Understanding Screen Printing Electrodes in Depth
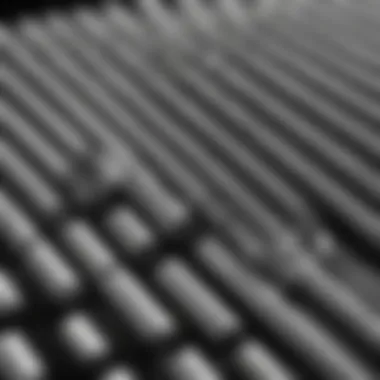
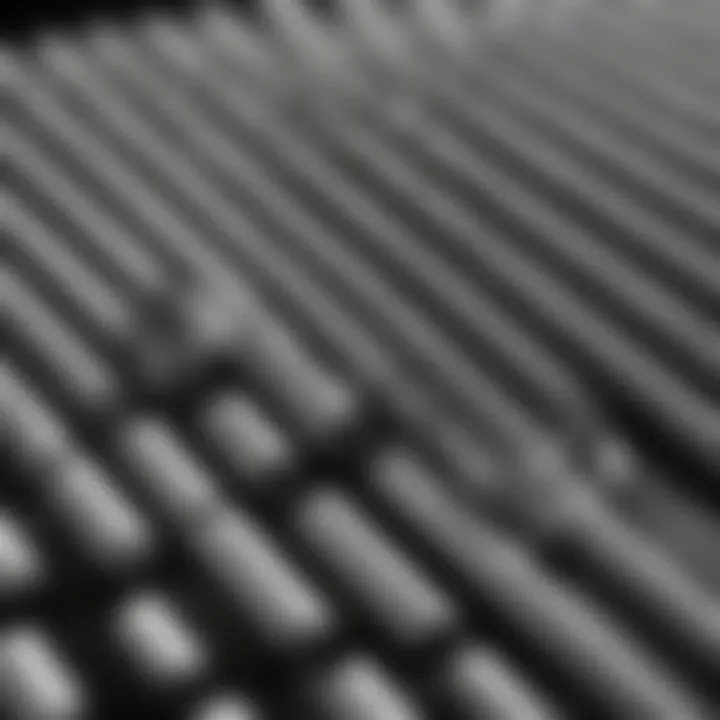
Intro
Screen printing electrodes hold a significant place in various technological domains, from the electronics industry to biomedical applications. As integral components, these electrodes facilitate essential processes that require precision and reliability. This article aims to provide a thorough understanding of screen printing electrodes, emphasizing their types, fabrication methods, materials utilized, and diverse applications. By exploring these dimensions, we unveil the complexities and advancements in electrode technology.
Research Methodology
Description of Research Design and Approach
The exploration of screen printing electrodes begins with a qualitative analysis of existing literature supplemented by experimental studies. This approach allows for a comprehensive examination of various electrode types and their applications. Literature from technical journals and industry reports serves as the foundation for understanding the historical context and current trends in electrode technology.
Materials and Methods Used in the Study
To provide specific insights into screen printing electrodes, the following methods were employed:
- Literature Review: A systematic review of research papers, articles, and patents was conducted to gather data on electrode types and materials.
- Case Studies: Selected case studies highlighting successful applications of screen printing electrodes were analyzed.
- Interviews: Discussions with professionals from the industry yielded practical insights into fabrication processes and current challenges.
Discussion and Interpretation
Interpretation of Results in the Context of Existing Literature
The findings indicate a significant variety in screen printing electrodes, each tailored for particular applications. For example, silver-based electrodes are widely used in electronic devices due to their excellent conductivity. In contrast, carbon-based electrodes find utility in medical diagnostics, offering biocompatibility and stability.
"Screen printing is not just a manufacturing technique; it is a bridge between material science and practical application."
This observation aligns with the trends noted in recent research, illustrating the importance of selecting appropriate materials and fabrication techniques in the production of screen printing electrodes.
Implications for Future Research or Practical Applications
The continuous evolution of screen printing technology enhances the potential for future applications in emerging fields. For instance, advancements in nanomaterials can lead to the development of more sensitive and efficient electrodes in healthcare diagnostics. As technology progresses, further research will be needed to address the limitations of current electrodes and explore novel materials and methods.
Preamble to Screen Printing Electrodes
Screen printing electrodes play a crucial role in various technological domains, acting as a fundamental element in devices we use every day. Their significance extends across fields including electronics, medical diagnostics, and renewable energy solutions. Understanding these electrodes requires a comprehensive approach, focusing on their types, materials, and fabrication methods.
Definition and Significance
Screen printing electrodes are conductive elements created using screen printing technology. This method allows for precise application of conductive materials onto diverse substrates. Their primary function is to facilitate electrical conductivity, enabling various applications such as sensors, displays, and medical devices. The importance of these electrodes lies in their ability to be fabricated in large scales while maintaining desired performance characteristics. As industries face demands for smaller, smarter, and more efficient devices, understanding the intricacies of screen printing electrodes becomes essential.
Screen printing electrodes provide a versatile solution for many high-tech applications. Their adaptability allows design flexibility, catering to specific needs across different sectors.
Historical Context
The evolution of screen printing electrodes closely aligns with advancements in materials and technology. Initially, screen printing originated in the 19th century and has since developed into a significant technique used in various manufacturing processes. The focus on screen printing electrodes began to gain momentum in the late 20th century. During this time, electronic devices became more prevalent, necessitating efficient and effective ways to create connections on printed circuit boards and other electronics. Over the years, ongoing research and innovation in conductive inks, substrates, and printing techniques have furthered the potential applications of screen printing electrodes in modern technology.
In summary, exploring the definition and historical context of screen printing electrodes illustrates their growing importance and relevance in today’s technology landscape. The following sections will detail the various types of electrodes and the materials used in their fabrication.
Types of Screen Printing Electrodes
Understanding the various types of screen printing electrodes is crucial because they play a significant role in diverse applications. This section will outline the primary categories and their implications on performance and utility. Each type serves specific purposes and has unique attributes that affect their use in industries like electronics, medical diagnostics, and energy solutions.
Conductive Ink Electrodes
Conductive ink electrodes are vital in screen printing technology as they enable the creation of electronic circuits directly onto substrates. This type of electrode uses inks laced with conductive materials, such as silver, copper, or carbon. The main advantage of these electrodes is their ability to provide excellent conductivity without the need for traditional wiring, thus simplifying the manufacturing process.
The utilization of conductive ink electrodes is particularly prevalent in printed circuit boards and RFID tags. The significant benefit is the cost efficiency compared to traditional methods of circuit creation. Additionally, the flexibility afforded by printed electronics allows for innovative designs that would be difficult to achieve otherwise.
Non-Conductive Substrate Electrodes
Non-conductive substrate electrodes serve distinct functions within screen printing applications. These electrodes utilize substrates that do not conduct electricity, making them suitable for specific applications like sensors where isolation from electrical interference is necessary. Materials such as certain polymers or glass are commonly used for these electrodes.
Their primary benefit lies in providing a stable base for other components, ensuring they do not disrupt the functionality of adjacent conductive areas. It is essential for industries where precise measurements and sensor accuracy are critical, such as in medical diagnostics where electrodes must maintain clear operational boundaries.
Flexible Electrodes
Flexible electrodes have gained prominence due to their adaptability across various innovative applications. Typically made from elastomers or other flexible materials, these electrodes are essential in wearable technology and smart devices. The flexibility allows for conforming to uneven surfaces, enhancing comfort for the end user in wearable applications.
They exhibit optimal performance where rigidity is a limitation. Integration in applications like health monitoring and environmental sensing demonstrates the versatility of flexible electrodes. They effectively balance performance with user experience, providing crucial data without discomfort.
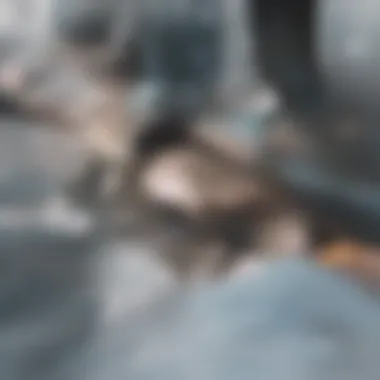
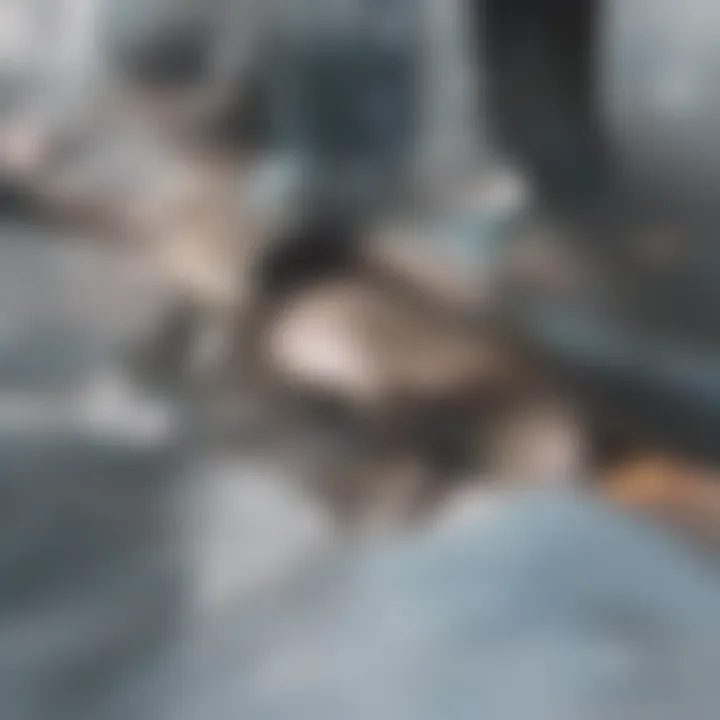
"Innovations in electrode design not only improve functionality but also open new avenues for technology integration."
In summary, the significance of understanding the types of screen printing electrodes lies in their broad impact on technology performance and application innovation. Recognizing these distinctions enables better decisions in material choice and manufacturing methods, catering effectively to the specific demands of various industries.
Materials Used in Screen Printing Electrodes
The selection of materials in screen printing electrodes is crucial for their performance and application. Understanding the materials used helps outline the possibilities and limitations of screen printing technology. The right choice of materials ensures efficient functioning, durability, and costs effectiveness, which are essential factors for success in various applications. In this section, we will discuss both conductive and substrate materials that play a significant role in screen printed electrodes.
Conductive Materials
Conductive materials are the backbone of any screen printing electrode. They determine how well the electrode will function in its intended applications. The two primary types of conductive materials are carbon-based materials and metallic nanoparticles, each with its own unique characteristics.
Carbon-based materials
Carbon-based materials are a popular choice when it comes to screen printed electrodes. One key characteristic of carbon-based materials is their excellent electrical conductivity. This makes them suitable for various electronic applications. Moreover, carbon materials, like graphite or carbon black, are often cost-effective, which is a significant benefit.
A unique feature of carbon-based materials is their flexibility. This property allows them to be used on various substrates, including flexible and stretchable electronics. However, this flexibility might lead to decreased mechanical stability over time. Overall, the benefits often outweigh the disadvantages, making carbon-based materials a solid choice in screen printing electrodes.
Metallic nanoparticles
Metallic nanoparticles contribute significantly to the performance of screen printed electrodes as well. Their defining characteristic is their high electrical conductivity, which often surpasses that of carbon-based materials. This property can enhance the efficiency of electrodes in critical applications, such as sensors and power storage devices.
Metallic nanoparticles, such as silver or gold nanoparticles, are advantageous due to their ease of dispersion and adhesion to various substrates. However, a notable disadvantage is their cost. They typically have a higher price point than carbon-based materials. The decision to use metallic nanoparticles will depend on the specific application requirements and cost considerations.
Substrate Materials
Substrate materials provide the foundation for screen printing electrodes, influencing their overall performance and usability. The most commonly used substrate materials include polymers and glass, and each presents unique advantages and drawbacks.
Polymer substrates
Polymer substrates are widely used in screen printing electrodes because of their flexibility and lightweight properties. A key characteristic is their ability to conform to various shapes, making them ideal for wearable and portable electronic devices. Their ease of processing adds to their popularity in this field.
One unique feature of polymer substrates is their compatibility with various printing techniques. This versatility allows for diverse application scenarios. However, polymer substrates may face issues with durability and temperature resistance compared to other materials. Understanding these factors is essential for maximizing their effectiveness.
Glass substrates
Glass substrates are valued for their rigidity and thermal stability. One significant advantage is that glass can withstand higher temperatures during manufacturing processes without degrading. This characteristic makes them suitable for applications needing stringent durability standards.
A unique feature of glass substrates is their optical transparency, which can be useful in specific electronic applications like displays. However, the inherent fragility of glass also poses challenges. It can be more susceptible to breakage during handling or application, which might not be suitable for every situation. Thus, careful consideration during material selection is essential.
Choosing appropriate materials for screen printing electrodes enhances performance and application versatility. The balance between conductive and substrate materials is essential to achieving desired outcomes in technology.
Fabrication Processes
The fabrication processes of screen printing electrodes are fundamental to their overall functionality and application. Understanding these processes is essential for maximizing the efficiency and performance of electrodes in various uses. The core aspects of fabrication include screen preparation, inking and printing techniques, and curing processes. Each element plays a significant role in determining the quality of the final product.
Screen Preparation
Screen preparation is a critical initial step in the screen printing process. It involves creating a mesh screen that will transfer the electrode design onto a substrate. The choice of mesh type, size, and material directly influences ink flow and print resolution. For many applications, a finer mesh can yield higher resolution prints, but this comes with challenges in ink deposition.
Moreover, various treatments can be applied to the screen to enhance adhesion between the ink and the substrate. Such treatments might involve coating the screen with a specific chemical or employing techniques like photo-emulsion printing. Proper screen preparation affects not only the quality of the print but also the efficiency of the printing process.
Inking and Printing Techniques
Inking and printing techniques are vital in determining how the conductive materials are applied to the substrate. There are several methods, two of which are notably effective: the stencil method and the squeegee technique.
Stencil method
The stencil method involves creating a stencil that selectively allows ink to pass through in specific patterns. This method is particularly useful for producing intricate designs with high precision. One key characteristic of the stencil method is its adaptability to various substrates, including flexible and rigid surfaces.
A significant advantage of this technique is the ability to control ink thickness and coverage, enabling the production of layers with specific electrical properties. However, one potential drawback lies in its setup time, which can be considerable when many designs need to be printed accurately.
Squeegee technique
The squeegee technique utilizes a squeegee to push ink through the screen onto the substrate. This method is efficient for large-scale production, making it a popular choice in industry settings. Its primary characteristic is the ability to achieve consistent ink distribution across the surface area.
The unique feature of the squeegee technique is the speed at which it can print multiple electrodes, thus reducing production time. Nevertheless, it can be prone to issues like smudging if not executed correctly. Careful control of pressure and movement is necessary to maintain print quality without sacrificing speed.
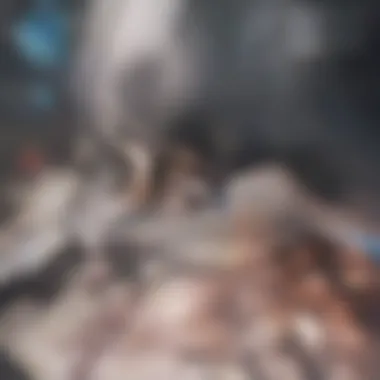
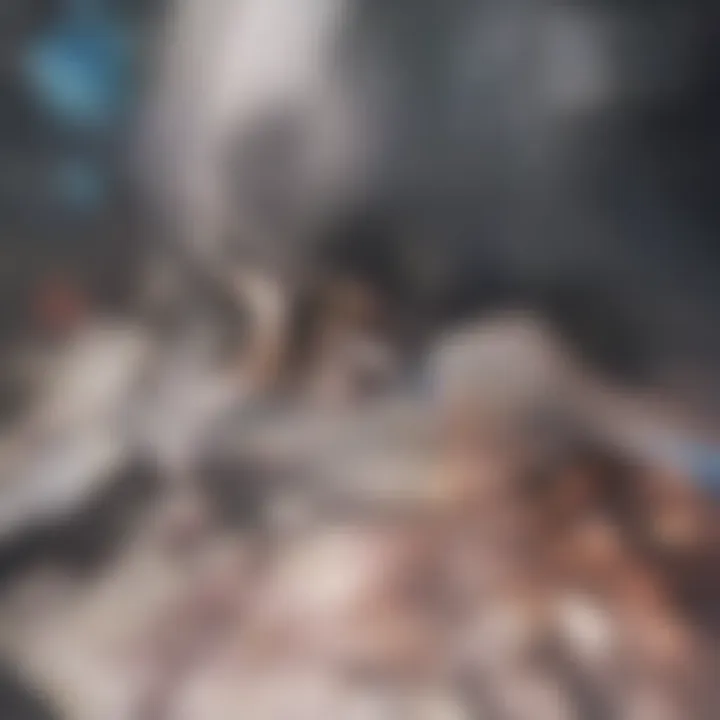
Curing Processes
Curing processes are crucial for solidifying the printed electrodes and ensuring durability. Once the ink is applied, curing typically involves heat or ultraviolet light to drive off solvents and initiate chemical reactions that bond the materials together. The choice of curing method can significantly affect the performance of the final electrode in terms of conductivity and adhesion to the substrate.
Technical Parameters and Performance Metrics
Understanding the technical parameters and performance metrics of screen printing electrodes is vital for evaluating their effectiveness across various applications. These metrics serve as benchmarks to assess the functionality and reliability of electrodes in real-world scenarios. The two primary facets discussed here are conductivity measurements and durability/wear resistance. These aspects are essential, as they directly impact how well the electrodes perform in demanding environments.
Conductivity Measurements
Conductivity measurements provide insights into how well an electrode can transmit electrical current. This parameter is crucial, particularly in applications such as printed circuit boards and flexible electronics. High conductivity ensures that the device operates efficiently, with minimal energy loss.
The measurement of conductivity involves the use of specific devices like multimeters or four-probe setups, which can accurately assess the electrical resistance of the electrode material. Factors influencing conductivity include:
- Material Composition: The type of conductive materials used, such as carbon or metallic nanoparticles, significantly affects the electrode’s performance.
- Printing Technique: Variations in screen printing methods can lead to differences in thickness and uniformity, thereby impacting conductivity.
Maintaining optimal conductivity is essential for applications where precision and reliability are paramount, such as in the aerospace and automotive industries. Conversely, low conductivity can lead to increased power consumption, heat generation, and potential device failure.
Durability and Wear Resistance
Durability and wear resistance are equally significant. An electrode must withstand various environmental factors, including humidity, temperature fluctuations, and mechanical stress. These attributes contribute to the longevity and consistent performance of screen printed electrodes in their intended applications.
Factors that influence endurance include:
- Material Selection: Using advanced materials with higher resilience can increase durability. For example, polymer substrates can offer better resistance to wear compared to traditional materials.
- Curing Techniques: Proper curing processes during fabrication immensely affect wear resistance. Insufficient curing might lead to premature degradation.
_"Durability is not just a feature; it is a requirement for reliability in high-stress applications."
In industries like medical diagnostics, where consistent performance is crucial, durability speaks to the electrode's lifespan and reliability. Hence, understanding and optimizing these technical parameters ensures that screen printing electrodes can meet the rigorous demands of contemporary applications.
Applications of Screen Printing Electrodes
Screen printing electrodes play a crucial role in various applications across multiple sectors. Their unique ability to create thin, flexible, and highly conductive patterns makes them particularly significant in fields where space and precision are at a premium. This section delves into three main areas where these electrodes are most effectively utilized: the electronics industry, medical diagnostics, and energy generation and storage.
Electronics Industry
In the electronics industry, screen printing electrodes are indispensable. They are widely used to produce printed circuit boards and flexible electronics. The thin films created during the screen printing process ensure that these components can be both lightweight and efficient. This quality is especially vital for modern devices that demand miniaturization without compromising performance.
- Design Flexibility: Manufacturers can design intricate circuit patterns that can fit more functions into limited space.
- Cost-Effectiveness: Screen printing allows for large-scale production, reducing costs compared to traditional manufacturing methods.
- Compatibility: These electrodes can be applied to various substrates, making them suitable for a range of electronic applications, including wearables and sensors.
Medical Diagnostics
The medical diagnostics field has seen a surge in the use of screen printed electrodes. They are essential components in devices like biosensors and diagnostic tools, enabling real-time monitoring of physiological markers. The advantages include:
- Rapid Prototyping: New sensor designs can be developed and tested quickly, speeding up research and development processes.
- Sensitivity and Accuracy: Advances in conductive inks have enhanced the performance of these electrodes, providing reliable and accurate results for critical medical applications.
- Portability: Many devices are designed to be portable, allowing for on-site testing and diagnostics, which is vital in emergency situations.
Energy Generation and Storage
Energy generation and storage applications rely increasingly on screen printed electrodes for efficiency and sustainability. This technology has been applied in fuel cells, batteries, and solar cells.
- Increased Efficiency: Screen printing can lead to better contact between the electrode and the electrolyte, enhancing overall performance.
- Innovation: As research progresses, new materials and formulations are emerging, allowing for the development of more efficient energy solutions that are cost-effective and environmentally friendly.
- Scalability: The manufacturing process can be easily scaled, meeting the demands of commercial applications.
"The integration of screen printing technology in energy solutions exemplifies the shift towards more sustainable practices across various industries."
Limitations and Challenges
Understanding the limitations and challenges associated with screen printing electrodes is essential for professionals in this field. These challenges can impact the overall effectiveness and viability of electrodes in various applications. Analyzing material limitations and environmental concerns will shed light on critical factors influencing the future of screen printing technologies.
Material Limitations
One of the most significant challenges in screen printing electrodes is the inherent material limitations. Various conductive materials have distinct properties, and not all are suitable for every application. For example, while carbon-based materials offer flexibility and good conductivity, they might not perform well under extreme temperatures. Metallic nanoparticles, while effective, can suffer from issues like oxidation, affecting durability.
To address these limitations, researchers must focus on developing new materials or improving existing ones. This involves conducting experiments to understand the behavior of different conductive inks and their interaction with the substrate. Some common challenges faced include:
- Adhesion: The electrode must adhere well to the substrate. Poor adhesion can lead to peeling or flaking.
- Print Resolution: High-resolution printing is often necessary for intricate designs. The property of the ink can impact how fine the detail can be.
- Scalability: As demands grow, manufacturing processes must be scalable and reliable. Material limitations can pose issues in meeting these demands.
Environmental Concerns
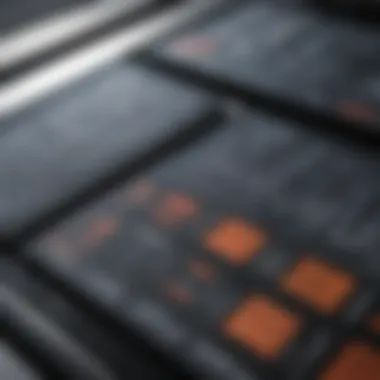
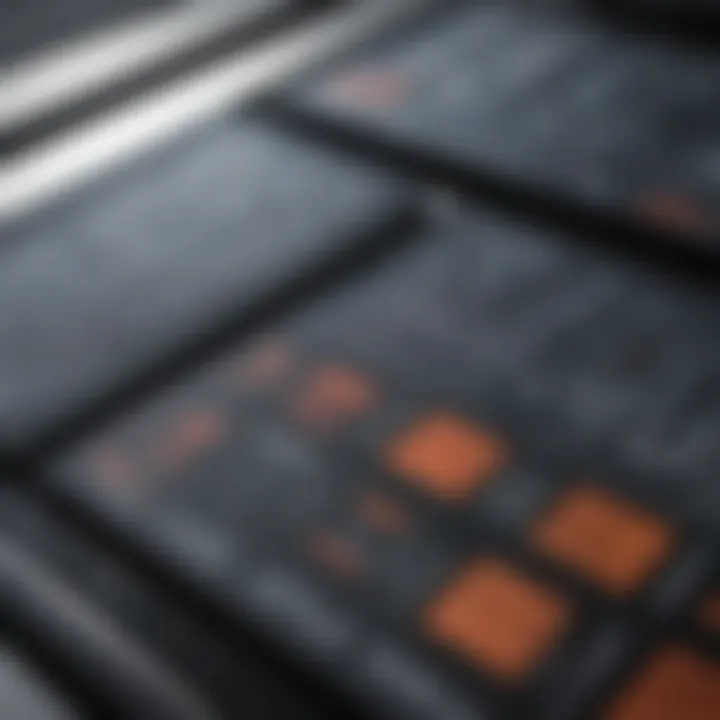
Environmental concerns related to screen printing electrodes cannot be overlooked. The production processes often involve chemicals that may be harmful to the environment, which is a growing concern among regulators and consumers alike. Additionally, the disposal of old or unused electrodes presents challenges, particularly in the context of e-waste.
Efforts are being made to shift towards greener materials and processes. For example, researchers are exploring biodegradable substrates and inks that harness less harmful chemicals.
Some key environmental considerations include:
- Chemical Waste: The need for appropriate disposal of waste generated during the manufacturing process. This includes the solvents and other materials used in printing.
- Recycling: Opportunities for recycling old electrodes to minimize waste are essential. Effective recycling methods can reduce the environmental footprint.
- Sustainability: Looking towards sustainable production methods is vital. This includes selecting materials that have a low environmental impact and promoting practices that enable responsible sourcing.
These limitations and challenges provide a framework for ongoing research and development in the field of screen printing electrodes. Innovations will hinge on overcoming these hurdles to enhance performance, sustainability, and application versatility.
"The advancement in electrode technologies hinges importantly on understanding and addressing the limitations we face today."
Efforts to improve materials and mitigate environmental effects is vital for the future of screen printing electrodes.
Recent Advancements in Technology
The realm of screen printing electrodes is rapidly evolving. Recent advancements in technology play a crucial role in enhancing performance and expanding the applications of these electrodes. The integration of cutting-edge materials and innovative printing methods greatly contributes to their effectiveness and efficiency. These advancements not only improve the quality of the products but also make them more accessible and reliable for various industries.
Innovations in Materials Science
Innovations in materials science have brought forth significant changes in the field of screen printing electrodes. New conductive materials have emerged, which offer higher electrical conductivity and better adhesion properties. For example, silver nanowires are increasingly popular due to their excellent conductivity and flexibility. The development of these materials allows for the production of thinner and more efficient electrodes, which is particularly important for wearable technology.
Moreover, recent progress in organic electronics has led to the creation of conductive polymers. These materials provide additional benefits, such as lightweight characteristics and ease of processing. The combination of traditional and novel materials enhances the versatility of screen printing electrodes and opens new possibilities for their application in various sectors.
Emerging Printing Technologies
Emerging printing technologies have reshaped how screen printing electrodes are fabricated. Traditional methods are being complemented or replaced by advanced techniques such as inkjet printing and roll-to-roll printing. Inkjet printing allows for precise placement of materials, which reduces waste and enhances design flexibility. The ability to print complex patterns with high resolution offers substantial advantages, particularly in the electronics industry.
Roll-to-roll printing is another technique gaining traction due to its scalability and efficiency. This method enables mass production of electrodes on flexible substrates, making it ideal for large-scale applications like solar cells and flexible displays. The continuous workflow of roll-to-roll printing speeds up production times, ultimately reducing costs and increasing availability.
Advances in material science and printing technology are critical for the future of screen printing electrodes, enabling higher performance and broader usage.
Overall, staying updated with these advancements is essential for researchers, educators, and professionals in the field. By focusing on both innovations in materials and emerging printing technologies, the landscape of screen printing electrodes continues to evolve, paving the way for new opportunities in numerous industries.
Future Directions
In the field of screen printing electrodes, understanding the future directions is crucial for innovation and applicability. As technology evolves, so does the need for more efficient, reliable, and versatile electrodes. Advancements can lead to enhanced performance metrics and greater commercialization possibilities. Key areas of research and development have been identified to push the boundaries of this technology.
Potential Research Areas
Focused research can significantly contribute to the advancement of screen printing electrodes. Areas that merit attention include:
- Biocompatible Materials: Researching materials that are not only conductive but also compatible with biological systems. This can open new avenues in medical diagnostics and wearable health monitoring devices.
- Sustainability Practices: Exploring eco-friendly materials and processes can reduce the environmental impact of screen printing technologies. Studies on recycling conductive inks and substrates are essential.
- Nanoengineering: This field has vast potential for enhancing the properties of screen printed electrodes. Investigating the use of carbon nanotubes or graphene can significantly improve conductivity and mechanical stability.
- Smart Materials: Development of materials that can adapt to changes in environment through conductive responses. Smart electrodes can have varied applications in sensors and actuators.
- Integration with Wireless Technology: Researching ways to combine screen printed electrodes with wireless technology for better functionality in portable applications, specifically in the electronics sector.
Prospects for Commercial Applications
As researchers explore various potentials, the commercial applications of screen printing electrodes are poised for growth. Some notable prospects include:
- Healthcare Devices: The importance of affordable and efficient diagnostic tools continues to rise. Screen printed electrodes could facilitate the production of low-cost biosensors for diseases monitoring, thus enhancing patient care.
- Consumer Electronics: For everyday devices, enhancing screen printing technology can allow for thinner and more efficient electronic components tailored towards consumer demands.
- Renewable Energy Solutions: The push for sustainability can lead to innovations such as printed solar cells, offering a new way of harnessing solar energy at a lower production cost.
- Automotive Applications: Incorporating screen printed electrodes into automotive sensors could improve efficiency and functionality, particularly in electric vehicles.
As the landscape of screen printing electrodes evolves, the focus must remain on bridging these potential advancements with practical applications, thus ensuring that both academia and industry can benefit effectively.
Finale
The conclusion section of this article brings to light the significance of screen printing electrodes in various fields, emphasizing their implications and future potential. Summarizing the core insights within, this part encapsulates the essential takeaways from each section, providing clarity on how these electrodes function and their various applications. This not only reinforces the information discussed but also positions the reader to understand the relevance of screen printing electrodes in today's technologically driven landscape.
A comprehensive understanding of screen printing electrodes aids in numerous areas such as product development, research, and educational pursuits. With the blend of technical know-how and practical applications, professionals and scholars alike can leverage this knowledge effectively. The exploration of different types, materials, and fabrication processes highlights the versatility of these electrodes, revealing potential uses across industries.
"Screen printing electrodes represent a confluence of technology, innovation, and practical application. Their importance today cannot be overstated."
Recognition of limitations and challenges also plays a crucial role in this discussion. It is vital for stakeholders to be aware of material restrictions and environmental issues as they design and optimize products. By understanding these factors, one can navigate the complexities of implementation in various applications more adeptly.
Ultimately, the insights gathered in this article serve as a foundation for future inquiries and developments. As screen printing technology continues to advance, ongoing research may uncover new possibilities and elevate the utility of screen printing electrodes in multifarious domains.
Summary of Key Insights
This article offers a thorough discussion of the various aspects of screen printing electrodes. Key insights include:
- Types of Electrodes: Different electrodes serve unique functions, paving ways for diverse applications. Key types include conductive ink electrodes, non-conductive substrate electrodes, and flexible electrodes.
- Materials Used: The materials used for making these electrodes, such as carbon-based materials and metallic nanoparticles, contribute significantly to their performance and applications across different fields.
- Fabrication Processes: Understanding methods like screen preparation, inking and printing techniques, and curing processes is crucial to producing effective electrodes.
- Technical Performance: Parameters such as conductivity measurements and durability influence how well the electrodes perform in their intended applications.
- Applications Across Industries: The practical uses in electronics, medical diagnostics, and energy storage highlight the electrodes' importance.
- Limitations and Challenges: Consideration of material limitations and environmental issues is critical for sustainable development.
- Future Directions: Insights into potential research areas and commercial prospects suggest fruitful paths for innovation and advancement in electrode technology.
Final Thoughts
Reflecting on the content of this article, it becomes apparent that screen printing electrodes are not mere tools but pivotal elements in the progression of multiple industries. As technology evolves, their significance will likely increase. Continuous improvements in fabrication methods, materials, and application techniques will lead to enhanced functionalities and broader usage.
For students, researchers, and professionals, staying informed about the latest findings and developments related to screen printing electrodes is vital. Understanding the fundamentals, as well as emerging trends, can guide future projects and research endeavors. Ultimately, the knowledge shared in this article aims to inspire a deeper inquiry into the world of screen printing electrodes, fostering innovation and exploration within this dynamic field.