Vibration Detection Sensors: Technology and Applications
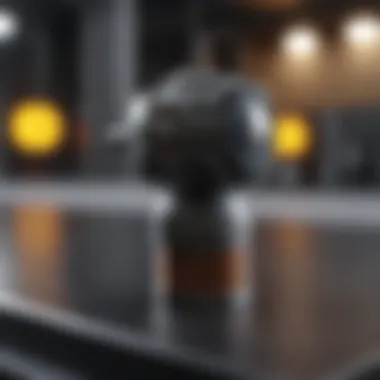
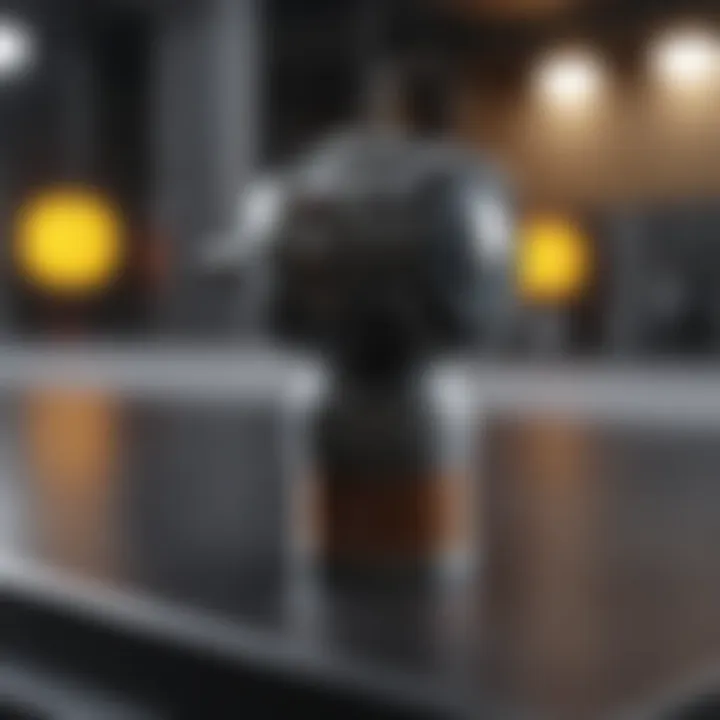
Intro
Vibration detection sensors play a crucial role in various industries, including automotive, aerospace, and structural monitoring. These devices help in identifying unwanted vibrations, ultimately safeguarding equipment and structures. Understanding their technology, applications, and significance helps us appreciate their contribution to safety and efficiency.
In this article, we examine vibration detection sensors in depth. We explore their underlying principles, types, and advancements in technology. It is essential to look at how these sensors impact different sectors and what challenges they may face in the future. Each section will provide insights relevant to students, researchers, educators, and professionals interested in this field.
Preamble to Vibration Detection Sensors
Vibration detection sensors play a crucial role in many fields. These sensors are essential for monitoring vibrations in structures, machinery, and vehicles. They help detect issues early, which can prevent failures and accidents. By understanding these sensors, professionals can improve safety and efficiency in various industries.
Definition and Purpose
Vibration detection sensors are devices that measure oscillations in physical systems. They convert mechanical motion into measurable electrical signals. The main purpose of these sensors is to monitor and analyze vibrations. This can help engineers understand the condition of structures and machinery. Common types include accelerometers and piezoelectric sensors, each suited for specific applications.
A primary benefit of these sensors is their ability to enhance safety. In industrial environments, for instance, timely detection of abnormal vibrations can indicate potential equipment failure. This leads to reduced downtime and maintenance costs.
Historical Context
The use of vibration detection dates back several decades. Early sensors were mechanical, relying on physical movements to indicate vibration levels. With advancements in technology, electronic sensors became prevalent in the 20th century. The 1950s saw the introduction of piezoelectric sensors, which significantly improved sensitivity and response time.
As industries evolved, the demand for accurate vibration monitoring grew. Aerospace and automotive sectors were some of the first to adopt modern vibration detection methods. Today, vibration sensors are integral to many systems including civil engineering and automotive applications. The ongoing evolution of these sensors reflects advancements in material science and technology.
Fundamental Principles of Vibration Detection
Understanding the fundamental principles of vibration detection is crucial for grasping how these sensors function and their applications across various fields. Fundamental principles encompass the basic concepts and operational mechanisms that govern how vibration detection sensors detect and measure vibrations. It is essential to recognize these principles as they directly impact the sensor's accuracy, sensitivity, and overall effectiveness.
Vibration detection sensors rely on certain physical principles to sense vibrations. Specifically, they translate mechanical vibrations into measurable electrical signals. This conversion is key to their role in monitoring the health and performance of machinery, structures, and even living organisms.
Different types of sensors utilize various operational mechanisms, ensuring that there is always a suitable option available for different applications. Knowing these principles can help experts choose the right sensor for specific tasks, which is vital in industries like aerospace, automotive, and structural engineering.
Basic Concepts of Vibration
Vibration can be defined as the oscillation or repetitive motion of an object or system around its equilibrium position. The measurement of vibration is important because excessive vibrations can indicate problems such as misalignment, imbalance, or wear in machinery. Understanding the characteristics of vibrations includes frequency, amplitude, and duration.
- Frequency: Refers to how often the vibration occurs over a specific time. Higher frequencies often represent rapid oscillations, which can signify potential issues in systems.
- Amplitude: This is the maximum displacement from the equilibrium position and indicates the intensity of the vibration.
- Duration: This describes the time period over which the vibration occurs, which is critical in determining the extent of potential damage.
Sensor Operation Mechanisms
Understanding the operational mechanisms of vibration detection sensors reveals how they interpret vibrations into usable data. Different mechanisms have unique characteristics that make them suitable for various applications.
Piezoelectric Effect
The piezoelectric effect is a phenomenon where certain materials generate an electrical charge in response to mechanical stress. This characteristic makes piezoelectric sensors a popular choice in vibration detection. The key feature of these sensors is their sensitivity to slight changes in pressure or force, allowing them to accurately detect vibrational activity.
- Unique Feature: Piezoelectric sensors have a broad frequency response, making them versatile for both low and high-frequency applications.
- Advantages: They are compact, capable of measuring dynamic forces, and have a wide measurement range. However, they may not perform well in static load conditions.
Capacitance Changes
Capacitance-based sensors measure vibrations by detecting changes in capacitance caused by the relative motion of conductive plates that occur when a vibration is present. The main advantage of these sensors is their ability to provide measurements in real-time without requiring extensive calibration.
- Key Characteristic: Capacitance changes enable these sensors to be sensitive to both displacement and acceleration.
- Advantages/Disadvantages: They are effective in environments with low-frequency vibrations. However, they can be affected by temperature variations and humidity, which may impact reliability.
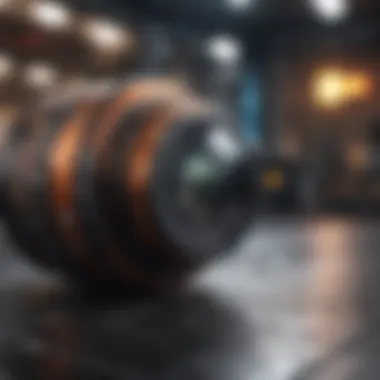

Optical Sensors
Optical sensors utilize light to detect vibrations, often using laser technology to measure tiny movements in a target. Their primary appeal lies in their non-contact nature, which allows for measurements without influencing the system being monitored.
- Key Characteristic: Optical sensors provide high precision and accuracy because they can measure small displacements at a high sampling rate.
- Advantages: They are beneficial in complex environments where traditional sensors might struggle. The disadvantage is that they can be more expensive and require clear line-of-sight to the target surface.
"Understanding these various sensor operation mechanisms is essential for making informed decisions about which technology is appropriate for specific vibration detection tasks."
The principles and mechanisms underpinning vibration detection sensors have far-reaching implications across various industries. As technology advances, the integration and improvement of these sensors will continue to evolve, ensuring better monitoring and maintenance of critical systems.
Types of Vibration Detection Sensors
Understanding the different types of vibration detection sensors is crucial for anyone looking to utilize this technology effectively. Each type has unique characteristics, applications, and advantages that can be leveraged across various industries. By exploring these types, readers get insights into how these sensors function and their specific relevance in practical applications.
Accelerometers
Accelerometers are devices that measure the acceleration forces acting on an entity, commonly employed to assess motion and vibration. They can provide data on static and dynamic acceleration. The main advantage of accelerometers is their ability to measure in multiple axes, offering comprehensive information about vibration patterns. They play a significant role in numerous industries such as automotive for crash detection systems and smartphones for orientation sensing. The design can vary from micro-electro-mechanical systems (MEMS) to larger models, fitting diverse applications.
Seismic Sensors
Seismic sensors are specialized in monitoring ground vibrations. These sensors are indispensable in geological studies and structural health monitoring. They capture seismic waves produced by earthquakes or construction activities. Their ability to detect minute vibrations makes them vital for predicting seismic events or assessing the integrity of structures like dams and bridges. These sensors typically require robust data processing systems to interpret the signals accurately, highlighting their complexity in data interpretation and equipment setup.
Strain Gauges
Strain gauges measure deformation or strain on an object. They are widely used in engineering fields to monitor structural integrity. A critical advantage of strain gauges is their sensitivity to small changes, making them effective in detecting even slight vibrations. They can be attached to various materials, and their application spans from civil engineering, where they monitor the stress on bridges, to aerospace for analyzing aircraft components. Proper installation and calibration are essential for accurate readings, reflecting the precision required in their application.
Tachometers
Tachometers measure the rotation speed of an object, such as a motor shaft. They are essential in mechanical systems where precise speed regulation is required. Tachometers provide continuous feedback, which is vital for maintaining operational stability in machinery. For instance, in automotive applications, they help monitor engine performance, ensuring efficient operation. Their implementation can range from simple analog devices to complex digital sensors that integrate with control systems. Reliability and accuracy in their measurements are paramount, especially in high-speed environments.
Applications in Various Industries
Vibration detection sensors are integral to many sectors, affecting safety, efficiency, and longevity of equipment and structures. Their role in various industries demonstrates significant value, often influencing operational decisions and maintenance strategies. Understanding the applications in these fields showcases the versatility and necessity of these technologies.
Structural Health Monitoring
Structural health monitoring involves the use of vibration detection sensors to assess the condition of structures like bridges, buildings, and dams. These sensors track vibrations that can indicate potential issues such as cracks or fatigue. Regular monitoring allows for the early detection of problems, potentially preventing catastrophic failures.
Key benefits include:
- Increased Safety: Continuous monitoring reduces the likelihood of unexpected structural failures, ensuring safety for users and occupants.
- Cost Effective Maintenance: Identifying issues early can save substantial repair costs and prolong the lifespan of structures.
- Data Collection: Sensors compile vast amounts of data for analyzing structural integrity over time.
Monitoring systems need to be calibrated and often use complex algorithms to interpret data correctly. This analysis is crucial for reliable maintenance strategies.
Automotive Industry
The automotive sector employs vibration detection sensors for various purposes. These sensors help in evaluating vehicle performance, improving ride comfort, and ensuring safety. They monitor vibrations caused by engine performance, road conditions, and suspension systems.
Some applications are:
- Suspension Analysis: Sensors assess damping forces and vibrations to enhance ride quality.
- Engine Diagnostics: Vibration data can help diagnose engine imbalances or misfires, leading to quicker resolutions.
- Safety Systems: Vibration detection is vital in advanced driver-assistance systems (ADAS) for warning of potential accidents or malfunctions.
Thus, boosting both driving experience and vehicle safety.
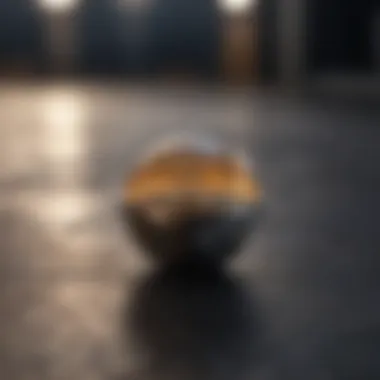
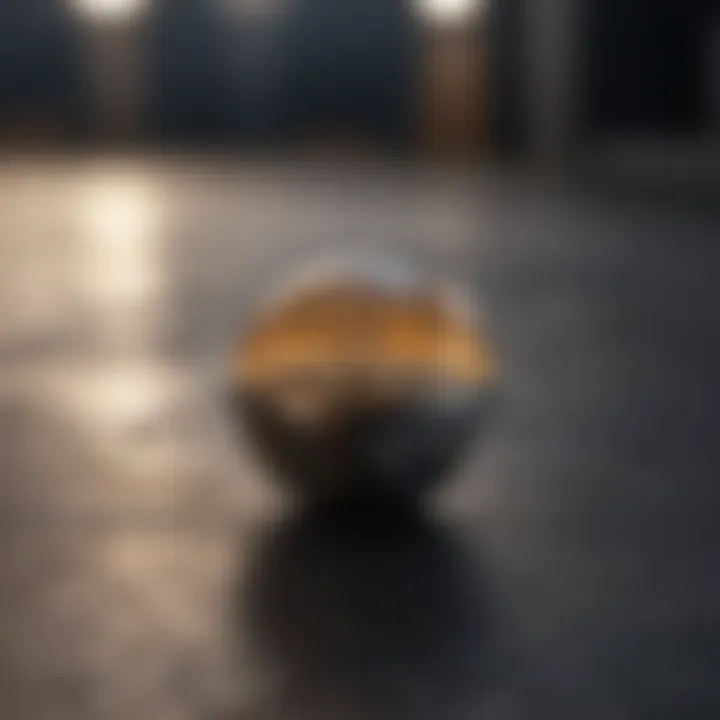
Aerospace Applications
In aerospace, vibration detection is essential for monitoring aircraft health. Sensors are used to analyze vibrations in components, ensuring they work within safe parameters. This is particularly relevant for engines and airframes, where unmonitored vibrations can lead to material fatigue or failure.
Key points include:
- Flight Safety: Continuous monitoring helps ensure that all systems are functioning correctly, preventing in-flight issues.
- Performance Optimization: Data allows for the fine-tuning of components leading to better fuel efficiency.
- Predictive Maintenance: Analyzing data can indicate when components need repair or replacement, minimizing downtime.
Industrial Machinery
Vibration detection sensors are crucial in the manufacturing and industrial sectors. These sensors monitor machines, detecting imbalances or misalignments that can lead to costly breakdowns.
Applications involve:
- Condition Monitoring: Sensors keep track of machinery health, allowing for scheduled maintenance.
- Failure Prevention: Early identification of problems can avert unexpected failures, reducing interruptions in operations.
- Efficiency Improvement: Analyzing vibration patterns can lead to operational adjustments, enhancing overall performance.
The integration of vibration sensors in industrial settings clearly enhances operational reliability and productivity.
Advancements in Vibration Detection Technology
Vibration detection technology has seen significant progress in recent years. These advancements are crucial in enhancing the performance and versatility of vibration sensors. As industries become increasingly reliant on accurate and timely data, the evolution of this technology becomes essential. Emerging capabilities and integration into broader systems enhance the overall utility and application of these sensors.
Miniaturization of Sensors
Miniaturization is a key trend in the development of vibration detection sensors. Smaller sensors enable easier integration into various devices and environments. This reduction in size often comes without sacrificing performance, making them suitable for applications where space constraints are an issue. For instance, in personal electronics or compact machinery, these miniaturized sensors can fit seamlessly without impacting other components.
Furthermore, miniaturized sensors can lower costs due to reduced material usage and simpler installation processes. The advent of micro-electromechanical systems (MEMS) has been instrumental in this miniaturization process. MEMS technology enables the creation of tiny sensors with high sensitivity, allowing them to measure minute vibrations. This advancement opens pathways to innovative applications, such as in medical devices or smart wearables.
Integration with IoT
The integration of vibration detection sensors with the Internet of Things (IoT) is transforming various sectors. Connected sensors provide real-time data, allowing for immediate analysis and response. This capability is particularly significant in monitoring systems that require constant vigilance.
By linking these sensors to IoT platforms, industries can implement predictive maintenance strategies. For example, in manufacturing, machines equipped with IoT-enabled vibration sensors can signal when maintenance is necessary before a failure occurs. This proactive approach can significantly reduce downtime and maintenance costs.
Moreover, IoT integration facilitates data sharing across platforms. This interconnectedness can enhance decision-making processes by providing comprehensive insights into operational conditions. As a result, companies can optimize performance and resource allocation more effectively.
Data Analytics and Machine Learning
Data analytics and machine learning play pivotal roles in maximizing the effectiveness of vibration detection sensors. The sheer volume of data these sensors generate can be overwhelming. However, advanced analytical tools can sift through this data to provide meaningful insights.
Machine learning algorithms can analyze vibration patterns and help in identifying anomalies or early signs of equipment failure. By using historical data, these algorithms can learn typical operational signatures and detect deviations, which may indicate issues that need addressing.
Additionally, applying data analytics allows for better understanding of trends over time. This understanding helps industries not only react to potential problems but also strategically improve systems for increased efficiency. Such advancements lead to more intelligent systems capable of making autonomous decisions based on real-time data and historical learning.
The integration of data analytics with vibration detection sensors is not just enhancing performance but is also shaping the future of predictive analytics in multiple industries.
Challenges in Vibration Detection
In the field of vibration detection, several challenges arise that can significantly impact the effectiveness and accuracy of sensors. Understanding these obstacles is crucial for professionals and researchers who utilize these systems to gather reliable data. Identifying and addressing these challenges can enhance sensor performance, provide valuable insights, and ultimately advance the technology further.
Environmental Interference
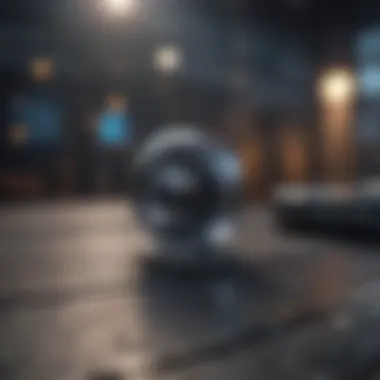
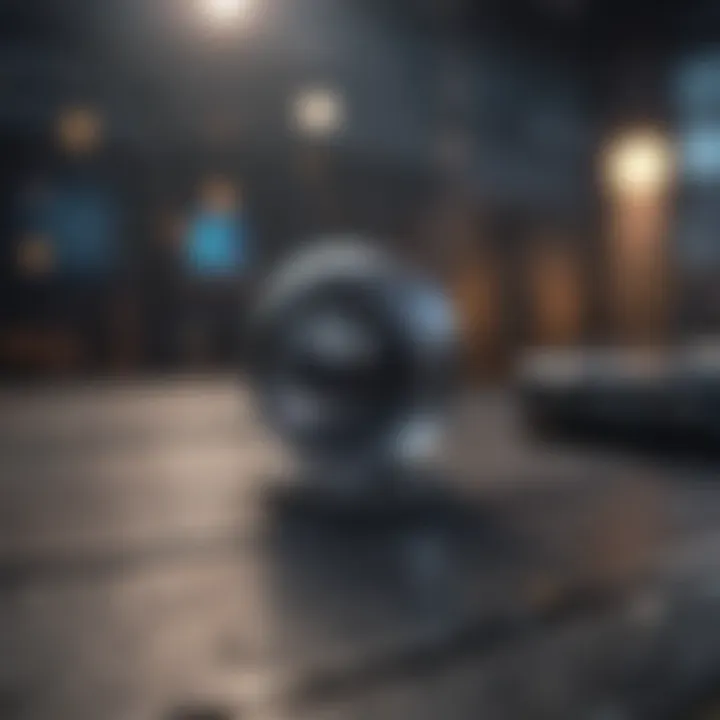
Environmental interference is one major challenge faced by vibration detection sensors. Various external factors can distort the data collected by sensors. For example, temperature fluctuations can affect sensor readings. Changes in humidity may also lead to inaccuracies. Additionally, electromagnetic interference from nearby equipment can further disrupt measurements. This interference must be accounted for during the design and installation of vibration detection systems.
To mitigate these hurdles, engineers often incorporate shielding and filtering techniques into the design. Employing adaptive algorithms can also help differentiate between normal operational vibrations and external noise. Maintaining a controlled environment as much as possible can enhance measurement accuracy.
"Environmental factors must be understood and controlled to ensure effective vibration measurements."
Calibration Issues
Calibration is another critical aspect that can pose problems in vibration detection. Regular calibration is essential to ensure that sensors function correctly. Without proper calibration, readings can become skewed, leading to faulty conclusions. Various factors contribute to calibration issues, such as mechanical wear over time, changes in the environment, and improper installation.
Ensuring accurate calibration involves following standardized procedures. It often includes using reference standards to compare readings and adjusting the sensor accordingly. Institutions and professionals must prioritize ongoing training for personnel to maintain high calibration standards.
Data Interpretation Complexity
The complexity of data interpretation is perhaps the most significant challenge facing users of vibration detection technology. The data collected from sensors can be intricate and require careful analysis to extract meaningful insights. This complexity can arise due to the nature of the signals, different sensor types, or the influence of multiple environmental factors.
Analysts must employ advanced tools and techniques to interpret data effectively. This includes the use of machine learning algorithms and data fusion methods, which can aid in breaking down large datasets into usable information. Moreover, developing a thorough understanding of the subjective nature of vibration data is essential for accurate interpretations.
As the field of vibration detection continues to evolve, addressing these challenges will be pivotal in enhancing the reliability and utility of vibration detection sensors. Understanding how to improve sensor performance in various aspects can ultimately lead to better decision-making across multiple industries.
Future Trends in Vibration Detection Sensors
Vibration detection sensors are integral in various fields today. Their evolution continues with emerging technologies, market needs, and regulatory dynamics influencing their future. Understanding these trends is crucial for stakeholders aiming to remain competitive and innovative.
Emerging Technologies
Modern advancements in vibration detection are largely driven by technological innovations. Miniaturized sensors, for instance, are allowing for greater flexibility in their placement and reducing system costs. New materials, such as graphene and nanomaterials, are showing promising potential to enhance sensor performance. Also, the integration of piezoelectric materials with micro-electromechanical systems (MEMS) opens pathways for highly sensitive and accurate devices.
Another important development is the convergence with artificial intelligence. Sensors increasingly utilize machine learning algorithms for real-time data analysis. This capability allows for predictive maintenance. Businesses can anticipate failures before they happen, thus reducing downtime and maintenance costs.
Market Projections
The vibration detection sensor market is on a growth trajectory. Analysts predict that the market size, valued at several billion dollars today, could see substantial growth by the end of the decade. Increasing demand comes from industries such as aerospace, automotive, and industrial applications prominently. Companies are investing heavily in R&D to unlock new applications and functionalities.
Moreover, as IoT technology becomes prevalent, the adoption of vibration sensors in consumer products will rise. In fact, one study indicates a significant increase in sensor integration in home automation and smart devices. It highlights that these sensors will enable better energy management and user interaction. The future indeed looks promising for this sector.
Regulatory and Safety Considerations
With the rise of such sensors comes the need for regulation and standardization. Regulatory bodies are beginning to introduce guidelines and standards to ensure safety and reliability. Compliance with these regulations is essential for manufacturers and developers.
Safety protocols must also adapt to the increasing sophistication of sensors. As systems become more automated, understanding the implications of sensor data is critical. Any failure could lead to safety risks, particularly in high-stakes environments like healthcare and transportation.
The End
The conclusion serves as a critical synthesis of the insights presented throughout the article on vibration detection sensors. It encapsulates the key learnings while reaffirming the significance of understanding these sensors in contemporary applications. Vibration detection sensors are pivotal in various sectors including structural engineering, automotive safety, and even aerospace applications. Their ability to diagnose issues before they escalate can lead to substantial cost savings and increased safety.
Summary of Key Points
Throughout this exploration, several core points emerge regarding vibration detection sensors:
- Definition & Purpose: Vibration sensors are instruments designed to detect and quantify vibration in structures, machinery, and in various applications.
- Types of Sensors: Different sensors like accelerometers, seismic sensors, and strain gauges serve specific functionalities based on their operational principles.
- Industry Applications: These sensors find applications across industries, from monitoring the integrity of bridges to ensuring vehicle safety.
- Technological Advancements: Innovations such as IoT integration and miniaturization have made these sensors more accessible and effective.
- Challenges: Issues like environmental interference and calibration problems can hinder sensor accuracy and performance.
- Future Trends: Emerging technologies suggest an ongoing evolution in vibration detection methodologies, including enhancements in data analytics and machine learning.
Implications for Future Research
The future of vibration detection sensors holds immense potential for research and development. Several avenues could be worth investigating:
- Sensor Fusion: Exploring how combining different types of sensors could yield more comprehensive data sets.
- Advanced Algorithms: Developing better algorithms for data interpretation can enhance the accuracy and speed of analysis.
- Sustainability: Researching eco-friendly materials for sensor construction may align the technology with sustainability goals.
- Networked Systems: Investigating the potential of integrating these sensors within larger automated systems could improve monitoring capabilities.
In summary, a thorough understanding of vibration detection sensors not only enriches our knowledge of the technology but also accentuates its importance in enhancing safety and efficiency in various fields. The implications for future research are vast, pointing towards a continuous evolution within this domain.