Understanding Non-Contact Flow Switch Technology
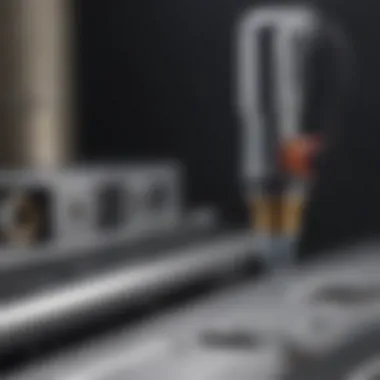
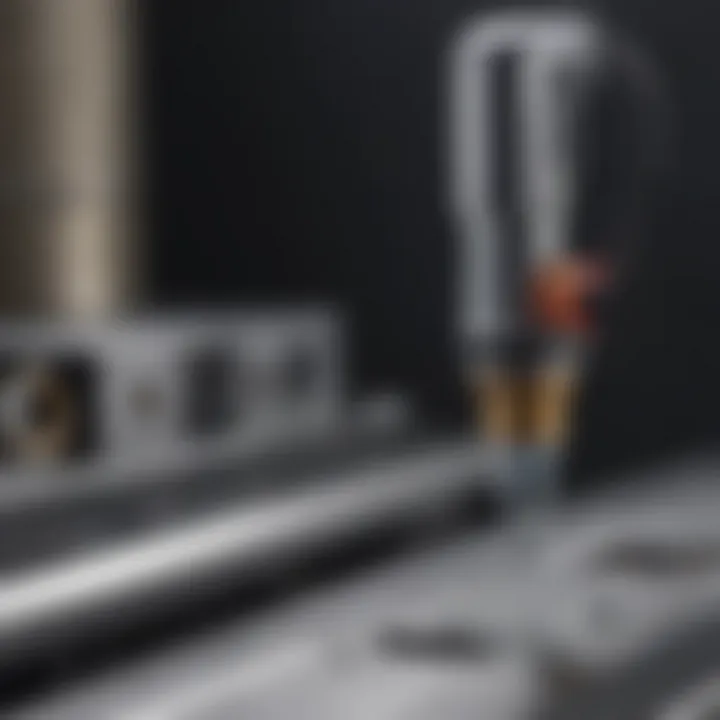
Intro
In an era where precision and efficiency in industrial processes matter more than ever, understanding how technology evolves to meet these demands is crucial. Among the innovations in flow measurement, non-contact flow switch technology stands out as a game changer. Unlike traditional devices that rely on physical contact with the fluid, these non-invasive switches monitor flow without interrupting the flow path, which minimizes the risk of wear and contamination. This article will guide you through the intricacies of this technology, unraveling its operational principles, applications, and the advantages it offers over its more conventional counterparts.
By the end, you'll gain a comprehensive grasp of the various types of non-contact flow switches, key selection criteria, and the hurdles that might come up when implementing them in real-world settings. Let’s embark on this exploration of what makes non-contact flow switches such a significant feature in today's technological landscape.
Research Methodology
Description of research design and approach
The examination of non-contact flow switch technology incorporates a mixed-methods approach. This combination allows for a robust understanding of both theoretical and empirical perspectives. The theoretical framework focuses on established fluid dynamics principles while also integrating case studies that illustrate practical applications across various sectors.
Materials and methods used in the study
A comprehensive review of existing literature serves as the foundation for understanding the principles and mechanisms underlying non-contact flow switches. Key materials include:
- Academic journals detailing advancements in fluid dynamics
- White papers from leading manufacturers of flow switch technology
- Case studies from industries employing these devices, like HVAC, food processing, and chemical manufacturing
The analysis of these materials provides insights into how non-contact flow switches operate and the benefits they provide in enhancing process efficiency and safety. Interviews with industry experts further enrich the research, offering firsthand accounts of the operational challenges and successes encountered in implementing this technology.
"Non-contact flow switches are not just equipment; they are pivotal in driving efficiency while reducing maintenance costs in many industrial applications."
Discussion and Interpretation
In reviewing the various resources, several common themes emerge. One predominant finding is that non-contact flow switches, often utilizing ultrasonic or electromagnetic principles, significantly reduce the risk of damage or contamination typically found in traditional flow measurement systems. This characteristic proves especially advantageous in industries where hygiene standards are paramount, such as in food processing and pharmaceuticals.
Furthermore, the implications of these findings for future research are substantial. As industrial applications continue to evolve, there remains a need for more nuanced studies that explore real-time data analytics paired with non-contact flow measurement. This integration could lead to even greater process improvement and safety outcomes.
Foreword to Flow Sensing Technologies
Flow sensing plays a pivotal role in various industries, acting as the backbone for processes ranging from manufacturing to environmental management. In a world where efficiency and precision are paramount, understanding flow measurement technologies appears essential. This part of the article explores not only the different methods of flow measurement but also underlines the advantages of employing modern sensing technologies, such as non-contact flow switches.
Overview of Flow Measurement
Flow measurement represents the quantification of movement of liquids, gases, and even slurries through defined systems. This process can take several forms, with each technology boasting distinct methodologies tailored to the specific characteristics of the fluid being measured.
When we consider traditional flow meters, they often involve some sort of direct contact with the flowing medium. These models can include devices like positive displacement meters, turbine meters, or even mechanical rotameters. However, they can face hurdles, such as wear and tear, maintenance issues, and contamination risks, especially in sensitive applications.
Non-contact flow measurement, on the other hand, emerges as a revolutionary wave, particularly in situations involving hazardous materials or critical health requirements. By using different physical principles such as ultrasonic, electromagnetic, or optical detection, non-contact systems can provide accurate readings without compromising the integrity of the flow medium.
Importance of Accurate Flow Measurement
Accurate flow measurement is not just about numbers—it's fundamentally tied to safety, cost efficiency, and environmental consciousness. Precision in flow detection ensures:
- Operational Efficiency: With accurate flow rates, industries can minimize waste and optimize processes, reducing unnecessary expenditures. Misinformation in flow metrics can lead to significant operational bottlenecks.
- Safety Compliance: In environments where safety is non-negotiable, such as chemical processing or petroleum. Incorrect flow readings can potentially result in catastrophic events, making accurate measurement a legal and ethical necessity.
- Environmental Stewardship: Effective flow measurement can lead to better resource management, allowing companies to track water usage or emissions that could harm the environment.
Accurate flow measurement isn't just a technical necessity — it's a commitment to operational integrity and environmental responsibility.
Capturing and interpreting fluid dynamics accurately is not just an academic pursuit but an imperative for thriving industries. As we navigate through this article, the advancements in flow sensing technologies will illuminate how non-contact flow measuring devices stand to reshape industry standards, enhancing both safety and performance.
Flow sensing thus stands as not only a tool for measurement but as a crucial parameter that molds the very landscape of modern industry. The coming sections will outline specific technologies and their associated benefits, providing a detailed look at what the future of flow measurement may hold.
Understanding Non-Contact Flow Switches
Understanding non-contact flow switches is pivotal in unraveling the advances in flow measurement technologies. In an era where accuracy and safety are paramount, these switches take center stage, providing a means to measure flow without physical interference. This offers significant advantages, ensuring that processes run efficiently, while also minimizing the risk of contamination, which can compromise both product quality and operational safety.
Definition and Functionality
A non-contact flow switch operates without the need for direct contact with the fluid being measured. Unlike traditional flow meters that rely on mechanical components or physical barriers, non-contact models utilize various technologies, such as ultrasonic, electromagnetic, or optical sensors.
For instance, ultrasonic flow switches send sound waves through the fluid. If you picture throwing a rock into a pond and measuring the ripples caused, you can visualize how these sound waves behave. As they hit particles in the flow, they reflect back, allowing for precise calculation of flow rates based on the time it takes the sound to bounce back. This simple yet effective method helps in gauging flow rates, all without the parts ever touching the fluid.
Functions of non-contact flow switches can vary but broadly include:
- Flow detection: Identifying whether there is flow or not, which is critical in many industrial processes.
- Flow rate measurement: More advanced models can provide continuous data on the speed or volume of the flow.
- Safety alerts: Many models are designed to trigger alarms if flow values exceed or drop below predefined thresholds, which is essential for preventing system failures.
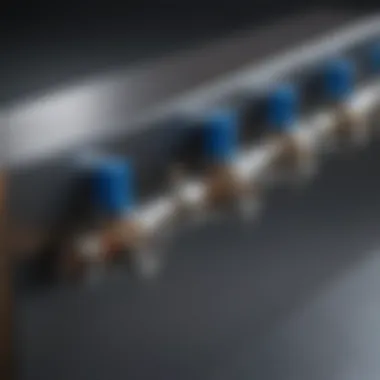
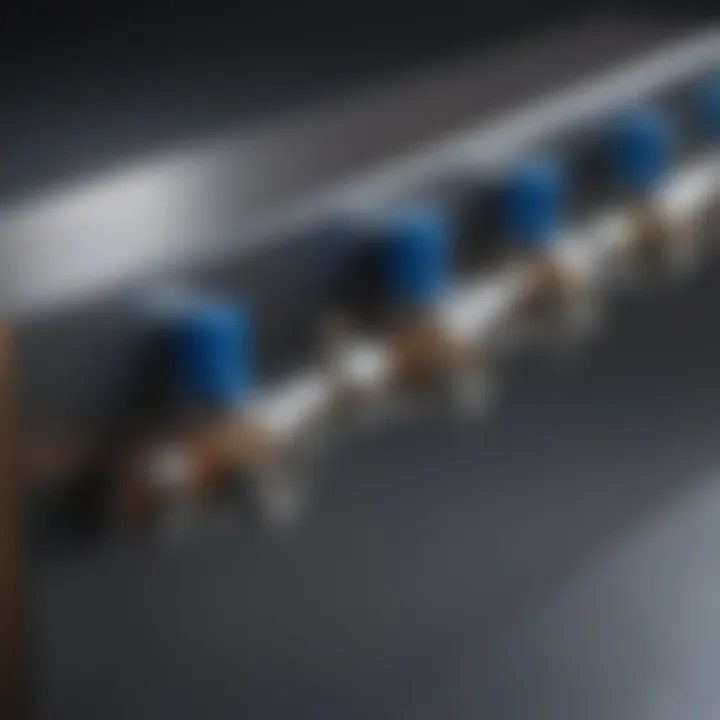
Differences Between Contact and Non-Contact Models
When drawing a line between contact and non-contact flow measurement, several distinctions become evident. While both types aim to provide accurate flow data, their methodologies differ significantly.
- Physical Interaction: Contact flow switches, like those using mechanical paddles, require physical immersion into the fluid. This leads to wear and tear, potentially compromising accuracy over time. In contrast, non-contact models function entirely outside the fluid, thereby greatly reducing maintenance needs and extending the operational lifespan of the devices.
- Scalability and Versatility: Non-contact switches often adapt more easily to various applications, from high-viscosity liquids to hazardous fluids. For example, filling systems in the food and beverage industry benefit from non-contact models due to their ability to handle sensitive ingredients without contamination fears.
- Accuracy and Response Time: Non-contact models generally demonstrate superior accuracy because they are unaffected by factors such as turbulence or sediment that can interfere with contact-based methods. Furthermore, they can provide near-instantaneous readings, crucial in fast-paced industrial environments.
"Non-contact flow switches not only streamline workflows but also contribute to maintaining product integrity by minimizing physical interactions."
Clearly, each model carries its own set of pros and cons, yet non-contact technologies are becoming increasingly popular where sanitation and accuracy are non-negotiable. Understanding these technologies is a vital step for anyone who wishes to keep pace within the evolving landscape of flow measurement and automation.
Mechanics of Non-Contact Flow Switches
When it comes to non-contact flow switches, understanding the mechanics behind these devices is crucial. The underlying principles of their operation not only dictate their efficiency but also their suitability for specific environments and applications. In this section, we’ll examine how these switches operate, what makes them unique, and the components that form the backbone of their functionality.
Operating Principles
At their core, non-contact flow switches operate using various strategies that do not require physical contact with the fluid being monitored. Unlike traditional flow sensors that may wear down or become contaminated, these advanced mechanisms ensure heightened reliability.
- Ultrasonic waves are one of the more common methods. These switches emit sound waves that bounce back after hitting a fluid's surface. By measuring the time it takes for the sound to return, the device can determine the flow rate.
- Electromagnetic systems utilize Faraday’s law of electromagnetic induction. When fluid moves through a magnetic field, it generates a voltage proportional to the flow rate. Thus, even with a barrier between the fluid and the device, accurate readings are achievable.
- Optical sensors provide another perspective. They scrutinize changes in light refraction as fluid flows through a specific area. These sensors detect variations that signal flow changes, often employed in clearer liquids where visibility of light is paramount.
The beauty of these operating principles lies in their ability to function in harsh conditions. They mitigate risks commonly associated with contact methods, such as fouling and wear. Because the sensors do not come into direct contact with the fluid, maintenance costs and replacement cycles decrease, which is a win-win for industries aiming to optimize their operations.
Key Components
Dissecting the functionality of non-contact flow switches unveils several key components that are essential for their operation.
- Sensor Head: The face of the device that interacts with the flow medium. The design can vary depending on whether it's ultrasonic, electromagnetic, or optical. This component’s material and adaptation are pivotal in ensuring durability and efficiency.
- Signal Processor: This part takes the raw data received from the sensor head and interprets it into meaningful metrics. Depending on the complexity, it may perform real-time calculations and adjustments, which help in monitoring performance.
- Power Supply: Non-contact flow switches typically require a reliable power source to ensure continual operation. Some systems may even incorporate energy harvesting mechanisms to enhance sustainability.
- Output Interface: The pathway for relaying information to other systems, this could be a digital or analog signal. Integration capability with existing infrastructure is vital for seamless operation, especially in automated environments.
In summary, dissecting the mechanics of non-contact flow switches reveals a combination of innovative operating principles and robust components. Each element works harmoniously to provide accurate, reliable, and maintenance-friendly solutions across various industries. Understanding these mechanics is not just academic; it's a necessary step in selecting the right flow switch for specific applications.
Types of Non-Contact Flow Switches
Understanding the types of non-contact flow switches is crucial for professionals and researchers engaging with advanced flow measurement techniques. These devices, while subtly distinct in their operational methodologies, serve a common goal: efficient and reliable flow measurement without interference in the fluid dynamics. Each type comes with its own set of advantages and potential application constraints that can significantly influence the performance and reliability of fluid systems across industries.
Ultrasonic Flow Switches
Ultrasonic flow switches operate on a principle that many might find quite fascinating. They rely on the time it takes for ultrasonic waves to travel through the fluid. When the fluid flows, the time for these waves to bounce back changes, allowing for an assessment of the flow rate. They work exceptionally well in applications where cleanliness and hygiene are essential.
Utilizing ultrasonic technology means that these switches do not physically come in contact with the fluid, thereby minimizing contamination risks. Their robustness in harsh environments also makes them versatile, particularly in water treatment facilities or chemical industries.
- Key Benefits:
- Non-invasive, reducing contamination risks
- Accuracy across a wide range of flow rates
- Adaptability to various fluid compositions
However, it's important to consider their limitations as well. Ultrasonic switches may struggle with fluids containing bubbles or particulates, as these can interfere with the acoustic signals.
Electromagnetic Flow Switches
Electromagnetic flow switches, on the other hand, utilize the principle of electromagnetic induction. When a conductive fluid flows through a magnetic field, it induces a voltage that can be measured to determine the flow rate. This technology is quite prevalent in industries dealing with liquids, particularly water and chemical processing, where the fluid's conductivity can be utilized effectively.
Advantages of electromagnetic flow switches include:
- No moving parts, which leads to enhanced durability
- Immunity to changes in fluid density, viscosity, or temperature
- Accurate readings even in fluctuating conditions
Yet, there are downsides as well. These switches require a certain level of conductivity in the fluid—non-conductive fluids will not work with this type. They are also typically limited to certain pipe sizes and configurations, which can complicate integration into existing systems.
Optical Flow Switches
Finally, we have optical flow switches, which employ light to monitor flow. They function by using a beam of light that is interrupted when fluid passes through a designated area. This method is particularly suitable for smaller pipes and systems where precision is paramount.
One might appreciate the precision optical flow switches offer; they can detect even minor changes in flow, making them ideal for sensitive environments like laboratories or critical manufacturing processes. Here are some key points about optical switches:
- High sensitivity allows for detailed flow monitoring
- Can be used for both clear and colored fluids
Yet again, a challenge crops up. They may struggle with turbid fluids that scatter light excessively or environments where dust and debris could interrupt the light beam.
"Choosing the right non-contact flow switch is not just about picking a device; it’s about understanding the fluid dynamics and specific application requirements.”
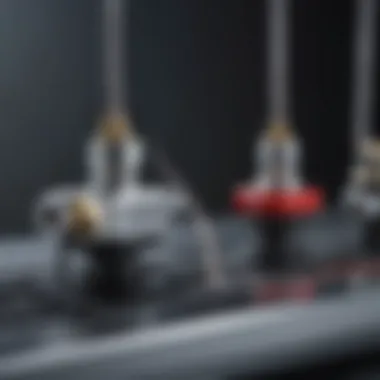
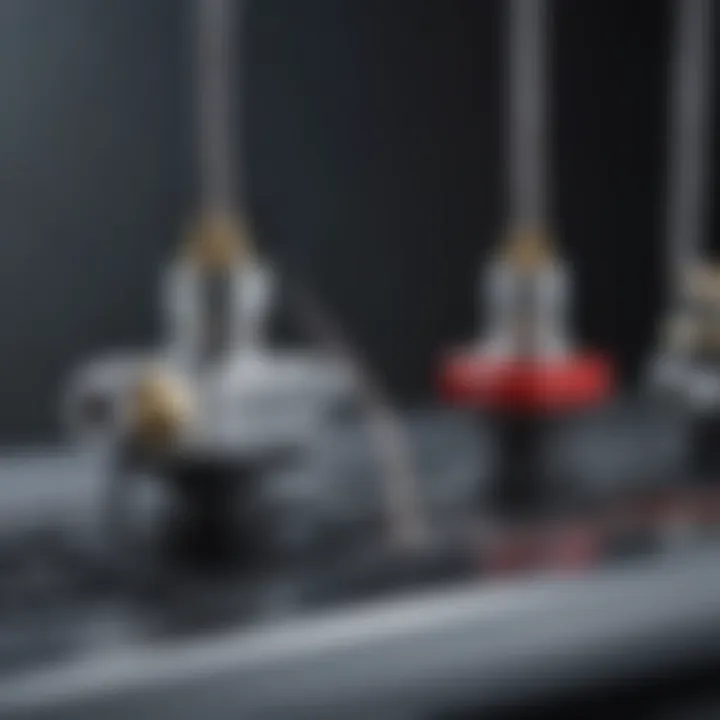
In summary, each type of non-contact flow switch offers unique characteristics and benefits, factoring into their selection for specific applications. From ultrasonic's cleanliness to electromagnetic's durability and optical's sensitivity, understanding these distinctions can guide professionals in making informed choices that enhance their operational efficiency.
Applications in Various Industries
The versatility and efficiency of non-contact flow switches have sparked considerable interest across multiple industries. These devices are particularly valuable due to their ability to monitor flow rates without direct contact with the fluid, which in turn helps mitigate contamination, wear, and tear of components. This section delves into the specific applications of non-contact flow switches in water and wastewater management, chemical processing, and food and beverage production.
Water and Wastewater Management
In the realm of water and wastewater management, non-contact flow switches play an indispensable role. They facilitate accurate flow measurement in pumping stations, treatment facilities, and distribution systems. By utilizing ultrasonic or electromagnetic techniques, these switches can reliably determine water flow rates without interrupting the flow or risking contamination.
The demand for real-time monitoring in this sector is crucial for maintaining quality standards and regulatory compliance. For instance, if a treatment plant identifies an unexpected drop in flow, it can swiftly implement corrective actions to avert potential bottlenecks. Furthermore, these switches drastically reduce maintenance costs as they do not have moving parts that are susceptible to wear. Hence, operators can observe a marked decrease in downtime related to maintenance tasks, allowing for a more streamlined operation.
Chemical Processing
Chemical processing presents unique challenges when measuring fluid dynamics, particularly the high corrosiveness and temperature variability of certain substances. Non-contact flow switches are particularly suited for this environment, as they can function effectively with corrosive chemicals without the risk of corrosion damaging the sensing equipment.
The precision offered by these devices enables accurate control of chemical flow, which is essential for ensuring optimal reactions in reactors or mixers. Moreover, the reliability of non-contact switches minimizes the risk of contamination during batch processes, a key consideration in the production of sensitive chemicals or pharmaceuticals. This translates directly into better product quality and adherence to safety standards. Notably, companies can increase the efficiency of their operations, leading to cost savings and improved profitability.
Food and Beverage Production
In the food and beverage industry, hygiene is paramount. Non-contact flow switches offer an ideal solution to measure liquid flows while adhering to strict sanitation requirements. By eliminating contact with the fluid, these switches help maintain the purity and taste of food products, which is essential for consumer safety and brand reputation.
Furthermore, these devices can be employed in various applications, from monitoring the flow of water used in washing produce to managing the flow rates of juices, sauces, and dairy products during processing and packaging. The enhanced reliability of non-contact flow monitoring leads to improved yield and efficiency in production lines.
The integration of non-contact flow switches aligns well with the increasing trends towards automation and smart systems in food production. This convergence not only simplifies operations but also promotes better data analytics, enabling producers to make informed decisions quickly. A notable benefit here is the ability to track flow rates in real-time, leading to prompt responses to fluctuations and avoiding costly production halts.
Non-contact flow switches are transforming how industries interact with flow measurement technology, helping to achieve higher efficiency while maintaining safety and compliance standards.
In summary, the applications of non-contact flow switches across different sectors underscore their importance in modem fluid dynamics. As industries evolve towards smarter and more efficient systems, these devices will undoubtedly continue to play a pivotal role in optimizing operations.
Advantages of Non-Contact Flow Switches
When examining flow measurement systems, the advantages of non-contact flow switches stand out like a beacon. These devices offer pivotal benefits that make them indispensable across various applications. Emphasizing their advantages not only highlights their significant role in modern technology but also underscores their increasing relevance in an array of industries.
Reduced Risk of Contamination
One of the standout features of non-contact flow switches is their capability to minimize contamination risk. Traditional flow switches often rely on physical contact to measure flow, which can introduce various problems. For instance, when these devices touch a medium—be it liquid or gas—there is a higher potential for particles, bacteria, or other contaminants to latch onto the measurement device. This risk could lead to inaccurate readings or, worse, compromise the integrity of the system as a whole.
In environments like food processing or pharmaceuticals, where hygiene is paramount, non-contact devices shine. They function without touching the fluid. This means that sensitive processes can maintain purity, ensuring that the end products remain uncontaminated. Less contact also translates to fewer cleaning cycles, which is a notable convenience. In turn, this leads to lower operational costs, as less time and resources are spent on maintenance – a win-win situation.
"In sectors where purity matters, eliminating contact is not just a benefit; it’s a necessity."
Enhanced Reliability and Maintenance
Beyond contamination concerns, non-contact flow switches present enhanced reliability and maintenance advantages. Because these devices operate without direct interaction with the flowing medium, they generally experience less wear and tear compared to traditional switches. This durability translates into longer lifespans, reducing the need for frequent replacements.
Moreover, non-contact models tend to require less maintenance overall. Without moving parts that are susceptible to wear, these devices can function properly over extended periods with minimal oversight. As a result, operators can focus on critical tasks instead of constantly monitoring and servicing their flow measurement instruments.
In fast-paced industries, this reliability is crucial. Imagine a chemical plant where accurate flow control is vital. Any hiccup in measurement can lead to costly downtime or safety hazards. Non-contact flow switches alleviate such fears by ensuring that the system remains operational and efficient without constant intervention.
In essence, transitioning to non-contact flow switches from traditional models can greatly improve overall system resilience and operational ease. With a solid understanding of their advantages, industries can harness the full potential of flow measurement technologies, paving the way for increased efficiency and safety in their processes.
Choosing the Right Non-Contact Flow Switch
When it comes to flow measurement, picking the right non-contact flow switch is crucial. The selection not only impacts operational efficiency but also plays a significant role in ensuring safety and reliability across various industries. Understanding the nuances of non-contact flow switches can lead to better decision-making and ultimately enhance workflow processes.
Key Selection Criteria
Choosing a non-contact flow switch involves considering several key factors. First and foremost, it’s essential to look at the specific application requirements. For instance, if you are dealing with viscous fluids, an ultrasonic flow switch might be more suitable than an electromagnetic one.
Additionally, consider the following criteria when selecting:
- Accuracy and Precision: Ensure that the switch can provide the level of accuracy required for your specific application. It’s not just about what looks good on paper; real-world performance matters tons.
- Operating Range: Verify the flow rate limits specified by the manufacturer. Some switches may have a narrow operating range that will not suit your needs.
- Environment Compatibility: Assess the environment where the flow switch will operate. Factors like temperature extremes, humidity levels, and exposure to corrosive substances can affect performance.
- Maintenance Needs: Non-contact flow switches often require less maintenance than their contact counterparts, but you should still check what maintenance, if any, is needed. Opt for devices that are easy to clean or require minimal upkeep.
- Cost Considerations: Don’t let price be the only factor, but keep budget constraints in mind. Evaluate the total cost of ownership to ascertain whether the investment is justified over time for your operation.
System Compatibility

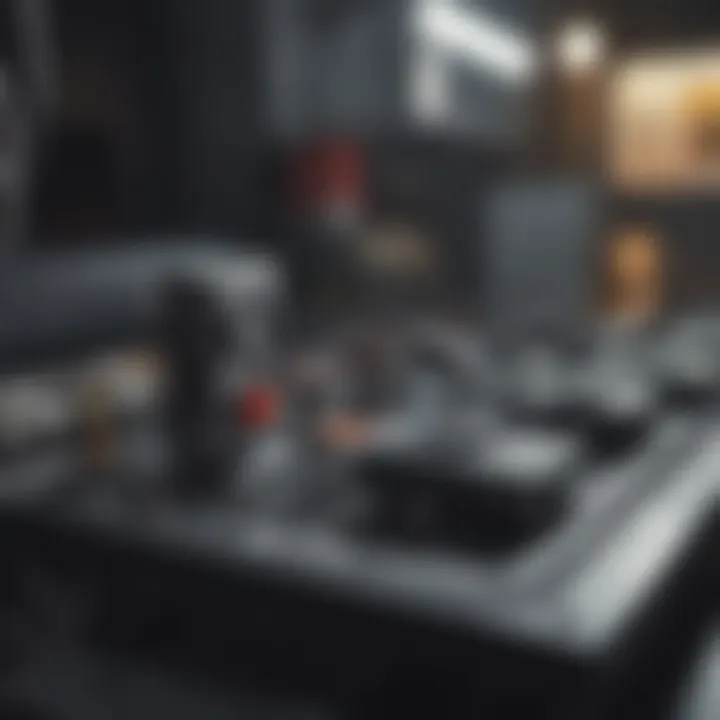
Compatibility with existing systems is another critical aspect when choosing a non-contact flow switch. Ensuring that the flow switch integrates well with your current infrastructure can save time, money, and headaches down the road.
- Communication Protocols: Check whether the flow switch supports the communication protocols that your system utilizes. Whether it’s Modbus, Profibus, or another standard, alignment here is key for smooth data exchange.
- Voltage Requirements: Confirm that the voltage and power supply of the flow switch is in sync with what your system requires. Mismatched voltage can lead to malfunctions or even worse, damage.
- Physical Dimensions and Mounting: Pay attention to the size and mounting options available for the flow switch. Not all spaces are created equal, and finding a switch that fits without extensive modifications can streamline installation.
In essence, choosing the right non-contact flow switch is not merely a matter of preference, but rather a thorough evaluation of functionality, compatibility, and long term feasibility. These considerations help not just in making the right choice but in ensuring honed efficiency too.
Challenges in Non-Contact Flow Measurement
As industries continue to evolve and embrace advanced technologies, understanding the challenges faced in non-contact flow measurement becomes paramount. Despite their numerous advantages, non-contact flow switches are not without hurdles. Acknowledging these challenges helps professionals and researchers make informed decisions when considering these systems.
Environmental Constraints
Environmental factors can significantly impact the effectiveness and performance of non-contact flow switches. For instance, the presence of dust, moisture, or other particulates can interfere with the sensors' operation. In areas with high humidity or temperature fluctuations, ultrasonic flow switches may struggle to provide accurate readings. Furthermore, external vibrations and electromagnetic interference could distort sensor signals, causing erroneous flow measurements.
Some key considerations include:
- Temperature and Humidity: Extreme conditions could affect the integrity of sensors and their ability to function correctly.
- Dust and Contaminants: Dust accumulation on sensors might obstruct detection capabilities, leading to loss of accuracy.
- Vibration: Machinery nearby generates vibrations that could disrupt sensor readings, compromising reliability.
Careful assessment of the operating environment is essential. Using protective housings or selecting devices designed to operate under harsher conditions can mitigate these challenges, maintaining reliable performance despite adverse environmental influences.
Limitations in Certain Applications
While non-contact flow switches offer several advantages, they may not be suitable for every application. Certain fluids, particularly those with low flow rates or highly viscous characteristics, can present challenges. For example, in low-flow scenarios, an ultrasonic flow switch might struggle to detect and measure accurately due to its reliance on sound wave propagation, which necessitates a minimum flow to generate reliable readings.
Several limitations to consider include:
- Fluid Properties: Viscous or opaque fluids may hinder accurate measurements by optical or ultrasonic switches.
- Installation Constraints: Physical layout and the orientation of piping systems could limit the effective deployment of non-contact sensors.
- Cost Considerations: In certain low-budget setups, these advanced devices may not be cost-competitive compared to traditional flow measurement tools, especially if their benefits do not outweigh the investment.
In situations where these limitations apply, it may be prudent to explore alternative sensing technologies or consider hybrid systems that can integrate both contact and non-contact methods, depending on the specific requirements.
"A well-rounded understanding of both the strengths and weaknesses of any technology is critical for effective implementation."
By addressing these challenges, industry professionals can better navigate the complexities of fluid measurement, ensuring their systems function efficiently and accurately in various applications.
Future Trends in Flow Switch Technology
The landscape of flow measurement technology is evolving at a brisk pace. This evolution is not merely a fad but is deeply rooted in the pursuit of efficiency, accuracy, and system integration. The growth of non-contact flow switch technology speaks to the heart of future advancements, aligning with the increasing demand for enhanced operational capabilities across various industries.
With industries such as water management, chemical processing, and food production relying on accurate flow measurement, the trends signaling a shift towards non-contact methods indicate a significant leap in how these sectors approach flow control. Understanding these trends is crucial for professionals aiming to stay ahead in their respective fields.
Technological Advancements
Recent developments in technology are reshaping how non-contact flow switches function and are deployed. One noteworthy advancement is the refinement of signal processing algorithms. These algorithms help in better interpreting data from flow switches, leading to increased accuracy and reduced error rates. For instance, ultrasonic flow switches are employing advanced signal processing which greatly enhances their sensitivity to flow variations.
Additionally, sensor miniaturization is enabling the design and implementation of compact flow measurement solutions. These smaller devices can be integrated into existing systems without significant alterations, making it easier for businesses to upgrade their flow measurement capabilities.
- Improved sensor technology that enhances measurement precision.
- Integration of artificial intelligence for real-time analysis and predictive maintenance.
- Utilization of IoT for remote monitoring and operational efficiency.
Integration with Smart Systems
The future also leans towards the integration of non-contact flow switches with smart systems. The shift towards smart technologies requires flow measurement instruments to communicate seamlessly with various operational platforms. This integration allows for better data sharing and management across systems, significantly enhancing process control.
Incorporating non-contact flow switches into smart manufacturing setups provides numerous advantages:
- Real-time monitoring: Instant data feedback helps in making quick operational decisions.
- Enhanced diagnostics: Identifying potential issues before they escalate, thus minimizing downtime.
- Data-driven insights: Utilizing gathered data to optimize processes and reduce wastage.
"The future integration of non-contact flow technologies with smart systems not only aims at improving efficiency but also promotes sustainability through better resource management."
As organizations embrace these advanced systems, the potential for improved safety and operational efficiency becomes apparent. With technological advancements paving the way and smart systems providing the framework for integration, the future of flow switch technology looks promising. It is vital for stakeholders in various industries to recognize these trends and adapt accordingly, ensuring they harness the full potential of what non-contact flow switch technology offers.
End
In the realm of flow measurement, the significance of non-contact flow switch technology cannot be overstated. This article has cast a spotlight on the many layers of this innovative approach to measuring fluid flow without direct interaction. As industries strive for efficiency and safety, understanding non-contact mechanisms presents clear advantages and opens new pathways for innovation.
Non-contact flow switches work by using advanced techniques such as ultrasonic and electromagnetic principles, making them enviable alternatives to traditional methods. Their ability to function without contacting the fluid stream reduces the risk of contamination, making them a boon for sectors like food and beverage as well as chemical processing.
When looking back at the content shared, several key points emerge:
- Diverse Applications: Non-contact flow switches are not confined to a single industry; they find use in water management, chemical processing, and even in food technology, catering to various operational needs.
- Enhanced Reliability: With fewer mechanical parts necessary in non-contact flow measurements, there’s a marked increase in durability and reduced maintenance needs.
- Environmental Considerations: Understanding the environmental limitations is crucial. Non-contact systems must still adapt to climatic challenges without compromising accuracy.
Moreover, as we venture into the future, the integration of these switches with smart technologies promises a profound impact. The internet of things and automation will likely intertwine with flow measurement, leading to enhanced monitoring, data collection, and predictive capabilities.
In summary, grasping the principles and workings of non-contact flow switches equips educators, researchers, and professionals alike with valuable insights necessary for optimizing operational efficiency. Their importance extends beyond just the mechanics; it encapsulates a broader perspective on fluid dynamics and technological evolution. As industries continue to adapt and evolve, so too must our understanding and implementation of these technologies.