Low Density Polyethylene Powder: Key Insights and Trends
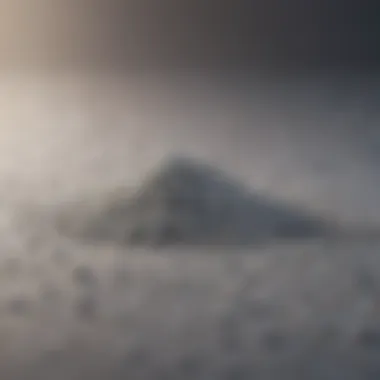

Intro
Low density polyethylene (LDPE) powder has carved a vital niche in various industries due to its unique properties and versatility. More than just a basic compound, this material emerges from a complex interplay of molecular structure and production dynamics. Its wide assortment of applications spans multiple sectors, including packaging, construction, and even the automotive industry. Understanding LDPE powder better means delving into why it has gained such traction and how it may continue to evolve in a world increasingly focused on sustainability.
Its chemical makeup is a significant determinant of its characteristics. LDPE is created through the polymerization of ethylene, leading to a branched structure that is more flexible compared to its high-density counterparts. This flexibility makes LDPE powder both lightweight and resilient, qualities that allow it to serve diverse functions.
In exploring the topic, factors such as production methods, current market dynamics, eco-friendly alternatives, and the future direction of LDPE powder are examined. Each aspect intertwines, creating a intricate yet fascinating portrait of a material that is becoming increasingly relevant in modern discussions about sustainability and industrial innovation.
To give a clearer understanding of the topic ahead, we steer into the research methodology employed to analyze LDPE powder in various contexts.
Intro to Low Density Polyethylene Powder
Low Density Polyethylene (LDPE) powder is a multidimensional material that has carved out a niche for itself in various industries. Understanding the characteristics and applications of LDPE powder is not merely an academic exercise; it has significant implications for innovation, sustainability, and economic growth. It serves as the foundation for countless applications, from packaging materials to medical devices. This section will delve into essential aspects of LDPE powder, illuminating its significance in contemporary material science and commercial use.
Definition and Overview
Low Density Polyethylene powder is a thermoplastic made from the polymerization of ethylene monomers. Its defining features include a branched molecular structure, which results in a lower density compared to other forms of polyethylene, such as high-density polyethylene (HDPE). It typically appears white and is available in various particle sizes, making it versatile for different applications. LDPE exhibits excellent impact resistance, flexibility, and chemical resistance, making it suitable for various industries.
In terms of production, it is manufactured through processes like free radical polymerization, which helps achieve the unique molecular structure. The properties of LDPE powder, such as its ability to be molded and extruded, make it a common choice for producing robust and lightweight products, appealing to both manufacturers and consumers alike.
Historical Context
The journey of Low Density Polyethylene powder began in the early 20th century. The discovery of polyethylene itself dates back to 1933, when chemists at ICI marked the first synthesis of this plastic. Initially, LDPE was produced using high-pressure methods. Over the years, it gained traction as the demand for lighter, more flexible materials rose, particularly for packaging applications.
During World War II, LDPE found substantial use in military applications for insulation and protective coverings, showing that it could hold up under harsh conditions. Its evolution did not stop there; by the 1950s and 60s, advances in polymer technology allowed for a boom in consumer goods, thus bolstering LDPE's presence in households worldwide. Today, while it remains a powerful player in the plastics industry, discussions about LDPE also take into account environmental concerns regarding plastic waste and recycling challenges.
As such, its historical trajectory provides a backdrop necessary for understanding its current applications and prospective innovations, which we will discuss further in this article.
Chemical Composition and Properties
Understanding the chemical composition and properties of low density polyethylene powder is crucial in appreciating how this material behaves in various contexts. Its molecular structure, physical attributes, and thermal and mechanical properties are the keystones of its versatility and functionality. This section will dissect these aspects, revealing the hidden intricacies of a substance that permeates numerous industries.
Molecular Structure of Low Density Polyethylene
Low density polyethylene (LDPE) is characterized by its highly branched polymer structure, differentiating it from its more rigid counterparts. The apportionment and distribution of polymer chains give LDPE its distinctive properties. Polymer chains are arranged in a way that forms a flexible and elastic structure, which is less dense compared to other polyethylene types. Each molecule in LDPE is primarily composed of carbon and hydrogen atoms, indicating its origin from ethylene, a gaseous hydrocarbon.
- Significance of Branching: The branches in LDPE's molecular framework contribute to its lower density, which in turn affects its mechanical properties. This branching allows for loose packing of the polymer chains, making it softer and providing a greater degree of flexibility.
- Comparative Aspect: In contrast to high density polyethylene, which has a linear structure leading to crystalline regions, LDPE's structure results in an amorphous state. This amorphous nature leads to a lower melting point and higher resilience against cracking under stress.
Physical Properties
When it comes to physical properties, low density polyethylene powder is a true chameleon. Its unique characteristics make it suitable for various applications, from packaging to textiles.
- Density: Typically ranges from 0.910 to 0.925 g/cm³, this lower density enables its use in lightweight materials.
- Flexibility: LDPE exhibits remarkable flexibility, which is essential in its application to produce stretch film and plastic bags.
- Transparency: This material often appears somewhat translucent, which adds to its appeal in packaging applications where product visibility is key.
- Chemical Resistance: LDPE can withstand many chemical solvents, making it a superior choice for containers and piping systems that handle various substances.
The combination of these characteristics allows LDPE to triumph in environments that demand durability without compromising on performance.
Thermal and Mechanical Properties
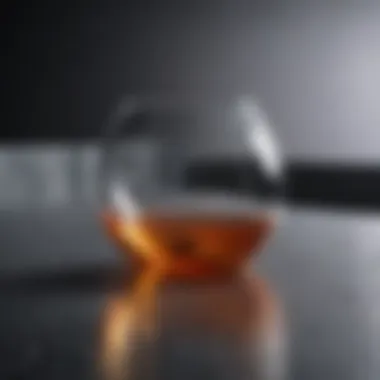

Thermal and mechanical properties reveal how LDPE functions when exposed to varying conditions. These properties are essential for engineers and designers when considering the suitability of materials for specific applications.
- Melting Point: With a melting point around 105 – 115 °C, LDPE can be formed and reformed without significant degradation, which is particularly advantageous during manufacturing processes such as extrusion and molding.
- Tensile Strength: While LDPE is not the strongest polyethylene variant, its elongation at break (often exceeding 600%) allows it to absorb impacts without fracturing.
- Thermal Conductivity: This material has low thermal conductivity, making it suitable for applications in insulation.
LDPE's low melting point and exceptional flexibility make it a material of choice in sectors that require safety and comfort, paving the way for innovative solutions across various industries.
In essence, understanding the molecular structure and properties of low density polyethylene powder provides vital insights into its wide-ranging applications. These characteristics not only inform its uses but also inspire ongoing innovations and enhancements in the fields that rely on this adaptable polymer.
Production Processes of Low Density Polyethylene Powder
The production processes of low density polyethylene (LDPE) powder hold paramount significance in this article. Understanding these processes not only provides insights into how LDPE is manufactured, but also underscores the material's versatility, affordability, and application scope. Different production methods contribute to the final properties of the polymer, influencing its mechanical behavior, clarity, and degree of crystallinity. A thorough grasp of these processes allows researchers and industry professionals to optimize product performance and align with market demands.
Polymerization Techniques
At the heart of LDPE manufacture are the polymerization techniques, which determine the molecular structure of the final product. Two primary methods are commonly used: free radical polymerization and high-pressure polymerization.
- Free Radical Polymerization: This technique involves subjecting ethylene gas to high temperatures and pressures in the presence of a catalyst. The reaction is initiated via free radicals. The outcome can vary; the structure tends to be less branched, leading to a more flexible and softer material.
- High-Pressure Polymerization: This method utilizes extreme pressure—often above 1000 atmospheres—to polymerize ethylene gas. The resulting LDPE exhibits a highly branched architecture, which contributes to its lower density. The branched chains create spaces between molecules, making it somewhat softer and more pliable compared to other polyethylene types.
These techniques not just influence the physical attributes of LDPE but also its end-use capabilities. For instance, LDPE made via high-pressure methods finds favor in packaging applications due to its superior flexibility and resilience. It's like that friend who is adaptable and fits into any situation—you see them thriving in diverse environments.
Processing Methods
The production methods extend beyond polymerization. After polymerization, the processing techniques play a critical role in shaping the LDPE powder into useful products. Various methods come into play here:
- Extrusion: This is a common method where crushed LDPE is melted and forced through a die to create continuous shapes. It’s widely used in the manufacture of films and sheets. The process allows for efficient mass production, making it suitable for packaging uses.
- Blow Molding: In this technique, LDPE powder is melted and inflated into a mold to form hollow parts. This is handy in producing items such as bottles and containers. The ability to create complex shapes is a strong advantage.
- Injection Molding: LDPE is injected into molds under pressure. This method is prevalent for creating precise, detailed components with good surface finish, often used in the automotive and household sectors.
- Thermoforming: Here, heated LDPE is formed against a mold or die. It's ideal for making packaging trays and containers. A quick and efficient way to create items that require moderate detail and strength.
Modern advancements in processing technology also involve using additives that enhance certain properties like UV resistance or flame retardance, allowing LDPE to suit even more applications.
In summary, the production processes of low density polyethylene powder encompass a blend of sophisticated polymerization and processing techniques. These methods not only dictate the characteristics and versatility of LDPE but also pave the way for innovative applications in myriad sectors. Understanding these processes equips stakeholders with the tools to develop LDPE products that meet evolving market needs while juggling the challenges of sustainability and environmental impact—a balance that has become increasingly essential in today’s manufacturing landscape.
Applications of Low Density Polyethylene Powder
Low Density Polyethylene (LDPE) powder is a versatile material with a wide range of applications that play a pivotal role in various industries. From packaging to medical supplies, its utility is vast and pivotal in today’s market. Understanding these applications is crucial as they not only showcase the inherent benefits of LDPE powder but also underline its impact on both industry practices and consumer products.
Packaging Materials
One of the most significant uses of LDPE powder is in the packaging sector. Its lightweight nature, combined with durability, makes it an ideal choice for manufacturing bags, films, and wrappers. Many grocery and retail stores rely heavily on LDPE for their plastic shopping bags. The flexibility of this material allows for the production of bags that can carry diverse items, reducing the risk of tearing or breaking.
Some key advantages include:
- Moisture Resistance: LDPE prevents water from damaging the contents, making it suitable for food packaging.
- Chemical Stability: This allows for the storage of various chemicals without a risk of degradation to the packaging material.
- Recyclability: Many LDPE products can be recycled, supporting sustainability efforts in reducing plastic waste.
"The reliable use of LDPE in everyday packaging underscores its importance in modern consumer behavior, where convenience meets safety".
Adhesives and Coatings
LDPE powder is also prominent in the production of adhesives and coatings. Its excellent adhesion properties enable it to bond well with surfaces, whether in construction or crafting. For example, it can be found in products utilizing hot-melt adhesives that are integral in laminating and binding applications. The characteristics enhance the strength and integrity of the final product, making it both resistant to weather effects and durable over time.
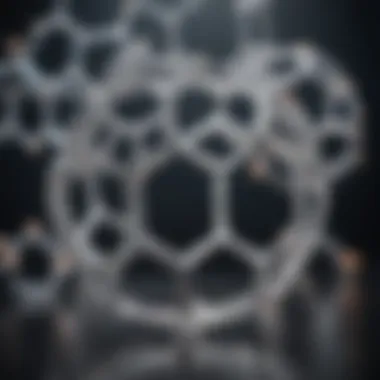

Another benefit is its ease of processing. LDPE coatings are often used in applications that demand a tough, protective surface, such as in the manufacturing of automotive parts or consumer goods.
Construction and Insulation Products
In construction, LDPE powder has carved out a niche for itself as a key component in insulation products. Its lightweight yet strong characteristics contribute to its effectiveness in thermal insulation applications. Builders often use it to create insulation panels that help in maintaining energy efficiency by limiting heat transfer.
- Common applications include vapor barriers, which prevent moisture ingress into buildings, thus improving overall structural integrity and safety.
- It also plays a crucial role in sound insulation, providing a quieter environment in urban settings.
Medical and Pharmaceutical Applications
LDPE powder shines in the medical and pharmaceutical fields as well. Its biocompatibility and non-toxic nature make it suitable for various applications in healthcare products. For instance, it is often used in packaging for medical devices and pharmaceuticals, ensuring that products remain sterile and safe for usage.
Some notable uses include:
- Syringes and containers: LDPE’s flexibility and formability make it ideal for creating components that require precision and reliability.
- Protective gear: Many components in personal protective equipment (PPE) utilize LDPE to provide both comfort and protection during medical procedures.
Thus, low density polyethylene powder is not just a manufacturing commodity; it is a strategic material that enhances operational efficiency, maintains safety standards, and meets the diverse needs of various sectors. As industries adapt to new demands, LDPE's relevance continues to grow, ensuring its position as a core player in the material landscape.
Advantages and Challenges of Low Density Polyethylene Powder
Understanding the advantages and challenges of low density polyethylene powder is essential for anyone engaging with this material. It serves as a bridge between its practical applications and the environmental considerations that come with its use.
Versatility and Ease of Processing
Low density polyethylene powder is renowned for its versatility across numerous industries. One of its standout attributes is the simplicity in processing. Thanks to its low melting point and excellent flow characteristics, it can be molded, extruded, or formed with relative ease. This makes it a popular choice in packaging materials, where rapid turnaround is crucial. The powder can be blended with additives to enhance its characteristics, such as increasing its toughness or reducing its flammability.
Moreover, it adapts well in applications ranging from films to complex molded products. Just consider the diverse applications across different sectors like food packaging, where the material encloses items without compromising on security, or in medical supplies, where cleanliness is paramount. Its adaptability is like having a Swiss Army knife; it comes in handy in various scenarios. Finally, this low density polyethylene powder boasts a good balance between rigidity and flexibility, which means it can be used effectively in applications requiring both, providing manufacturers with a viable option that meets their design needs without breaking the bank.
Environmental Impact Considerations
On the flip side, one must not ignore the environmental consequences associated with low density polyethylene powder. While it has many practical benefits, its production and disposal raise red flags. The conventional manufacturing processes often involve the use of fossil fuels, contributing to greenhouse gas emissions. Furthermore, once discarded, low density polyethylene can persist in the environment for years, leading to pollution in our oceans and landscapes.
There’s a pressing need to assess how this material can fit into a more sustainable future. Innovations in recycling technologies are an encouraging development. For instance, certain initiatives aim to convert used polyethylene into new products, thereby breaking the cycle of waste. Similarly, the exploration of biodegradable alternatives is gaining traction.
"Addressing the environmental concerns tied to low density polyethylene powder is crucial for a balanced understanding of its advantages and limitations, paving the way for more sustainable practices in the industry."
Market Trends and Economic Factors
Understanding the market trends and economic factors surrounding low density polyethylene powder is essential. It helps to gauge not only the current landscape but also future trajectories within various sectors. By analyzing elements such as global demand, supply chains, and production costs, stakeholders can make informed decisions regarding investments and innovations. Such an assessment is critical for researchers, educators, and industry professionals alike, enabling them to stay ahead of the curve in a rapidly evolving marketplace.
Global Demand and Supply Analysis
Low density polyethylene powder has gained traction across a multitude of industries, including packaging, construction, and healthcare. The demand for this material is on an upward trend. This can be attributed to several key factors:
- Increased Consumer Awareness: As people become more conscious about packaging sustainability, the need for versatile materials like low density polyethylene has surged.
- Growth of E-commerce: The rise of online shopping has bolstered the demand for packaging materials that provide durability while remaining lightweight.
- Application Expansion: Innovations in product formulations have fostered new applications in fields such as medical devices, which further propels demand.
However, this growing demand does not exist in a vacuum. Supply chain dynamics also play a significant role. The global market for low density polyethylene powder faces challenges such as:
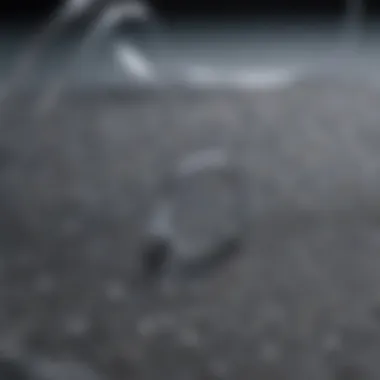

- Supply Chain Disruptions: Events like natural disasters or geopolitical tensions can hinder production.
- Raw Material Availability: The availability of essential feedstocks is crucial. Any fluctuations in petroleum prices can directly impact production costs and availability.
"Global demand for low density polyethylene powder has been positively influenced by a shift towards eco-friendliness and versatility in material selections across industries."
Cost Factors Influencing Production
The economics of producing low density polyethylene powder hinge on multiple cost factors that influence how and where production takes place:
- Feedstock Prices: The price of crude oil is a primary driver of production costs. As oil prices fluctuate, so do the expenses related to raw materials.
- Technology Investments: Companies need to invest in advanced processing technologies to enhance efficiency and quality. Higher initial costs can be offset by long-term savings through optimized production processes.
- Labor and Operational Costs: Depending on regional economic conditions, labor costs can significantly affect the overall production costs. Countries with a high labor cost may struggle to compete in the global market.
- Regulatory Compliance: Meeting environmental regulations may require additional investments. Companies are increasingly expected to adhere to stricter guidelines, impacting the production cost structure.
By closely monitoring these factors, businesses can work towards improving their supply chain strategies, making cost-effective choices while addressing market demand. Ultimately, the interplay of these elements shapes the economic landscape of low density polyethylene powder, impacting its viability and sustainability in the marketplace.
Innovations in Low Density Polyethylene Powder
In the ever-evolving world of materials science, innovation is the driving force behind the development of new applications and improvements in existing technologies. The field of low density polyethylene (LDPE) powder is no exception. This section explores some of the latest advancements in materials technology specific to LDPE powder, as well as sustainable alternatives being developed to meet the growing demand for environmentally friendly options.
Advanced Material Technologies
Advanced material technologies are shaping the landscape of how LDPE powder is produced, processed, and utilized. One notable advancement is the integration of nanotechnology. By incorporating nanoparticles into LDPE matrices, manufacturers can enhance the physical properties of the powder. For instance, these nanoparticles can improve mechanical strength, reduce friction, and even enhance thermal stability. This not only broadens the range of potential applications but also pushes the boundaries of performance beyond traditional LDPE capabilities.
Additionally, there have been significant improvements in polymer processing techniques. Take the example of supercritical fluid technology. This innovative approach allows for the use of supercritical carbon dioxide to process LDPE powder, creating a final product that exhibits superior characteristics such as lower density and enhanced dispersibility. Not only does this method potentially reduce energy consumption, but it also minimizes waste during production.
Moreover, smart additives that respond to environmental stimuli have started making their way into LDPE formulations. These materials can change their properties based on factors like temperature or pH, leading to applications in responsive packaging systems that extend shelf life and optimize food preservation. As manufacturers embrace these advanced technologies, they pave the way for a new generation of LDPE applications that can meet the demands of various industries, from packaging to automotive.
Sustainable Alternatives and Biodegradable Options
The increasing awareness of environmental issues has led to a surge in interest around sustainable alternatives and biodegradable options in the field of LDPE powder. Consumers and industries alike are searching for materials that not only perform well but also have minimal environmental footprints. One promising avenue is the exploration of biopolymers derived from natural sources, such as corn starch or sugarcane.
These biopolymers can be engineered to mimic the properties of LDPE, making them suitable substitutes in applications from packaging to industrial use. While they might not yet match LDPE's versatility in all respects, the potential for development is substantial. For instance, the introduction of polylactic acid (PLA) as a packaging material has shown that alternatives can be both functional and compostable, catering to the needs of a market increasingly focused on sustainability.
Furthermore, innovations in recycling technologies are changing how LDPE can be utilized post-consumer. Enhanced sorting methods and chemical recycling processes can reclaim LDPE from waste streams, breaking it down to its fundamental components. This recycling could pave the way to a circular economy for LDPE, where the material is continuously reused rather than discarded.
"As we innovate, we also have the responsibility to ensure these new materials are sustainable and can replace conventional plastics in a practical manner."
Overall, the innovations in low density polyethylene powder, both in terms of advanced materials and sustainable options, highlight an important shift in the industry. The quest for more functional, environmentally friendly materials not only drives technological advancements but also sets the stage for a future where materials science aligns better with ecological imperatives.
Future Prospects and End
The future of low density polyethylene powder stands at a crucial intersection where innovation meets environmental consciousness. With industries continually undergoing shifts, driven largely by technological advancements and consumer preferences, understanding the trajectory of this material becomes essential.
Predictions for Industry Growth
As the demand for low density polyethylene powder rises, several factors are anticipated to steer its growth. Experts suggest a compound annual growth rate (CAGR) bolstered by the escalating needs for sustainable packaging solutions and the gradual shift towards eco-friendly products. The expected expansions in sectors like construction and automotive, where this versatile material shows promising applications, contribute to these optimistic forecasts.
Additionally, the global preference for lightweight materials, pivotal in sectors including aerospace, aligns with what low density polyethylene offers. Just imagine packaging that not only protects the product but also offers flexibility in design, reducing waste in transit. Meanwhile, the influence of regulations around plastic use can't be dismissed. Stricter governance around environmental factors often drives industry innovation, compelling companies to invest in alternative materials or enhancing recycling methods to remain competitive.
The adaptability of low density polyethylene powder in various applications will likely play a major role in its future. Some foresight projects that usage will extend beyond traditional applications, entering realms like 3D printing, where it can be used to create intricate designs with less waste generated. If companies can harness these advantages effectively, they can ensure a robust market presence moving forward.
Final Thoughts on Low Density Polyethylene Powder
Reflecting on the information presented, it is evident that this material is not just a replacement but rather a partner in sustainable development. Direct engagement and collaboration between industries, manufacturers, and researchers will be fundamental in charting a path that favors both profitability and environmental stewardship.
"Innovation is the key to transcending current limitations and paving the way for new opportunities in low density polyethylene powder applications."
An emphasis on sustainable practices, coupled with a forward-thinking approach, will enable the materials industry to not only thrive but to do so in harmony with the environment. As we step into this new era, an open dialogue focused on future prospects may unlock greater potential in low density polyethylene powder, assuring its relevance in an ever-evolving marketplace.