Exploring the Future of Additive Electronics
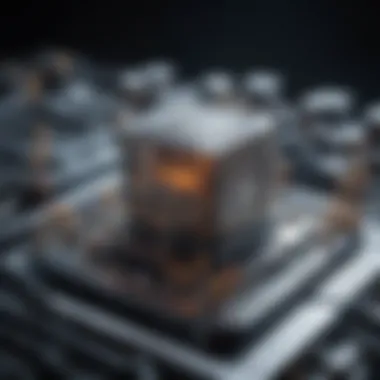
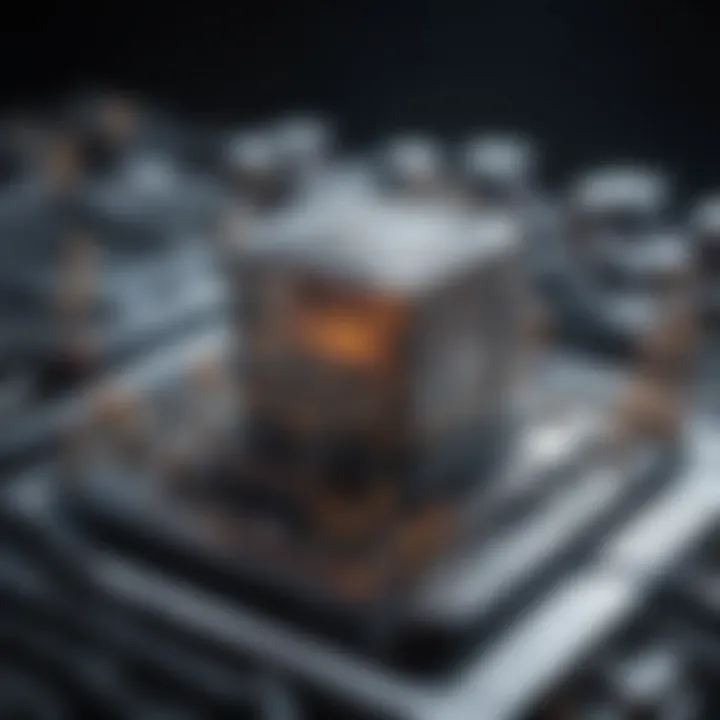
Intro
Additive electronics stands at the intersection of innovation and practicality, reshaping how electrical devices are conceived and created. This approach leverages the additive manufacturing paradigm, where materials are deposited layer by layer, enabling intricate designs that were previously unfeasible with traditional methods. By understanding the core principles of additive electronics, readers can appreciate its relevance to various applications, ranging from consumer goods to advanced electronics.
This article aims to illuminate the various facets of additive electronics, discussing not just the principles, but also its advantages and challenges. The ongoing research in this field reflects a growing interest from both academia and industry, revealing a robust landscape of potential and promise. As technology continues to advance, additive electronics propels forward, opening new pathways in manufacturing and design.
Research Methodology
Description of Research Design and Approach
The research design for this overview includes a comprehensive literature review, focusing on recent advancements in additive electronics. A systematic approach was applied to aggregate information from peer-reviewed journals, conference papers, and industry reports. The objective is to synthesize existing knowledge while identifying gaps for future exploration. Interviews with industry professionals also provided invaluable insights into current practices and trends.
Materials and Methods Used in the Study
Various materials employed in additive electronics include polymers, metals, and ceramics. The selection of materials is crucial, as each offers distinct properties that influence functionality and performance. Techniques like 3D printing, inkjet printing, and direct writing are among the most common methods utilized.
In certain instances, testing and prototyping were conducted using specific software tools like COMSOL and Autodesk, allowing simulation of additive processes. This methodology aids in understanding the complexities involved in layer construction, including adhesion and thermal effects.
Discussion and Interpretation
Interpretation of Results in the Context of Existing Literature
The accumulated data suggests that additive electronics can significantly enhance production efficiency and reduce waste. The existing literature highlights successes in creating compact electronic components through additive methods. These devices are not only lighter and smaller but also customizable to meet specific user needs.
Implications for Future Research or Practical Applications
Considering the rapid advancements, there are several implications for future research. One notable area of interest is the integration of additive electronics with smart materials, potentially leading to innovative applications in wearable technology and IoT devices. Additionally, exploring the functionality of biodegradable materials in electronics represents a crucial step toward sustainability in production.
"The evolution of additive electronics signals a paradigm shift in manufacturing, with far-reaching implications for design and functionality."
Integration of feedback from industry applications continually shapes the future of additive electronics. Further investigations may reveal ways to overcome current limitations, paving the way for broader adoption in varied sectors.
Intro to Additive Electronics
Additive electronics offers a new perspective in the realm of manufacturing electrical devices, providing insights into how layers of material can be combined to form intricate functional components. This section introduces the foundational ideas of additive electronics within the context of modern engineering and technology. Recognizing the strategic significance of this approach is imperative for anyone involved in electronics design and production.
The primary benefit of additive electronics lies in its ability to produce complex geometries that are challenging or impossible to achieve with traditional manufacturing methods. This innovative technology enables the rapid prototyping of electronic devices and creates potential for customizing components to meet specific user requirements. The implications of this process extend beyond mere manufacturing; they signify a shift toward more efficient and sustainable practices in the electronics industry.
In discussing additive electronics, it is crucial to understand the foundational definitions before exploring its historical development. Identifying the core principles allows for a deeper comprehension of its current applications and future potential.
Defining Additive Electronics
Additive electronics refers to the processes of constructing electronic devices layer by layer, utilizing various materials to build up complex structures. This contrasts with subtractive methods, where material is removed from a larger block to form components. Instead, in additive procedures, precise application of inks, polymers, and conductive materials allows for the creation of intricate pathways and connections essential in electronics.
Some prominent techniques in additive electronics include 3D printing, inkjet printing, and screen printing. Each of these methods varies in terms of the materials used and the specific applications they support. For instance, 3D printing can utilize metals, polymers, and ceramics to create components with varying degrees of functionality. The capability to customize materials lends itself to tailored solutions in many fields, from consumer devices to advanced healthcare technologies.
Historical Context
The origins of additive electronics can be traced back to the surge of interest in 3D printing technology in the late 20th century. Initially focused on rapid prototyping, the first commercial 3D printers primarily produced models and prototypes for design evaluations. Over time, developments in materials and processes led to the integration of conductive inks and materials, paving the way for their adoption in electronics manufacturing.
By the early 2000s, researchers began to recognize the potential of 3D printing not just for prototyping, but for creating actual electronic components. This marked a pivotal shift in the field, as the industry began to embrace additive manufacturing as a legitimate method for producing functional electronic devices.
Now, with advancements in nanotechnology and material science, additive electronics is poised to revolutionize how devices are created, enhancing the electronics landscape significantly. It is rational to assert that the progression from traditional fabrication to additive techniques will play a paramount role in the future of electronics, addressing challenges of efficiency and sustainability in production.
Fundamental Principles
Understanding the fundamental principles of additive electronics is crucial for grasping how this technology transforms the production of electronic devices. The essence of these principles lies in the intricate processes that bring together various materials to create complex electronic structures. These processes offer compelling advantages, such as lower material waste and enhanced design flexibility, which makes them paramount for today's fast-paced technological environment.
Layering Techniques
Layering techniques are at the heart of additive electronics, enabling the deposition of materials in successive layers to construct a final product. This method differs significantly from traditional subtractive manufacturing. In additive electronics, the focus is on build-up rather than reduction.
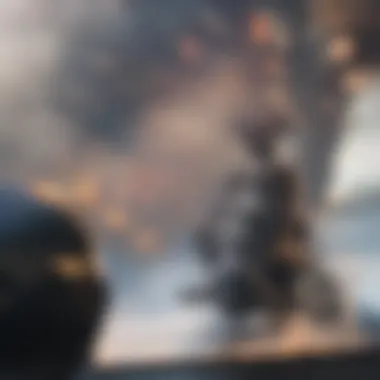
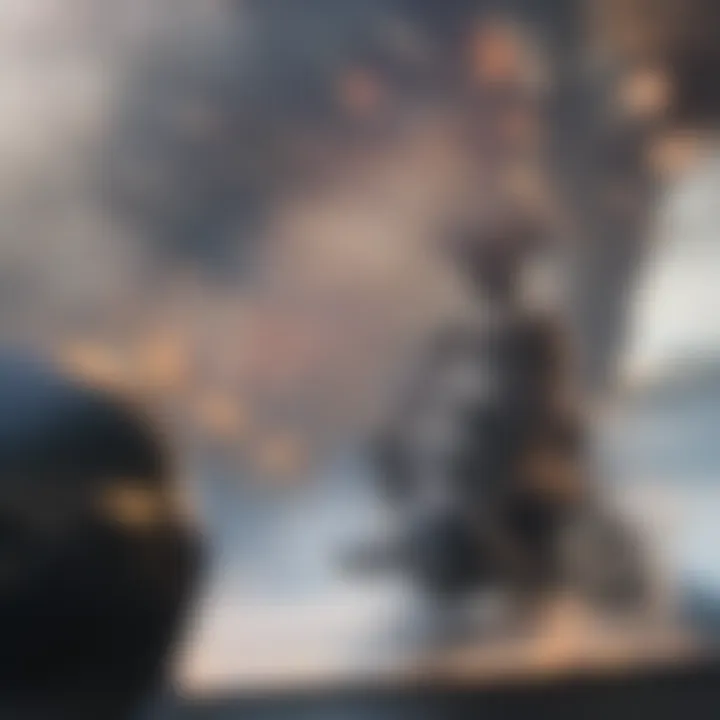
Several key layering techniques are widely implemented in additive electronics:
- Fused Deposition Modeling (FDM) - Uses thermoplastic filaments to create layers through heating and extrusion. This is common in 3D printing for various components.
- Stereolithography (SLA) - Utilizes a laser to cure liquid resin layer by layer. It achieves high precision and is particularly useful in rapid prototyping.
- Selective Laser Sintering (SLS) - Involves the use of a laser to fuse powder materials, forming solid structures. This technique is suitable for intricate designs.
Each of these techniques carries distinct benefits and trade-offs in terms of resolution, material compatibility, and scalability. Understanding these will empower designers and engineers to select the most appropriate method based on the desired application.
Material Selection
Material selection is another fundamental principle that directly affects the performance and viability of additive electronics. The variety of materials available for additive manufacturing extends beyond traditional metals and plastics. New materials, such as conductive inks and flexible substrates, have emerged, expanding the scope of possible applications.
When selecting materials, several considerations come into play:
- Conductivity - The ability of a material to conduct electricity impacts the functionality of electronic devices. Materials like silver, copper, or conductive polymers are often chosen for their superior conductive properties.
- Flexibility - In applications where devices need to be wearable or embedded in non-rigid forms, flexible materials become essential. Materials like polyimides are gaining attention for such purposes.
- Thermal Properties - The heat resistance of materials influences the durability and performance of electronic devices, especially in high-temperature environments.
Choosing the right material often involves balancing these factors while also considering cost and manufacturability. As research advances, innovations in materials science will continue to enrich the landscape of additive electronics.
"The choice of materials directly influences the design and functionality of electronic components, making it a vital aspect of additive electronics."
In summary, the fundamental principles of additive electronics revolve around layering techniques and material selection. Both elements hold critical importance in determining the efficiency and effectiveness of electronic device manufacturing. Understanding these principles lays the foundation for future advancements in the field.
Types of Additive Electronics Methods
Understanding the different methods of additive electronics is essential for appreciating their varied applications and benefits. Each technique comes with its own unique advantages and limitations. The methods used significantly influence the quality, speed, and cost-effectiveness of the production process. This section outlines the main types of additive electronics methods, highlighting specific characteristics, uses, and considerations for each.
3D Printing Techniques
3D printing has become a cornerstone of additive electronics due to its versatility and wide applicability. This technique involves creating objects layer by layer through the deposition of materials, which are then cured or solidified to form a functional component. Technologies such as Fused Deposition Modeling (FDM) and Stereolithography (SLA) are often employed in this field.
Advantages of 3D printing include:
- Complex Geometries: It allows for the construction of intricate designs that are difficult or impossible to achieve using traditional manufacturing methods.
- Customization: Products can be tailored to specific customer requirements easily, making the process highly adaptable.
- Rapid Prototyping: Designers can quickly create models for testing and evaluation.
However, this method can also present challenges, such as material compatibility and production speed.
Inkjet Printing
Inkjet printing in the context of additive electronics uses a jet nozzle to deposit tiny droplets of conductive ink onto a substrate. This method is particularly significant for creating intricate circuit designs and electronic components because of its high precision. By controlling droplet placement, manufacturers can achieve resolutions that meet the exact specifications required for modern electronics.
Key benefits of inkjet printing include:
- Precision: High resolution can enable smaller components and finer detail than some other methods.
- Material Variety: Different inks can be utilized, including conductive, insulating, and semi-conducting materials, broadening its scope.
- Less Waste: The ability to only deposit materials where needed reduces waste, promoting sustainability in production.
Yet, there are concerns over the drying time of the inks and the conditions required for their application.
Screen Printing
Screen printing has a long-standing history in the production of electronics, particularly for creating circuit boards. The method involves forcing ink through a mesh screen, which holds a stencil of the desired pattern. It is well-suited for high-volume production since it allows for the rapid application of thick layers of materials.
Advantages are:
- Speed: This technique can produce large quantities in a relatively short time.
- Cost-Effectiveness: For mass production, it often proves to be cheaper than other additive methods due to lower material costs.
- Layer Thickness: Screen printing facilitates the application of thicker materials, which can enhance conductivity in certain applications.
On the flip side, screen printing may lack the precision of other techniques and can face limitations in terms of the complexity of designs.
Direct Write Technologies
Direct write technologies involve writing conductive patterns directly onto a substrate using a material dispensing system. The approach can be likened to inkjet printing but is generally aimed at larger-scale applications or different types of materials, such as pastes. This includes techniques like aerosol jet printing and micro-dispensing.
The main strengths of direct write technologies include:
- Flexibility: Can be used on various substrates, including flexible and non-planar surfaces.
- Material Diversity: Various materials can be deposited, facilitating innovative applications.
- Precision: Offers high-resolution patterned deposition, which benefits complex designs.
Challenges include the potential for slower production speeds and the difficulty in duplicating exact patterns consistently.
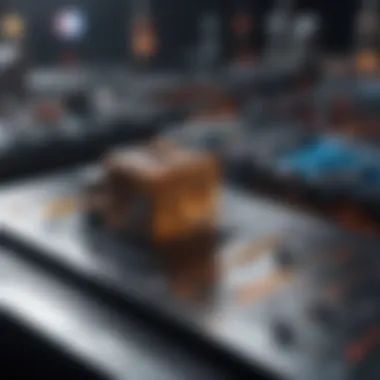
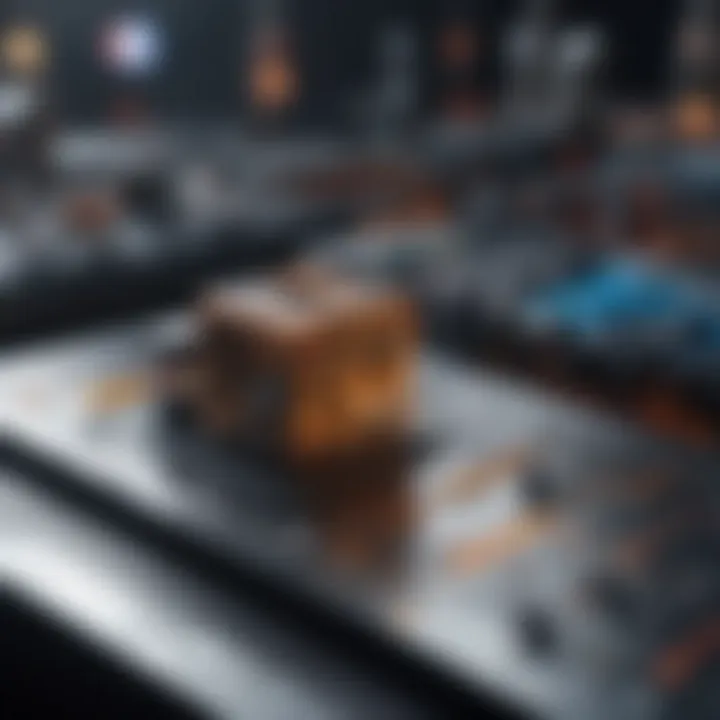
In summary, each method of additive electronics holds unique advantages and considerations. Understanding these distinctions is crucial for selecting the appropriate technique for a given application. The evolution of these methods continues to shape the landscape of electronics manufacturing.
Applications of Additive Electronics
The applications of additive electronics play a crucial role in understanding its impact on various fields. This technology is not only revolutionizing traditional manufacturing processes but also enabling innovative solutions across different industries. By integrating multi-layered structures, additive electronics can create complex functionalities that were challenging or impossible to achieve with conventional approaches. Letโs delve deeper into the most pertinent applications, highlighting their significance and potential implications.
Consumer Electronics
One of the most prominent sectors benefiting from additive electronics is consumer electronics. This field encompasses a wide range of products, including smartphones, tablets, wearables, and home appliances. The primary advantage here is the ability to produce lightweight and compact components with high functionality.
Additive manufacturing allows for tailored designs that can fit specific consumer needs. For example, a company may create flexible circuits that can be incorporated into wearable technology or intricate antennas for improved connectivity in smartphones. Furthermore, the lower material waste associated with additive processes leads to cost savings, which can be crucial for maintaining competitive pricing in a crowded market.
Healthcare Devices
The healthcare sector has seen a transformative shift with the advent of additive electronics. These technologies enable the production of highly specialized devices that cater to individual needs. For instance, 3D printing technology is used to manufacture custom prosthetics or implants. This customization ensures better fit and comfort for patients, enhancing their overall experience and health outcomes.
Moreover, additive electronics facilitate the development of advanced biosensors and diagnostic devices. These devices can monitor specific health parameters and provide real-time feedback, paving the way for more precise and timely medical interventions. The added benefit is a reduction in manufacturing complexities and time, allowing for faster delivery of essential medical devices to those in need.
Automotive Applications
In the automotive industry, additive electronics is reshaping how vehicles are designed and manufactured. With the move towards electric and autonomous vehicles, the need for lightweight yet functional components has increased. Additive technologies help address this requirement by enabling the creation of complex geometries that traditional methods cannot achieve.
In addition to weight reduction, additive electronics improves the integration of sensors and control systems within vehicles. For example, manufacturers can embed electronic components into structural parts, thus enhancing overall vehicle performance and durability. This approach not only streamlines manufacturing processes but also reduces costs associated with assembly and supply chain management.
"Additive electronics is paving the way for innovation across consumer electronics, healthcare, and automotive sectors, creating opportunities for unprecedented designs and functionalities."
Advantages of Additive Electronics
Additive electronics signifies a notable shift in the manufacturing landscape of electronic devices. This section will delve into the key advantages that additive electronics offers, thus emphasizing its relevance in the broader context of technological evolution. Various factors, such as cost efficiency, design flexibility, and material utilization, highlight why researchers, manufacturers, and industries increasingly favor this innovative approach.
Cost Efficiency
One of the striking advantages of additive electronics is its cost efficiency. Traditional manufacturing methods often require extensive material resources, leading to significant waste. In contrast, additive techniques apply materials only where necessary. By meticulously layering material, the need for excess is drastically reduced. This results in lower expenses, as companies can save on raw materials and minimize waste disposal costs.
Moreover, the shortcut in manufacturing time also contributes to cost reduction. Additive manufacturing enables rapid prototyping and testing. Companies can produce prototypes of electronic components much faster than conventional methods. This accelerates the design process and speeds up the path to market. As a result, startups and smaller firms find themselves with greater access to capabilities that were once only viable for large manufacturers.
Design Flexibility
Design flexibility stands out as another pivotal benefit of additive electronics. Traditional production techniques often impose limitations on the geometrical complexity of components. However, with additive manufacturing, intricate designs are more feasible than before. The process allows for the construction of shapes and structures that would be challenging or impossible to achieve with conventional methods.
This flexibility opens doors for innovation. Engineers and designers can experiment with unique layouts and combinations of materials, optimizing performance and functionality. For example, custom housing for electronic devices can improve thermal management and electromagnetic shielding. The result is a broadening of the design horizon, where creativity and technology intersect seamlessly.
Material Utilization
Lastly, material utilization in additive electronics warrants attention. This approach harnesses a variety of materials, including polymers, metals, and conductive inks, optimizing their properties for specific applications. The ability to mix various outputs leads to the development of hybrid materials that can serve multiple functions. For instance, a single component could possess both structural and electronic properties.
Furthermore, additive techniques allow for multi-material printing. This usage results in reduced assembly times and increased efficiency since components can be printed as a single piece. It streamlines the manufacturing process and ultimately leads to improved product reliability.
"The transition to additive electronics presents a unique opportunity to revolutionize traditional manufacturing."
In summary, the advantages of additive electronics are manifold, encompassing cost efficiency, design flexibility, and effective material utilization. As the field evolves, embracing these benefits will likely yield transformative results not only in electronics manufacturing but also across numerous sectors.
Challenges in Additive Electronics
Additive electronics, despite its promising potential, faces several challenges that can hinder its widespread adoption. These challenges necessitate thorough examination. Understanding these factors is crucial for stakeholders in the industry, including material scientists, engineers, and manufacturers.
Material Limitations
Material choices in additive electronics are critical, yet they come with limitations. While traditional electronics often rely on well-established materials like silicon, additive processes demand materials that can be precisely layered and processed. This can restrict the performance characteristics of devices fabricated through additive methods. Furthermore, many conductive inks or pastes lack the stability and conductivity of traditional materials. This limitation often results in decreased performance and reliability in final products. The challenge then lies in developing new materials suitable for this method. Researchers are actively exploring alternatives such as conductive polymers and metal nanostructures. These materials could potentially offer enhanced electrical properties and allow for more intricate designs, but their commercialization requires additional time and research.
Manufacturing Consistency
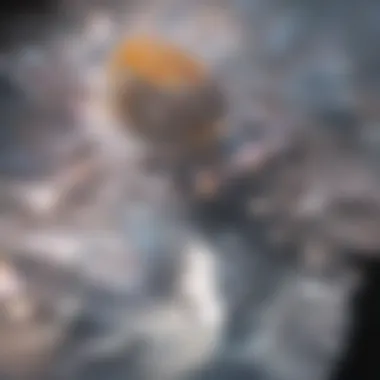
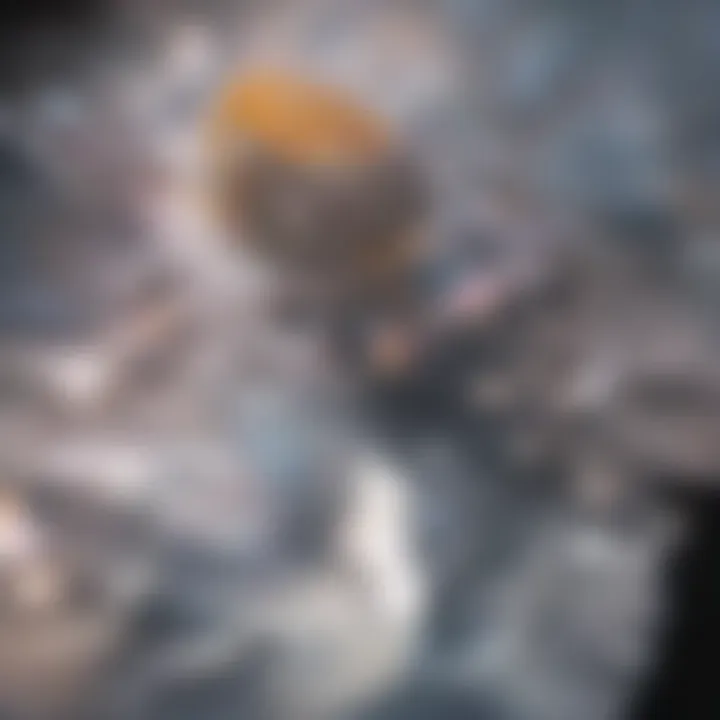
Consistency in manufacturing is another significant hurdle for additive electronics. The layer-by-layer approach that characterizes additive manufacturing can lead to variability in the final product. This inconsistency may result from several factors, including equipment calibration, environmental conditions, and even the materials used. As manufacturers aim for higher precision, even minor deviations can yield defects in the final product. The concept of zero defect manufacturing becomes complicated in the additive space. To combat this, standardization and quality assurance protocols are essential. Regular calibration of machines and stringent quality control measures can help to maintain uniformity. Unless addressed, these consistency issues could pose a challenge in markets that demand high reliability, such as aerospace or medical devices.
Regulatory Considerations
Lastly, regulatory considerations impose an additional layer of complexity in additive electronics. As this technology evolves, regulatory bodies struggle to keep up with its pace. The lack of clear standards can hinder innovation and create barriers for companies looking to enter the market. It is important for manufacturers to understand existing regulations and comply with them to avoid legal pitfalls. In many regions, regulatory standards for safety, health, and environmental considerations are still developing. This is especially relevant for healthcare-related devices, where rigorous testing is necessary to ensure patient safety. Stakeholders must engage with regulatory bodies to advocate for guidelines that consider the unique nature of additive technologies.
The challenges present in additive electronics are a double-edged sword; they require significant attention yet simultaneously spur innovation in material science, manufacturing processes, and regulatory frameworks.
In summary, while additive electronics holds immense potential, navigating the challenges related to material limitations, manufacturing consistency, and regulatory considerations is paramount for its future. Addressing these challenges head-on will not only pave the way for improved products but also enhance the overall reputation of additive electronics in various sectors.
Current Research Trends
Research in additive electronics is constantly evolving. The exploration of new materials and methods plays a crucial role in improving functionality and performance in various applications. The ongoing studies focus on enhancing efficiency, scalability, and sustainability.
Nanomaterials in Additive Electronics
Nanomaterials have gained significant attention in the realm of additive electronics. They offer unique properties that traditional materials often lack. For instance, their increased surface area and enhanced electrical conductivity can lead to better device performance. Researchers are exploring materials like graphene and carbon nanotubes for their exceptional strength and conductivity. These materials can revolutionize printed circuit boards and sensors, enabling more compact and efficient designs.
The integration of nanomaterials into additive processes also provides opportunities for innovative applications. In the healthcare sector, for example, nanomaterials can be used to create biosensors that accurately detect biological substances. Thus, advancing medical diagnoses while minimizing costs.
Integration with IoT
The integration of additive electronics with the Internet of Things (IoT) is another pivotal area of research. The IoT relies on interconnected devices that can communicate and exchange data. Additive electronics can facilitate the production of smaller, more efficient devices that serve this purpose. By utilizing additive manufacturing techniques, it becomes possible to create prototypes rapidly. This reduces the time to market for new IoT devices.
Moreover, the flexibility in design afforded by additive techniques means that we can develop customized solutions that meet specific needs in smart homes and cities. As the capabilities in additive electronics advance, so does the potential to create more efficient energy solutions. For example, integrating sensors directly into the structure of smart buildings could help monitor energy consumption in real-time.
Continued research in these areas can lead to groundbreaking applications and innovative designs that redefine industries.
In summary, both nanomaterials and IoT integration in additive electronics present exciting research opportunities. They are key to developing smarter, more efficient technologies that can benefit diverse sectors.
Future Prospects
Additive electronics is on a trajectory that points towards significant advancements and applications. The future prospects of this field are crucial as they shape the direction of technology. Understanding market trends and potential innovations will empower stakeholders to invest wisely, adapt their strategies and explore new opportunities in this evolving domain.
Trends in Market Growth
The market for additive electronics is predicted to experience substantial growth. The increasing demand for electronic devices that can be customized and produced quickly is fueling this expansion. Recent reports indicate that the global additive manufacturing market, which includes electronics, could reach billions of dollars in the coming years. Key factors contributing to this growth include:
- Customization Demand: As consumers seek personalized electronics, manufacturers are turning to additive processes to fulfill these needs efficiently.
- Sustainability Focus: With a rising emphasis on sustainable practices, companies are exploring additive methods that produce less waste and utilize materials more effectively.
- Technological Advancements: Innovations in materials and techniques lead to better performance and functionalities in electronic devices.
As these trends continue, industries will likely pivot, adapting their production lines to incorporate additive processes more seamlessly.
Innovations on the Horizon
Looking ahead, several innovations have the potential to revolutionize additive electronics. These advancements are not merely incremental; they have the capacity to redefine how electronics are designed and fabricated. Some notable areas of innovation include:
- Advanced Materials: New conductive inks and materials are being developed. These can enhance device performance and reliability.
- Integration with AI: The incorporation of artificial intelligence into additive manufacturing processes could optimize production, reduce errors, and facilitate real-time adjustments.
- Bioprinting: Innovations in bioprinting technology could lead to developments in healthcare electronics, creating devices that are biocompatible and optimized for medical applications.
- Flexible Electronics: As the demand for wearables and other flexible devices increases, advancements in producing flexible circuits through additive methods will become crucial.
"The convergence of additive manufacturing with emerging technologies promises to reshape the electronics landscape profoundly."
In summary, the future of additive electronics is promising, fueled by market growth and innovative developments that could fundamentally change the industry. Stakeholders should remain attentive to these shifts, as they hold the key to competitive advantage and technological leadership.
End
In this section, we articulate the critical role of additive electronics within the modern manufacturing landscape. The significance of this technology extends beyond its innovative production methods; it encapsulates a paradigm shift that influences multiple industries, from consumer electronics to automotive sectors. As we have explored, additive electronics not only fosters design flexibility and material efficiency but also poses certain challenges that require thoughtful consideration and ongoing research.
Summarizing Key Points
Throughout this article, we have covered numerous facets of additive electronics. The core topics include:
- Defining Additive Electronics: Understanding what constitutes additive manufacturing and its principles.
- Applications Across Industries: Highlighting uses in consumer electronics, healthcare devices, and automotive applications.
- Advantages: Discussing benefits such as cost efficiency, design flexibility, and enhanced material utilization.
- Challenges: Acknowledging hurdles like material limitations, manufacturing consistency, and navigating regulatory frameworks.
- Research Trends: Examining findings in nanomaterials and their integration with IoT devices.
- Future Prospects: Exploring market growth trends and potential innovations on the horizon.
The interplay of these elements underscores the dynamic nature of additive electronics and its transformative potential. As this field progresses, it will play an increasingly vital role in shaping the future of electronic devices.
Implications for the Future
The implications of additive electronics are manifold. With advancements in technology, the ability to produce sophisticated electronic devices at a lower cost will likely enhance accessibility and adoption across various sectors. Emerging trends such as the integration of nanomaterials may lead to devices that not only work better but are also greener and more sustainable.
Moreover, as the Internet of Things (IoT) continues to evolve, the demand for innovative electronic components will rise. Additive electronics can meet this demand through rapid prototyping and the ability to create tailored solutions that traditional manufacturing methods cannot easily replicate. This adaptability will be crucial in navigating an increasingly complex technological landscape, where customization and speed are key.