PDMS Mold Fabrication: A Comprehensive Guide
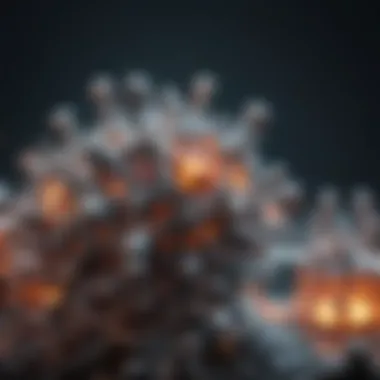
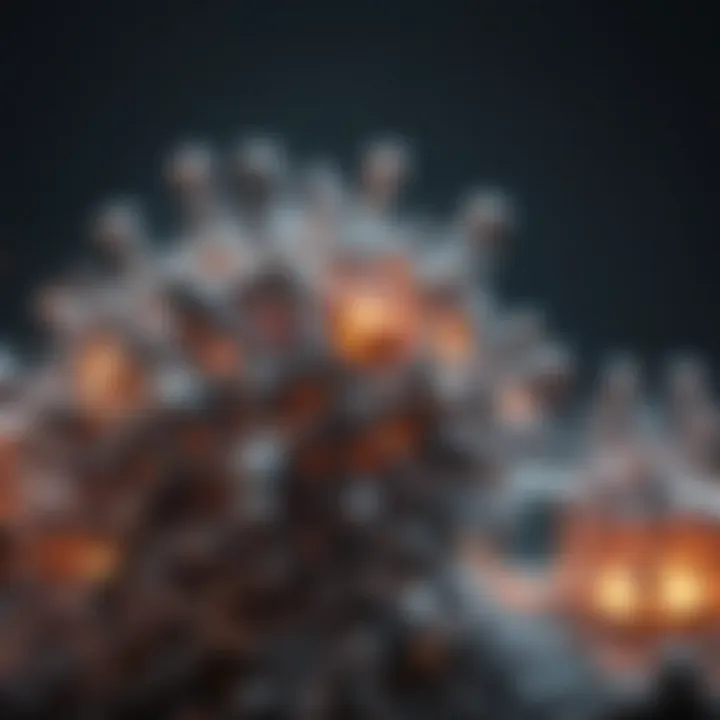
Intro
In the realm of material science and engineering, the significance of polydimethylsiloxane (PDMS) cannot be overstated. This silicone-based organic polymer has found its way into numerous applications, particularly in micro and nanofabrication. Its remarkable properties—including flexibility, optical transparency, and biocompatibility—make it a preferred choice for researchers and industry professionals alike. PDMS mold fabrication is not just about creating molds; it's about enabling innovative designs that can lead to transformative advancements in various scientific fields.
This process is intricate and multifaceted, requiring a meticulous understanding of both the material and the techniques employed in fabrication. From the selection of raw materials to the curing process and final implementation, each step in the PDMS molding procedure holds its own challenges and opportunities.
Herein, we will embark on a thorough examination of the methods and materials utilized in PDMS mold fabrication, as well as the practical implications of these molds in real-world applications. Understanding these aspects is essential for those looking to harness the potential of PDMS in their respective fields.
Research Methodology
Description of research design and approach
The research design employed for examining PDMS mold fabrication leans heavily on both qualitative and quantitative methodologies. This dual approach facilitates a balanced view of the intricacies involved in the fabrication process. Qualitative research allows us to explore the nuanced characteristics of PDMS, while quantitative data helps in understanding the efficiency and effectiveness of various fabrication techniques.
In crafting this comprehensive study, we have relied not only on primary experimental data but also on extensive literature reviews. Examining previous studies lends credibility and context, highlighting gaps that thiis article aims to address.
Materials and methods used in the study
The materials used in PDMS mold fabrication typically include:
- Polydimethylsiloxane (PDMS): The primary material, known for its specific properties conducive to molding.
- Curing Agents: These are necessary for the polymerization of PDMS and play a crucial role in determining the mechanical properties of the end product.
- Release Agents: Often used to ensure easy demolding, these agents mitigate adhesion between the mold and the final product.
The methods employed include:
- Preparation of PDMS: This involves mixing the base PDMS with curing agents in a specified ratio, typically 10:1.
- Degassing: To ensure no air bubbles affect the mold, the mixture is placed in a vacuum chamber.
- Pouring and Curing: The prepared mixture is poured into the desired mold and allowed to cure at room temperature or in a heating device, depending on the requirements.
- Demolding: Once fully cured, the PDMS mold is carefully removed, ready for application.
This methodology lays the groundwork for deeper discussions and analysis regarding the implications of PDMS mold fabrication in the following sections.
Prelims to PDMS Mold Fabrication
Polydimethylsiloxane, commonly known as PDMS, has carved a niche within the realm of material science, particularly in mold fabrication. It’s not just another run-of-the-mill silicone; it's a versatile polymer that boasts unique properties conducive to soft lithography, microfluidics, and various biomedical applications. Understanding PDMS mold fabrication is pivotal for students, researchers, and professionals who aspire to explore new frontiers in micro and nanofabrication.
The significance of introducing PDMS mold fabrication lies in its practical implications across numerous domains. First, it opens the door to innovations in microfluidic device design, allowing for precise control over fluid flow at microscale. Additionally, PDMS molds provide a cost-effective approach for fabricating complex structures that ease the production process in laboratories that operate on a shoestring budget.
Given the increasing demand for miniaturization in technology, this analysis delves into both the methodology and material properties involved in PDMS mold creation, highlighting its relevance in contemporary research. The following sections will unravel the how-tos, historical context, and the myriad applications of PDMS, thereby aiding professionals in making informed decisions surrounding material use and fabrication techniques.
What is PDMS?
PDMS, a silicone-based organic polymer, is composed of repetitive siloxane units. Its molecular structure allows it to maintain remarkable elasticity and hydrophobicity. You find it being utilized in everything from common household items to sophisticated biomedical devices. One of the standout features of PDMS is its biocompatibility, making it a prime candidate for applications in healthcare and life sciences.
Due to its low surface energy, PDMS molds can easily release casted parts, which is crucial for producing intricate designs without incurring damage to the molds themselves. This characteristic is particularly beneficial during the manufacturing stages involving delicate features or fragile components.
Historical Context and Development
The journey of PDMS began post-World War II, as researchers sought to develop materials with specific properties suitable for a burgeoning electronics industry. By the 1980s, PDMS found its footing in the field of microfabrication. The adaptation of soft lithography techniques using PDMS revolutionized the way researchers approached the creation of micro and nano structures.
"The realization of PDMS' potential was a game changer in the field of microfluidics," noted one research paper on polymer materials.
As the technology advanced, PDMS molds became synonymous with the development of micro-devices, enabling widespread applications in diagnostics and biotechnology. Innovations in fabrication techniques, such as soft lithography, allowed for the meticulous crafting of intricate patterns and geometries, making PDMS a staple for engineers and researchers alike. Over the decades, the polymer has continued to evolve, thus solidifying its stance as an essential material in modern fabrication processes.
Material Properties of PDMS
Understanding the material properties of PDMS is essential in the realm of mold fabrication. These properties dictate how the material behaves under various conditions, influencing everything from mold longevity to the quality of the final product. PDMS, or polydimethylsiloxane, is celebrated for its versatility and unique characteristics, making it a popular choice in sectors like microfluidics and biotechnology.
Chemical Composition
PDMS is a silicone-based polymer comprised mainly of a repeating unit of siloxane, which is a chain of alternating silicon and oxygen atoms. This composition lends itself to remarkable stability and resistance to degradation. The ratio of silicon to oxygen in PDMS can be adjusted, which influences the properties of the final product. For instance, variations in this ratio can manipulate the surface properties and hydrophobicity of the PDMS, thus enabling tailored applications in different fields. With the introduction of fillers or additives during the synthesis process, one can achieve specific performance characteristics, like improved mechanical strength or thermal resistance.
Physical Characteristics
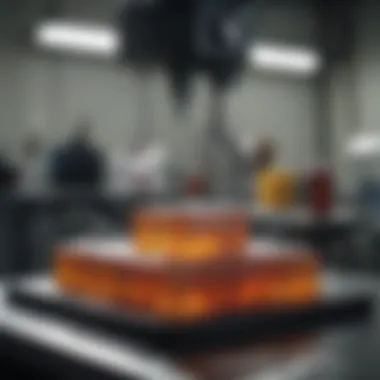
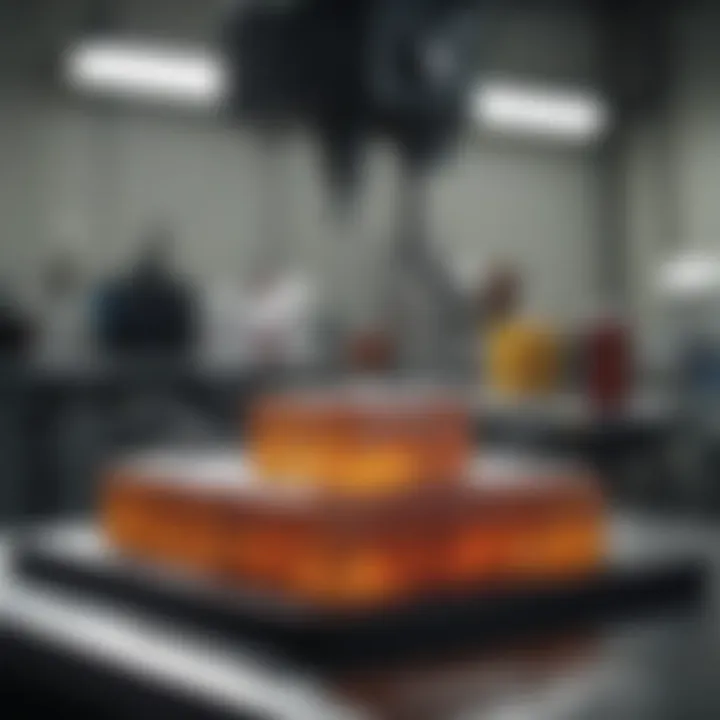
When it comes to physical attributes, PDMS is fairly distinct. Its low density and high flexibility stand out, both crucial for applications that demand precision and detailed reproduction of intricate designs. The material is optically transparent, which is quite beneficial for applications in optofluidics or bio-imaging, where light interactions are paramount. Among its many features, the following are worth highlighting:
- Flexibility: This allows PDMS to conform to various shapes, which is invaluable when creating molds with complex geometries.
- Low Surface Energy: This characteristic limits adhesion, making it easier to demold final products while also providing a barrier to certain contaminants and chemicals.
- Biocompatibility: PDMS is non-toxic and has been found to be compatible with biological systems, a critical factor in medical applications.
Thermal and Mechanical Properties
Delving into thermal and mechanical properties, PDMS exhibits remarkable resilience. It remains stable over a wide range of temperatures, typically between -50°C to 200°C. This stability allows it to maintain its form and function in varied environments.
From a mechanical standpoint, PDMS possesses good elasticity and tensile strength, making it suitable for applications requiring stable molds under mechanical stress. However, it’s noteworthy that while PDMS can stretch significantly, it may suffer from wear over time, leading to fatigue in high-use scenarios.
Additionally, the toughness of PDMS can be enhanced by blending it with stronger rubbers or other polymers. This layered approach provides a solution for applications that may expose the mold to harsh conditions or stress.
In summary, the chemical composition, physical characteristics, and thermal as well as mechanical properties of PDMS play a significant role in mold fabrication. Each aspect contributes not just to the production process but also to the performance of the final molded devices, making an understanding of these properties indispensable for researchers and professionals alike.
Mold Fabrication Techniques
Understanding the various mold fabrication techniques is essential to grasp the intricacies of PDMS mold creation. Each method has its unique attributes and applications that can significantly influence the final product's functionality and effectiveness. The choice of technique can alter the resolution, reproducibility, and even the physical characteristics of the molds. This section aims to dissect the most prevalent methods, providing insights into why they matter and how they interrelate.
Soft Lithography Process
Soft lithography is a standout technique in the realm of PDMS mold fabrication. This process primarily utilizes a soft elastomer to replicate intricate features on a substrate. The first critical step involves creating a master mold, often made from silicon or photoresist material, where micro-patterns are etched out. Once this master is ready, PDMS is poured over it. After curing, the PDMS solidifies and can be peeled off, revealing features that are exact counterparts to the master mold.
There are several advantages to using soft lithography:
- High-resolution features: The ability to replicate intricate details is unparalleled, making it suitable for applications requiring precision.
- Versatility: Soft lithography can accommodate a range of designs and materials, broadening its application spectrum.
- Cost-effectiveness: The materials and processes involved are often more affordable compared to other high-resolution techniques.
However, it’s critical to consider factors like the surface energy of the substrate and the viscosity of the PDMS to ensure optimal results. Adjustments in these parameters can enhance the quality of the features reproduced.
Photolithography vs. Soft Lithography
Both photolithography and soft lithography are pivotal in producing PDMS molds, but they cater to different requirements. Photolithography employs light to transfer geometric patterns onto a photoresist, providing exceptional accuracy. In contrast, soft lithography focuses on the flexibility of the elastomer to create molds from existing features.
When comparing the two, it’s vital to keep in mind the following points:
- Feature size: Photolithography typically allows for finer feature sizes, while soft lithography might reach larger scales without compromising detail.
- Processing time: Soft lithography can be more efficient for rapid prototyping due to fewer steps; however, photolithography may be preferred for long production runs requiring uniformity.
- Setup costs: Initial investments in photolithography equipment tend to be higher, making soft lithography a compelling choice for startups or smaller projects.
Ultimately, the best technique depends on the specific needs of the project at hand.
Casting Techniques
Casting techniques form the backbone of making molds in PDMS fabrication. The simplest approach involves taking a designed template and pouring the PDMS mixture into it, allowing it to cure. This method is straightforward but can also lead to certain challenges.
There are several casting methods:
- Open casting: The PDMS is simply placed in an open mold. This method works well for large molds but can sometimes result in imperfections depending on environmental conditions.
- Closed casting: Often used for more intricate designs, in this technique, both sides of the mold are enclosed. This can lead to finer detail replication and improved mold strength when setting.
- Injection molding: Though less common with PDMS, some setups allow for injecting mixed PDMS into the mold cavity, which can reduce air bubbles and achieve uniform thickness.
An important consideration in casting is how the curing conditions, such as time and temperature, can affect the mechanical properties of the final product. Uniform curing is critical for predictable outcomes.
"The process of choosing the right mold fabrication technique can significantly affect the final application's performance and design flexibility."
By delving into these various methods, one gains a comprehensive view of the options available in PDMS mold fabrication and how they can be optimally utilized based on specific project requirements.
Design Considerations for PDMS Molds
When diving into the world of PDMS mold fabrication, one must consider several intricate design factors. The design considerations are critical, serving as a foundation for the successful application and functionality of the molds. Each choice made during the design phase profoundly impacts the performance and usability of the final product, especially in specialized fields like microfluidics and biotechnology.
Geometrical Constraints
Geometrical constraints encompass the physical limitations imposed by the mold's design. Understanding these limits is paramount to achieving precise functionality. PDMS molds can replicate complex geometries, but certain factors must be taken into account:
- Aspect Ratio: The ratio of the mold's height to width can affect how well a feature fills during casting. Features that are too tall relative to their width may lead to incomplete casts.
- Undercuts: These arise when the mold has features that prevent easy removal of the final product. Proper planning is necessary to avoid design snafus that complicate demolding.
- Taper Angles: Designing slopes in features can ease the process of removing the mold, ensuring that delicate details aren’t lost.
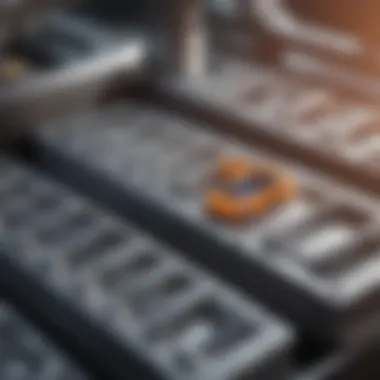
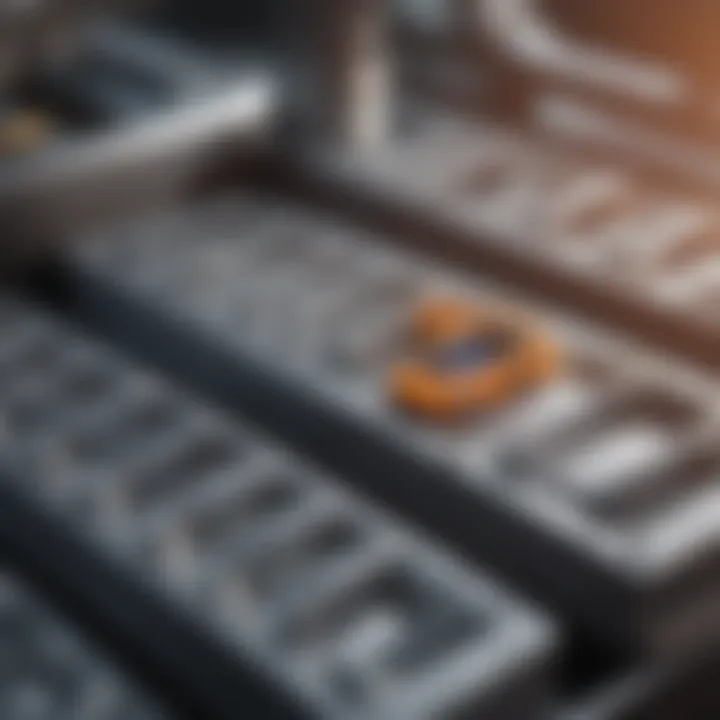
In essence, having a firm grasp on geometrical constraints can make or break the efficiency of PDMS molds.
Feature Resolution and Scale
The feature resolution defines the smallest details that can be accurately captured in the mold. This is critical when creating devices that depend on precision. Considerations include:
- Minimum Feature Size: The ability to produce fine details directly relates to the resolution of your fabrication technique. Soft lithography can often achieve resolutions down to a few micrometers, which is impressive for many applications.
- Scaling Up: As designs grow, maintaining accuracy becomes challenging. The relation between the features and the overall size of the mold needs careful handling. A larger design might seem straightforward, but it can introduce discrepancies in feature replication.
Thus, designers must balance the need for detail with realistic manufacturing limits to ensure successful outcomes.
Design Software and Tools
Choosing the right design software and tools can smoothen the mold creation process. Ingenious designers leverage specific programs tailored for mold design, which help in visualizing and perfecting the designs before physical modeling. A few noteworthy options include:
- AutoCAD: This widely-used CAD software offers detailed 2D/3D drafting capabilities.
- SolidWorks: Known for its simulation features, it aids in evaluating the mechanical performance of molded parts during the design phase.
- COMSOL Multiphysics: Particularly beneficial for modeling fluid dynamics, essential in microfluidics applications.
Before fabricating a mold, having a blueprint that is formulated with a capable tool can save considerable time and resources down the line. As the saying goes, "Measure twice, cut once"—in the context of PDMS molds, this means meticulous planning can lead to less waste and more precise end results.
"Understanding the nuanced aspects of mold design is the key to unlocking the full potential of PDMS technology."
Ultimately, these design considerations not only determine the quality of PDMS molds but also their practical applications in various high-tech fields. By carefully contemplating geometrical limits, ensuring feature precision, and utilizing top-notch design software, researchers and professionals can set the stage for successful mold development.
Applications of PDMS Molds
The applications of PDMS molds stretch far and wide across various fields, catching the attention of researchers and engineers alike. Known for its versatile properties and simple fabrication process, PDMS is valuable in developing devices that operate at the micro and nanoscale. This section outlines the key areas where PDMS molds have made significant impacts, highlighting their benefits and the considerations necessary for effective application.
Microfluidics
Microfluidics, the science of manipulating fluids within micro-sized channels, has seen immense growth driven by PDMS molds. This can be likened to a conductor orchestrating a symphony, where each fluid droplet plays its part in a grand design. PDMS's clarity allows for optical observations, permitting researchers to monitor reactions in real-time, which is critical for applications in diagnostics and chemical analysis.
There are several factors that contribute to the success of PDMS in microfluidic applications:
- Chemical Compatibility: PDMS is compatible with a wide range of biological and chemical substances, making it suitable for bio-assays and environmental monitoring.
- Ease of Fabrication: The soft lithography process enables the quick and cost-effective production of intricate channel designs.
- Hydrophobicity: This characteristic allows researchers to manipulate fluid flow easily, adapting channels for specific experiments.
Nonetheless, challenges remain, such as potential leaching of uncured PDMS into the fluid. Ensuring proper curing and fabrication techniques is crucial to maintain the reliability of the results.
Biotechnology and Biomedical Devices
PDMS molds have revolutionized the fields of biotechnology and biomedical engineering. The versatility of PDMS materials means they can be fashioned for various applications, from drug delivery systems to cell culture plates. In biomedical devices, for instance, PDMS is often used due to its flexibility and biocompatibility.
Some notable advantages include:
- Low Surface Energy: This property assists in the easy detachment of devices from molds, which is critical in high-throughput applications.
- Porosity Control: The permeability of PDMS allows for gas exchange, making it an ideal material for cell growth.
- Ease of Integration: PDMS can be easily integrated with other materials, aiding the development of complex tissue engineering applications.
However, the mechanical properties of PDMS can lead to limitations in certain instances, such as a tendency for deformation under stress. Thus, careful consideration of design and application requirements is needed to leverage its benefits efficiently.
Electronics and Sensor Fabrication
The integration of PDMS into electronics and sensor fabrication has paved the way for lightweight and flexible devices. From wearables to advanced sensors, PDMS provides a platform for innovative technological developments. Its excellent dielectric properties and ability to form complex geometries present vast opportunities in the electronics sector.
Benefits include:
- Flexibility: Devices made from PDMS can bend and stretch, enabling new applications in flexible electronics.
- High Sensitivity: PDMS sensors are being developed that can detect minute changes in environmental conditions, useful for real-time monitoring tools.
- Simple Production: PDMS’s fabrication processes allow for rapid prototyping, shortening the time between design and deployment.
Nevertheless, issues like moisture permeability and thermal instability need to be addressed in product designs to ensure long-term reliability. The potential to marry PDMS's unique qualities with other materials can drive forward innovation in this field.
"From microfluidic devices to advanced sensors, the applications of PDMS are shaping the future of technology and science."
In summary, PDMS molds find their relevance across multiple domains, with each carrying unique challenges and benefits. Whether it’s conducting a microfluidic experiment or pushing the boundaries of biomedicine, PDMS continues to play a crucial role in modern advancements.
Challenges in PDMS Mold Fabrication
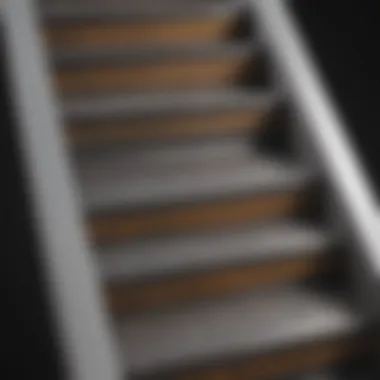
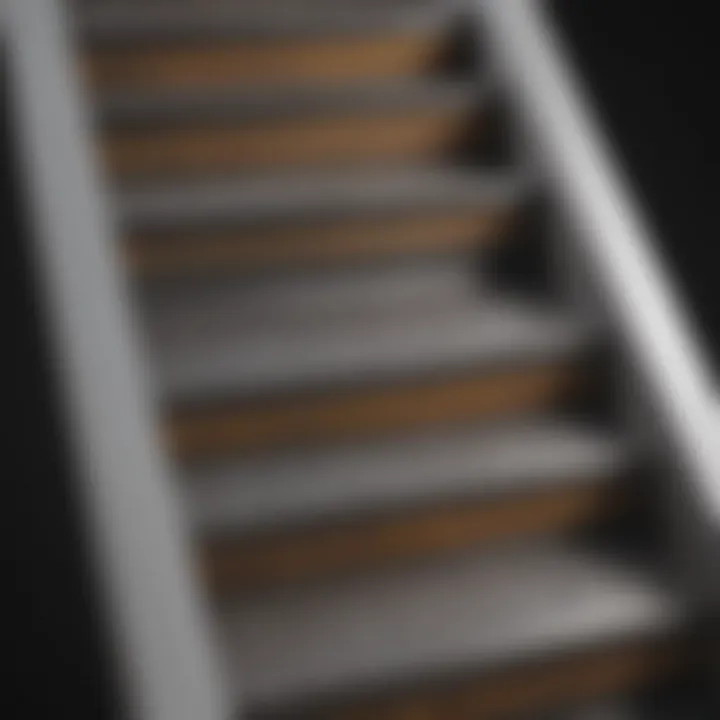
The realm of PDMS mold fabrication, while brimming with potential, is not without its hurdles. A clear grasp of the challenges faced during this intricate process is crucial for advancing both academic knowledge and practical application. Understanding these challenges not only enhances the quality of PDMS molds but also ensures that researchers and industry professionals can devise strategies to push the boundaries of what's achievable in the fields of micro and nanofabrication.
Material Limitations
PDMS, known for its flexibility and biocompatibility, does have certain constraints that can impede its use. For instance, its thermal stability isn’t the best, particularly at elevated temperatures. This can lead to softening or deformation, making it unsuitable for applications requiring high-temperature processes. Furthermore, PDMS has a tendency to absorb small molecules. If one is working with sensitive biochemical applications, this property might interfere with reactions or results, leading to contamination or compromised data.
Additionally, PDMS can be somewhat tricky when it comes to surface treatment. Without adequate preparation, the surface might not hold subsequent layers of materials like polymers or metals well. This can limit its application in multi-layer structures, often required in sophisticated device design.
Process Optimization Issues
Optimizing the fabrication process of PDMS molds is a balancing act. Achieving the desired mold precision while maintaining cost-effectiveness is pivotal. Too often, there’s a compromise between accuracy and the time-intensive nature of fabrication techniques.
For instance, soft lithography—a popular technique in PDMS fabrication—requires precise alignment and control over curing conditions. Variations in these factors can lead to defects, impeding reproducibility. As a result, extensive process parameters must be meticulously defined and controlled, a task that can prove to be challenging on a large scale. Also, complicated features may require multiple iterations of design and testing, which adds to time and resource consumption.
Post-Fabrication Challenges
Once a PDMS mold is created, the journey doesn't simply end. Post-fabrication processes can introduce another layer of difficulty. One of the often-neglected aspects is the ease of mold handling. Due to its inherent flexibility, PDMS molds might deform under stress or when exposed to a different environment.
Moreover, when attempting to replicate intricate patterns, the release of the mold from the substrate can become problematic. If the mold sticks to the substrate, it can result in damages, hampering the overall yield. Another challenge involves maintaining mold cleanliness. Residue from previous use can affect subsequent experiments, necessitating rigorous cleaning protocols.
The challenges in PDMS mold fabrication highlight the need for ongoing innovation and research in this area. Recognizing and addressing these obstacles is not merely a matter of improving efficiency; it's about unlocking the full potential of PDMS applications in various innovative fields.
In sum, as professionals delve into the intricacies of PDMS mold fabrication, acknowledging these challenges is essential. Each of these issues presents an opportunity for improvement, and tackling them head-on can foster advancements that facilitate the widespread use of PDMS in pioneering technologies.
Future Directions in PDMS Mold Technology
The realm of PDMS mold technology is evolving. Understanding where it might head next is essential for those invested in micro and nanofabrication. The trajectory of PDMS mold applications not only highlights its critical role in contemporary research but also reflects the limitless possibilities that could unfold in diverse fields, from medicine to electronics. This section will underscore potential shifts in materials, techniques, and integration with emerging technologies.
Innovative Materials and Alternatives
The quest for enhanced performance often drives the exploration of innovative materials beyond traditional PDMS. For instance, new silicone elastomers and composites are being investigated for their superior chemical resistance or mechanical properties. These alternatives might include copolymers that blend PDMS with other polymers to achieve functions not possible with PDMS alone.
Additionally, biomaterials, like those derived from natural sources, are gaining traction due to their bio-compatibility. This could be revolutionary, especially in fields such as tissue engineering and drug delivery, where the interaction between materials and biological systems is crucial. Just imagine the potential of combining PDMS with biodegradable materials; it could lead to more sustainable practices in mold fabrication.
Advancements in Fabrication Techniques
The techniques employed in PDMS mold fabrication are also on the cusp of transformation. Traditional methods, while effective, come with limitations. For example, researchers are looking at ways to refine soft lithography processes, not just to increase resolution but also to enhance throughput and scalability. Techniques like roll-to-roll lithography might play a role in simplifying large-scale production while maintaining precision.
Moreover, recent advances in 3D printing technology for mold creation are noteworthy. This method allows for the rapid prototyping and customization of complex geometries that aren’t easily achievable through conventional techniques. Utilizing digital fabrication might open doors to creating bespoke molds tailored to specific applications, thereby speeding up iterations and development cycles.
Potential for Integration with Other Technologies
As the world marches toward a more interconnected future, the integration of PDMS mold technology with other emerging technologies could be a game-changer. For instance, the combination of PDMS with micro-electromechanical systems (MEMS) is posing exciting new possibilities. This synergy could lead to smarter microfluidic devices, pushing the boundaries of what we currently understand about fluid dynamics at a micro-scale.
Furthermore, merging PDMS molds with electronic components could foster the development of soft robotics and wearable technologies. The flexibility and tunable properties of PDMS make it an inviting candidate for creating advanced interfaces in these applications.
“Innovation is the ability to see change as an opportunity - not a threat.” - Unknown
The ongoing research and development in the field underscore the importance of remaining vigilant and adaptable. Not just for those working with PDMS specifically, but for all entities involved in micro and nanofabrication. Keeping an eye on these future directions can lead to enhanced methodologies that respond better to the demands of evolving technologies and industries.
Culmination
In wrapping up the exploration of PDMS mold fabrication, it becomes clear that this study is not merely academic; it embodies an essential facet of modern engineering and technology. The versatility of polydimethylsiloxane molds stretches across numerous fields, from microfluidics to biomedicine and electronics. As we've traversed the intricacies of this subject, several critical elements stand out that underline its significance.
Summary of Key Points
- PDMS molds are crafted using sophisticated fabrication techniques such as soft lithography and photolithography, each boasting its own merits.
- Understanding the chemical and physical properties of PDMS is crucial for tailoring molds to specific applications, ensuring a high level of performance and fidelity.
- Despite its advantages, challenges like material limitations and post-fabrication concerns persist, necessitating innovative solutions.
- The future promises exciting advancements, with a movement towards integrating PDMS technologies with other systems, broadening its application scope.
Through this article, readers have gained insights into the myriad uses of PDMS molds, and how they have revolutionized sectors such as biotechnology and electronics.
Final Thoughts on PDMS Mold Fabrication
The take-home message surrounding PDMS mold fabrication is one of potential and ingenuity. As technology evolves, so too does the capacity to push the boundaries of what's achievable with PDMS.
This material is not just a simple silicone; it represents a powerful tool that invites exploration and experimentation.
In the ever-changing landscape of scientific research and industrial applications, the role of PDMS cannot be overstated. Its ability to adapt and evolve alongside burgeoning technologies ensures its relevance in future innovations. As we look ahead, there is every reason to believe that PDMS will continue to play a pivotal role in shaping the future of fabrication at the micro and nano levels.