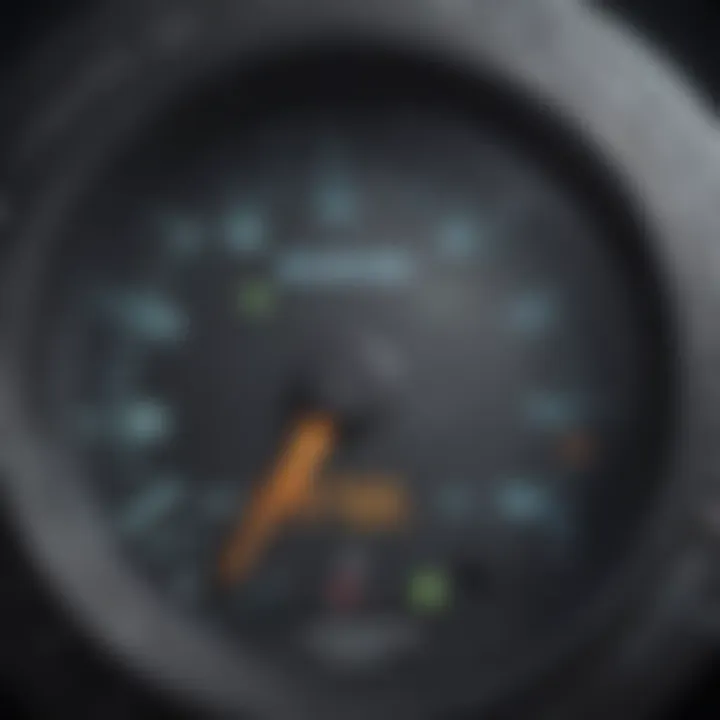
In summary, grasping the principles of pressure measurement is foundational for properly utilizing electronic manometers. This understanding aids individuals in interpreting data effectively and applying it in practical scenarios.
Construction of Electronic Manometers
The construction of electronic manometers is an essential aspect of understanding their functionality and effectiveness. The design choices directly impact measurement accuracy, reliability, and user interface. By analyzing the construction, one can appreciate how various components come together to create a sophisticated instrument capable of precise pressure measurement. This section explores the key elements involved in the construction and how they contribute to the device’s overall performance.
Key Components
The electronic manometer consists of several integral components, each designed to fulfill specific functions:
- Pressure Sensor: This is the heart of the manometer, converting pressure into an electrical signal. Common types of sensors used include piezoelectric, capacitive, and strain gauge sensors. The choice of sensor significantly affects the accuracy and range of measurements.
- Microprocessor: The microprocessor interprets the data from the pressure sensor, processing the electrical signals to provide a readable output. It may also manage calibration and compensation for environmental factors.
- Display Unit: This component presents the measured pressure in an user-friendly format. Displays can range from simple analog needles to advanced digital screens with graphical interfaces.
- Power Supply: Electronic manometers need a consistent power supply, often provided by batteries or direct current from an external source. The efficiency of the power supply impacts the device’s operational longevity.
- Housing: The construction material and design of the housing protect internal components from physical damage and environmental influences, such as moisture and dust. Materials like stainless steel or durable plastics are commonly used for increased durability.
Types of Sensors Used
Different applications require different types of sensors, influencing which manometer is suitable for a particular task. Some of the most common sensors in electronic manometers include:
- Piezoelectric Sensors: Known for their sensitivity, these sensors are especially useful in applications requiring rapid pressure change detection. They generate an electrical charge in response to mechanical stress.
- Capacitive Sensors: These sensors measure changes in capacitance as pressure varies. They are reliable for measuring low pressures and can be highly accurate, making them popular in laboratory settings.
- Strain Gauge Sensors: Utilizing the properties of strain gauges, these sensors convert mechanical deformation into an electrical signal, providing accurate readings particularly in challenging conditions.
Each sensor type comes with its own set of advantages and limitations, thus creating a spectrum of options for users based on their specific needs.
Display and Data Processing Features
The display and data processing features of electronic manometers play a pivotal role in the usability of the instrument. These features enable users to interpret data efficiently and can enhance measurement accuracy.
- Real-Time Displays: Modern electronic manometers often come equipped with real-time data displays that change instantaneously as pressure adjusts. This is important for monitoring systems in dynamic environments.
- Data Logging: Many units include the ability to log data over time, which is particularly valuable in research or industrial processes where trends are analyzed for operational adjustments.
- User Interfaces: Interfaces can include touchscreen options, buttons, or knobs for easier navigation. A well-designed interface increases user experience and reduces the possibility of error due to misinterpretation.
- Wireless Connectivity: With advancements in technology, electronic manometers may also offer features such as Bluetooth or Wi-Fi connectivity. This enables data transfer to remote displays or integration with other systems for enhanced analysis.
Types of Electronic Manometers
Understanding the types of electronic manometers is crucial for professionals in fields such as engineering, physics, and medicine. Each type serves specific applications, catering to various accuracy and operational needs. Differentiating between these types enables users to select the most appropriate instrument for their particular context, facilitating reliability in measurements.
Digital Manometers
Digital manometers are among the most common types of electronic manometers. They provide digital readouts of pressure, which enhance accuracy and ease of reading compared to analog devices. Their design often integrates features like data logging and the ability to connect to computers. This connectivity allows for real-time monitoring and detailed analysis of pressure data, which is especially useful in environments requiring continuous oversight.
The ease of use with digital manometers makes them a favorite in laboratory and industrial settings. Additionally, these devices often come with programmable settings, allowing them to accommodate various measurement units, like Pascals or bar.
Micromechanical Manometers
Micromechanical manometers represent a more advanced technology, utilizing tiny mechanical sensors to measure pressure. These devices work on the principle of detecting deflections caused by pressure changes. Micromechanical designs can achieve very high sensitivity, making them appropriate for applications requiring precise measurements, such as in microfluidics or aerospace industries.
One distinct advantage of micromechanical manometers is their compact size. Their small footprint allows for integration into systems where space is limited.
Load Cell Based Manometers
Load cell based manometers utilize load cells to measure pressure. These devices convert pressure into a proportional electrical signal, which can then be displayed digitally. Their design makes them exceptionally robust and capable of handling harsh environments, which is often necessary in industrial contexts.
In terms of benefits, load cell based manometers are reliable and can measure both static and dynamic pressures effectively. Their versatility in range of applications—from hydraulic systems to environmental monitoring—makes them a valuable tool.
In summary, selecting the appropriate type of electronic manometer hinges on application requirements, expected pressure ranges, and environmental conditions.
Calibration of Electronic Manometers
Calibration is a critical procedure in the lifecycle of electronic manometers. Ensuring accuracy in measurement is non-negotiable, particularly in high-stakes fields such as engineering, manufacturing, and medical diagnostics. If a manometer is not calibrated properly, the data produced can lead to incorrect conclusions or failing to meet safety and compliance standards. Calibration serves not only to verify the reliability of these instruments but also enhances their performance and effectiveness.
Importance of Calibration
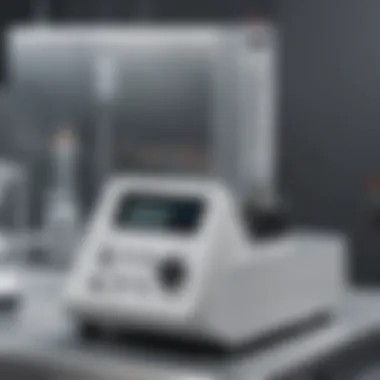
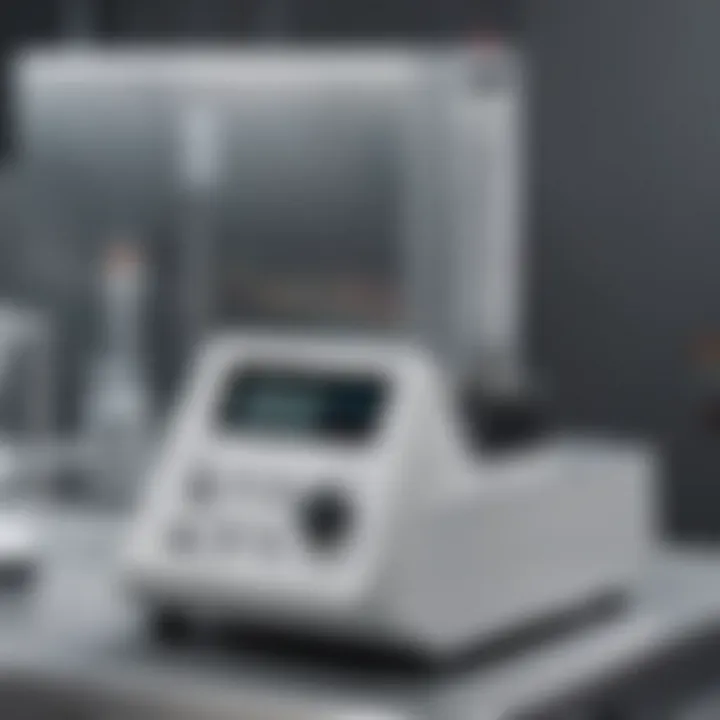
The importance of calibration cannot be overstated. Here are key reasons why calibration is essential:
- Precision in Measurements: Calibration ensures that the electronic manometer produces measurements that align with known standards. This precision is crucial for experiments and processes where measurement discrepancies can lead to severe consequences.
- Compliance with Standards: Many industries are governed by strict regulatory standards. Regular calibration of electronic manometers helps maintain compliance, minimizing risks associated with legal or operational penalties.
- Improved Performance: Over time, sensors can drift from their original performance specifications. Calibration helps in readjusting the sensors to their optimal state. This adjustment directly impacts the efficiency and accuracy of pressure readings.
- Cost Management: Frequent calibration prevents greater costs associated with errors. Misleading data can cause product failures, which, in turn, can lead to financial losses, increased time, and resource wastage.
- Safety Assurance: Many applications of manometers pertain to safety-critical setups. Calibration ensures that pressure measurements remain within safe operational limits, protecting personnel and equipment.
"Calibration bridges the gap between measurement and meaningful analysis. Without it, data loses context."
Methods for Calibration
There are several methods used for calibrating electronic manometers, each with distinct advantages and limitations. Below are common approaches:
- Static Calibration: This method involves comparing the electronic manometer readings against a known reference standard. The reference can be a primary standard pressure sensor or a calibrated manometer.
- Dynamic Calibration: This method is more complex and requires exposing the manometer to varying pressure levels over time. This procedure checks how the device responds to changes and tends to be more thorough than static calibration.
- Multi-Point Calibration: Instead of a single point, multiple reference pressure levels are used. This low-cost method improves the overall accuracy by mapping the measurement linearity across a range of pressures.
- Software Calibration: Some modern manometers come equipped with calibration software. This allows for the adjustments to be made digitally, improving the speed and efficiency of the calibration process.
In practice, the choice of calibration method should be influenced by the specific application requirements and the environmental conditions in which the manometer operates. All methods should be documented carefully to maintain an audit trail and ensure rigorous standards of practice.
Applications of Electronic Manometers
Electronic manometers play a pivotal role in various fields, providing precise measurements that are essential for both industrial processes and scientific research. Their ability to accurately gauge pressure has profound implications in engineering, medicine, and environmental monitoring. Understanding their diverse applications enhances the appreciation of these instruments and sheds light on their significance in modern technology. In this section, we explore specific domains where electronic manometers are indispensable.
Use in Engineering and Manufacturing
In engineering and manufacturing, precision is paramount. Electronic manometers serve a vital function by ensuring that pressure levels are maintained within specified ranges. For example, in the automotive industry, electronic manometers are used to monitor tire pressure. Accurate tire pressure contributes not only to fuel efficiency but also to safety on the road. Additionally, the calibration of hydraulic systems often relies on these devices to achieve optimal performance and prevent accidents.
Moreover, electronic manometers support quality control processes in manufacturing. They facilitate detailed analysis of pressures during production, helping to identify anomalies that could lead to product defects. This monitoring ability enhances overall productivity and reduces waste, benefiting both manufacturers and consumers.
Applications in Medical Diagnostics
Electronic manometers also find significant applications in the medical field. They are essential in devices like sphygmomanometers, which measure blood pressure. With the rise of telemedicine, the integration of these manometers in portable diagnostic tools has increased accessibility to vital health metrics. Accurate blood pressure readings allow healthcare providers to monitor patients remotely, effectively managing conditions such as hypertension.
Furthermore, electronic manometers are utilized in respiratory devices, where accurate pressure measurement is critical for assessing lung function. These applications demonstrate how these instruments contribute directly to patient care and overall healthcare improvements.
Role in Environmental Monitoring
Environmental monitoring has increasingly relied on electronic manometers. These devices measure atmospheric pressure, providing crucial data for weather forecasting and climate studies. Meteorologists use them to track changes in pressure systems, which directly influence weather patterns. Additionally, electronic manometers are important in assessing air quality. By measuring the pressure of gas emissions, they help quantify pollutants and evaluate compliance with environmental regulations.
In summary, the applications of electronic manometers cover a broad spectrum, from engineering and manufacturing to critical roles in medical diagnostics and environmental observation. Their adaptability and reliability make them invaluable across various fields, underscoring the importance of exploring these advanced instruments.
Comparative Analysis with Mechanical Manometers
In the realm of pressure measurement, the comparative analysis between electronic and mechanical manometers is crucial for understanding their respective roles, efficiencies, and applications. This examination reveals not just the technological evolution of pressure measurement devices, but also highlights their specific advantages and limitations in various contexts. The rise of electronic manometers serves a need for precision and automation that mechanical designs struggle to provide. Additionally, these comparisons can guide professionals in selecting the appropriate tool for their operational needs.
Advantages of Electronic Over Mechanical Manometers
Electronic manometers present several advantages compared to mechanical counterparts, making them preferable in many situations:
- Increased Precision: Electronic manometers often provide higher accuracy due to advanced sensor technologies. They can measure pressure changes with greater sensitivity.
- Data Recording and Storage: Many electronic models come equipped with features for data logging. This allows for long-term storage of measurements which can be invaluable in detailed analyses or research projects.
- Ease of Use: The user interfaces on electronic manometers tend to be more straightforward. Digital displays offer clear readings, which reduces the possibility of human error during interpretation.
- Integration Capabilities: Electronic devices can easily integrate with computer systems and data analysis software. This feature enables real-time monitoring and advanced analytics, which support better decision-making processes.
- Less Susceptible to Mechanical Wear: Since electronic manometers do not rely on mechanical moving parts, they often have a longer lifespan and require less maintenance. This reliability is beneficial in hostile environments where wear and tear can significantly impact performance.
Overall, these factors contribute to a growing preference for electronic manometer systems in industries that demand high standards of accuracy and efficiency.
Limitations of Electronic Manometers
Despite their numerous advantages, electronic manometers have limitations that can affect their application:
- Sensitivity to Environmental Factors: Electronic manometers can be sensitive to temperature variations, humidity, and electromagnetic interference. These factors might introduce errors or affect functionality if not properly managed.
- Cost: While they offer performance benefits, electronic manometers typically come at a higher initial investment compared to mechanical types. This can be a significant consideration for organizations operating on tight budgets.
- Power Dependency: Electronic devices require a power source to operate. In remote locations or situations where power supply is unreliable, this reliance can limit their use.
- Complexity in Calibrating: Electronic systems often require more complex calibration processes. This can necessitate specialized training for personnel, potentially increasing operational costs.
- Vulnerability to Damage: The delicate components of electronic manometers may be more prone to damage from physical shock or exposure to corrosive substances compared to their mechanical counterparts.
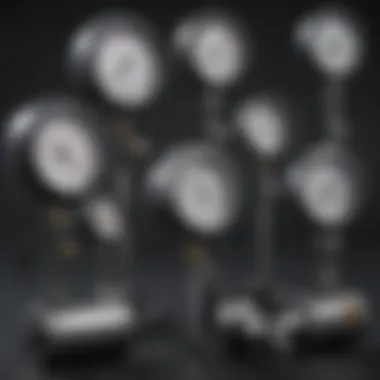

In summary, while electronic manometers provide significant advancements in measurement technology, they are not without drawbacks. A careful assessment of the specific requirements, environments, and available resources should guide the selection of either electronic or mechanical systems for pressure measurement.
Challenges in Using Electronic Manometers
Electronic manometers offer precision and reliability in pressure measurement, but they are not without challenges. Understanding these challenges is crucial for various professionals that rely on accurate pressure readings in their fields. This section explores the impact of environmental factors on the functionality of electronic manometers, as well as common operational issues faced by users.
Impact of Environmental Factors
Environmental factors can significantly affect the performance of electronic manometers. These instruments are designed to function within specific conditions, and deviations from these can lead to inaccurate readings or malfunctioning. Temperature fluctuations can alter sensor accuracy; high temperatures can cause components to expand, affecting performance.
Humidity is another critical factor. Excess moisture can lead to corrosion of internal components or create electrical interference, leading to erratic readings. Moreover, exposure to dust and other particulates can obstruct pressure sensors, compromising their accuracy. It is essential for users to monitor environmental conditions closely and employ proper protective measures to mitigate these impacts.
Common Operational Issues
Even with proper care, common operational issues can arise during the use of electronic manometers. A frequent problem is calibration drift, where the device's accuracy diminishes over time due to prolonged use or environmental changes. This can result in erroneous pressure measurements, potentially leading to severe consequences in sensitive applications.
Another issue is battery life. While many electronic manometers are built with efficient power management, prolonged usage or extreme conditions can drain batteries quickly, causing the device to shut down unexpectedly. Regular maintenance checks and battery replacements are necessary to ensure reliability.
Finally, user errors can also contribute to operational issues. Incorrect setup, such as improper connections or incorrect pressure range settings, can lead to misleading results. Users should be well-trained in the operation of these instruments to minimize misunderstandings and ensure accurate data collection.
Key takeaway: Environmental factors and operational issues must be acknowledged and addressed to enhance the effectiveness of electronic manometers in practical applications.
Future Trends in Manometer Technology
The field of pressure measurement is undergoing significant transformations, primarily due to the advancements in technology. Understanding future trends in manometer technology is essential for professionals in various industries, as it helps inform decisions regarding equipment adoption and system integration. These trends can lead to improved accuracy, efficiency, and functionality in measurements. With the rise of smart technologies, we can expect electronic manometers to evolve in ways that enhance their operational capabilities and user interactions.
Advancements in Sensor Technology
Recent developments in sensor technology are revolutionizing electronic manometers. New materials and designs allow for greater sensitivity and stability. For instance, piezoresistive sensors and capacitive sensors are at the forefront of these advancements. They offer better precision in pressure readings and handle a broader range of environmental conditions. The ability to miniaturize sensors means that manometers can be more compact, facilitating use in various applications without sacrificing performance. Additionally, these modern sensors can operate over extended periods with minimal drift, enhancing reliability in long-term measurements.
"Advancements in sensor technology are key to unlocking new operational capabilities and ensuring precise measurements in diverse environments."
Integration with IoT and Intelligent Systems
The integration of IoT (Internet of Things) technology is another notable trend impacting electronic manometers. This connectivity can enable real-time data monitoring and analysis over the internet. In industries such as manufacturing and healthcare, this integration allows for enhanced remote diagnostics and immediate responses to pressure changes. Intelligent systems can utilize data analytics to provide predictive maintenance alerts, reducing downtime caused by unexpected failures. Furthermore, IoT-enabled manometers can facilitate data sharing among multiple devices, leading to more informed operational and strategic decisions.
In addition to IoT, the incorporation of machine learning algorithms into electronic manometer systems plays a crucial role. These algorithms can analyze pressure trends and detect anomalies, identifying potential issues before they escalate. The synergy between enhanced sensor capabilities and smart technology is poised to increase the efficiency and ease of pressure measurement in various applications.
Epilogue
The concluding section of this article serves as a significant distillation of insights regarding electronic manometers. To understand their role, one must consider the various elements that contribute to their functionality and importance in multiple fields. Electronic manometers are not just tools for measurement; they symbolize precision engineering that enhances scientific inquiry and industrial procedures alike.
Summary of Key Points
In this article, we explored several critical aspects of electronic manometers:
- Definition and Overview: We defined what electronic manometers are and outlined their significance in scientific and industrial contexts.
- Pressure Measurement Principles: Important concepts such as absolute pressure, gauge pressure, and differential pressure were covered.
- Construction Details: We discussed key components and the types of sensors utilized in these devices, along with their display features.
- Types of Electronic Manometers: A thorough examination of various types including digital manometers and micromechanical manometers was presented.
- Calibration Necessities: Calibration methods were highlighted to emphasize the importance of accuracy in pressure measurements.
- Applications Across Fields: The diverse applicability of electronic manometers in engineering, medical diagnostics, and environmental monitoring illustrates their value.
- Comparative Analysis: We compared electronic manometers with mechanical ones, discussing advantages and limitations.
- Challenges and Future Trends: Lastly, practical challenges regarding environmental factors and advancements in technology, particularly integration with IoT, were also detailed.
Final Thoughts on the Importance of Electronic Manometers
The role of electronic manometers cannot be overstated. In various disciplines, precise pressure measurements are crucial for innovation and safety. Industries depend on these devices for quality control, loss prevention, and operational efficiency. Their significance in medical diagnostics has revolutionized how we monitor health conditions, while their application in environmental monitoring is essential for sustainability efforts.
Benefits of Citing References
- Credibility: Proper citations enhance the trustworthiness of the information.
- Contextual Awareness: They help readers understand prior research and developments in the field.
- Navigational Tools: References serve as pathways for readers to conduct further research.
"References are not just ancillary; they are an integral part of scientific rigor."
Considerations When Using References
It is vital to choose sources wisely. Quality must prevail over quantity. Peer-reviewed journals, authoritative textbooks, and articles from respected organizations provide reliable information. Avoiding dubious online content ensures that the narrative remains grounded in verified knowledge. Also, consider the timeliness of the references; outdated information can mislead or obscure advances in technology.