Exploring NdFeB Magnet Manufacturing in India
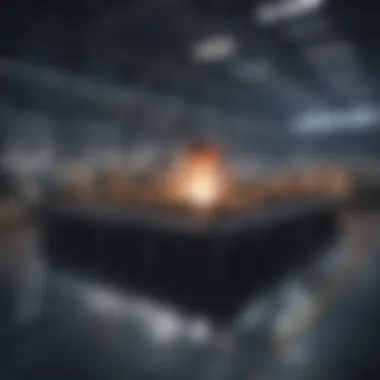
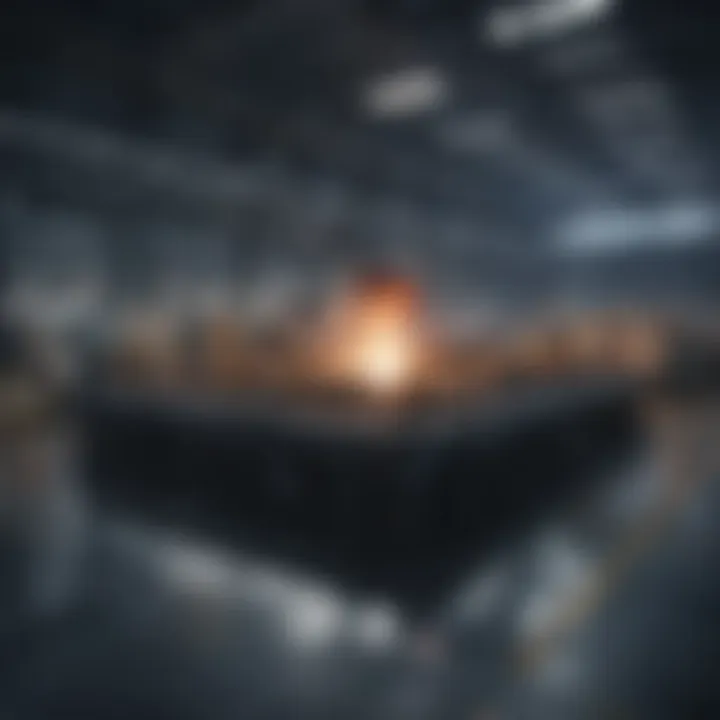
Intro
The manufacturing landscape of NdFeB magnets in India has witnessed significant growth in recent years. As one of the strongest permanent magnets available, Neodymium Iron Boron (NdFeB) magnets play a crucial role in various applications, from electric vehicles to renewable energy systems. This section will serve as a foundation, introducing core concepts and setting the stage for a deeper exploration of this intricate field.
Understanding the nuances of NdFeB magnet production and its implications involves appreciating both the technological advancements that have emerged and the underlying industrial context. With the manufacturing sector in India growing rapidly, it is vital to investigate what makes the country a fertile ground for NdFeB magnet production. Key challenges, opportunities, and innovations will form the backbone of the discussion, providing a 360-degree view of the trends shaping this industry.
From raw material sourcing to adherence to quality standards, each aspect of NdFeB magnet production interlinks with broader market dynamics. In this article, we will dissect these elements meticulously, bringing to light the relevant manufacturers, technologies, and applications. Furthermore, it is essential to grasp how government policies impact the industry and how global market demands influence local manufacturing strategies.
This groundwork establishes context for the subsequent sections, which will unpack specific methodologies used in research, the discussion of findings, and the implications for future advancements in the area of NdFeB magnets in India.
Research Methodology
Description of Research Design and Approach
This study underwent a systematic approach aimed at gathering comprehensive information about the NdFeB magnet manufacturing sector in India. The research design incorporated qualitative and quantitative data collection techniques to ensure a balanced perspective. The primary focus was on existing data from industry reports, interviews with experts, and market analysis.
Materials and Methods Used in the Study
The research involved analyzing various sources, including:
- Industry Reports: Input from established market research firms provided insights into market trends and forecasts.
- Expert Interviews: Discussions with industry professionals helped capture firsthand experiences and perspectives related to manufacturing processes.
- Surveys: Data gathered from manufacturers regarding production capacities, challenges faced, and technological advancements were instrumental in understanding the prevailing landscape.
Additionally, case studies of notable manufacturers offer concrete examples of operational strategies and competitive advantages. The combination of these methods ensures a well-rounded understanding of the NdFeB magnet manufacturing process in India.
Discussion and Interpretation
Interpretation of Results in the Context of Existing Literature
The results indicate that India is increasingly positioning itself as a critical player in the global NdFeB magnet market. Several manufacturers have established themselves, operating with state-of-the-art machinery and adhering to international quality standards. The growing demand for NdFeB magnets across various sectors, including automotive and electronics, underscores the relevance of this industry within the broader manufacturing ecosystem.
Implications for Future Research or Practical Applications
The findings raise several critical points for future exploration. Understanding the challenges in raw material sourcing can help manufacturers devise strategies to overcome supply issues. It is also important for researchers to examine how government policies can foster or hinder growth in this sector. Innovations in production processes could lead to increased efficiency and sustainability in magnet manufacturing.
"As the demand for NdFeB magnets continues to grow, India's role in the global market could become more influential, provided the industry adapts to changing dynamics."
Understanding these dynamics will not only allow us to appreciate current trends but also provide valuable insights into the strategic direction of NdFeB magnet manufacturing in India.
Intro to NdFeB Magnets
The significance of NdFeB magnets in today’s industrial landscape cannot be overstated. These magnets, also known as neodymium magnets, have revolutionized various applications due to their high magnetic strength and compact size. Understanding these magnets is crucial for grasping the role of India in the global magnet market. As this article unfolds, we will explore critical aspects, including definitions, historical developments, manufacturing processes, and current trends.
Definition and Composition
NdFeB magnets consist primarily of neodymium, iron, and boron, creating a powerful permanent magnet material. The typical formula for their composition can be represented as Nd2Fe14B. This combination of elements results in magnets that possess a much higher energy density than conventional magnet materials. This energy density has made NdFeB magnets essential in various fields such as electronics, automotive, and renewable energy sectors. They are often available in different grades, each defined by its unique magnetic properties, including coercivity and remanence, which affect performance in specific applications.
Historical Context
The journey of NdFeB magnets began in the 1980s, with the first production implemented in Japan. This marked a significant shift in magnetic technology. Before NdFeB, materials like ferrite and alnico dominated the market, but they could not provide the same level of performance. The development of NdFeB magnets was a response to the growing need for more powerful, compact solutions in technology and industry.
Over the years, production techniques have evolved. They initially involved costly methods, making NdFeB magnets expensive to produce. However, with advancements and scaling of production, costs have decreased. This change contributed to an increase in the adoption of NdFeB magnets across multiple industries.
"The introduction of NdFeB magnets represents a groundbreaking advancement in materials science, driving innovation in several sectors."
Despite their advantages, the environmental impact of raw material mining and concerns about supply chain vulnerability remain issues for manufacturers. Nevertheless, the fascinating history and ongoing innovation in the NdFeB magnet sector continue to shape the global market.
Overview of the Indian Market
The manufacturing of NdFeB magnets in India has become a critical segment of the broader magnet industry. This market is increasingly important due to the growing demand for NdFeB magnets in various applications, ranging from consumer electronics to industrial systems. Understanding the structure and dynamics of the Indian market offers insight into the trends influencing growth and investment opportunities as well as the challenges that the industry faces.
Market Size and Growth Rate
The Indian NdFeB magnet market has undergone significant growth in recent years. According to industry reports, it is projected to reach considerable valuation within the next few years, with a robust compound annual growth rate (CAGR).
Factors contributing to this growth include:
- The rising demand for smaller, lighter, and more efficient magnets in various sectors.
- Increased investment in renewable energy solutions requiring high-performance magnet materials.
- A shift towards electric vehicles, which rely on NdFeB magnets for motor and battery technologies.
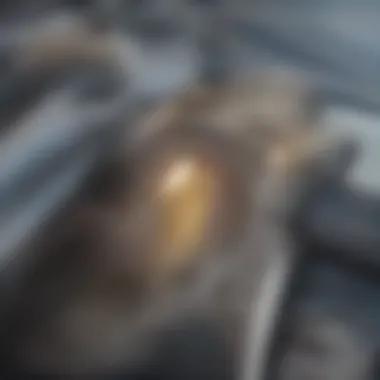
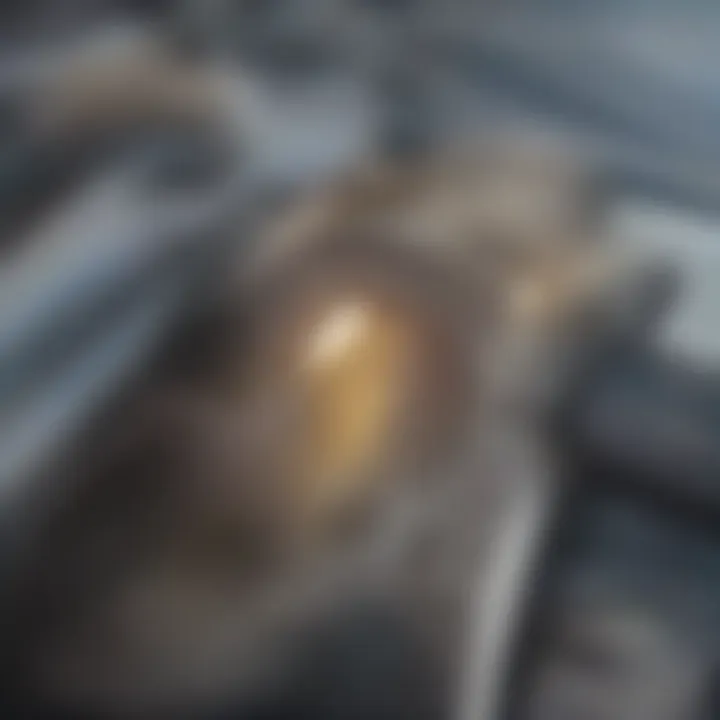
This expanding market presents manufacturers with opportunities to innovate and enhance production capacities.
Key Players in the Industry
The Indian NdFeB magnet landscape is shaped by several key players. Notable companies such as Bharat Electronics Limited and Magma Ceramics are prominent in this sector. These manufacturers are recognized for their commitment to quality and innovation.
Some of the leading attributes of these players include:
- Research and Development: Investments in R&D are vital in fostering innovation. Companies are consistently improving their products to meet global standards.
- Strategic Alliances: Collaboration with international firms enhances technology transfer and market reach.
- Sustainability Efforts: With increasing awareness about environmental issues, many manufacturers are adopting sustainable practices in their operations.
"The growth in the NdFeB magnet market reflects India’s strategic focus on emerging technologies and sustainable manufacturing practices."
Understanding the Indian market, including its size, growth rate, and key players, is crucial for stakeholders aiming to navigate this sector effectively. This analysis sets the foundation for exploring further components of NdFeB magnet production, including technological advancements and applications.
Manufacturing Processes
The manufacturing of NdFeB magnets is a complex yet crucial element in understanding the Indian market for these materials. Effective manufacturing processes not only influence the quality of the magnet produced but also impact the overall cost-effectiveness of production. As the demand for NdFeB magnets continues to rise in various applications, it becomes necessary to delve into the distinctive processes that manufacturers in India adopt. Through an analysis of raw material sourcing, production techniques, and quality control measures, one can appreciate the core aspects of magnet production and their implications for the industry.
Raw Material Sourcing
Raw material sourcing serves as the foundation of NdFeB magnet production. The primary components needed include neodymium, iron, and boron. Neodymium is a rare earth metal, while iron is more abundant, and boron is vital for producing a stable magnet.
India has access to a range of both domestically produced and imported raw materials. However, relying on international markets for rare earth elements poses risks. Fluctuations in global prices or supply chain disruptions can affect production capacity. Manufacturers must therefore establish strategic partnerships with suppliers, ensuring a consistent flow of quality materials. This dynamic requires careful negotiation and planning to maintain production efficiency.
Production Techniques
Production techniques encompass the methods employed to transform raw materials into finished NdFeB magnets. There are several prevalent techniques in use today, including the bonded magnet method and the sintering method.
- The sintering method involves compacting the raw material powders under high pressure before heating them to a temperature where they bond together. This technique often results in magnets with greater magnetic strength and density.
- The bonded magnet method involves mixing the powdered NdFeB with a polymer binding agent. This method allows for shaping into complex forms and is typically used in applications requiring less magnetic strength compared to sintered magnets.
Both techniques present unique advantages, and the choice often depends on the intended application of the final product. The sintering method generally leads to stronger magnets, while bonded processing allows for greater flexibility in form.
Quality Control Measures
Quality control measures are essential in ensuring that the manufactured NdFeB magnets meet specific performance standards. Given the advanced materials involved, manufacturers typically adhere to both domestic and international quality standards.
The quality control process often includes several checkpoints:
- Raw Material Inspection: Quality checks on raw materials upon arrival.
- In-Process Tests: Monitoring quality during the manufacturing phases to catch defects early.
- Final Product Testing: Extensive tests to measure the magnetic properties and overall durability before delivery.
It is essential for manufacturers to employ rigorous quality control systems. Doing so not only ensures product reliability but also strengthens customer trust and satisfaction.
"Quality is not an act; it is a habit."
In summary, the manufacturing processes of NdFeB magnets in India are complex and involve careful consideration rather than simple procedures. From sourcing raw materials to employing suitable production techniques and establishing robust quality control measures, each step plays a significant role in shaping the success of manufacturers in this competitive market.
Technological Advancements
Technological advancements in the NdFeB magnet manufacturing sector are crucial for sustaining competitive advantage and meeting the demands of various industries. These advancements not only improve production efficiency but also enhance the performance and quality of the magnets. In recent years, innovative manufacturing technologies have emerged, enabling companies to produce NdFeB magnets with better magnetic properties and lower production costs.
Innovation in Manufacturing
The innovation landscape within NdFeB magnet manufacturing has seen a variety of technologies being adopted. For instance, the implementation of automated processes and advanced robotics has streamlined production. This increases output while minimizing human error. Furthermore, techniques such as rapid prototyping allow manufacturers to quickly bring new designs to market. New materials are also being explored to replace or enhance existing raw materials, aiming to improve magnet performance or reduce costs.
Some of the notable innovations include:
- High-throughput manufacturing techniques that significantly reduce the time taken to produce magnets.
- Sintering technologies that promote better magnetic alignment during manufacturing.
- The development of recycling methods for NdFeB magnets, which helps in sustainability and reduces dependence on raw materials.
These innovations are essential for manufacturers to respond to the changing needs of various sectors, particularly in a world that increasingly values efficiency and sustainability.
Research and Development Initiatives
Research and Development (R&D) plays a critical role in advancing the NdFeB magnet industry in India. Many manufacturers are investing significantly in R&D to explore new applications and improve existing technologies. This effort not only fosters innovation but also positions Indian manufacturers favorably in the global market.
A strong R&D focus can lead to:
- Enhanced magnetic performance, which is vital for applications in electric vehicles, renewable energy technologies, and electronics.
- Cost-effective production methods, which can lower the overall manufacturing expenditure and ultimately benefit consumers.
- New applications for NdFeB magnets in fields such as medical technology, where strong, compact magnets can improve device efficiency.
Collaborations between academic institutions and industry leaders also fuel these R&D initiatives. Such partnerships lead to significant advancements, driven by research-focused approaches that benefit both sectors. By continuing to invest in R&D, manufacturers can stay at the forefront of technology, adapting to both the challenges of today and opportunities of tomorrow.
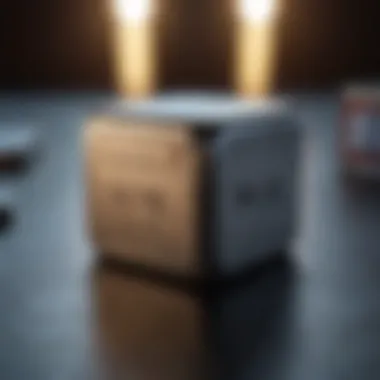
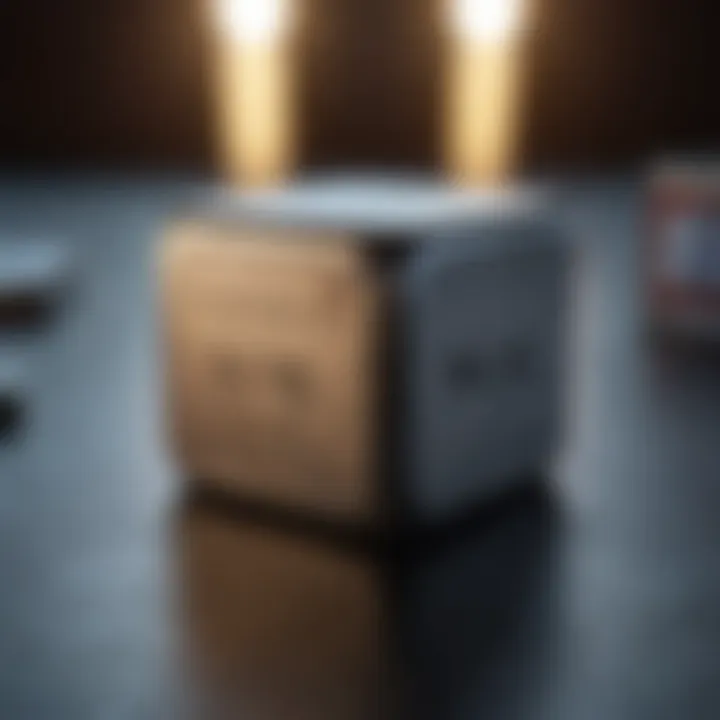
"The future of NdFeB magnets lies in the continuous advancement of technology, research, and innovation to meet diverse industrial needs."
Applications of NdFeB Magnets
The versatility of NdFeB magnets makes them essential across various industries. Their applications go beyond simple magnetic tasks, showcasing innovative uses that drive many technological advancements. Understanding these applications provides insights into their market importance and how manufacturers can cater to specific customer needs.
Industrial Applications
NdFeB magnets are widely utilized in industrial settings. Their strength allows for compact designs that save space and reduce weight. Some key sectors include:
- Automation and Robotics: In manufacturing, these magnets enable precise movement in robotics, improving production efficiency.
- Electric Motors: They enhance the performance of motors used in pumps, fans, and other machinery, leading to energy efficiency.
- Generators: The renewable energy sector relies on NdFeB magnets for wind turbine generators, contributing to sustainable energy solutions.
Due to their cost-effectiveness and high magnetic field strength, industries often prefer NdFeB magnets over other types, making them a cornerstone in modern manufacturing.
Consumer Electronics
In consumer electronics, NdFeB magnets find applications that improve everyday devices. Their small size and high magnetic strength are crucial for:
- Smartphones: NdFeB magnets are integral in speakers and vibration functions, contributing to sound quality and user experience.
- Headphones: The magnets used in headphones allow for high fidelity audio processing, essential for music lovers.
- Hard Drives: These magnets are employed in hard disk drives, enhancing data storage technology.
The growing demand for sleek and efficient electronic devices drives the need for stronger magnets in this sector, making NdFeB magnets increasingly relevant.
Medical Technologies
In the field of medical technology, NdFeB magnets offer unique benefits due to their strong magnetic properties. Key applications include:
- MRI Machines: Their ability to create powerful magnetic fields makes them essential in magnetic resonance imaging, allowing doctors to conduct detailed scans.
- Magnetic Therapy Devices: These magnets are often used in therapeutic devices, claiming to relieve pain and promote healing.
- Robotic Surgery Instruments: In advanced surgical procedures, NdFeB magnets are used to improve the precision and control of robotic instruments.
As the healthcare industry continues to evolve, the significance of NdFeB magnets in medical devices is likely to increase.
"NdFeB magnets are changing the landscape of multiple industries through their remarkable performance and adaptability."
In summary, the applications of NdFeB magnets span diverse sectors. Their efficiency and compactness make them a preferred choice, establishing their presence as a vital component in industrial, consumer, and medical applications.
Export Potential
The export potential of NdFeB magnets represents a significant aspect of India's position in the global manufacturing landscape. Understanding this potential is crucial for manufacturers, investors, and policymakers. NdFeB magnets are known for their high magnetic strength and efficiency, which makes them indispensable in various applications, from automotive to electronics. With the global demand for these magnets increasing, the Indian manufacturers stand to gain considerably by tapping into international markets.
Global Demand for NdFeB Magnets
As industries worldwide seek efficient and powerful magnetic solutions, the demand for NdFeB magnets has surged. Factors driving this demand include:
- Growth of electric vehicles (EVs): The transition to cleaner energy sources has prompted a rise in the manufacture of electric vehicles, which heavily rely on high-performance magnets for electric motors.
- Advancements in renewable energy technologies: Wind turbines and solar panel systems utilize NdFeB magnets, further elevating the need for these products.
- Increasing consumer electronics market: Devices such as smartphones, laptops, and smart appliances incorporate NdFeB magnets, leading to consistent demand growth.
This global demand can be seen influencing the Indian market, where manufacturers are increasingly focusing on capacity expansion and upgrading production techniques to maintain competitiveness.
Trade Relationships
The export opportunities are closely linked to trade relationships established between India and various countries. Key factors influencing these relationships include:
- Bilateral trade agreements: Agreements between India and nations looking to import NdFeB magnets can facilitate smoother transactions and reduce tariffs.
- Networking with international organizations: Participation in global trade fairs and forums can help Indian manufacturers gain visibility and forge crucial partnerships.
- Quality standards compliance: Adherence to international standards is vital for gaining and maintaining trust in overseas markets.
Regulatory Environment
The regulatory environment surrounding NdFeB magnet manufacturing in India plays a crucial role in shaping the industry. This sector is influenced by various government policies, compliance standards, and international regulations. Understanding regulatory frameworks ensures that manufacturers not only achieve efficiency in production but also align with global expectations.
These frameworks encourage practices that protect the environment and ensure the safety of workers. In addition, they create a conducive environment for innovation, attracting investments into the sector. Thus, it's essential for stakeholders to stay informed about the evolving regulations that could impact their operations.
Government Policies and Initiatives
Government policies significantly impact the NdFeB magnet industry. The Indian government has launched several initiatives, such as the Make in India campaign, which aims to boost local production, enhance export capability, and reduce reliance on imports. Among the initiatives, the National Mineral Policy promotes sustainable mining practices for raw material sourcing, essential for magnet production.
Some key policies include:
- Promotion of indigenous manufacturing: This encourages local manufacturers to enhance production capacities.
- Incentives for research and development: The government allocates funds to support innovative projects in the magnet sector.
- Tax benefits and subsidies: These financial advantages help lower manufacturing costs.
By aligning with these initiatives, manufacturers can position themselves for growth.
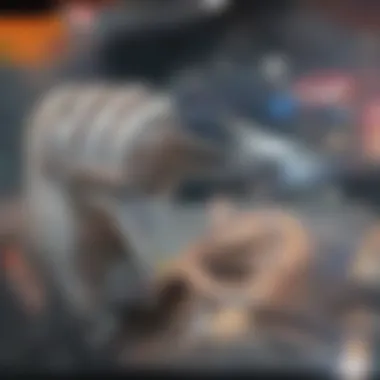
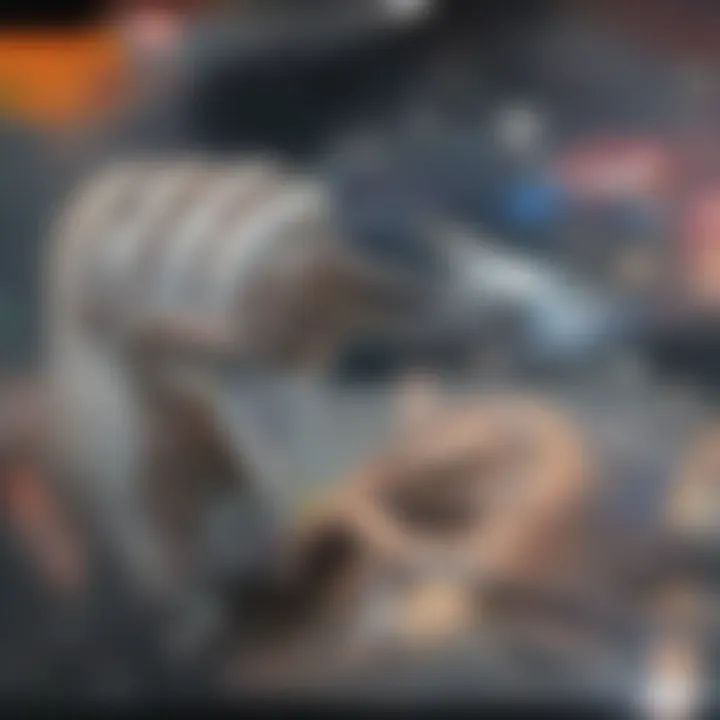
Compliance with International Standards
Compliance with international standards is not merely a regulatory requirement; it serves as a competitive advantage in the global market. Standards set by organizations such as the International Organization for Standardization (ISO) provide benchmarks for quality, safety, and environmental management. Adherence to these standards facilitates easier access to international markets and enhances the reputation of Indian manufacturers.
Manufacturers must focus on:
- Quality management systems: Implementing ISO 9001 ensures consistent quality in production.
- Environmental management systems: ISO 14001 compliance enhances sustainable practices in manufacturing processes.
- Worker safety regulations: Compliance with OSHA standards can mitigate workplace hazards.
"Achieving compliance with international standards can greatly enhance marketability and consumer trust, essential for long-term success."
Challenges Faced by Manufacturers
Manufacturers of NdFeB magnets in India face a range of challenges that can impact production efficiency and overall market performance. These obstacles must be navigated carefully to maintain a competitive edge in the industry. Understanding these challenges is crucial for stakeholders involved in the NdFeB production spectrum, including suppliers, manufacturers, and end-users. This segment addresses the key hurdles related to supply chain disruptions, cost constraints, and technological barriers.
Supply Chain Disruptions
Supply chain disruptions pose a significant risk to NdFeB magnet manufacturers. These interruptions can stem from various factors including geopolitical tensions, natural disasters, or the ongoing aftermath of the COVID-19 pandemic. When raw materials are delayed or unavailable, it hinders production schedules and leads to missed deadlines for clients.
Furthermore, many NdFeB magnets require rare earth elements, which are primarily sourced from specific regions. For example, China holds a monopoly over these materials. This reliance on limited suppliers complicates the supply chain, increasing vulnerability to fluctuations in pricing and availability.
Mitigation strategies are essential to combat these problems. Building diversified supplier relationships and investing in local sourcing can improve resilience against supply chain shocks. By adopting these strategies, companies can secure a more stable flow of materials.
Cost Constraints
Cost constraints significantly impact the manufacturing landscape for NdFeB magnets. The manufacturing process requires expensive raw materials as well as advanced machinery and technology. Fluctuations in the prices of rare earth metals can drastically raise production costs, affecting profit margins.
Additionally, the Indian manufacturing sector often struggles with high operational costs due to labor, utilities, and compliance with regulatory standards. These expenses challenge manufacturers to maintain competitive pricing in a global market often dominated by lower-cost competitors.
To address cost constraints, companies may seek to optimize their manufacturing processes through automation or lean manufacturing techniques. Cost analysis and efficiency improvements can help manage expenses, ultimately alleviating some financial pressure.
Technological Barriers
Technological barriers also represent a significant obstacle for NdFeB magnet manufacturers. The production of high-quality magnets requires state-of-the-art technology and skilled labor to operate complex manufacturing equipment. Many Indian manufacturers may not have access to the latest advancements, limiting their ability to produce magnets that meet international quality standards.
Moreover, as the industry evolves, there is a continual need for research and development to drive innovations in magnet applications and efficiency. Companies that fail to keep pace with technology risks being outperformed. Investing in R&D can foster new product innovations and improve manufacturing processes.
"Investing in technology is not just an option but a necessity for staying relevant in the competitiveness of the NdFeB magnet market."
Future Prospects
The future prospects for NdFeB magnet manufacturers in India can be characterized by both exciting opportunities and significant challenges. As industries increasingly lean on NdFeB magnets for more efficient operation and advanced technology, understanding these prospects becomes crucial. By evaluating emerging trends in manufacturing and anticipating market growth, stakeholders can prepare strategically and capitalize on future developments.
Emerging Trends in Manufacturing
The manufacturing landscape for NdFeB magnets is evolving rapidly. Several trends are shaping the future.
- Automation and Efficiency: Manufacturers are integrating automation in production processes to enhance efficiency. Robotics and AI technology are being employed to optimize assembly lines and maintain quality standards. This minimizes human error and lowers production costs, which is critical for maintaining competitiveness.
- Sustainability Initiatives: As the global conversation shifts towards sustainability, Indian manufacturers are also prioritizing eco-friendly practices. This includes adopting green technologies in the production process and ensuring responsible sourcing of raw materials. Manufacturers are focusing on developing recycling methods for NdFeB magnets to reduce waste and environmental impact.
- Advanced Manufacturing Techniques: Techniques such as additive manufacturing are being explored. This allows for more complex geometrical designs and reduced materials wastage. These techniques not only improve product performance but also cater to specialized applications in high-tech industries.
Forecast for Market Growth
Looking ahead, the NdFeB magnet market in India is set to experience substantial growth. Current market indicators suggest a robust increase in demand driven by several sectors:
- Electronics Sector: The booming consumer electronics market is a significant driver. With devices requiring smaller yet more powerful magnets, NdFeB's unique properties make it ideal for smartphones, laptops, and other electronic devices.
- Electric Vehicles: The rising trend of electric vehicles is projected to push demand for NdFeB magnets. They are crucial components in electric motors, which are essential for EV performance.
- Renewable Energy: The push towards renewable energy sources also presents growth opportunities. Wind turbines and other energy technologies that use NdFeB magnets for generators are witnessing increased investment.
In summary, the future for NdFeB magnet manufacturing in India presents a landscape filled with potential. The combination of emerging manufacturing trends and a positive growth forecast positions Indian manufacturers to become vital players in the global market.
End
The conclusion of this article on NdFeB magnet manufacturing in India brings clarity and significance to the discussion. As the demand for NdFeB magnets continues to rise, understanding the trends, challenges, and dynamics within this market becomes crucial. This section synthesizes the key insights and reflects on the implications for various stakeholders.
Summary of Key Points
The article has explored numerous facets of the NdFeB magnet sector. Important takeaways include:
- Growth Potential: The Indian market for NdFeB magnets is expanding, driven by various industries such as automotive, electronics, and renewable energy.
- Technological Advancements: Innovations in manufacturing processes have increased efficiency and quality, making Indian manufacturers more competitive.
- Sourcing Raw Materials: Reliable and sustainable sourcing of raw materials is essential for maintaining production levels and quality standards.
- Regulatory Impact: Government initiatives and policies shape the operational landscape, aiming to boost domestic manufacturing and reduce dependency on imports.
These points emphasize the multifaceted nature of the industry and highlight the different elements that contribute to its success.
Implications for the Industry
The implications for the NdFeB magnet industry are profound. Understanding these factors can assist manufacturers, policymakers, and investors in making informed decisions. Some critical implications include:
- Investment Opportunities: With the market's growth, there are ample opportunities for investment in technology and innovation.
- Strategic Partnerships: Collaborations between domestic and international players can enhance competitive advantages and market reach.
- Focus on Sustainability: The emphasis on environmentally friendly practices and sourcing is likely to become a central theme in the industry.
- Regulatory Compliance: Adapting to changing regulations will be crucial for maintaining competitiveness and ensuring quality standards.
Overall, the future of NdFeB magnet manufacturing in India is bright, but it demands attention to evolving global dynamics and the ability to adapt strategically.