Understanding Surface Roughness Inspection Techniques
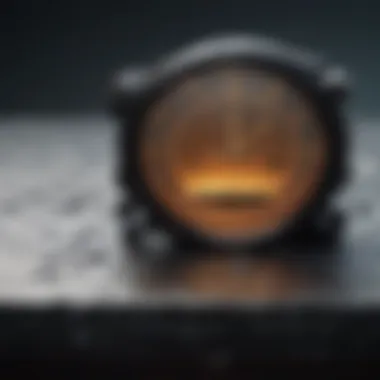
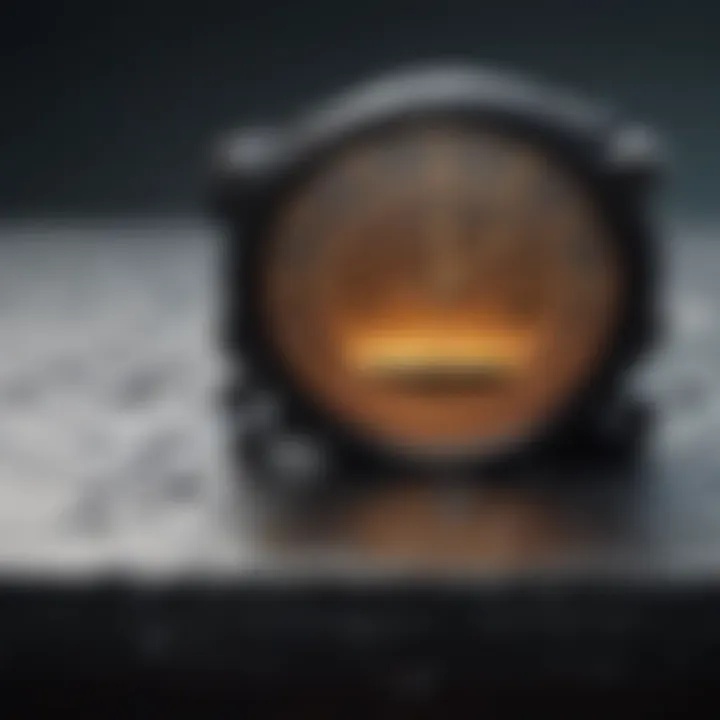
Intro
Surface roughness inspection is a critical factor in engineering and manufacturing. It plays a significant role in determining how materials interact with each other in various applications. Poor surface quality can lead to many issues, such as increased friction, wear, and potential failure of parts. Understanding the techniques used to assess surface roughness and the overarching importance of this inspection provides a foundation for optimizing product performance and longevity.
This article will elaborate on various measurement techniques, highlight their applications, and address challenges in quality control related to surface roughness. Moreover, we will touch on emerging technologies that serve as solutions in this domain. Through this comprehensive analysis, the objective is to provide a rich understanding of surface roughness inspection and its crucial role within multiple disciplines.
Intro to Surface Roughness
Understanding surface roughness is crucial for engineers and manufacturers alike. This concept influences how materials interact, perform, and are perceived in various industries. Surface roughness plays a significant role in everything from friction and wear to fluid flow characteristics. By comprehending its intricacies, one can improve product designs, enhance functionality, and ensure reliability in engineering applications.
Definition of Surface Roughness
Surface roughness refers to the texture of a surface, quantified by the irregularities present on its micro and macro levels. It arises from various manufacturing processes and can significantly affect the performance of mechanical systems. The parameters that characterize surface roughness include average roughness (Ra), root mean square roughness (RMS), and maximum height of profile (Rz). Each of these metrics provides insight into the surface condition and influences how the material will behave in practical applications.
Historical Context
The study of surface roughness has evolved over time, tracing back to early machinist practices. Initially, surface finishes were judged by visual inspection or tactile feedback. As technology advanced, so did methods for measuring these surfaces. The invention of profilometers in the mid-20th century marked a significant leap. This allowed for precise, repeatable measurements, paving the way for more sophisticated applications in engineering and manufacturing.
Importance in Engineering
In engineering, the importance of surface roughness cannot be overstated. It affects the following key factors:
- Friction and Wear: A rough surface can increase friction, leading to faster wear and reduced lifespan.
- Fit and Tolerance: Accurate surface roughness specifications ensure better fitting of components, especially in precision machinery.
- Coating and Adhesion: Surface texture can influence how well coatings adhere to materials, impacting durability and performance.
Fundamental Concepts in Surface Roughness
Surface roughness is a critical focus in many engineering fields. Understanding the fundamental concepts ensures precise measurements, contributes to quality control, and enhances product performance. A solid grasp of these concepts provides a platform for diving into advanced inspection techniques and applications.
Measurement Parameters
Average Roughness (Ra)
Average Roughness, commonly referred to as Ra, is a key parameter that helps quantify the roughness of a surface. It represents the arithmetic average of the absolute values of the profile heights over a specified length. The relevance of Ra lies in its simplicity and ease of calculation, making it a widely adopted choice for many industries. However, one should be cautious because it may not capture all the nuances of surface characteristics.
One significant advantage of Ra is its established presence in regulatory standards, facilitating comparison across various projects. This consistency is beneficial for engineers who require reliable data. On the downside, Ra may overlook extreme surface features, which could affect certain applications where these features are critical.
Root Mean Square Roughness (RMS)
Root Mean Square Roughness, or RMS, adds another layer of understanding to surface measurements. Unlike Ra, RMS takes into account the squares of the profile heights, giving more weight to larger deviations. This characteristic is beneficial when surfaces have significant peaks and valleys, making RMS a popular choice in precision engineering and materials science.
Advantageously, RMS is more sensitive to surface texture variations compared to Ra, which helps in identifying subtle inconsistencies. However, its more complex calculation can pose challenges in practical implementation for some users, especially in less controlled environments.
Maximum Height of Profile (Rz)
Maximum Height of Profile, known as Rz, measures the vertical distance between the highest peak and the lowest valley of a surface within a given sampling length. This metric can provide a clear view of the overall surface profile, which can be crucial in applications where average roughness may not show critical variations.
The strength of Rz lies in its ability to highlight extreme features, making it a valuable tool in sectors such as aerospace and automotive engineering, where performance depends on precise surface conditions. Nevertheless, its reliance on maximum values may sometimes give an incomplete picture of the surface performance, potentially misleading in quality assessments.
Surface Topography
Regular and Irregular Surfaces
The classification of surfaces into regular and irregular types plays a significant role in understanding overall roughness. Regular surfaces exhibit predictable patterns, essential for processes requiring uniformity, such as machining parts. In contrast, irregular surfaces display more chaotic characteristics, which can be detrimental in precision applications.
Recognizing these surface types allows engineers and manufacturers to tailor their processes accordingly. Understanding how these surfaces interact with other materials is vital for optimizing functionality and ensuring longevity. The major drawback of relying solely on this classification is the risk of oversimplification, which may not capture all relevant details.
Profile vs. Areal Surface Roughness
The distinction between profile and areal surface roughness offers deeper insights into surface analysis. Profile roughness measures variations along a one-dimensional line, while areal roughness assessments consider a two-dimensional area. This differentiation is critical for applications needing comprehensive surface data, such as coatings and textures.
Utilizing both profiles and areal assessments allows for a more textured understanding of surface interactions. As a downside, the complexity and potential costs of areal measurements might deter some users, particularly in smaller operations.
Factors Influencing Surface Roughness
Manufacturing Processes

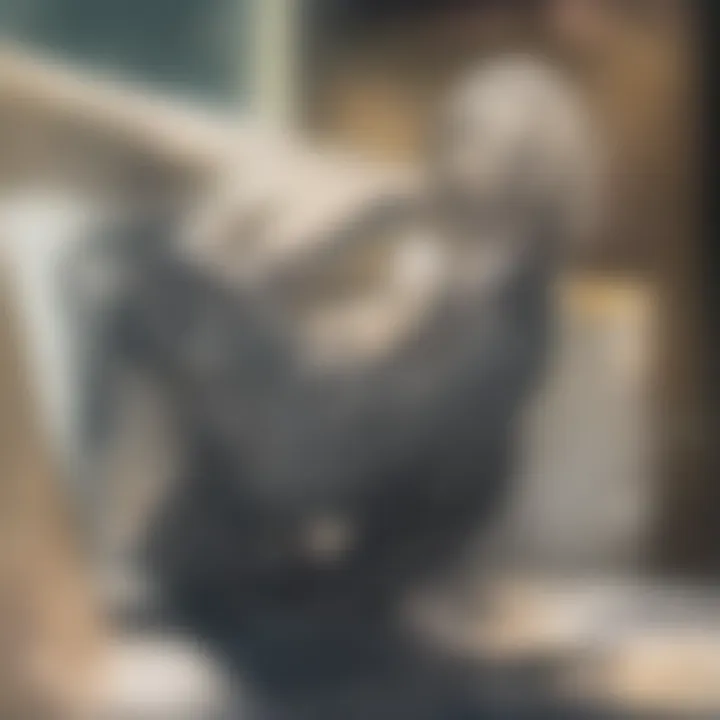
Understanding how various manufacturing processes impact surface roughness is essential. Different techniques, such as turning, milling, and grinding, each create distinct surface characteristics. The choice of method influences overall performance, efficiency, and cost-effectiveness in the production cycle.
Moreover, selecting the appropriate process can directly affect the surfaces' durability and functionality. For instance, a more aggressive machining operation might lead to higher roughness, which could be undesirable for specific applications. On the other hand, precision processes, while potentially more time-consuming, yield smoother surfaces beneficial in high-performance settings.
Material Properties
The intrinsic properties of materials significantly dictate surface roughness outcomes. Harder materials may withstand machining better, resulting in smoother surfaces. Conversely, softer materials might produce more significant roughness due to their susceptibility to deformation during processes. Understanding these elements helps in predicting and controlling surface characteristics.
Choosing the right material can help in achieving desired roughness levels, optimizing functionality, and extending product lifetimes. However, this relationship is not always linear, and external interventions may still be needed to enhance the final surface qualities.
Post-Processing Operations
Post-processing represents a critical phase in refining surface quality. Techniques such as polishing, coating, or surface treatment all contribute to achieving the desired roughness. The selection of the right post-processing procedure can significantly enhance performance characteristics while minimizing the roughness.
Despite the advantages, post-processing may increase production times and costs. Timely assessments and adjustments are essential to maintain efficiency without compromising quality.
Measurement Techniques in Surface Roughness Inspection
Measurement techniques in surface roughness inspection play a vital role in understanding material finish and performance. Accurate measurement helps ensure that components meet design specifications and function reliably in their applications. By selecting the appropriate measurement technique, manufacturers can optimize processes and manage quality effectively. This section explores various contact and non-contact methods used in surface roughness inspection, along with emerging technologies that promise to enhance measurement precision.
Contact Methods
Stylus Profilometry
Stylus profilometry is one of the most common contact methods used for measuring surface roughness. It involves dragging a stylus across the surface and recording the vertical movements as the stylus traces the profile. This method is widely accepted due to its accuracy and established standards. Key characteristics include its high resolution, which allows for detailed analysis of surface features.
Stylus profilometry is beneficial for situations requiring precise and repeatable results, making it a frequent choice in engineering and material science. Its unique feature is the ability to generate a 2D surface profile, thus offering insights into surface texture.
However, there are disadvantages as well. The contact with the surface may cause damage or wear, especially on softer materials. Additionally, operational speed is limited compared to some non-contact techniques.
Contact Microscopy
Contact microscopy employs a microscope objective to evaluate surface roughness through direct physical contact. It can be effective in detailed imaging and quantifying surface topography. The primary strength of contact microscopy lies in its ability to provide high-resolution images, which can be particularly useful for materials with intricate surface patterns.
This method is popular for applications that require visual inspection and quantitative analysis simultaneously. The unique capability of magnifying the surface makes it advantageous for studying micro-scale features.
Nevertheless, since it also involves contact with the surface, potential scratching and wear remain concerns, particularly with soft or delicate materials. Furthermore, sample preparation may require additional steps, complicating the measurement process.
Non-Contact Methods
Optical Interferometry
Optical interferometry is a sophisticated non-contact technique that uses the interference of light waves to measure surface roughness. This method stands out for its ability to gather high-resolution data over large areas quickly. One major characteristic of this technique is its non-invasive nature, which means it can be applied to delicate or valuable materials without risking damage.
Optical interferometry is favorable for applications where traditional methods are impractical, such as in the aerospace or biomedical fields. Its unique feature includes the capability to capture 3D surface topography, enabling comprehensive data analysis.
Despite its advantages, optical interferometry can be sensitive to environmental factors like vibrations and temperature fluctuations. Moreover, the equipment required can be costly, requiring careful justification for its use in certain applications.
Laser Scanning Confocal Microscopy
Laser scanning confocal microscopy represents another advanced non-contact approach. It employs lasers to illuminate the sample while capturing images at different depths, allowing for precise 3D reconstruction of the surface topography. Its key characteristic is the ability to provide detailed spatial resolution and depth information.
This method is particularly popular in research and quality control because of its rapid data acquisition capabilities. The unique feature of high sensitivity to surface roughness makes it highly effective for assessing fine details in complex geometries.
However, laser scanning confocal microscopy may also face limitations such as the dependency on specific material reflectivity. Some surfaces may not provide adequate contrast, resulting in reduced measurement quality. Additionally, initial setup and calibration require time, impacting operational efficiency.
Emerging Technologies
3D Surface Measurement
3D surface measurement is an emerging trend that incorporates various techniques, including both optical and laser systems. This approach shows promise in redefining standards for surface inspection, offering detailed topographical maps of surfaces. Its key characteristic is the depth of analysis it provides, enabling in-depth understanding of complex surface structures.
This method is beneficial for industries focusing on precision, such as electronics and optics. Its capability to integrate easily with digital technologies further enhances its appeal, enabling seamless data management and analysis.
However, despite its potential, the investment cost for advanced 3D systems can be considerable. Additionally, interpreting complex data requires skilled personnel, which may not always be readily available in smaller organizations.
Digital Holographic Interferometry
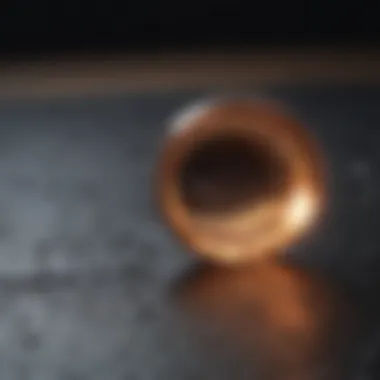
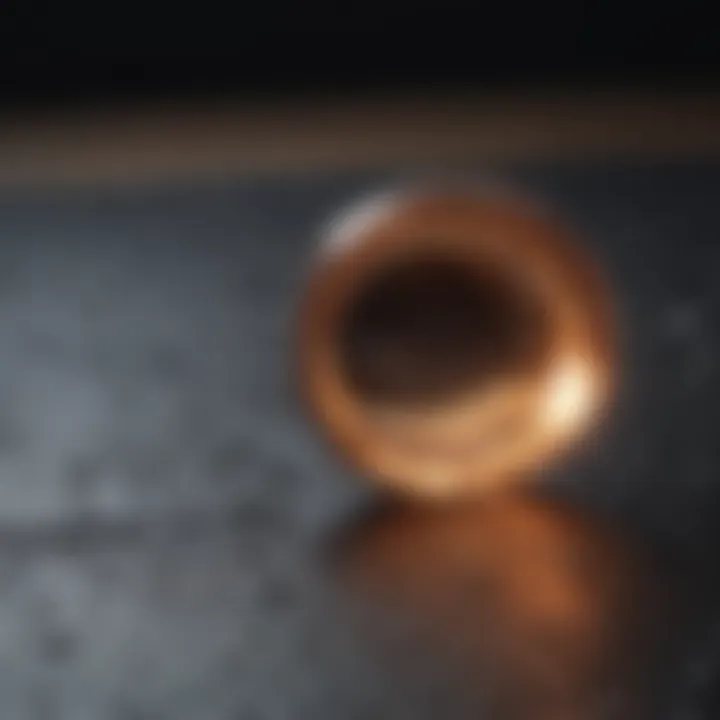
Digital holographic interferometry leverages holography techniques to measure surface changes with high sensitivity. This method stands out for its ability to capture dynamic processes in real-time, contributing significantly to fields like structural analysis and material testing. Its key characteristic is the use of digital recording, which enhances data accuracy and allows for advanced processing capabilities.
This technique is gaining traction for its applicability in both research and industrial sectors. The unique ability to visualize wavefronts significantly aids in understanding surface phenomena better.
However, the complexity of the technology can pose challenges. Required software for data analysis may demand advanced training to master. Furthermore, the cost of necessary equipment can be a barrier for smaller entities.
Understanding the various measurement techniques in surface roughness inspection is crucial for effective quality control in engineering and manufacturing. Each technique offers unique advantages and potential challenges that must be evaluated in the context of specific applications.
Quality Control and Surface Roughness
Quality control is a fundamental aspect in manufacturing and engineering processes. Surface roughness is a key element within this domain. By continual monitoring of surface roughness, the quality assurance processes can be enhanced significantly. Proper assessment of surface characteristics leads to improved product performance and increased lifespan of materials. This section will delve into the specific roles, challenges, and standards concerning the quality control processes associated with surface roughness inspection.
Role in Quality Assurance
In quality assurance, surface roughness acts as a direct indicator of a machined component's functionality. Smooth surfaces can imply low friction properties, which is essential in components like bearings. Conversely, certain applications require increased roughness to enhance adhesion or improve friction.
Effective quality assurance means implementing precise measurement techniques to quantify roughness. Utilization of proper standards ensures that measurements are consistent, which in turn builds trust and reliability among stakeholders in a production chain.
Regulatory Standards
Manufacturers often rely on established regulatory standards to guide their inspection processes. These standards ensure uniformity and reliability for measurements. Among the most important standards are ASTM and ISO guidelines.
ASTM Standards
ASTM Standards provide a comprehensive set of guidelines focused on testing materials, including surface roughness inspection. A distinctive attribute of these standards is the wide acceptance across industries.
One notable characteristic is the clarity of procedures outlined for various measurement techniques. This resonates well with industries looking for consistency. ASTM Standards are beneficial as they often evolve with technological advances, keeping pace with the latest measurement techniques. However, users must familiarize themselves with the specific ASTM standard relevant to their particular application, as nuances between standards can affect results.
ISO Guidelines
ISO Guidelines complement ASTM by providing an international framework for quality standards. A critical aspect of ISO guidelines is their global recognition. Companies benefit from these standards as they allow for international trade and collaboration.
The unique feature of ISO Guidelines is their commitment to continuous improvement through regular updates. However, the challenge lies in the complexity that can arise from their implementation; understanding the specific requirements of each ISO standard necessitates time and expertise.
Challenges in Quality Control
Quality control is often faced with hurdles due to the nature of surface roughness measurement.
Variability in Measurements
Variability of measurements can stem from many factors, including operator skill and measurement equipment. This inconsistency can misrepresent actual surface conditions, affecting product quality. Recognizing factors leading to variability is critical to maintaining reliable quality control processes. By implementing controlled procedures and training programs, organizations can reduce variability and achieve more accurate measurements.
Environmental Factors
Environmental factors can also greatly influence surface roughness measurements. Changes in temperature, humidity, and even dust can introduce errors. Monitoring these conditions is vital. One key aspect is maintaining a controlled environment to ensure that measurements are taken under stable conditions, thus minimizing the potential for error in assessments. This focus on the environment can lead to more reliable results and ultimately improve the quality control framework across the board.
"Quality control in surface roughness is not just about meeting standards but understanding the implications of the surface finish on product performance."
In summary, understanding the relationship between surface roughness and quality control enhances efficiency in engineering and manufacturing. By adhering to established standards and addressing the challenges involved, manufacturers can achieve high product quality and reliability.
Applications of Surface Roughness Inspection
The relevance of surface roughness inspection is evident across various industries. It plays a critical role in ensuring product quality, performance, and lifespan. By understanding how roughness can affect functionality, manufacturers can make informed decisions concerning materials, processes, and surface treatments. The advantages of effective roughness inspection are vast, impacting production efficiency, cost-effectiveness, and product safety.
Automotive Industry
Engine Components
Engine components are pivotal in vehicle performance. The intricacies of these parts dictate how well an engine can operate under stress. For instance, the roughness of a cylinder bore can affect oil retention and efficiency. A finely tuned surface can lead to optimal sealing, minimizing leakages and ensuring better fuel economy. The key characteristic of engine components is their high precision requirement, making them susceptible to failures if surface roughness is not adequately inspected. Choosing the right inspection technique ensures that these parts meet stringent standards for quality.
Surface Treatments
Surface treatments are techniques applied to enhance the functionality and longevity of engine components. They can involve coatings, polishing, or thermal treatments to achieve desired roughness parameters. The unique feature of surface treatments lies in their ability to provide protection against wear and corrosion, which is crucial in automotive applications. However, a downside is the potential trade-off between surface smoothness and other mechanical properties. Inspecting surface roughness before and after treatment is essential for assessing effectiveness.
Aerospace Industry
Aircraft Components
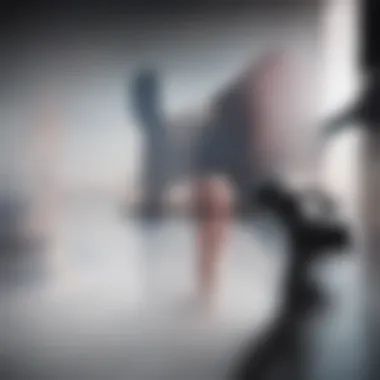
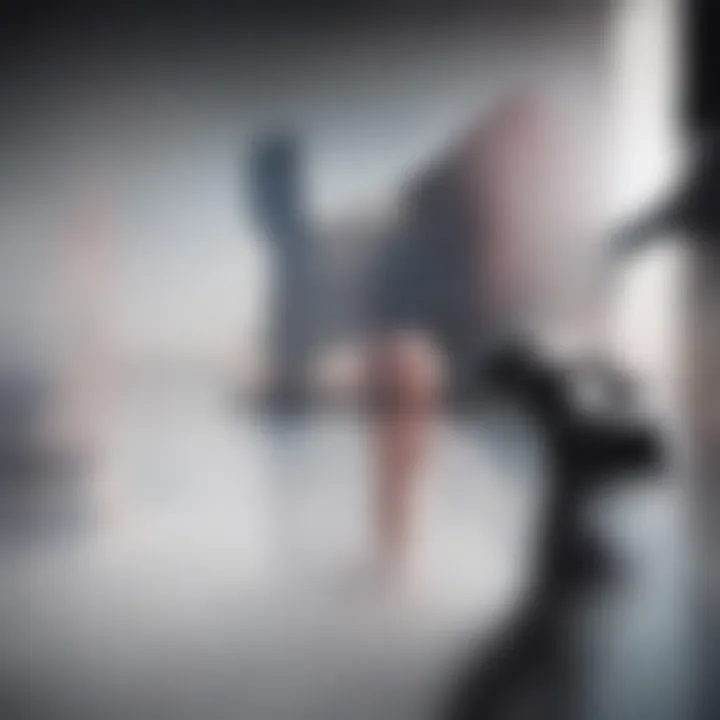
In the aerospace sector, aircraft components must meet demanding safety and performance criteria. The surface finish of these components directly influences aerodynamic efficiency and structural integrity. For example, turbine blades require specific roughness metrics to optimize airflow and reduce drag. The highlighted characteristic of aircraft components is their rigorous manufacturing standards. This makes precise surface roughness inspections indispensable to avoid catastrophic failures.
Safety Standards
Safety standards play a significant part in ensuring that aerospace products perform reliably and safely. These standards often specify maximum allowable roughness levels for critical components, making inspections a legal and safety obligation. The unique feature of safety standards is their role in protecting lives and investments. Yet, compliance can be challenging due to the variability in materials and manufacturing processes. Adhering to these standards via thorough roughness inspections helps maintain a high safety level.
Medical Devices
Implants
Implants are key to modern medicine, affecting patient recovery and longevity. The surface roughness of implants can influence tissue integration and healing. A rougher surface can enhance osseointegration, allowing for better bone attachment. The important characteristic of medical implants is biocompatibility. However, they may face issues such as surface contamination or biofilm formation. Thus, consistent surface roughness inspection is crucial to ensure safety and efficacy.
Biocompatibility
Biocompatibility refers to an implant's ability to interact safely with tissues. The surface characteristics of these devices play a large role in determining biocompatibility. Specific roughness levels can promote biological responses that favor bonding with host tissue. The unique aspect of biocompatibility is its direct impact on patient outcomes. Regular inspections for roughness can help mitigate risks associated with implant failure and improve overall satisfaction.
Future Trends in Surface Roughness Inspection
Future trends in surface roughness inspection are crucial for improving measurement accuracy and operational efficiency. Integrating advanced technologies not only enhances inspection methods but also reduces the time and cost involved in quality control processes. Organizations are increasingly recognizing the importance of deploying faster, more reliable tools to maintain competitive advantages. The objectives of these trends include increasing precision, reducing human error, and fostering sustainability in manufacturing.
Integration of AI and Machine Learning
Predictive Analysis
Predictive analysis in the context of surface roughness inspection helps anticipate potential issues before they arise. It utilizes data from past inspections to forecast future outcomes. This characteristic makes it an appealing choice for manufacturers. By leveraging historical performance metrics, organizations can pinpoint specific challenges associated with surface quality. The unique feature of predictive analysis lies in its capability to analyze large datasets efficiently. Advantages include timely interventions and minimized downtime, while disadvantages may involve the need for substantial initial investment in data systems and algorithms.
Automated Inspections
Automated inspections provide significant advantages in terms of efficiency and consistency. Automation reduces human involvement in the measurement process, which can otherwise introduce variability. The key characteristic of this method is its ability to operate continuously without fatigue, leading to a higher throughput. Automated inspections streamline the quality assurance process, making it a popular choice for high-volume production lines. A unique feature is the precision offered by automated systems, resulting in fewer errors. However, some disadvantages include the high costs associated with setup and maintenance.
Advancements in Measuring Devices
Portability and Usability
Portability and usability of measuring devices are becoming increasingly important. Compact and user-friendly devices enable inspectors to conduct measurements in diverse environments, improving flexibility. The essential characteristic here is ease of transport and setup, allowing for inspections to take place at different sites or during various stages of production. This adaptability is particularly beneficial for real-world applications. A notable advantage is enhanced accessibility to measurement tools; on the downside, more portable devices may sometimes compromise measurement precision compared to traditional systems.
Data Collection and Management
Efficient data collection and management systems play a pivotal role in modern inspection processes. The key characteristic of effective data management is integration with other manufacturing systems. This capability allows for real-time analytics and monitoring of surface quality metrics. Benefits include improved decision-making based on robust data insights. A potential disadvantage is the complexity involved in managing vast amounts of data, which can lead to information overload if not handled properly.
Sustainable Practices
Reducing Waste in Manufacturing
Reducing waste in manufacturing associated with surface roughness inspection focuses on minimizing material and operational waste. The crucial feature here is the implementation of efficient processes that not only improve surface quality but also conserve resources. This approach is considered beneficial as it not only enhances profitability but also promotes environmental sustainability. A disadvantage may be the resistance to change from established practices, which can hinder the adoption of more efficient methods.
Life Cycle Assessments
Life cycle assessments evaluate the environmental impacts of manufacturing processes from start to finish. This analytical approach is essential for understanding how surface roughness influences not just product performance, but also its environmental footprint. The key characteristic of life cycle assessments is their holistic view of resources and waste. This makes it an impactful choice for organizations looking to improve their sustainability practices. The advantage is the identification of areas for improvement throughout the productโs life cycle, while a disadvantage could be the time-consuming nature of conducting these assessments.
Epilogue
The conclusion of any comprehensive study holds particular importance, acting as the final synthesis of the information discussed. In this article, the conclusion encapsulates the essence of surface roughness inspection, emphasizing its critical role across diverse fields such as engineering and manufacturing. This topic not only highlights the necessity of robust measurement techniques but also underscores the relationship between surface roughness and product performance.
In revisiting the key points articulated throughout the article, readers gain clarity on the diverse measurement techniques, including contact and non-contact methods. These techniques can differ in effectiveness based on the application and the specific requirements of the materials being assessed.
Furthermore, understanding the challenges encountered in maintaining quality control due to surface roughness variability ensures that professionals are better equipped to manage and mitigate potential issues.
"Engaging with the complexities of surface roughness inspection aids in optimizing manufacturing processes and elevating product reliability."
The integration of advanced technologies, such as artificial intelligence and machine learning, signifies a shift toward a more efficient approach in surface roughness inspection. These emerging trends are crucial for ensuring that products are not only viable but also sustainable in the competitive market.
Summary of Key Points
- Definition and Importance: Surface roughness inspection plays a vital role in ensuring the functionality and longevity of products.
- Measurement Techniques: Both contact and non-contact methods have distinct advantages and applications, making it essential to choose the right technique based on specific needs.
- Quality Control: Quality assurance relies heavily on monitoring surface roughness, addressing challenges such as measurement variability and compliance with regulatory standards.
- Emerging Technologies: Innovations in technology continue to reshape how surface roughness is measured and assessed, enhancing precision and efficiency in manufacturing processes.
Future Perspectives
Looking ahead, the future of surface roughness inspection is promising. Key developments in the field suggest a trend toward heightened automation and integration of intelligent systems in the inspection workflow. This may lead to:
- Predictive Maintenance: The utilization of AI may facilitate predictive analysis capabilities, allowing for proactive management of manufacturing processes based on surface roughness data.
- User-Centric Innovations: The advancement of measuring devices will likely focus on portability and usability, simplifying the inspection process in various settings.
- Sustainability: Efforts to reduce waste during manufacturing processes can lead to greener practices, positively affecting the entire lifecycle of products.
The combination of these factors will inevitably draw attention to the transformative potential of surface roughness inspection, asserting itself as a cornerstone of quality control and manufacturing excellence.