Exploring Reactive Injection Molding: Mechanisms and Uses
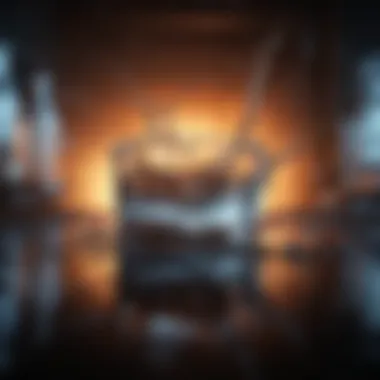
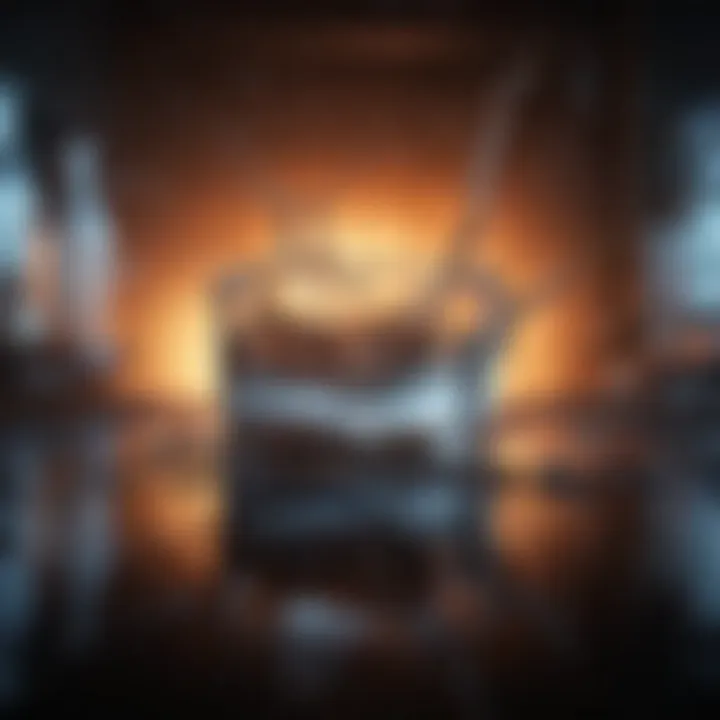
Intro
Reactive injection molding (RIM) stands as a noteworthy advancement in manufacturing, seamlessly integrating chemical reactions with traditional injection molding. This melding of processes enhances the ability to create sophisticated polymer structures that cater to various industrial needs. As the demand for high-performance materials increases, understanding the intricacies of RIM becomes crucial.
The article will delve into the mechanisms underpinning reactive injection molding, elucidating its fundamental principles, material choices, and far-reaching applications across different sectors. Further, it will provide a comprehensive analysis of the increasing innovations in RIM technology, emphasizing the significance of optimized process parameters and reaction kinetics. By exploring environmental sustainability and future trends, we aim to present a holistic view of RIM's role in contemporary manufacturing.
Research Methodology
Description of Research Design and Approach
The research on reactive injection molding utilizes a multi-faceted approach that blends theoretical analysis with empirical studies. The design encompasses both experimental setups and simulation models. These methodologies facilitate an in-depth examination of reaction kinetics and material properties in RIM processes. Data collection is performed through systematic experimentation, allowing for the collection of quantitative insights on product performance.
Materials and Methods Used in the Study
The materials utilized in reactive injection molding typically include thermosetting resins such as polyurethane and epoxy. The selection of these materials is critical, as their properties dictate the efficiency and effectiveness of the RIM process.
The methods employed in this study involve:
- Material Characterization: Involves assessing the mechanical and thermal properties of the raw materials to ensure compatibility with RIM.
- Process Optimization: Focuses on adjusting parameters such as temperature, pressure, and injection speed. Such adjustments aim to enhance the reactivity and mold filling behavior.
- Empirical Testing: Products are manufactured using standardized molds to analyze performance metrics like strength and durability.
Discussion and Interpretation
Interpretation of Results in the Context of Existing Literature
Results from recent studies have shown that enhancements in reaction kinetics directly correlate with improved production efficiencies. This parallels findings in literature that emphasize the importance of precise control over chemical reactions.
Implications for Future Research or Practical Applications
The implications of these findings are profound. Future research may focus on developing new, sustainable materials for RIM that reduce environmental impact. Additionally, practical applications of RIM continue to expand into sectors such as automotive, aerospace, and consumer electronics. The adaptability and efficiency of RIM positions it as a pivotal manufacturing strategy moving forward.
"Reactive injection molding is not just a process; it represents a paradigm shift in how complex polymer structures are engineered."
By unraveling the mechanisms and applications associated with reactive injection molding, we pave the way for innovations that could redefine manufacturing standards.
Prelude to Reactive Injection Molding
Reactive injection molding, often abbreviated as RIM, represents a sophisticated intersection of conventional injection molding and chemical reactions. This method unfolds a realm of possibilities that go beyond traditional techniques, enhancing the capabilities of manufacturing in various industrial sectors. Understanding RIM is crucial for grasping modern advancements in polymer science and technology.
RIM is particularly significant due to its ability to create complex polymer structures with tailored properties. Manufacturers can develop products that are not only strong and durable but also lightweight and versatile. This becomes increasingly important in industries like automotive and electronics, where the demand for high-performance materials is ever-growing.
In addition to performance benefits, reactive injection molding presents substantial cost advantages. By streamlining production processes and minimizing waste, RIM allows companies to enhance efficiency while reducing material consumption. Such economic factors cannot be overlooked, especially as manufacturers strive to remain competitive in a rapidly evolving market.
Moreover, the innovations in RIM technology continue to foster advancements in material science. The development of new polymeric resins, additives, and catalysts reflects the ongoing evolution within the field. Understanding these developments provides insight into the future of manufacturing processes and materials.
In essence, the exploration of reactive injection molding is not merely an academic exercise; it is a vital discourse for students, researchers, and professionals alike. As industries pivot towards sustainable and efficient production methods, RIM stands at the forefront of this transformation, underscoring the importance of continuous learning in the field of advanced polymer manufacturing.
Definition and Overview
Reactive injection molding is a process that combines the principles of traditional injection molding with the chemical reactions of synthetic materials. During the RIM process, reactive resins are injected into a mold where they undergo polymerization. This reaction occurs within the confines of the mold, allowing for the formation of solid structures that have specific desired properties. RIM allows for great versatility in the types of products that can be produced, including composites, elastomers, and other complex materials.
The primary components in RIM involve two or more liquid components that react chemically. Upon mixing, a catalyst initiates the reaction, leading to a rapid curing of the material. This feature enables faster production rates and more effective use of the materials involved.
RIM is advantageous in applications where complex geometries and high-performance qualities are required. It can be used to produce parts that necessitate superior strength, durability, or elasticity. These factors underscore the significance of RIM in fields such as automotive, aerospace, and consumer electronics.
History and Evolution
The roots of reactive injection molding date back to the 1970s, during which the demand for materials that could meet higher-performance demands surged. Early adopters of RIM technology recognized its potential to produce strong, lightweight components that could withstand rigorous conditions.
As research progressed, the understanding of the kinetics involved in reaction processes improved. This led to enhanced control over material properties and the ability to tailor products for specific applications. The integration of advanced material science, particularly in polymer chemistry, significantly contributed to the evolution of RIM technology.
The 1990s saw a significant increase in the adoption of RIM in the automotive industry, driven by stringent regulations on weight and fuel efficiency. Manufacturers began investing in RIM technology to create intricate parts like body panels and other structural components.
Today, RIM continues to evolve. Advancements in automation and computer-aided processes are streamlining production, while innovations in materials research allow for the development of new resins with improved characteristics. As these trends continue, the future of reactive injection molding appears promising, with ongoing research dedicated to further enhancing this vital production technique.
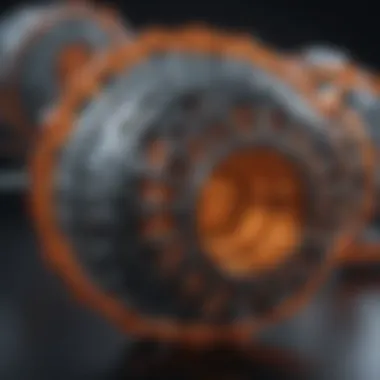
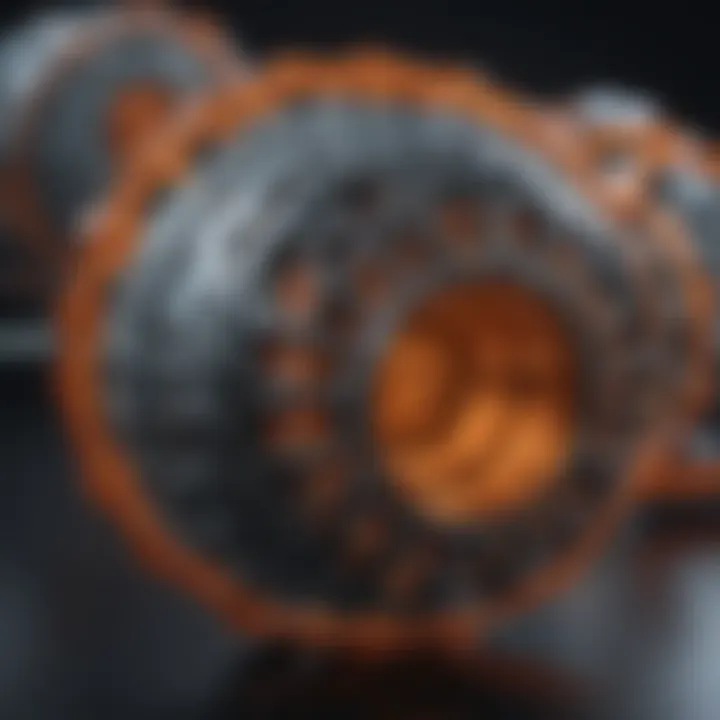
Mechanics of Reactive Injection Molding
Understanding the mechanics of reactive injection molding (RIM) is critical in grasping how this technology revolutionizes traditional manufacturing approaches. RIM’s ability to merge chemical properties with the physical process of injection molding leads to advancements in producing performance-oriented polymer structures. Focusing on mechanics allows for a more comprehensive dive into the operational principles, crucial reactions involved, and the kinetics that govern the overall process.
Basic Principles of Injection Molding
Injection molding is a well-established technique known for its efficiency in manufacturing complex shapes. The basic principles of injection molding include heating thermoplastic or thermosetting materials until they reach a molten state, followed by injecting this material into a mold under pressure. As the material cools and solidifies, it adopts the shape of the mold. In reactive injection molding, this method is enhanced through the addition of chemical reactions occurring simultaneously during the injection process. This fusion allows for a unique transformation of the material properties, leading to enhanced performance.
One notable aspect of RIM is that it often utilizes two-component systems, where a resin and a hardening agent are mixed. This reaction changes the viscosity of the material, impacting flow characteristics and how easily it fills the mold. Common techniques include:
- High-pressure injection for precision filling.
- Low-pressure injection to accommodate more complex molds requiring more delicate handling.
Additionally, maintaining the correct temperature and timing during the injection is crucial for achieving optimal material properties.
Chemical Reactions in RIM
The core of reactive injection molding lies in the chemical reactions that take place as the resin is injected into the mold. These reactions can include polymerization, cross-linking, or curing. The resulting material often exhibits superior cohesion, integrity, and thermal stability compared to non-reactive processes.
For instance, polyurethane-based systems are common in RIM processes because they enable rapid curing times and significant customization in hardness and flexibility. Understanding the specific chemistry allows engineers to tailor the final product for specific applications, thereby enhancing functionality. Common reactions include:
- Addition reactions where monomers bond together.
- Condensation reactions that also produce byproducts which may affect curing time.
Each chemical reaction type presents its own set of advantages and challenges that must be understood for successful application in manufacturing.
Kinetics of Reaction Processes
Kinetics plays a pivotal role in optimizing reactive injection molding processes. It focuses on the rates of chemical reactions, helping to determine how quickly a material can be manipulated and formed into a final product. For RIM, critical kinetic parameters include:
- Reaction time: The time it takes for a material to cure properly influences production timelines.
- Temperature: Higher temperatures can accelerate reactions but may lead to unwanted degradation.
- Concentration of reactants: The proportions of resin and hardener can impact both the speed and quality of the reaction.
Understanding these kinetic factors assists manufacturers in designing processes that enhance throughput while maintaining product quality.
"A thorough grasp of reactive kinetics is crucial for optimizing both quality and efficiency in RIM."
Materials Used in Reactive Injection Molding
The materials utilized in reactive injection molding are fundamental to the success and versatility of this technique. Understanding these materials allows for enhanced performance, improved product attributes, and greater design options. Moreover, it is essential to grasp how these materials interact with one another during the reactive process, which can significantly influence both the quality of the finished product and the efficiency of the manufacturing process.
Types of Polymeric Resins
Polymeric resins are the backbone of reactive injection molding. The choice of resin affects not only the physical characteristics of the final product but also how the molding process is executed.
Common types of polymeric resins include:
- Polyurethane (PU): PU resins are particularly valued for their flexibility and durability. These materials are known for their excellent mechanical properties and can be tailored for specific applications.
- Epoxy Resins: Renowned for their strong adhesive properties and thermal stability, epoxy resins provide an excellent solution for applications demanding high strength and resistance to temperature.
- Polyamide (Nylon): These resins offer great resistance to wear and tear, making them ideal for applications in automotive and industrial components.
- Polyethylene (PE): With its excellent chemical resistance and low-density properties, PE is commonly used in a wide range of consumer applications.
Each type of resin brings unique benefits. For instance, PU's adaptability allows it to be compounded with other additives to achieve desired characteristics like improved flame resistance or increased tensile strength.
Additives and Catalysts
Additives and catalysts play a critical role in enhancing the properties of the resins used in reactive injection molding. These materials are utilized to modify and optimize the performance of final products.
Common additives used include:
- Plasticizers: These improve the flexibility of the resin, enabling easier processing and better performance in applications where flexibility is crucial.
- Fillers: Often used to reduce costs, fillers can also enhance properties like thermal conductivity or dimensional stability.
- Stabilizers: They help in maintaining the performance of the resin when exposed to environmental factors, such as UV light or high temperatures.
Catalysts are equally important in controlling the speed and effectiveness of the chemical reactions during molding. They ensure that the desired physical properties are attained within the required time frame. Effective use of catalysts can lead to:
- Faster curing times, increasing productivity.
- Improved molecular structure, resulting in enhanced mechanical attributes.
Overall, the careful selection and application of materials and additives are paramount in achieving optimal results in reactive injection molding. The right combination not only contributes to product performance but also ensures efficient manufacturing processes, making it a vital consideration for professionals in the field.
Advantages of Reactive Injection Molding
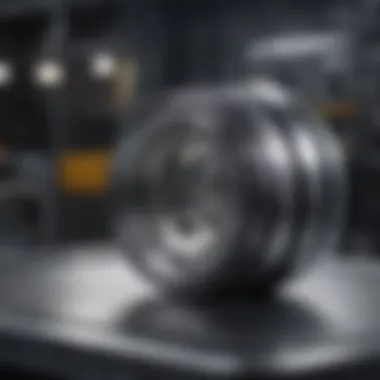
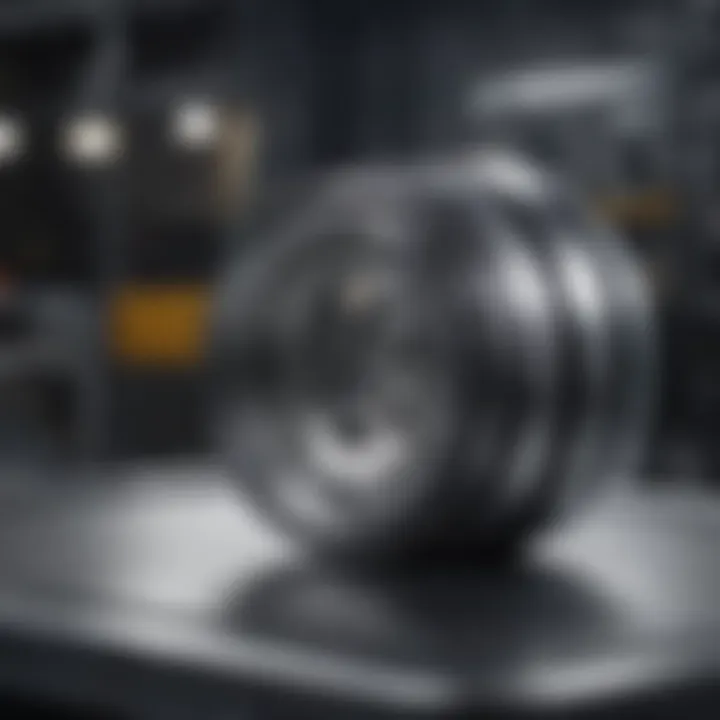
Reactive Injection Molding (RIM) offers substantial benefits that enhance manufacturing processes across various industries. Understanding these advantages is crucial for embracing the full potential of RIM technology. The following sections highlight specific elements such as cost efficiency, design flexibility, and enhanced material properties that underline the importance of RIM in modern manufacturing.
Cost Efficiency
One of the primary advantages of Reactive Injection Molding is its cost efficiency. The process combines the use of chemical reactions with injection molding, reducing the need for multiple manufacturing steps. This integration allows companies to minimize labor costs while also shortening production times. By eliminating secondary processes such as surface finishing and assembly, manufacturers can achieve significant savings. Furthermore, RIM typically supports the use of less material waste compared to traditional methods. As a result, lower costs often lead to competitive pricing for products in the marketplace, encouraging wider usage in the industry.
Design Flexibility
Reactive Injection Molding also stands out for its design flexibility. The nature of RIM allows manufacturers to create complex shapes and geometries that might be difficult or impossible to achieve with conventional injection molding. This flexibility opens new avenues for product innovation. Designers can explore unique attributes, including intricate surface details and optimized structures, without worrying about manufacturing limitations. The capacity to combine different materials and additives in one process supports the customization of products, meeting diverse requirements from various sectors. In addition, the ability to design lightweight components without sacrificing durability is increasingly valuable in industries like automotive and aerospace.
Enhanced Material Properties
Another significant benefit of RIM is the enhancement of material properties. The chemical reactions that occur during the molding process can lead to improved mechanical, thermal, and chemical resistance characteristics. This aspect can elevate the performance of components produced through RIM. For instance, the use of specialized resins and additives can result in materials that withstand higher temperatures or exhibit increased tensile strength. Additionally, RIM enables enhanced adhesion between layers, crucial for multi-material applications. As a result, products manufactured through RIM often have superior qualities that can lead to increased product longevity and reliability, addressing the demands of modern consumers.
"The effectiveness of Reactive Injection Molding is not just in its application, but in the way it reshapes the manufacturing capabilities of various industries."
In summary, the advantages of Reactive Injection Molding are being recognized by students, researchers, educators, and professionals alike. Understanding and leveraging these benefits can provide a competitive edge in manufacturing.
Challenges in Reactive Injection Molding
Reactive Injection Molding (RIM) presents unique challenges that must be addressed for effective production. Understanding these challenges is essential for achieving optimal results in various applications. Key elements include process control and material compatibility, two vital factors influencing the overall efficiency and effectiveness of RIM.
Controlling the RIM process involves maintaining precise conditions that affect both the physical and chemical aspects of production. Manufacturers face hurdles in optimizing these conditions, as small variations can lead to significant alterations in the final product. Hence, technological innovations and detailed monitoring systems are vital to overcome these difficulties.
Process Control and Optimization
One critical aspect of RIM is process control. Manufacturers must continuously monitor the reaction conditions throughout the RIM process. Factors such as temperature, pressure, and the rate of material injection significantly influence the characteristics of the final product.
The optimization of these parameters requires advanced methods, such as:
- Real-time monitoring of reaction kinetics,
- Implementation of automated systems,
- Use of predictive modeling techniques.
Real-time monitoring helps in adjusting process parameters dynamically. Automated systems decrease human error and improve speed. Predictive modeling assists in identifying potential issues before they occur, ensuring consistency and quality of output.
"Effective process control in RIM minimizes waste and maximizes product integrity."
However, achieving this level of control demands substantial investment in technology and training, which can pose a challenge for smaller manufacturers. Therefore, striking a balance between cost and efficiency is crucial.
Material Compatibility Issues
Material compatibility is another major challenge in RIM. The process involves multiple components that must interact correctly to yield the desired properties. Incompatibility can lead to unsuccessful reactions or inferior product quality.
Factors influencing material compatibility include:
- Chemical composition of the resins and additives,
- The presence of contaminants,
- Environmental conditions.
To address these issues, manufacturers must conduct thorough compatibility testing before full-scale production. Using additives that enhance adhesion and reduce the risk of delamination is also critical.
Finding the right materials that work together seamlessly is essential for ensuring reliability and performance. Selecting the appropriate resin system is not always straightforward, which can complicate the development processes. To mitigate risks, collaboration with material scientists is encouraged to leverage their expertise in formulating compatible systems.
Applications of Reactive Injection Molding
The relevance of Reactive Injection Molding (RIM) in modern manufacturing cannot be understated. Its applications span various industries, reflecting its versatility and the distinct advantages it brings to production processes. As RIM technology evolves, manufacturers continuously discover new ways to optimize their products through advanced material properties and innovative design capabilities. This section highlights the importance of RIM applications, focusing on the automotive, electronics, and consumer goods sectors. Through this exploration, we can appreciate the transformative potential of RIM in creating complex structures that meet specific industry needs.
Automotive Industry
The automotive industry stands as a primary beneficiary of Reactive Injection Molding. Here, RIM facilitates the production of lightweight and durable components that are essential for modern vehicles. Such components include bumpers, interior panels, and casings for electronics, which require both strength and aesthetic appeal. The efficiency of RIM allows for rapid prototyping and production, enabling manufacturers to respond quickly to market demands.
Moreover, RIM supports intricate designs that traditional molding processes may struggle to achieve. Complex geometries and integrated functionalities lead to reduced assembly times and overall costs. The process's inherent capability for material versatility means that manufacturers can explore composites that enhance performance, such as improved energy absorption and impact resistance, which are crucial for vehicle safety.
Electronics and Electrical Components
In the field of electronics, RIM offers significant advantages for producing enclosures and protective casings. Devices in consumer electronics, telecommunications, and industrial applications often require robust yet lightweight materials while maintaining precise tolerances.
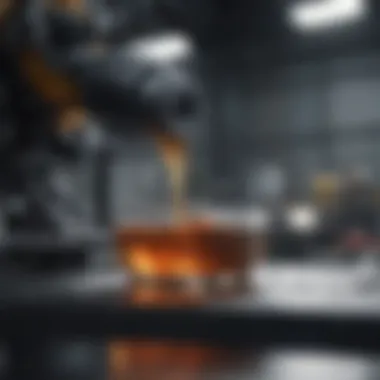
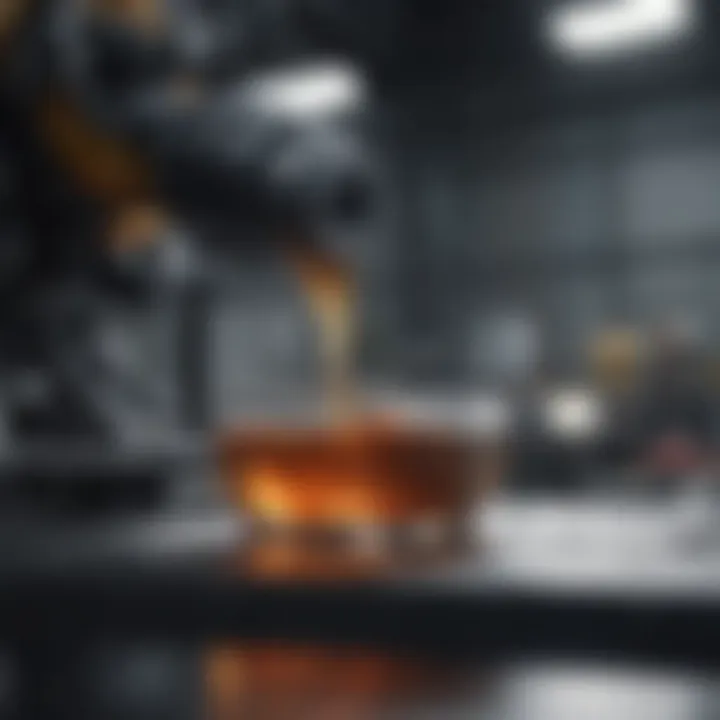
Reactive Injection Molding enables manufacturers to create components that are not only structurally sound but also environmentally friendly. The use of eco-friendly resins and additives aligns with a growing consumer preference for sustainable products. Additionally, the ability to incorporate various functionalities into single components—such as electromagnetic shielding or heat resistance—translates into enhanced product performance and energy efficiency.
Furthermore, the rapid pace of technological advancement in electronics demands a quick turnaround in component design and production. RIM's efficiency in scaling production meets this requirement, allowing for continuous innovation while keeping costs manageable.
Consumer Goods Manufacturing
The consumer goods sector also reaps the benefits of RIM, particularly in producing items that require both functionality and visual appeal. Products such as packaging, kitchen utensils, and household appliances often involve complex designs that can be efficiently manufactured using RIM processes. The flexibility offered by RIM allows for customization that meets specific consumer preferences.
In addition, the integration of sustainable practices in this sector highlights the importance of RIM. Manufacturers are seeking ways to reduce waste and optimize material use, which aligns with the principles of RIM. This means less energy consumption during production and minimized leftover materials.
"The versatility of Reactive Injection Molding allows for the development of products that are not only innovative but also responsive to the evolving market dynamics."
Environmental Considerations in RIM
Environmental considerations in Reactive Injection Molding (RIM) are increasingly crucial as industries strive for sustainable production methods. The intricate nature of RIM not only involves the synthesis and application of materials, but it also raises imperative questions about environmental impact. The growing awareness surrounding climate change and resource conservation drives the need for improved sustainability practices in manufacturing processes.
The importance of integrating environmental implications into RIM cannot be overlooked. As the demand for complex, high-performance polymer products rises, manufacturers face the responsibility of ensuring their processes align with sustainable development goals. Environmental considerations evoke crucial aspects such as resource depletion, emissions, and the lifecycle of products. RIM offers opportunities for resource efficiency, enabling firms to minimize waste while maximizing output quality.
Sustainability Practices
Sustainability practices in RIM focus on reducing the ecological footprint of production. This can be managed through:
- Material Selection: Choosing renewable or bio-based polymer resins enhances the sustainability of RIM. By utilizing materials derived from sustainable sources, emissions during the product lifecycle can be significantly reduced.
- Process Efficiency: Optimizing the RIM process can lead to decreased energy consumption. Implementing energy-efficient machinery and improving process timing can lead to significant reductions in energy usage.
- Lifecycle Assessment: Conducting assessments to evaluate the environmental impacts associated with the production, use, and disposal of RIM products ensures comprehensive understanding. This assessment helps manufacturers implement more sustainable practices based on empirical data.
These practices collectively contribute to a greener manufacturing process, focusing explicitly on reducing environmental impacts while maintaining the benefits of RIM technology.
Recycling and Waste Management
Recycling and waste management are essential components of sustainability in RIM. As with any manufacturing process, waste generation is an unavoidable reality. However, RIM allows for innovative recycling processes to mitigate these impacts further.
- Material Recovery: Efforts to recover scrap material from the RIM process can minimize waste. By recycling off-spec products and eliminating extraneous materials, manufacturers not only stem waste but also optimize resource use.
- Closed-Loop Systems: Implementing closed-loop systems in RIM enables manufacturers to reintegrate recycled materials into the production cycle. This practice not only reduces the environmental burden but also streamlines material consumption.
"The potential for recycling in RIM illustrates a paradigm shift in the approach toward sustainable manufacturing, enabling closer alignment with environmental objectives."
- End-of-Life Management: Establishing strategies for effective disposal or recycling of RIM products at the end of their lifespan is critical. Encouraging responsible product disposal practices can contribute to a circular economy where materials are continually reused and emissions minimized.
Future Trends in Reactive Injection Molding Technology
Future trends in Reactive Injection Molding (RIM) technology are crucial for understanding how the industry will evolve. Adapting to these trends can lead to improved manufacturing methodologies, enhanced material properties, and reduced environmental impact. Companies that align themselves with these advancements can benefit significantly, gaining competitive advantage in market.
Advancements in Materials Science
Materials science is at the core of RIM evolution. Recent advancements focus on developing new polymer blends and composites. These materials can enhance properties such as durability, thermal stability, and chemical resistance. One notable progress is the development of bio-based polymers. These alternatives not only reduce reliance on fossil fuels, but also offer similar strength and performance characteristics to traditional materials.
In addition, nanomaterials are also gaining attention. Incorporating nanoparticles into resins can dramatically improve their mechanical and thermal properties. The ability to fine-tune these characteristics allows for more specialized applications. Hence, the choice of materials is expanding, leading to greater design flexibility.
Integration of Automation and AI
Automation and artificial intelligence (AI) are reshaping many manufacturing processes, including RIM. AI can optimize the entire production cycle, analyzing vast amounts of data to predict outcomes, reduce waste, and enhance efficiency. For instance, machine learning algorithms can predict the ideal conditions for specific reactions.
Moreover, integrating robotic systems into RIM can improve precision and speed in the injection process. Automation reduces human errors and enables consistent quality. By leveraging these technologies, companies can meet growing demand for higher quality products while minimizing operational costs.
"The integration of AI and automation not only speeds up production but also enhances quality control, allowing for a more efficient manufacturing process."
Overall, the future of Reactive Injection Molding is promising. Both advancements in materials science and the adoption of automation and AI contribute to a more efficient, customizable, and sustainable manufacturing environment. Stakeholders in the field must remain vigilant and adaptable to these trends to maintain relevance and drive innovation.
Ending
The significance of concluding an article on Reactive Injection Molding (RIM) cannot be understated. This section encapsulates the critical insights gathered throughout the discussion, solidifying the core principles and practical implications of RIM. Moreover, it emphasizes the importance of understanding these mechanisms, as they directly influence design and manufacturing effectiveness.
Summary of Key Points
Reactive Injection Molding presents a unique fusion of traditional injection molding and chemical reactions. This synergy enables the creation of intricate polymer structures with enhanced performance capabilities. The key points discussed in this article include:
- Definition of RIM: A fundamental overview clarifying the principles and workings of the RIM process.
- Mechanics: An analysis of the basic principles of injection molding and the kinetics involved in RIM, pinpointing how chemical reactions are interwoven into the process.
- Materials: A review of the types of polymeric resins and additives used in RIM, showcasing their benefits and roles in successful molding outcomes.
- Advantages: The cost efficiency, design flexibility, and superior material properties offered by RIM are highlighted.
- Challenges: The challenges related to process control, optimization, and material compatibility are examined, providing a balanced perspective.
- Applications: The diverse applications of RIM across various sectors, including automotive and consumer goods, demonstrate its practicality and relevance.
- Environmental Considerations: A discussion on sustainability and waste management reinforces the responsibility of manufacturers in adopting environmentally friendly practices.
- Future Trends: Anticipated advancements in materials science and automation integration are explored, signaling the trajectory of RIM technology.
Implications for Future Research
Future research in Reactive Injection Molding holds the potential for significant innovations and enhancements in the field. Areas where development can be pursued include:
- Material Science Advancements: Exploring novel polymeric materials that can further improve mechanical properties and processing efficiency.
- Optimization Techniques: Investigating enhanced computational models for process simulation to predict outcomes more accurately and improve control methods.
- Sustainability Practices: Researching alternative raw materials and energy-efficient processes that reduce environmental impacts.
- AI Integration: Leveraging artificial intelligence and machine learning to optimize the RIM process in real time, ensuring better quality control and reduced waste.