Polycrystalline Diamond: An In-Depth Exploration
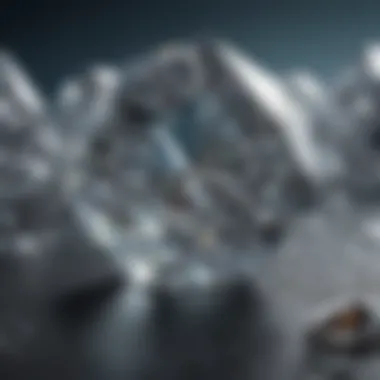

Intro
Polycrystalline diamond (PCD) represents a fascinating advancement in material science. This synthesized material exhibits remarkable attributes that make it a sought-after choice for various industrial applications. With the capabilities to outperform natural diamonds in specific contexts, it brings forth a blend of durability, thermal conductivity, and cutting precision that few materials can rival.
In recent years, the importance of PCD has surged. Its unique properties have opened doors in sectors ranging from cutting tools to the electronics industry. This article aims to delve deeper into the facets of PCD, illuminating its synthesis processes, physical characteristics, and the accompanying challenges, while also exploring its influence on future innovations.
The relevance of understanding PCD extends beyond its industrial implications. As industries evolve, the materials used must adapt to meet demanding specifications. PCD stands at the forefront, demonstrating how man-made solutions can address growing technological needs while also facing various hurdles in research and application.
Throughout this exploration, we will examine how PCD is both a product of advanced engineering and a pivotal element in driving forward new technological advancements. Thus, the forthcoming sections will offer insights into the research methodologies that underpin this material's development, as well as the larger implications of its usage in contemporary industries.
Prelude to Polycrystalline Diamond
Polycrystalline diamond (PCD) holds significant relevance in contemporary material science, as it embodies a remarkable blend of industrial utility and advanced technology. The advancements in the synthesis and application of polycrystalline diamond expand its usefulness in various sectors, including manufacturing, electronics, and healthcare. This introduction serves to highlight its importance, exploring essential benefits and considerations about PCD in a structured manner.
Definition and Overview
Polycrystalline diamond refers to a synthetic diamond material composed of numerous small diamond crystals. Unlike natural diamonds that form over millennia, PCD is produced through engineered processes that enhance its unique properties. One of the fundamental advantages of PCD is its high hardness, making it an optimal choice for cutting tools. Furthermore, PCD exhibits excellent thermal conductivity, offering significant advantages over conventional materials in applications that require heat dissipation.
The structure of polycrystalline diamond contributes to its mechanical strength. Its grainy composition gives PCD superior durability, making it suitable for demanding conditions. Additionally, the versatility of PCD allows for tailoring its properties for specific industrial usages, ranging from abrasives to innovative applications in electronics.
Historical Context
The journey of polycrystalline diamond technology began in the mid-20th century. Initial efforts at synthesizing diamond-like materials led to varied outcomes, but the breakthrough came with the development of high-pressure high-temperature (HPHT) techniques. These methods required immense pressure and elevated temperatures to transform carbon into diamond. This advance made possible the creation of synthetic diamonds with remarkable physical properties.
In the late 1970s, a notable shift occurred with the introduction of chemical vapor deposition (CVD) methods. These methods allowed for the growth of diamond films at lower pressures, paving the way for significant cost reductions in diamond production. As a result, PCD began to gain traction in various industrial applications, marking its rise as a practical alternative to both natural diamonds and other cutting materials.
In recent decades, ongoing research and innovations have broadened our understanding and application of PCD. This transformative material now plays an essential role not just in manufacturing but also in fields like electronics and biomedical technology, showcasing its invaluable contribution across varied industries.
Synthesis Processes of Polycrystalline Diamond
Understanding the synthesis processes of polycrystalline diamond is crucial for appreciating its role in modern material science. These methods define not only the quality and properties of PCD but also its applicability across industries. The synthesis techniques determine the material's mechanical, thermal, and electrical attributes, which make it suitable or unsuitable for specific applications. With advancements in technology, synthesizing polycrystalline diamond has become more efficient, allowing for wider use. Two of the most notable synthesis methods are High Pressure High Temperature (HPHT) and Chemical Vapor Deposition (CVD).
High Pressure High Temperature (HPHT)
High Pressure High Temperature is one of the oldest methods for synthesizing polycrystalline diamond. The HPHT method simulates the high-pressure and high-temperature conditions that natural diamonds undergo in the Earthโs crust. In this process, carbon sources such as graphite are subjected to extreme pressures (typically around 5 GPa) and temperatures (over 1500ยฐC). Under these conditions, carbon atoms rearrange into the diamond structure.
Key benefits of the HPHT method include:
- Cost-Effectiveness: HPHT continues to be a less expensive method compared to CVD for producing larger volumes of polycrystalline diamonds.
- Material Reliability: Diamonds produced via HPHT often exhibit better consistency in terms of structural integrity, making them ideal for cutting tools and abrasives.
However, the HPHT method has some limitations. The size of diamonds produced tends to be relatively small, which might not meet the demands of all applications. Furthermore, the process requires substantial energy, raising environmental concerns related to energy expenditure.
Chemical Vapor Deposition ()
Chemical Vapor Deposition involves the deposition of carbon atoms from gaseous precursors onto a substrate, forming polycrystalline diamond layer by layer. This technique allows for more control over the conditions, including temperature and pressure. Compared to HPHT, CVD provides the opportunity to create diamonds with specific characteristics tailored to various applications.
The advantages of the CVD method include:
- Uniformity and Quality: CVD can produce thin films of PCD with uniform thickness and without defects, which is particularly beneficial in electronics applications.
- Versatility: This method can produce diamonds of various shapes and sizes, enhancing its application in specialties like biomedical devices.
However, there are some drawbacks. The CVD process can be more time-consuming and complex, requiring careful monitoring and adjustment of numerous parameters throughout the growth cycle.
Comparison of Synthesis Methods
When analyzing HPHT and CVD methods, several factors emerge as key in choosing the appropriate synthesis technique:
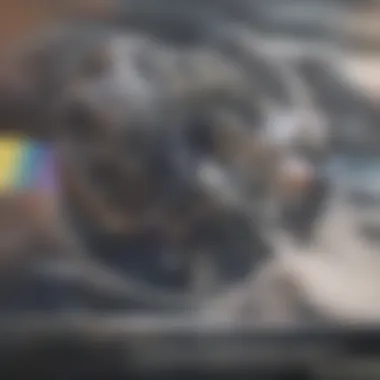

- Cost: HPHT is often the more economical choice for bulk production, while CVD can be more expensive due to prolonged production times and material costs.
- Quality of Material: CVD generally results in higher quality diamonds with fewer impurities, suitable for high-end applications, whereas HPHT diamonds are known for their durability.
- Production Scale: HPHT is more beneficial for large-scale production, whereas CVD allows for tailored solutions for specific small-batch production requirements.
"The choice between HPHT and CVD ultimately depends on the application requirements and cost considerations."
Physical Properties of Polycrystalline Diamond
Understanding the physical properties of polycrystalline diamond (PCD) is crucial. These characteristics dictate how PCD performs across various applications. The unique structure of polycrystalline diamond contributes to its outstanding qualities. Difference between PCD and single-crystal diamond is significant, impacting its usage.
One can classify the primary physical properties into three main areas: mechanical strength, thermal conductivity, and electrical conductivity. Each property has distinct implications for industrial applications.
Mechanical Strength
Mechanical strength is one of the most remarkable attributes of polycrystalline diamond. This material exhibits exceptional hardness, which is essential for its role in cutting tools and abrasives. The compressive strength of PCD can reach levels as high as 10-20 GPa, allowing it to withstand high stress without deformation.
The reason for this impressive strength lies in its microstructural configuration. PCD consists of numerous small diamond grains bonded together, forming a robust matrix. This feature not only enhances its hardness but also contributes to its wear resistance. Consequently, PCD is often selected in scenarios where durability is essential, such as in the manufacturing of drill bits and saw blades.
Further, the impact resistance of PCD makes it suitable for applications under extreme conditions. For instance, in oil and gas drilling, where tools face harsh environments, PCD tools last longer than conventional materials.
Thermal Conductivity
Polycrystalline diamond is also known for its high thermal conductivity. It can transfer heat more efficiently than copper or aluminum, which is highly advantageous in various sectors. In electronics, for example, effective heat dissipation is critical for maintaining performance and longevity. Using PCD in electronic components helps in managing thermal loads, mitigating risks of overheating.
The thermal conductivity of PCD typically ranges from 900 to 2200 W/mยทK. This unique property arises from the effective phonon transport in its crystalline structure. Here, the diamond's atomic arrangement promotes rapid heat transfer, providing superior cooling mechanisms in electronic devices.
Moreover, in industrial applications involving high-speed machining, the thermal properties of PCD help to prevent the overheating of tools. This fosters efficiency and prolongs tool life.
Electrical Conductivity
Electrical conductivity in polycrystalline diamond is an intriguing aspect. While diamond in its pure form is an excellent electrical insulator, PCD can exhibit varying degrees of conductivity depending on factors such as doping and temperature. The introduction of certain impurities can convert diamond into a semiconductor, opening avenues for its usage in advanced electronic applications.
The ability to adjust the electrical conductivity makes PCD attractive for devices like high-power transistors and sensors. They can function effectively in environments that necessitate robust electrical performance under extreme conditions. Additionally, this property aids in the development of new materials for energy-efficient technologies.
In summary, the physical properties of polycrystalline diamond play a pivotal role in its versatility and effectiveness in diverse industrial applications. Mechanical strength, thermal conductivity, and electrical conductivity are vital parameters that enhance PCD's suitability in cutting tools, electronics, and beyond.
Applications of Polycrystalline Diamond
Polycrystalline diamond (PCD) is increasingly recognized for its diverse applications across multiple industries. Its unique characteristics make it an essential material in various fields, enhancing both efficiency and performance. Understanding the range of applications showcases the significance of PCD in modern technology and manufacturing processes.
Cutting Tools and Abrasives
PCD is most commonly used in cutting tools and abrasives. Its remarkable hardness and wear resistance allow for significant improvements in cutting efficiency. Industries such as metalworking, construction, and mining benefit from PCD tools, which deliver superior performance compared to conventional materials.
- Durability: Tools made from PCD last much longer, reducing the need for frequent replacements.
- Precision: The ability to maintain sharp edges ensures high-quality finishes in machined products.
- Cost Efficiency: While the initial investment for PCD tools may be higher, the long-term savings from reduced tool wear and downtime are substantial.
PCD is utilized in various forms, including inserts, milling tools, and drill bits. The versatility of these tools allows for applications in a wide range of materials, from composites to hard metals. This adaptability further cements PCD's position in cutting technology.
Electronics and Semiconductors
In the realm of electronics, PCD's properties extend beyond traditional applications. Its excellent thermal conductivity makes it a candidate for heat sinks and other thermal management systems.
- Heat Dissipation: PCD effectively transfers heat away from sensitive electronic components, enhancing reliability and performance.
- Electrical Insulation: Although primarily a good conductor of heat, PCD can also be engineered to provide electrical insulation, adding to its utility in electronic designs.
Moreover, PCD finds relevance in semiconductor technology. It is increasingly used in the fabrication of high-performance devices. The purity and structure of synthetic diamond materials provide a platform for advanced semiconductor applications.
Biomedical Applications
PCD's biocompatibility opens doors to innovative biomedical applications. This material finds use in surgical tools, implants, and dental applications due to its durability and inert nature.
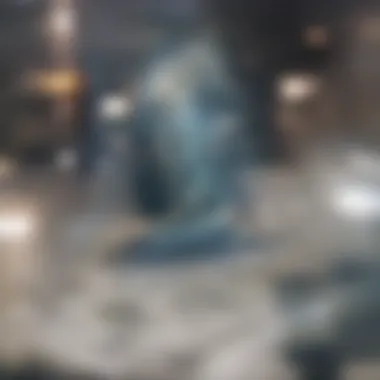

- Surgical Instruments: The hardness of PCD tools allows for precision cutting in surgeries, leading to better outcomes. They offer longer service life compared to standard steel instruments.
- Dental Applications: In dentistry, PCD is used for drills and burs. Its properties ensure minimal wear and high performance during dental procedures.
The unique qualities of PCD also contribute to its potential in future medical technologies, such as prosthetics and implants. The ability to tailor these materials allows engineers to meet specific healthcare needs effectively.
In summary, polycrystalline diamond's applications are vast and varied, spanning from cutting tools to advanced electronics and biomedical devices. Its unique properties not only enhance performance but also open avenues for future innovations, illustrating the essentiality of PCD in contemporary industrial practices.
Advantages of Polycrystalline Diamond
Polycrystalline diamond (PCD) is recognized for its significant advantages in various industries. It combines superior physical properties with versatile applications and cost-effectiveness, making it an essential material in todayโs technological landscape. This section explores the critical elements that contribute to the growing importance of PCD.
Superior Durability
PCD exhibits remarkable durability. One of its most outstanding characteristics is its hardness. Unlike natural diamonds, which can be fragile, polycrystalline diamonds offer increased toughness due to their unique structure. This hardness allows PCD to withstand high wear and tear. In applications such as cutting tools, this translates to longer tool life and reduced downtime.
Additionally, PCD is resistant to thermal degradation and can function in high-temperature environments. This durability makes it advantageous for industries like mining and oil drilling, where conditions are harsh. The longevity of PCD products leads to less frequent replacements, resulting in lower overall costs for companies.
Versatile Applications
The versatility of polycrystalline diamond is evident in its wide range of applications. Its unique properties make it suitable for use in cutting tools, abrasives, and even electronic components. The material is utilized in the manufacture of drill bits, saws, and grinding wheels.
Moreover, PCD is becoming increasingly popular in electronics, where its thermal conductivity is beneficial for managing heat in semiconductor devices. In the biomedical field, researchers are exploring its use for implants and surgical tools due to its biocompatibility and durability. This adaptability ensures that PCD remains relevant across various sectors, encouraging ongoing research and development.
Cost-Effectiveness in Mass Production
When considering mass production, polycrystalline diamond proves to be cost-effective. The technologies for synthesizing PCD, such as Chemical Vapor Deposition, have advanced significantly, leading to reduced production costs. This has made PCD more accessible to manufacturers looking for high-performance materials.
Substantial cost savings come from the reduced frequency of tool replacement and maintenance as a result of PCDโs durability. Companies in different industries can benefit from investing in PCD, as long-term operational savings often outweigh the initial investment. With continued advancements in production techniques, the cost of polycrystalline diamond is likely to decrease further, expanding its use in various applications even more.
"Polycrystalline diamond is redefining the standards of performance in many industrial applications, reflecting a significant shift towards more robust materials."
In summary, the advantages of polycrystalline diamond cannot be overstated. Its superior durability, versatility across applications, and cost-effectiveness position it as a leading material in modern engineering and production sectors.
Challenges and Limitations
Understanding the limitations and challenges faced by polycrystalline diamond (PCD) technology is crucial for both current actors in the industry and those entering the field. While PCD offers significant advantages, its production and application are not without hurdles that could impact its broader adoption. This section discusses key challenges such as production complexity, material consistency issues, and market competition, illuminating the complexities involved in the utilization of this advanced material.
Production Complexity
The synthesis of polycrystalline diamond involves intricate processes. High Pressure High Temperature (HPHT) and Chemical Vapor Deposition (CVD) are the principal methods of creating PCD. Both techniques require precise control of conditions such as temperature, pressure, and chemical composition.
- HPHT Method: This approach emulates the natural formation of diamonds, using extreme conditions that can be technically demanding.
- CVD Method: This method, while more controllable, necessitates a careful selection of gases and involves a long growth period.
These complexities can lead to expensive production costs and technical difficulties. Additionally, managing the environmental conditions safely is critical. Therefore, continuous innovation in synthesis methods is essential for enhancing yield and efficiency.
Material Consistency Issues
Another significant challenge lies in the consistency of the material produced. Variations in the synthesis processes can result in different properties of the final product, which may affect its performance in practical applications.
- Impurity Levels: The presence of impurities can alter the electrical and thermal conductivity of PCD. Controlling these impurities is vital for maintaining quality and reliability.
- Structural Variability: The diamond grains formed during the synthesis might vary in size and quality, resulting in uneven performance across batches.
These inconsistencies can deter potential users from fully integrating PCD into their applications, as reliable performance is paramount in industries like aerospace and electronics.
Market Competition
The market for cutting-edge materials, including polycrystalline diamond, is incredibly competitive. With multiple materials available for similar applications, PCD faces challenges in proving its worth. Companies are often drawn to alternatives like carbide or ceramic materials that may have lower upfront costs.
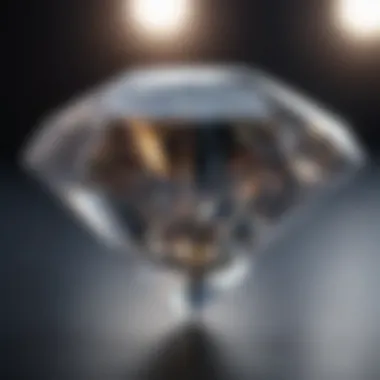

- Pricing Strategies: The high production costs associated with PCD can make it less attractive compared to other materials.
- Innovation and R&D: Competing materials also attract heavy investment in research and development, thus continuously eroding PCD's market position.
For PCD to remain relevant, stakeholders must focus on demonstrating its unique advantages and driving down production costs through technological improvements.
"The true potential of polycrystalline diamond can be unlocked by addressing its challenges through sustained innovation and strategic market positioning."
This section has covered some of the key challenges and limitations faced by polycrystalline diamond technology and its applications. Recognizing these factors allows stakeholders to develop strategies to navigate the landscape more effectively, ensuring that the benefits of PCD can be fully realized.
Recent Innovations in Polycrystalline Diamond Technology
Recent innovations in polycrystalline diamond (PCD) technology are transforming both the manufacturing process and the applications of this versatile material. The advancements in this field not only enhance the material's inherent properties but also open doors to new areas of utilization. As industry demands evolve, PCD continues to adapt, proving its value in diverse sectors. Understanding these innovations is essential for students, researchers, educators, and professionals who aim to keep pace with developments in this area.
Advancements in Synthesis Techniques
The synthesis of polycrystalline diamond has seen noteworthy innovations in recent years. Both High Pressure High Temperature (HPHT) and Chemical Vapor Deposition (CVD) methods have received significant upgrades.
- HPHT: Developments in HPHT synthesis have focused on refining the conditions under which high-quality PCD is produced. Improvements in equipment durability and operational control have led to enhanced crystal growth rates and reduced impurity levels. This resulted in stronger and more consistent diamond materials.
- CVD: The CVD method has seen advancements such as the implementation of microwave plasma techniques. These improvements permit a greater control over the deposition process, enabling the creation of PCD with specific properties tailored for particular applications. Moreover, researchers are exploring novel precursor gases that further enhance the efficiency of the synthesis process.
These advances in synthesis techniques not only improve the quality of polycrystalline diamonds but also contribute to cost-effectiveness in mass production, making PCD more accessible for various industrial uses.
Emerging Applications in New Fields
Alongside advancements in synthesis, polycrystalline diamond is finding applications in fields that previously did not involve this material. The versatility of PCD makes it suitable for numerous industries:
- Quantum Computing: Recent developments have led to the use of PCD in quantum computing research. Its exceptional thermal properties and ability to host quantum bits (qubits) make it a candidate for improving computational performance and efficiency.
- Medical Technology: In the biomedical field, PCD is being investigated for use in advanced imaging techniques and as a coating material for surgical tools. Its biocompatibility and hardness are beneficial in enhancing the performance and durability of medical instruments.
- Optoelectronics: Innovations in optoelectronic applications are also notable. PCD is being explored for use in devices that require efficient thermal management and high-density integration, offering potential improvements in performance and reliability.
These emerging applications are a testament to the adaptability of polycrystalline diamond technology. As research continues, the role of PCD is expected to expand further, addressing new challenges and needs in various industries.
Polycrystalline diamond proves itself not just as a material for cutting tools but as a significant player in technological advancements across various fields.
Future Directions in Polycrystalline Diamond Research
The realm of polycrystalline diamond (PCD) research is vibrant and evolving. This section will focus on the future directions that this field may take. Sustainability and integration with emerging technologies are key considerations for researchers, industries, and consumers alike. Addressing these points is crucial as society is increasingly demanding innovative and environmentally friendly solutions.
Sustainability and Environmental Impact
Sustainability plays a significant role in the future of polycrystalline diamond research. As industries aim for reduced environmental footprints, the creation and utilization of PCD materials must reflect these goals. Here are some key areas to consider:
- Resource Efficiency: The synthesis processes of PCD need continual refinement to ensure that they use fewer resources, both in terms of raw materials and energy consumption. HPHT and CVD methods should be optimized for better yield and lower costs.
- Recyclability and Lifecycle Assessments: Future work should also focus on the lifecycle of PCD products. Developing methods for recycling PCD can significantly minimize waste and environmental impact. Lifespan assessments can help determine the best practices for reusing or discarding PCD materials.
- Material Alternatives: Researchers might explore sustainable alternatives to conventional materials used in PCD production. This could include sourcing materials from renewable resources or utilizing waste by-products from other industries.
"The pursuit of sustainability in polycrystalline diamond technology is not merely a trend but a necessity. Our future depends on how we innovate responsibly."
Integration with Emerging Technologies
The integration of PCD with emerging technologies can create significant advancements in various fields. Here are some examples of this potential:
- Nanotechnology: The combination of PCD with nanotechnology could lead to innovative applications in electronics. For instance, embedding PCD within nanostructures could enhance the thermal and electrical properties of devices, resulting in increased efficiency.
- Artificial Intelligence: The utilization of AI in optimizing the synthesis of PCD materials can result in better quality diamonds with less trial and error. AI can also assist in predicting material performance in specific applications, boosting research and development.
- Biotechnology: As biomedical applications of PCD grow, integrating PCD materials with biological systems or structures can enhance biocompatibility. This could lead to improved devices for drug delivery or tissue engineering.
These emerging integrations promise to expand the impact and versatility of polycrystalline diamond. As researchers navigate these future directions, it is crucial to remain mindful of the associated implications, benefits, and challenges.
Epilogue
The conclusion section of this article presents a synthesis of the information discussed throughout. It highlights the multifaceted significance of polycrystalline diamond (PCD) in various industries. PCD shows distinctive traits that make it a preferred material in applications that require strength, precision, and durability.
Summary of Key Points
- Definition and Overview: PCD is a synthesized material that combines the superior attributes of diamond with versatility for industrial purposes.
- Synthesis Processes: Various methods, such as High Pressure High Temperature (HPHT) and Chemical Vapor Deposition (CVD), have been developed to create PCD, enhancing its availability and quality.
- Physical Properties: Notable properties include exceptional mechanical strength, high thermal conductivity, and varying electrical conductivity that cater to diverse applications.
- Applications: The use of PCD spans cutting tools, electronics, and biomedical fields, emphasizing its adaptability and effectiveness.
- Advantages: PCD offers superior durability, versatile applications, and cost efficiencies that are beneficial for mass production.
- Challenges: Despite its benefits, there are complexities in production, material consistency issues, and significant market competition.
- Recent Innovations: New advancements in synthesis and innovative applications are paving the way for the future of PCD.
- Future Directions: Research is increasingly focusing on sustainability and integration with emerging technologies, which can further influence the development and usage of PCD.
Final Thoughts
The exploration of polycrystalline diamond highlights not only the current applications but also future potential. As industries evolve and seek materials that can meet the demands of modern engineering and technology, PCD stands out as a material with significant promise. Continued research into its properties and applications could drive further innovations. Thus, understanding the importance of PCD is crucial for students, researchers, educators, and professionals engaged in material sciences. By appreciating its unique characteristics, they can better appreciate the impact of PCD in contemporary practices and future developments in the field.
"Polycrystalline diamond represents a fusion of science and practical application, creating a bridge for advancements across multiple sectors."