In-Depth Insights into Selective Laser Sintering Technology
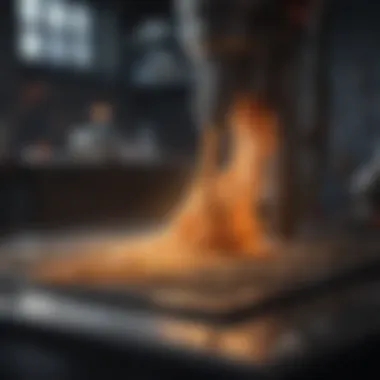
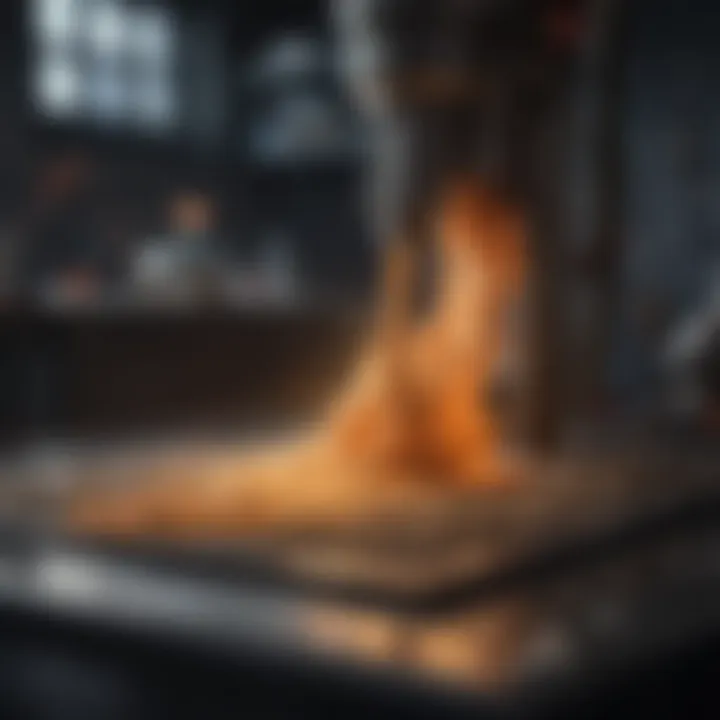
Intro
Selective Laser Sintering, often abbreviated as SLS, stands as a cornerstone in the realm of additive manufacturing. It represents a transformative leap in how we approach the creation of parts and prototypes. The technology allows for intricate designs and shapes that traditional manufacturing methods often struggle to produce efficiently. With SLS, a laser selectively fuses powder particles together, layer by layer, until the desired object takes shape. It is not merely a passing fad; it has fundamentally reshaped industries such as aerospace, automotive, and healthcare.
The upcoming sections will break down the essential components of SLS. We will investigate the materials utilized in this process, understand its applications across sectors, and consider its future trajectory. Furthermore, we’ll explore the benefits and constraints of using SLS technology in various scenarios. Instead of skimming over these complex topics, the aim is to provide an insightful overview that empowers readers to grasp the nuances of SLS and its implications in contemporary manufacturing.
We will also delve into the standard post-processing techniques that follow the SLS process. These methods can significantly impact the final quality and functionality of the produced parts. By dissecting these aspects, we prepare the ground for a detailed analysis of how SLS operates and where it is headed in the future.
Through this examination, our goal is to shed light on the intricate interplay of technology and innovation that defines SLS, giving readers the tools to not just understand but engage with this pivotal manufacturing process.
Foreword to Selective Laser Sintering
Selective Laser Sintering (SLS) stands out as a pivotal technology in the realm of additive manufacturing. By comprehending SLS, one can appreciate how it bridges the gap between innovative design and functional production. This section will delve into why understanding this technology is not just beneficial, but essential for anyone involved in manufacturing, engineering, or design.
Definition and Overview of SLS
At its core, Selective Laser Sintering is an advanced 3D printing process that employs a high-powered laser to fuse powdered materials into solid structures. It primarily utilizes various polymers, metals, and ceramic powders, selectively sintering them layer by layer. The beauty of SLS lies in its precision, allowing for the creation of intricate designs that traditional manufacturing methods often struggle to achieve. This technology is instrumental in enabling rapid prototyping, making it easier for designers to iterate their ideas without the lengthy lead times typically associated with conventional techniques.
Moreover, SLS produces parts that are strong and durable, which is a significant advantage. As a result, this process has found its footing in diverse industries, ranging from aerospace to healthcare, underscoring its versatility and reliability in producing end-use products. Readers can expect a rich understanding of how SLS serves as a catalyst for innovation in manufacturing.
Historical Context and Development
The inception of Selective Laser Sintering can be traced back to the mid-1980s. The technology was first conceptualized by Dr. Karl Jacobson, who sought to revolutionize manufacturing by employing laser technology. In 1988, it gained traction when 3D Systems introduced this method to the market, effectively planting the seeds for the future of additive manufacturing.
Over the years, SLS has evolved, driven by advancements in both material science and laser technology. Initially limited to simple forms of polymer powders, the process has broadened its horizons; now, it accommodates a variety of materials including metals and ceramics. This transformation has allowed engineers and designers alike to harness SLS for more than just prototypes but also for functional parts that meet rigorous industrial standards.
Key milestones in SLS development include the refinement of laser technology, leading to faster sintering times and enhanced material properties. The introduction of a wider range of materials has further expanded its applications and effectiveness. As the field of additive manufacturing continues to evolve, so does the journey of SLS—adapting to new challenges and opportunities that arise in modern manufacturing.
The Mechanics Behind SLS
Understanding the mechanics of Selective Laser Sintering (SLS) is crucial for grasping how this innovative technology operates and its implications for various industries. The heart of SLS lies in its two pivotal components: laser technology and the sintering process itself. Together, they form a system that enables the creation of intricate parts with remarkable precision.
Laser Technology Used in SLS
At the core of SLS is the laser, a marvel of modern science that plays an essential role in the sintering process. These lasers, often categorized by their wavelength and power output, melt or fuse the material layer by layer based on a 3D model. Typically, a CO2 laser is employed, known for its effectiveness and reliability.
SLS lasers function by scanning across the powder bed, heating specific areas to the point where the particles begin to fuse, effectively forming a solid object. This not only allows for high levels of detail but also opens up possibilities for the creation of complex geometries that conventional manufacturing methods struggle to achieve.
"Selective Laser Sintering transforms an idea into a tangible object through the precise manipulation of laser energy."
The advantages of utilizing laser technology in SLS are manifold: it offers exceptional control over the melting process, high-speed capabilities, and ultimately enables the production of sturdy, lightweight components. However, there are considerations to keep in mind; the cost of the equipment and the operational expertise required can be significant barriers for some organizations.
Sintering Process Explained
The sintering process is where the magic truly happens in SLS technology. After the laser has do its job on the initial layer, a new layer of powder is spread across the previous one, and the process is repeated, building up the part incrementally. This layer-by-layer approach allows for intricate details and structures to be realized.
During the sintering stage, a carefully balanced temperature is critical. The heat must be sufficient to bring the particles close to their melting point without fully melting them, allowing for the creation of solid parts through the fusion of particles. This balance preserves the strength and integrity of the newly formed structure, making it essential to monitor the conditions meticulously throughout the process.
This process generates several benefits:
- Complexity: Parts with internal channels, intricate designs, and custom fittings are possible.
- Material Variety: A wide range of materials, including polymers, metals, and ceramics, can be processed using SLS, bringing versatility to the table.
- Waste Reduction: Unlike traditional methods that cut away excess material, SLS only uses what is needed, making it a more efficient choice environmentally.
However, challenges do arise during sintering. For instance, achieving a uniform thermal profile can be tricky, leading to warping or distortion in some cases. Manufacturers often need extensive knowledge and practice to optimize the sintering conditions, showing that while SLS technology offers vast potential, it remains a nuanced field that requires expertise.
Materials Used in SLS
The materials selected for Selective Laser Sintering play a crucial role in defining the quality and application range of the finished products. The choice of material affects everything from mechanical properties to thermal resistance, thus shaping end-user experience. In this section, we will delve into various materials used in SLS, specifically focusing on polymers, metals, and ceramics. Understanding these materials helps the reader appreciate their unique characteristics and implications in the world of additive manufacturing.
Commonly Used Polymer Powders
Polymers are at the heart of many SLS applications, particularly in prototyping and small-scale production. Material types like Nylon 12, which boasts excellent strength and flexibility, lead the pack in popularity. Its resilient nature makes it ideal for producing intricate designs with high detail.
Key Benefits of Commonly Used Polymer Powders:
- Versatility: They can be tailored for various applications, addressing different needs in industries ranging from consumer goods to aerospace.
- Cost-Effectiveness: Compared to metals, polymer powders like polystyrene and Nylon are generally less expensive, which makes SLS viable for startups and small businesses.
- Post-Processing Friendly: These materials allow for various finishing techniques, ensuring the final product can meet aesthetic and functional requirements without extensive modifications.
However, the usage of polymers is not without its challenges. Limited thermal resistance and lower durability compared to metals might deter their adoption in certain engineering fields. Thus, while they are often the go-to choice, there are considerations to keep in mind.
Metallic Materials in SLS
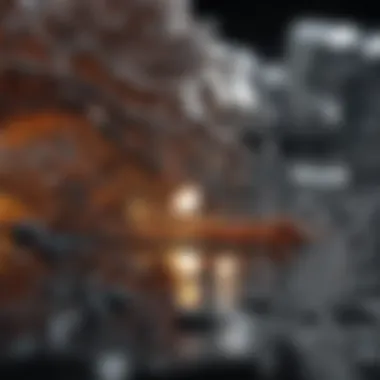
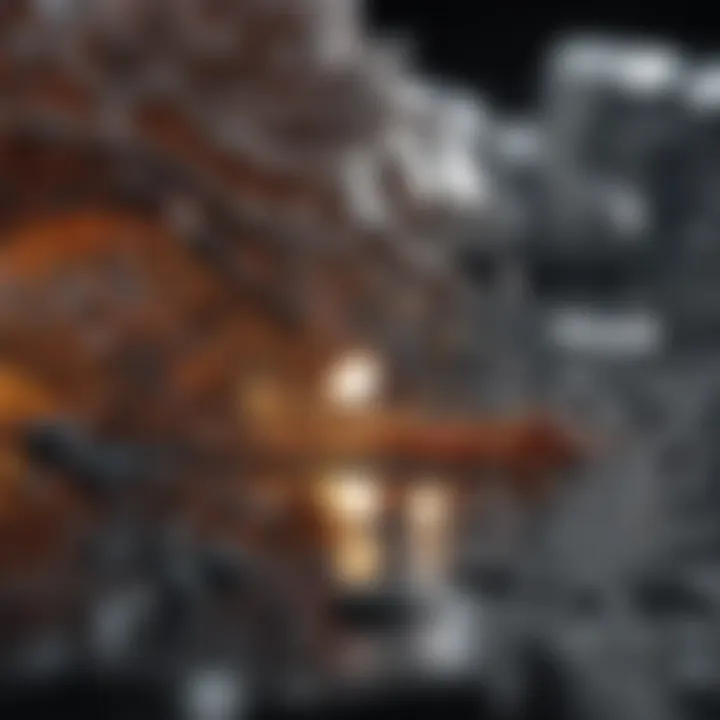
Metallic powders in SLS bring a whole new level of sophistication to additive manufacturing. Stainless steel, titanium, and aluminum are among the frontrunners here. Each offers unique properties that cater to specialized sectors.
Advantages of Metallic Materials:
- Mechanical Strength: Metals like titanium alloys are incredibly strong, making them suitable for high-stress applications, particularly in the aerospace and automotive sectors.
- Heat Resistance: Many metallic materials maintain integrity at high temperatures, which is crucial for components that will face extreme environmental conditions.
- Functional Parts: Unlike polymers, metal powders can be used to create parts that require high performance and functionality, reducing the need for further machining.
Yet, entering the realm of metallic SLS comes with its own set of issues.
- Higher Costs: The production costs can be significantly more than that of polymer powders, potentially making the process less accessible for individual users or smaller companies.
- Complicated Post-Processing: Parts often require additional surface treatments or technologies like machining to achieve desired finishes and tolerances.
Ceramics and Composites in SLS
While less common, ceramics and composites are making headway into the SLS landscape. Particularly valued for their properties like heat resistance and lightweight characteristics, they open new possibilities for specialized applications.
Key Features of Ceramics and Composites in SLS:
- Durability and Hardness: Ceramics like alumina are known for their robustness and abrasion resistance, which can be a significant advantage in harsh environments.
- Low Density: This characteristic makes ceramic fabrics attractive for industries where weight saving is paramount, such as aerospace.
- Chemical Resistance: Ideal for applications in industries like pharmaceuticals or chemical processing, where interaction with substances must be minimized.
That said, the brittleness of ceramics poses challenges. Parts can break easily under stress, which means careful consideration must be taken in design and application.
In wrapping up this section, it's evident that the materials used in SLS each offer distinct characteristics. Makers need to weigh these factors carefully to ensure that the right material aligns with their project requirements and desired outcomes.
Applications of SLS Technology
Selective Laser Sintering (SLS) technology has carved its niche across various industries, bringing about transformative changes that enhance production processes and product design. From rapid prototyping to intricate applications in aerospace, healthcare, and automotive sectors, SLS is invaluable. Understanding its applications provides insight into its benefits and considerations, illustrating how it shapes the future of manufacturing.
SLS in Prototyping
Prototyping is one of the most common applications of SLS. The technology allows designers and engineers to create functional prototypes with complex geometries that traditional methods struggle to achieve. This capability not only shortens the product development cycle but also reduces costs associated with multiple toolings. Since prototypes can be built directly from 3D CAD data, adjustments can be made on-the-fly, saving both time and resources.
Moreover, prototypes created with SLS can be tested under real-world conditions. For example, a company like Nike utilizes SLS to produce prototypes for their shoe designs, enabling them to test ergonomics and performance before committing to large-scale production.
SLS in Aerospace Industry
In the aerospace sector, SLS breathes life into lightweight designs without compromising strength and durability. Components like brackets, housings, and even entire ducting systems have been successfully produced with this technology. The ability to produce highly customized part shapes means that engineers can design components that fit their specific needs, rather than adhering to traditional limitations.
Boeing, for instance, employs SLS for producing parts that contribute to significant weight reductions, positively impacting fuel efficiency. Given that in aviation, even small weight savings can yield substantial economic benefits, the value of SLS here cannot be overstated.
SLS in Healthcare Solutions
The healthcare industry has also felt the influence of SLS. It's not just about manufacturing tools or implants but encompassing a broader spectrum of personalized medicine. Custom prosthetics and dental devices can be precisely manufactured for individual patients, improving comfort and fit.
For instance, companies like Align Technology use SLS to produce clear aligners designed specifically for patients’ teeth, allowing for a blend of aesthetic appeal and medical efficacy. Moreover, surgical models created through SLS offer surgeons a more accurate picture pre-operation, enhancing preparation and outcomes.
Automotive Applications of SLS
Automotive manufacturing has seen a significant uptake in SLS technology as well. The design teams are leveraging SLS for making lightweight components that simultaneously ensure structural integrity. From functional prototypes that undergo testing for aerodynamics, to production parts that go directly into vehicles, SLS has proven its worth.
Car manufacturers, such as Ford, utilize SLS to produce intricate parts that aid in vehicle performance and efficiency. With SLS, parts can be manufactured on demand, reducing inventory costs and expediting the supply chain.
"The flexibility of SLS allows us to innovate at a pace that was previously unimaginable in the automotive sector."
In summary, the applications of SLS technology represent a significant advancement in how products are developed and manufactured across various industries. By facilitating rapid prototyping, enhancing aerospace designs, offering personalized healthcare solutions, and revolutionizing automotive part production, SLS continues to challenge and redefine traditional manufacturing paradigms. As industries evolve, SLS stands at the forefront, eager to tackle upcoming challenges and opportunities.
Advantages of Selective Laser Sintering
Selective Laser Sintering (SLS), as a cornerstone of additive manufacturing, brings a multitude of advantages that can significantly transform production processes across various industries. Understanding these benefits is crucial, not only for those directly involved in the manufacturing sector but also for students, researchers, and professionals looking to leverage this technology for innovation. The advantages of SLS stretch from enhanced design flexibility to improved material efficiency, marking it as a leading choice for modern manufacturing.
Design Flexibility in SLS
One of the standout features of SLS is its remarkable design flexibility. Unlike traditional manufacturing methods that can impose strict limitations on geometry, SLS allows for the creation of complex shapes and intricate designs without any significant compromise on strength or durability.
Why does this matter? With SLS, designers have the freedom to explore unconventional forms that were previously impractical or outright impossible to achieve. For instance, think of custom prosthetic limbs molded to fit an individual's anatomy perfectly or intricate latticed structures that actively reduce weight without sacrificing stability. This innovation in design opens up a world of possibilities, unshackling creativity and allowing engineers to push the envelope on what is possible with any manufactured product.
Moreover, this flexibility makes the technology ideal for producing small batches of unique components. It’s not just about mass production anymore; it’s about tailoring products to meet specific demands or niche markets, which can be a game-changer in industries like fashion or bespoke automotive parts.
Material Efficiency and Waste Reduction
In a world becoming increasingly conscious of sustainability, the material efficiency of SLS paints a very appealing picture. This technology employs a powder-based method, meaning that after a part is printed, any unfused powder can be recycled for future builds. It’s estimated that around 85% of the powder can be reused, drastically reducing waste compared to traditional machining processes that cut away material from solid blocks.
"The more we recycle, the more sustainable our practices become, fostering a better environment for future generations.”
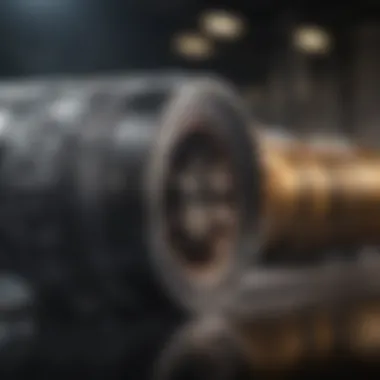
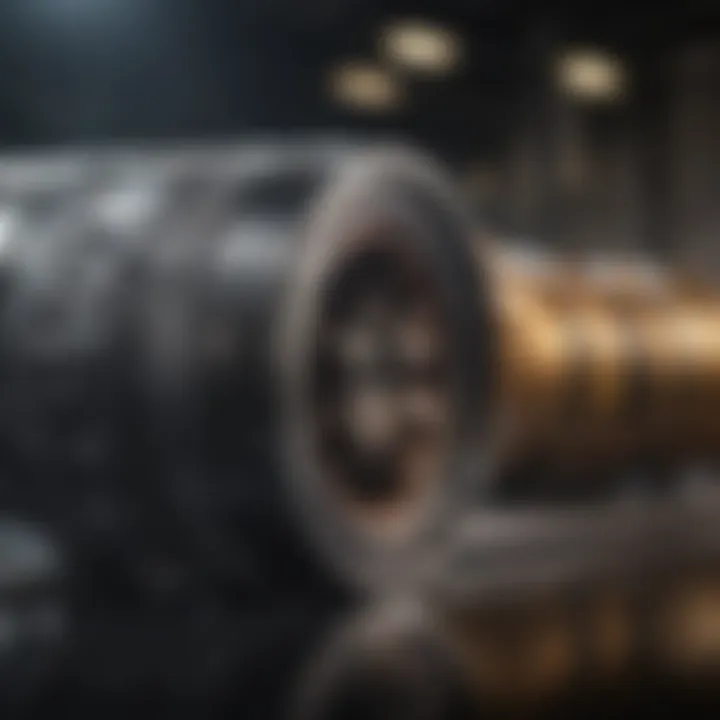
Using SLS not only conserves materials but also translates into cost savings over time. Manufacturers are able to stretch their budgets further with less raw material waste, leading to a more sustainable and economically viable production model.
Scalability of Production
Scalability is a vital consideration in manufacturing, and SLS technology excels in this area, allowing businesses to adapt quickly as demands change. Whether you need to increase production for a specific product line or scale down for a seasonal offering, SLS makes adjusting output a seamless process.
This adaptability stems from its layer-by-layer approach, enabling quick changes in design iterations, or even switching to different materials, all in a single setup. Because SLS systems can run unattended, manufacturers can achieve higher productivity rates without the need for significant labor increases. Furthermore, once the initial setup is complete, additional copies of the same part can often be produced quickly and without extra tooling costs, making it an attractive option for both large companies and startups alike.
Limitations of SLS Technology
Exploring Selective Laser Sintering (SLS) also means acknowledging its limitations. Understanding these challenges is vital for both current users and those considering this technology for the first time. By recognizing these limitations, one can make informed decisions that align with project requirements, budget constraints, and desired outcomes. Each limitation provides an opportunity for innovation and improvement in the broader additive manufacturing landscape.
Surface Finish Concerns
One of the prominent issues with SLS is the surface finish of the final parts. While SLS can produce complex geometries that are difficult to achieve with traditional methods, the texture can often be gritty or rough. This is primarily due to the grainy nature of the powder particles used in the process itself. For applications where aesthetics or tight tolerances are crucial, this roughness can be a significant drawback. Post-processing techniques, such as sanding or polishing, can mitigate these issues but can also add time and cost to the production cycle.
- Post-Processing Techniques: Some common practices include:
- Sanding: This can improve the surface feel but may alter dimensions slightly.
- Bead Blasting: This may enhance surface appearance but isn’t suitable for detailed features.
- Chemical Smoothing: Some polymers can be smoothed chemically, providing a glossy finish but potentially weakening the part's strength.
The choice of post-processing depends largely on the end use of the part, leading many manufacturers to weigh the need for a smooth finish against potential delays in production.
Cost Considerations for SLS
Cost is always a critical factor in any manufacturing technology. SLS does present a unique set of financial challenges. The initial investment in an SLS machine can be hefty—often requiring tens of thousands to hundreds of thousands of dollars. Material costs can also be significant, especially for high-performance polymers and metals.
- Operating Costs: In addition, factors such as:
- Energy Consumption: SLS machines consume a considerable amount of energy, impacting operational costs.
- Maintenance: High-tech equipment requires regular maintenance and potential upgrades to keep it running smoothly.
- Material Waste: Even though SLS is more efficient than many subtractive methods, materials that aren't fully fused contribute to overall waste and expense.
Balancing these costs against the benefits and potential savings from increased design freedom can be a difficult equation for manufacturers.
Production Speed Limitations
When it comes to production speed, SLS holds its own against other additive manufacturing methods, yet it still has inherent limitations. The build process can be slow, especially for complex or large parts. Each layer must be heated and sintered, which takes time—adding up considerably during larger runs.
- Factors Affecting Speed: Some elements that play into production speed include:
- Layer Thickness: Thicker layers can speed up the process at the expense of resolution.
- Part Density: The more dense the part, the longer it may take to print due to increased material requirements.
- Machine Calibration and Maintenance: A well-tuned machine processes faster, but frequent issues can slow down output.
Overall, patience is necessary when leveraging SLS technology for production, especially for larger volumes, and this can influence timeline forecasts and project duration.
By understanding the limitations of SLS, manufacturers can better strategize their approach, whether they are focusing on optimizing budgets, improving surface quality, or adjusting production timelines.
Post-Processing Techniques for SLS Parts
Post-processing of Selective Laser Sintering (SLS) parts is a crucial step that can greatly enhance the performance, appearance, and overall quality of 3D printed components. Once an SLS object comes out of the printer, it's not necessarily ready for use. There are certain techniques and processes that need to be applied to ensure that products meet specific functional and aesthetic criteria. This section will take a closer look at the various post-processing methods, highlighting why they matter and how they can contribute to the final output.
Removal of Unfused Powder
One of the first steps in post-processing SLS parts is the removal of unfused powder. During the SLS process, not all powder particles fuse together; many remain unfused and can easily be removed after printing. This process usually involves careful brushing or blowing away the excess material. Properly removing this powder is vital for several reasons:
- Aesthetic Quality: Unfused material can mar the finish of parts, leaving them looking rough or unprofessional.
- Functional Integrity: Excess powder can interfere with the function of moving components or assembled parts.
- Weight Reduction: Stripping away unnecessary powder helps in achieving the desired weight for the application.
In some cases, specialized equipment like vibrating tables can be utilized to help separate the unfused powder from the final part more effectively.
Surface Treatment Methods
Once the unfused powder is cleared away, the next hurdle is enhancing the surface quality. Surface treatments can significantly improve the visual appeal and durability of SLS parts. Common methods include:
- Sanding: This can smooth out rough surfaces, making them more appealing to the eye. It’s a manual, yet effective approach.
- Chemical Smoothing: Using solvents or chemical baths can help create a seamless finish by melting the surface layer of the material, allowing for better structural integrity.
- Coating: Applying paints, varnishes, or sealants can also enhance the finish of SLS parts while providing an additional layer of protection against environmental damage.
The selection of a particular surface treatment often depends on the material used and the application of the part, but the goal is typically to achieve a higher level of finish and performance.
Enhancing Mechanical Properties
To bolster the performance of SLS parts, enhancing mechanical properties is often necessary. Various methods to achieve this include:
- Heat Treatment: This process can relieve stresses and improve the overall strength of the material. Proper heat treatment can immensely change the properties of polymers and metals alike.
- Post-Curing: For parts made from photopolymers, exposing them to UV light can improve hardness and reduce brittleness, thereby extending the lifespan of the component.
- Reinforcement: In some instances, integrating additional materials through processes like impregnation can lead to increased strength and durability, essential for high-load applications.
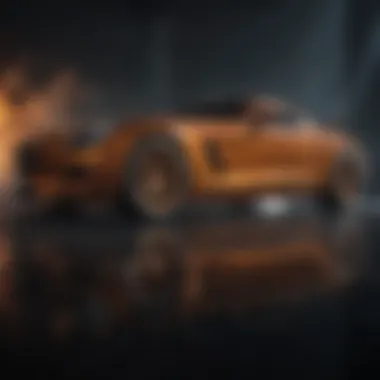
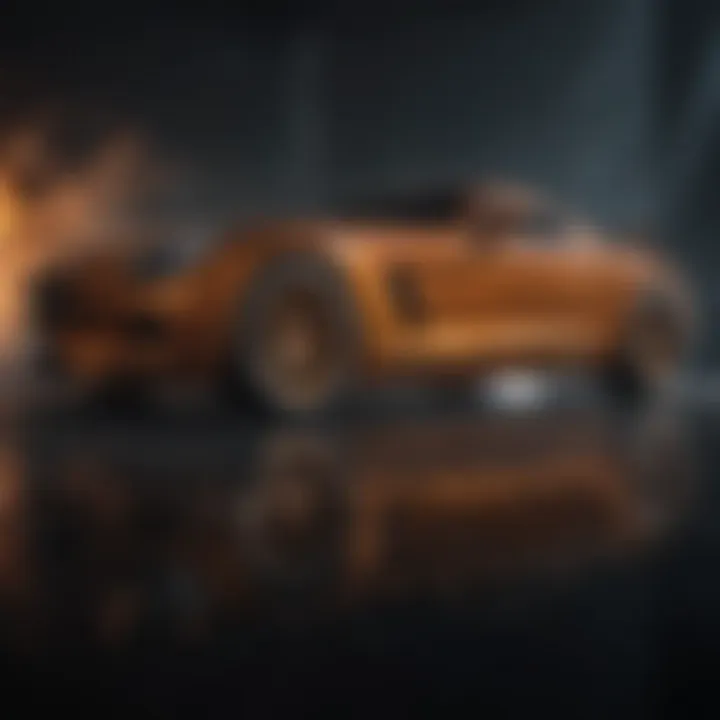
Overall, effective post-processing techniques are indispensable in making SLS parts not only usable but also competitive in the market. These methods emphasize the importance of thorough finishing processes in achieving high-quality results in additively manufactured products.
"Effective post-processing techniques can mean the difference between an average part and one that excels in performance and aesthetics."
In summary, the various techniques available for post-processing SLS parts not only ensure that items meet aesthetic standards but also significantly augment their functionality, making them more valuable in their respective applications.
Future Trends in SLS Technology
The landscape of Selective Laser Sintering is constantly evolving, and understanding its future trends is vital for anyone invested in the field, from curious students to seasoned professionals. This section aims to illuminate how these developments may redefine additive manufacturing by addressing** innovation, equipment advancements, and integration** with other manufacturing processes.
Innovations in Material Science
In the world of SLS, materials are the backbone of technology. In the near future, we can expect revolutionary innovations in material science that could broaden the horizons of what SLS can achieve. For instance, researchers are delving into advanced polymers that boast enhanced mechanical properties and thermal stability. This could lead to lighter, stronger parts suitable for more demanding applications.
Moreover, there’s a growing interest in bio-based materials and materials that can be recycled effectively. Such advancements not only promise to enhance performance but also address sustainability, an ever-increasing concern in manufacturing.
"The future of manufacturing isn’t just about building; it’s about building smartly and sustainably."
Additionally, hybrid materials that combine ceramics and metals are gaining traction. These composite materials can withstand extreme conditions, making them ideal candidates for aerospace and automotive industries. As the exploration of powder formulations continues, we may witness a diversification in material properties, enabling unique applications that were previously unimaginable.
Advancements in Equipment and Software
Tremendous strides are being made in the equipment used for SLS. Next-gen SLS machines are becoming more sophisticated and user-friendly, simplifying the journey from design to part production. Features like automated powder handling systems and built-in monitoring tools are becoming commonplace, streamlining the workflow and enhancing precision and safety.
The role of software cannot be overlooked. Sophisticated design software is evolving, allowing for more detailed simulations and optimizations of the sintering process before production begins. AI and machine learning are increasingly being integrated into these programs, enabling predictive analytics that can foresee potential issues, thereby minimizing errors and waste.
Furthermore, real-time data analysis can provide insights into improving print quality and performance. This kind of leap in software capabilities will help reduce downtime and enhance overall productivity on the manufacturing floor.
Integration with Other Manufacturing Techniques
As we move forward, a key trend will be the integration of SLS with other manufacturing techniques. This hybrid approach will capitalize on the strengths of various technologies, enabling seamless workflows. For example, combining SLS with traditional manufacturing methods such as CNC machining or injection molding can produce components that are not only complex in geometry but also superior in strength and finish.
Dual-process manufacturing is emerging as a significant area of interest. For instance, you might find parts that undergo initial build using SLS, followed by finishing processes in CNC. This could lead to faster production cycles and more efficient use of resources.
Moreover, additive manufacturing wouldn't stand alone as traditional methods remain vital. When combined effectively, these approaches can shorten lead times and enhance product customization. The capability to tailor solutions based on specific needs has never been more critical, especially in sectors where precision and agility are paramount.
Implications of SLS on Manufacturing
Selective Laser Sintering (SLS) isn't just a buzzword in the realm of additive manufacturing; it fundamentally alters the landscape of how products are designed and produced. Understanding the implications of SLS extends beyond mere curiosity; it's crucial for any stakeholder in the manufacturing sector, from engineers to business strategists. This section delineates both the transformative impacts SLS has on traditional manufacturing methods and the sustainability considerations that arise from its use.
Impact on Traditional Manufacturing Methods
The advent of SLS can be likened to a breath of fresh air in a sometimes stagnant industry. Traditional manufacturing methods, such as injection molding and CNC machining, often demand lengthy lead times, substantial tooling costs, and labor-intensive processes. SLS, on the other hand, offers a more streamlined approach. With the ability to create complex geometries that were previously unthinkable, SLS allows designers to explore innovative concepts without the constraints of traditional techniques.
- Rapid Prototyping: SLS enables faster iterations of prototypes. Designers can produce and test multiple versions quickly, reducing the time from concept to market significantly.
- Reduced Waste: Traditional methods often lead to a lot of scrap material. With SLS, the creation process uses only the material that's needed, which leads to less waste.
- Customization at Scale: In a world that increasingly favors personalization, SLS can produce multiple unique items in a single production run without changing the tooling.
In practice, this means that businesses leveraging SLS can quickly adjust to market demands and consumer preferences, eliminating the risk of overproduction.
"SLS technology invites a kind of creative freedom that traditional methods simply can't match, leading to a renaissance of product innovation."
Sustainability Considerations
As the manufacturing world grapples with the urgent need for sustainable practices, SLS presents both opportunities and challenges. The environmental impact of manufacturing is under a microscope, and SLS aligns with this scrutiny in certain respects.
- Material Efficiency: The way SLS works minimizes raw material usage. Any unused powder can often be recycled for future prints, meaning less strain on material suppliers and lower overall energy consumption in the material lifecycle.
- Localized Production: SLS can be implemented closer to where the end product is needed, cutting down on transportation emissions. This localization and potential for on-demand production can significantly reduce the carbon footprint associated with traditional supply chains.
But it's not all smooth sailing. There are concerns regarding the type of materials used in SLS, especially with synthetic polymers. As engineers look to innovate, the challenge lies in developing bio-based or recycled materials that can meet SLS's demanding requirements without compromising their properties.
Culmination and Reflections on SLS Technology
As we wrap our exploration into the world of Selective Laser Sintering, it’s essential to consider its significance not just as a manufacturing process but as a transformative technology in its own right. In today’s landscape of rapid innovation, SLS stands out for a few key reasons. It enables the creation of highly complex geometries that traditional methods often struggle with. Moreover, this versatility opens doors to new applications across various sectors from aerospace to healthcare, reshaping how products are conceived, developed, and produced.
Summary of Key Insights
Reflecting on the journey through SLS technology, several insights emerge. First, the fundamental principle of SLS—layering powder materials and selectively melting them—illustrates a shift from subtractive to additive manufacturing approaches. This means not only can manufacturers create intricate designs, but they can also do so with greater material efficiency.
- Material Variety: The availability of both polymer and metal powders allows a broad range of applications.
- Prototyping and Production: SLS serves both as a prototyping tool and a method for producing end-use parts. Each iteration can be tested and refined, speeding up time-to-market.
- Sustainability: Although challenges remain, SLS can contribute to more sustainable practices through reduced waste and the ability to recycle materials.
The reflection on these aspects prompts further inquiry into how SLS technology is positioned against traditional manufacturing methods. While SLS presents benefits, it also carries its own set of challenges, particularly concerning production speed and surface finish.
Visions for Future Research
Looking ahead, the road for SLS technology is laden with potential. Future research could dive deeper into several crucial areas:
- Innovative Materials: Exploring new composite and biodegradable materials could expand SLS applications dramatically.
- Automation and Software: Enhanced automation technologies paired with sophisticated software could streamline the process, making SLS more accessible.
- Hybrid Manufacturing Techniques: Integrating SLS with other manufacturing methods may yield hybrid solutions that maximize strengths and mitigate weaknesses.
The path forward for SLS technology hinges on creativity and innovation, inviting a collaborative approach among researchers, industry professionals, and material scientists.