Exploring the Efficiency of Induction Furnaces in Metallurgy
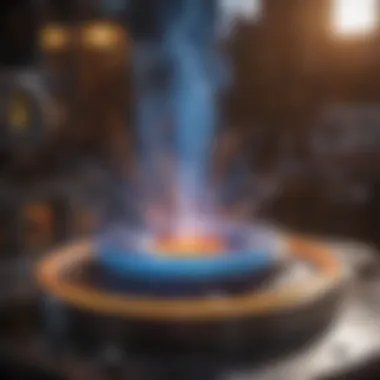

Intro
Induction furnaces hold a special place in the world of metallurgy. They are not just another piece of equipment in the factory; they are essential for melting various metals with remarkable efficiency. The technology enables industries to accomplish heating tasks without direct contact with fuel, which marks a significant leap from traditional melting methods. Understanding those furnaces moves us closer to grasping their pivotal role in everything from small workshops to large manufacturing facilities.
In this article, we’ll delve into a few prominent aspects of induction furnaces. We will explore their operational principles, identify key components, and discuss their advantages. Taking it a step further, it’s also crucial to uncover the breadth of applications across various industries that benefit from this technology. The discussion won't stop there; we’ll take a closer look at technological advancements that have fine-tuned their operation over the years and end with a look to the future. This breakdown aims to shine a light on how induction furnaces are shaping the world of modern manufacturing and metal processing.
Research Methodology
Description of research design and approach
To effectively understand induction furnaces, a thorough investigation required a blend of literary review and field analysis. Existing research provided a foundation, while practical insights from industry professionals brought the theoretical aspects into real-world context, illuminating their extensive applications and advantages. This approach offered a well-rounded understanding of the subject, bridging the gap between what’s documented and what’s done in the field.
Materials and methods used in the study
The materials studied included:
- Technical manuals detailing the operation of induction furnaces.
- Interviews with metallurgical engineers and technicians who work directly with these furnaces.
- Case studies documenting successful implementation in various industrial sectors.
Through this diverse approach, a broader scope of the functionality of induction furnaces and their implications for modern manufacturing became clear.
Discussion and Interpretation
Interpretation of results in the context of existing literature
When we dive into the literature, we find that induction melting has garnered significant attention for its energy efficiency. Studies have shown that these furnaces can reduce energy consumption by up to twenty percent compared to other methods, like arc melting. This insight echoes the growing concern for sustainability in industries worldwide.
"The induction furnace is not only a tool for melting metal but a reflection of our commitment to more efficient, safer production methods." – Industry Expert
Implications for future research or practical applications
As industries evolve, the need for further research on induction furnaces is also paramount. Future studies could focus on:
- Integration of AI in monitoring furnace performance to optimize energy use.
- Exploration of new materials that could be effectively melted using these furnaces.
- Innovations in safety protocols, reducing risks associated with operational variations.
By continuing to investigate these areas, we can not only enhance operational efficiency but also pave the way for sustainable practices within metallurgy.
Preface to Induction Furnaces
The foundation of induction furnaces is steeped in the principle of electromagnetic induction. At its core, this approach allows for the generation of heat within the metal itself, rather than relying on external heating elements. This leads to several benefits, such as improved energy efficiency and faster melting times. Induction furnaces excel in situations where large volumes of metal need to be melted quickly, lending themselves well to both small-scale operations and mass production settings.
Conceptual Framework
To delve into the operational aspects of induction furnaces, it's essential to grasp the conceptual framework that elucidates their function. The fundamental principle behind induction heating is Faraday's law of electromagnetic induction, which states that a changing magnetic field can induce an electric current in a conductor. In an induction furnace, a coil, typically made of copper, is energized with alternating current. This generates a magnetic field that penetrates the conductive material placed in the crucible.
The interaction between the magnetic field and the conductive metal results in the generation of eddy currents, which flow within the metal, producing heat. The efficiency of this process can be influenced by several factors, including the frequency of the alternating current, the type of metal, and the design of the inductor coil. By adjusting these parameters, operators can fine-tune the melting process to meet specific requirements.
Importance in Metal Processing
The significance of induction furnaces in metal processing cannot be overlooked. One reason is their versatility; they can melt ferrous and non-ferrous metals with equal efficacy. This has made them a staple in sectors ranging from steel production to foundries specializing in aluminum and copper alloys. In a world increasingly driven by precision and customizability, induction furnaces allow for consistent quality control that is critical for meeting industry standards.
"In terms of efficiency and control, induction furnaces offer capabilities that traditional methods simply cannot match."
Energy consumption is another consideration where induction furnaces shine. Compared to conventional furnaces, they often result in lower operational costs and reduced greenhouse gas emissions, making them not only a cost-effective choice but also an environmentally friendly one. Given current global trends focusing on sustainability, this makes induction furnaces especially attractive to forward-thinking manufacturers.
In summary, induction furnaces offer a unique blend of efficiency, versatility, and environmental consciousness, marking them as fundamental in contemporary metal processing practices. Understanding their functionality is not only important for professionals in the field but also for anyone interested in the future of metallurgy.
Principles of Operation
In the realm of metal processing, the operation of induction furnaces stands as a cornerstone, directly linked to their efficiency and effectiveness. At the heart of these operation principles lies the mechanism of electromagnetic induction, which is pivotal for transforming electrical energy into thermal energy. This section aims to delve into the intricacies of how these furnaces work, the various processes they employ, and the importance they hold in modern metalworking environments.
Electromagnetic Induction Explained
Electromagnetic induction is the starting gun in the race of induction furnace operations. Essentially, it’s all about generating heat through electricity without significant energy loss, a feat that makes induction furnaces a favorable choice among manufacturers.
Here's how it unfolds: when an alternating current passes through the inductor coil, it creates a fluctuating magnetic field. This magnetic field penetrates the conductive material inside the furnace—a metal or an alloy—and induces an electric current within it. This induced current generates heat due to the resistance of the material, thus raising its temperature. This principle harkens back to Faraday's Law of Electromagnetic Induction, which suggests that a changing magnetic environment can produce electric currents.
Moreover, as the current interacts with the metal, localized heating occurs. This means that metal can be melted from the inside out, which is beneficial in achieving precise melting points and improving material homogeneity.
"Induction melting allows for unprecedented efficiency and consistency in processing metals, making it a go-to technology in the industry.”
Melting Process Overview
The melting process in induction furnaces isn’t merely about reaching a specific temperature—it's a carefully orchestrated symphony of elements that harmonize to produce the desired molten metal. Once the induction coil has created that magnetic field and induced current, the process accelerates.
- Pre-Heating Stage: Initially, the metal charges are heated gradually to prevent stress and cracking caused by rapid temperature changes. This is a crucial step, especially for alloys that have different melting points.
- Core Melting: As the temperature rises, the metal's core begins to melt. Due to the nature of induction heating, the exterior often heats faster than the interior. Monitoring is essential to ensure uniform heating throughout the mass.
- Total Melting: Once the molten state is achieved, the management of the molten pool is critical. Pouring operations usually follow, requiring precision to ensure minimal waste and quality control.
- Post-Melting Process: After the molten metal is poured into molds or further processed, the next step involves cooling, which demands careful consideration to avoid defects.
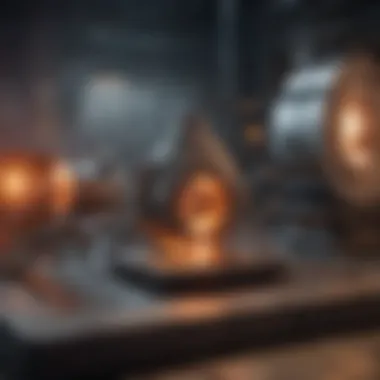

Key Components of Induction Furnaces
Induction furnaces rely on various crucial components that work together to melt metals efficiently and effectively. Understanding these components is not only essential from a technical perspective but also provides insights into the advantages and workings of induction melting technology. From the inductor coils generating electromagnetic fields to the power supply system that fuels the process, each element serves a particular purpose that significantly impacts overall performance.
Inductor Coils
Inductor coils are the heart and soul of induction furnaces. They are typically made of copper and are wound in a specific manner to create a magnetic field when alternating current flows through them. The design is not just a matter of aesthetics; it affects efficiency, power consumption, and the uniformity of the heating process. The coils induce currents in the metal, which results in rapid heating and melting. An advantage of this design is that it offers precise control over the melting temperature, enabling the processing of different metals and alloys.
A vital consideration for these coils is their cooling systems. Typically, water-cooling mechanisms are integrated to prevent overheating, which can lead to a drop in productivity and equipment lifespan.
Crucibles
Crucibles play an equally significant role in the induction furnace setup. These containers, usually made from ceramic or graphite materials, withstand high temperatures and direct contact with molten metals. The choice of crucible material is paramount since it needs to resist thermal shock and wear from both the metal being melted and the electromagnetic effects from the coils.
The geometry and thickness of the crucible also influence melting times and energy consumption. A well-designed crucible can enhance thermal efficiency by minimizing heat loss. Notably, the right crucible material can also minimize contamination, a critical concern in high-purity metal applications. This aspect is particularly crucial in fields such as jewelry manufacturing and aerospace, where material integrity is vital for performance.
Power Supply System
The power supply system is the backbone of any induction melting operation. It provides the necessary electricity to the inductor coils and dictates the frequency of the alternating current supplied to them. Typically, induction furnaces operate at frequencies ranging from 50 Hz to a few hundred kHz, depending on the specific requirements of the melting process.
An important benefit of a robust power supply system is its capability to maintain a steady voltage throughout the melting cycle, allowing for consistent output and energy efficiency. Moreover, modern power supply systems often incorporate digital controls, which enhance operational flexibility by allowing precise adjustments during the melting process.
A well-tuned power supply system not only reduces overall energy costs but can also improve the quality of metal produced, thus offering significant advantages over traditional melting methods.
In summary, a thorough understanding of the key components of induction furnaces—inductor coils, crucibles, and power supply systems—unveils the complexity and sophistication of this melting technology. Each component contributes uniquely to the efficiency, safety, and quality of metal processing, making it an indispensable tool in modern metallurgy.
Types of Induction Furnaces
Understanding the different types of induction furnaces is essential because each type serves unique purposes and applications in metal processing. This classification aids in identifying the most suitable induction heating solution for various industry needs. In this discussion, we will examine two primary types of induction furnaces: coreless induction furnaces and channel induction furnaces.
Coreless Induction Furnaces
Coreless induction furnaces are often the go-to option in many foundries due to their versatility and efficiency in melting a wide range of metals. Their design eliminates the need for a physical core, relying instead on the coil itself to generate the electromagnetic field necessary for heating.
Key Features:
- Flexibility in Capacity: Coreless furnaces can vary in their melting capacities, allowing them to handle small to medium batch sizes effectively. This adaptability is advantageous for foundries that deal with fluctuating orders.
- Fast Melting Times: The absence of a core reduces heat losses, enabling rapid heating and melting processes, which is particularly crucial in high-volume production environments.
- Energy Efficiency: These furnaces often consume less energy compared to traditional melting methods, leading to lower operational costs and a smaller carbon footprint.
"Coreless induction furnaces are efficient and versatile, making them an attractive choice in contemporary metallurgical processes."
However, it’s worth noting that with their benefits come certain considerations. For instance, there could be limitations regarding the melting of higher-resistance metals, which may require specific adjustments or cooling systems for effective operation.
Channel Induction Furnaces
Channel induction furnaces present another approach to metal melting, particularly recognized for their effectiveness in continuous casting and large-scale operations. Unlike coreless models, channel furnaces are structured with a channel that aids in the movement of molten metal, making them particularly suitable for handling large volumes of metal.
Core Benefits:
- Continuous Operation: These furnaces can operate continuously, allowing for uninterrupted production runs and efficiency in large manufacturing settings like steel mills.
- Consistent Heating: The design ensures uniform electromagnetic field distribution, which results in consistent melting and temperature maintenance. This is critical for industries that require homogeneity in their metal products.
- Scalability: Channel induction furnaces can easily be scaled for higher throughput without a significant loss in efficiency or effectiveness.
However, the implementation of channel furnaces often demands a higher initial investment compared to coreless options, which may pose a barrier for smaller operations.
Both types of induction furnaces play pivotal roles in the industrial landscape, each bringing unique advantages and considerations to metal processing. Understanding these differences aids manufacturers in making informed decisions about their melting processes.
Advantages of Induction Melting
Induction melting stands out as a frontrunner in modern metallurgy due to several significant advantages it presents. These advantages not only enhance the efficiency and effectiveness of metal processing but also align with contemporary concerns regarding sustainability and operational excellence. Let's delve into three core benefits: energy efficiency, improved product quality, and the environmental benefits that make induction melting a preferred choice in the industry.
Energy Efficiency
Induction melting furnaces are remarkably efficient compared to traditional melting methods. The heating mechanism relies on electromagnetic induction, which converts electrical energy into heat directly within the metal, minimizing heat loss to the surroundings. Because of this direct heating, the energy consumed is much lower, making induction melting an economically sensible alternative. The sector has observed cases where units report energy savings of up to 90%, especially when scaling down to smaller, dedicated melting operations.
- Quick Start-up: Induction furnaces can reach operating temperatures swiftly, meaning less idle time and reduced energy consumption.
- Precise Control: The ability to regulate temperatures precisely ensures that only the necessary energy is used, eliminating excess.
Improved Product Quality
When it comes to the end product, induction melting also excels. The process generates a uniform temperature throughout the melt, which is crucial for achieving consistent quality across batches. Impurities can also be more effectively removed during the induction melting process, leading to a cleaner, higher-grade final product.
- Reduced Oxidation: With quicker heating times and less exposure to air, there's a lower chance of oxidation occurring during the melting process, which is vital for improving metal quality.
- Alloys and Custom Composition: The precise temperature control allows for better manipulation of alloy compositions, enabling manufacturers to create specific grades of metal tailored for particular applications.
"In a competitive market, the quality of a product can make or break a manufacturing operation. Induction melting technology plays a critical role in ensuring that the output meets or exceeds industry standards."
Environmental Benefits
In today’s world, environmental concerns have become paramount, and induction melting provides a solution that aligns with eco-friendly practices. The reduced energy consumption signifies lower greenhouse gas emissions, making it a greener option for metal production. Moreover, the efficiency of the process leads to lesser waste generation.
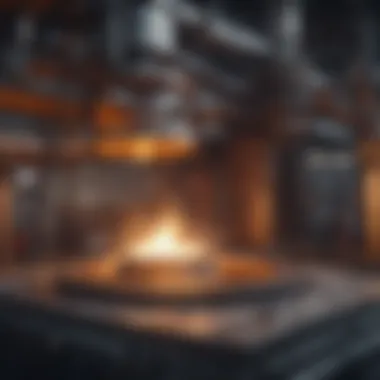

- Emissions Control: Compared to traditional furnaces that rely on fossil fuels, induction melting has a significantly smaller carbon footprint.
- Material Recycling: Induction systems are also adept at melting scrap materials, supporting recycling efforts and reducing the demand for raw resources.
Applications Across Industries
Induction furnaces have carved a niche in various sectors of metal processing, driving efficiency and innovation. Their ability to melt metals quickly and with precision makes them invaluable across multiple industries. Understanding these applications is essential for grasping the full scope and importance of induction furnaces in modern manufacturing.
Steel Production
In the realm of steel production, induction furnaces serve as a backbone for refining and melting operations. Steel plants utilize these furnaces to produce molten steel due to their ability to reach desired temperatures rapidly and maintain a uniform heat distribution. The process leads to higher quality steel with fewer impurities.
The melting capacity varies significantly among induction furnaces, allowing for both small-scale foundries and large production plants to utilize them effectively. This flexibility supports the just-in-time manufacturing model, which helps reduce inventory costs and increases responsiveness to market needs.
Some of the noticeable characteristics of induction melting in steel production are:
- Efficiency: Reduced energy consumption compared to traditional furnace methods.
- Cleaner Process: Less fume and waste generation, contributing to a more environmentally friendly operation.
- Versatility: Ability to melt different grades and alloys of steel simply by adjusting operational parameters.
Non-Ferrous Metal Melting
Non-ferrous metals, such as aluminum, copper, and bronze, also benefit significantly from induction furnaces. These metals typically have lower melting points, enabling induction furnaces to perform efficiently while ensuring a high degree of precision.
The enhanced control over temperature and melting rates allows for better handling of these metals, resulting in higher quality end products. Many industries, from automotive to aerospace, heavily rely on non-ferrous metals for components, so the role of induction furnaces in this context cannot be overstated.
Key points of using induction furnaces in non-ferrous metal melting include:
- Customized Melting Processes: Settings can be easily adjusted for different metals.
- Reduction in Oxidation: The melting process minimizes the risk of oxidation, retaining material integrity.
- Recyclability: Helps in melting scrap non-ferrous metals, promoting sustainability.
Jewelry Manufacturing
The jewelry industry has also found a significant ally in induction furnaces. Artisans use these furnaces for melting precious metals, which is crucial for creating intricate designs while maintaining quality. The precision offered by induction melting allows jewelers to work with more delicate materials without compromising their structural integrity.
With the rise of customized jewelry, the ability to produce small batches efficiently through induction melting has proven beneficial. This adaptability means artisans can create unique pieces without the need for excessive setup changes or downtime.
Important elements of induction melting for jewelry manufacturing include:
- Fine Control of Metal Quality: Ensures that gemstones and precious metals maintain their value through careful melting and casting.
- Speed of Operation: Accelerates the production process, meeting consumer demand swiftly.
- Reduced Material Loss: Efficient melting processes reduce spillage and waste.
"The ability to adapt and cater to specific needs of multiple industries makes induction furnaces not just tools of production, but harbingers of innovation."
Safety Considerations
Safety is paramount when dealing with induction furnaces. Given the high temperatures and electric currents involved in the melting process, it becomes crucial to prioritize safety measures. Understanding the potential operational hazards as well as implementing effective protective strategies can significantly reduce risks, ensuring a safer working environment for technicians and professionals alike. Many accidents can stem from minor oversights, making it essential to pay attention to safety considerations at all times.
Operational Hazards
When operating induction furnaces, several hazards can emerge that need addressing. The first major concern is thermal hazards. Operating at extreme temperatures can lead to serious burns or thermal shock if proper distance and safety gear are not maintained. Additionally, molten metals pose risks of spillage, which can cause severe injuries.
Another pressing issue is electrical hazards. Given that induction furnaces rely on high-frequency electric currents, any faults in the wiring or equipment can lead to electric shocks. Not just that, but there’s also a risk of arcs when the furnace is not properly grounded, revealing how crucial grounding systems are.
Mechanical hazards from heavy movements associated with metal handling cannot be overlooked either. Equipment and tools must be handled carefully. A misunderstanding in handling could lead to accidents or even equipment damage.
In summation, the operational hazards can broadly be categorized as:
- Thermal hazards involving high temperatures and exposure to molten metal
- Electrical hazards arising from high-frequency currents and poor grounding
- Mechanical hazards linked to heavy machinery and metal handling
"Safety does not happen by accident."
Protective Measures
Mitigating hazards, protective measures become the backbone of operational safety. Proper Personal Protective Equipment (PPE) is the first line of defense. This includes heat-resistant gloves, face shields, aprons, and sturdy boots aimed at protecting workers from thermal and molten metal exposure.
Furthermore, training plays a crucial role. Regular safety drills and educational sessions equip workers to recognize hazards and act appropriately. Ensuring everyone understands the risks and how to handle equipment properly can vastly improve safety standards.
Implementing a thorough maintenance schedule for equipment helps to identify and rectify potential faults before they become critical issues. Equipment like induction coils and power supplies must be routinely checked to ensure they operate correctly and safely.
Emergency response plans cannot be emphasized enough. In the event of an incident, having a clear action plan—ranging from spill containment to first-aid procedures—can save valuable time and potentially lives. This can include:
- Clearly marked emergency exits
- Accessible first-aid kits
- Regular fire drills
Lastly, fostering a culture of safety within the workspace, where everyone feels responsible for watching out for each other, is essential. When team members look out for one another, the overall safety level of the workplace is raised.
Technological Advances
In recent years, the landscape of induction furnace technology has undergone significant transformations. These changes not only enhance efficiency but also improve precision, control, and safety. Understanding these advancements is crucial for anyone involved in metal processing, as they redefine operational benchmarks. Keeping pace with these innovations is essential for optimizing production outcomes and minimizing energy consumption while ensuring safety and quality control.
Smart Induction Systems
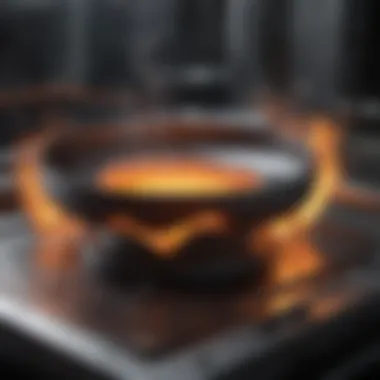

Smart induction systems represent the frontier of furnace technology. They leverage data analytics and machine learning to optimize the melting process. This system utilizes sensors and real-time data to adapt the power output and induction frequency based on the material being melted, resulting in a more consistent product.
In practical terms, imagine a scenario where a factory is melting different alloys. Traditional methods require frequent manual adjustments, which can lead to human error or inefficiencies. However, a smart induction system can seamlessly adjust parameters as different materials enter the furnace, allowing for uniform heating and reduced scrap rates. This capability not only saves time but drastically enhances the overall quality of the output.
By implementing smart systems, industries can tap into:
- Improved Efficiency: Enhanced energy use leads to cost savings.
- Quality Control: Real-time adjustments mitigate defects in the casting.
- Data-Driven Decisions: The accumulation of operational data can guide future strategies.
"The integration of smart technologies into induction furnaces marks a leap toward sustainable and efficient manufacturing practices."
Automation in Induction Melting
Automation in induction melting serves a dual purpose: enhancing productivity and improving safety. Automation minimizes human intervention in dangerous tasks, like handling molten metals, which presents significant hazards. As automatic systems take over tasks such as loading materials, monitoring temperatures, and controlling power levels, human operators can focus on more strategic responsibilities.
Consider a foundry where workers manually monitor gauges and adjust settings throughout the day. This approach can be labor intensive and exposes workers to high heat and toxic fumes. Contrast this with an automated system that can continuously monitor conditions and make instantaneous adjustments as needed.
The benefits are clear:
- Consistent Quality: Automation reduces variability in production, leading to uniform outcomes.
- Safety Enhancements: Fewer personnel are required near the furnace, reducing injury risks.
- Operational Cost Reduction: Less manual labor lowers wage expenditures and increases throughput.
Economic Impact
The economic impact of induction furnaces is a key element discussed in this article as it showcases how these systems influence not only individual manufacturing processes but also the entire industry landscape. Induction furnaces hold significant value by optimizing metal processing operations, affecting both the cost and efficiency of production. Their presence in various sectors makes them vital for understanding market dynamics and future advancements in metallurgy.
Cost Analysis
When evaluating the financial aspects of induction furnaces, several factors come into play. The initial investment in induction furnace technology can be substantial. However, it’s crucial to consider the total cost of ownership over time.
- Operational Efficiency: Induction furnaces tend to consume less energy compared to traditional melting methods. This can lead to cost reductions in energy bills. For instance, a plant utilizing induction melting can see energy savings of up to 30%.
- Maintenance Costs: Induction systems are often simpler in design, which translates to lower maintenance costs. Fewer moving parts mean less wear and tear, ultimately providing a more stable financial outlook.
- Labor Costs: Automation capabilities in modern induction furnaces can reduce labor needs. With smart systems taking over mundane tasks, companies can reallocate human resources to more impactful roles.
This holistic view of costs paints a picture where, despite high upfront expenses, the long-term savings could characterize induction melting as a wise financial choice.
Market Trends
Induction furnaces have not only changed the landscape of metal melting but have also shaped market trends across different sectors. Some key observations are:
- Growth in Steel and Non-Ferrous Sectors: With the rise of global infrastructure projects, there's an increased demand for steel, thereby boosting the induction furnace market. Moreover, non-ferrous metals like aluminum are also experiencing surging popularity, leading to a parallel growth in induction melting technology.
- Shift towards Sustainable Practices: As industries grapple with environmental concerns, induction melting is often regarded as a more sustainable choice. Induction furnaces produce fewer emissions and can easily incorporate recycled materials into the melting process, aligning with global sustainability goals.
- Technological Innovations: Ongoing advancements in induction technology, such as better control systems and enhanced power supplies, are anticipated to further drive the market. These innovations make induction furnaces more attractive due to their improved energy efficiency and performance.
"The evolution of induction furnaces reflects broader shifts in metal processing toward efficiency and sustainability, prompting industries to adapt to newer methodologies."
In sum, the economic impact of induction furnaces cannot be underestimated. They signify a crucial pivot point in cost management and market evolution, making it imperative for professionals to stay abreast of these trends. Understanding these nuances equips stakeholders—be they investors, manufacturers, or researchers—with knowledge essential for informed decision-making.
Future Directions
The future of induction furnaces is promising, as the industry aims for greater efficiency and sustainability. Technical advancements in automation and material processes are reshaping the landscape of metal melting. This evolution stands central to understanding operational longevity and energy conservation in manufacturing. By focusing on sustainability initiatives and innovations in material science, businesses can improve not only their productivity but also their ecological footprint.
Sustainability Initiatives
Sustainability is not just a buzzword; it is a critical aspect of modern industrial practices. In the realm of induction furnaces, this means adopting measures that reduce emissions and energy consumption. By prioritizing eco-friendly initiatives, companies can gain a competitive edge and meet rising consumer expectations for environmentally responsible practices.
One significant step is the optimization of energy use throughout the melting process. For example, recycling scrap metal significantly lowers overall material costs and energy consumption. The integration of advanced control systems can further fine-tune energy usage, ensuring that every kilowatt is utilized effectively. Additionally, many induction furnaces are now being designed to use renewable energy sources.
Moreover, there is a continuous push for stricter environmental regulations, driving industries to rethink their strategies. Following these guidelines not only enhances public perception but also mitigates potential legal risks linked to environmental mismanagement. Aspects to consider include:
- Smart Metering: Real-time monitoring can identify inefficiencies, leading to meaningful energy savings.
- Heat Recovery, which captures excess heat and redirects it, can significantly cut down energy waste.
- Material Upcycling, which allows waste by-products to be transformed into new, valuable materials, thereby reducing landfill contributions.
("Efficiency measures in induction melting are integral towards a sustainable future in metallurgy.")
Innovations in Material Science
The ongoing progress in material science opens doors for more efficient and advanced induction furnaces. Stronger and more resilient furnace materials can withstand higher temperatures, ultimately improving durability and performance. This is particularly critical in industries requiring high-intensity melting processes.
Innovative materials such as ceramic composites are gaining attention for their ability to endure extreme conditions without degrading. In addition to physical improvements, the development of advanced alloys can enhance thermal conductivity. This allows for more efficient heat transfer in the melting chamber, leading to faster melting times and energy savings.
Furthermore, innovations are paving the way for better insulation systems within induction furnaces. Improved insulation not only reduces heat loss, but it also maintains a more stable operating temperature, which is vital for consistent melting quality. Key developments to note include:
- Nanomaterials: These can enhance heat resistance and structural integrity, significantly extending the lifecycle of furnaces.
- Coatings: Advanced coatings can improve surface hardness and reduce wear and tear.
- Additive Manufacturing: This technique allows for the creation of intricate components that were previously impractical, optimizing furnace designs.
Epilogue
In wrapping up our exploration of induction furnaces, it’s vital to underscore their role in modern metallurgy. These furnaces don’t just melt metals; they revolutionize the way we think about material processing. Understanding their functionality leads us to appreciate not just the mechanisms at work, but also the broader implications for efficiency, safety, and sustainability in manufacturing.
Summary of Key Points
To recapitulate, here are the essential takeaways from this article:
- Principles of Operation: Induction furnaces operate via electromagnetic induction, allowing precise temperature control and faster melting times compared to traditional methods.
- Types of Induction Furnaces: Coreless and channel induction furnaces each have unique designs suited to different metal types and melting needs.
- Key Components: Inductor coils and crucibles play a central role in the heating and melting process, while a robust power supply system ensures consistent operation.
- Advantages: They offer remarkable energy efficiency, enhance product quality, and decrease environmental impact, which is increasingly crucial in today’s market.
- Applications: Ranging from steel production to jewelry manufacturing, these furnaces are indispensable across various industries.
- Safety and Technology: Addressing operational hazards and implementing protective measures are paramount in using induction furnaces. Recent technological advances, such as smart induction systems, further improve safety and efficacy.
- Economic Impact: The cost-efficiency of using induction furnaces represents a significant factor in their widespread adoption, with market trends favoring energy-saving technologies.
- Future Directions: Sustainability initiatives and advancements in material science signal a promising future for induction melting technology.
Final Thoughts on Induction Furnaces
The significance of induction furnaces in the manufacturing ecosystem cannot be overstated. They embody a fusion of efficiency, precision, and adaptability, responding to the demands of an ever-evolving industry. As we continue to forge lighter, stronger materials and embrace sustainable practices, induction furnaces stand at the forefront of innovation.
"Induction furnaces are not merely a part of metal processing; they signify a paradigm shift towards smarter, cleaner production techniques."